
眼镜产品,从老花镜、安全护目镜到明星同款太阳镜,是少数能在款式和功能上实现无限个性化的产品之一。眼镜制造商会在大到材料选择,小到镜头厚度的微米级差异上做出调整。
随着 3D 打印技术的分辨率、精确度、材料多样性和后处理工艺越来越先进,该技术为设计和制造眼镜提供了一种高性价比的方法。
在本指南中,我们将介绍设计和材料方面的注意事项、当前眼镜行业制造商利用 3D 打印技术的案例研究以及投资回报率计算,以帮助您建立商业案例。
介绍:3D 打印眼镜的兴起
在过去五年里,终端用途 3D 打印眼镜的采用率大幅提高,无论是小公司还是大品牌,都在利用 3D 打印带来的设计自由度、小批量生产能力和可持续发展优势。
无论是用于工作场所防护、功能性表现还是时尚,3D 打印已经渗透到眼镜行业中,并改变了设计师和制造商对生产的思考方式。
3D 打印的一大优势在于减少了制造过程中的装配步骤,同时保持了产品的高度一致性和质量。一些眼镜制造商表示,醋酸纤维镜框的制造需要多达 60 个独立步骤。
3D 打印大大降低了装配的复杂性并减少了相关人工操作,其基本流程如下:

选择性激光烧结 (SLS) 3D 打印是工业应用中最为常用的增材制造技术,因其能够生产坚固的功能性部件而受到不同行业工程师和制造商的信赖。
SLS 3D 打印机使用高功率激光来熔合小颗粒的聚合物粉末。未熔合的粉末在打印过程中支撑部件,所以不再需要使用专门的支撑结构。这使得 SLS 适用于构造内部特征、倒凹、薄壁和凹入特征等复杂几何形状。使用 SLS 打印技术制造的部件具有优良的机械特性,强度类似于注射成型部件,这使得该工艺成为生产 3D 打印眼镜的理想选择。
继续阅读,了解 3D 打印如何提高产品上市速度、减少人工操作,以及消除对镜框和镜腿最小订购量 (MOQ) 的需求。
为什么要打印 3D 眼镜?
制造可持续性
目前,镜框的制造主要通过注射成型、模切或精密数控铣削来完成,这迫使制造商投入大量的模具和设备成本。外包生产模具或加工部件可能需要数周时间,花费数千美元。为了分摊成本,制造商必须承诺极高
产量,这可能导致利润降低和大量滞销库存。
这种模式在财务和环境层面都不可持续。3D 打印可以让企业拥有自己的制造过程,无需模具投资,大大降低了新产品线的启动风险。内部 3D 打印可按需进行小批次制造,无需预付模具成本,从而使制造商摆脱了高 MOQ 要求和对冷门产品设计的承诺。
如今,大多数眼镜均通过注射成型或减材工艺制造,在这些工艺中,醋酸纤维被切割成指定的形状。切割过程中,大块醋酸纤维板材被裁出镜架形状,其余材料均成为废料。

通过切割工艺创建的传统醋酸纤维镜框。图片来源:Visio Optical
相比之下,3D 打印是一种增材制造工艺,即使用基础材料供应逐层创建部件。在形朗 (Formlabs) 的 SLS 生态圈中,未使用的粉末材料可回收再用于下一次打印,几乎不会造成材料浪费。

从 Fuse Sift 料块中取出的 Nylon 11 Powder 3D 打印镜框。
Fuse 系列 SLS 生态圈占地面积小,价格实惠,制造商可以为多个生产地点购买多台机器,将生产能力分配到离消费者更近的地区,减少对海外生产的依赖,避免因全球供应链的复杂性而降低生产速度。分布式生产还能减少生产过剩和运输对环境造成的负面影响。
设计自由
与其他聚合物 3D 打印技术不同,通过 SLS 3D 打印技术生产的部件不需要支撑结构,因为周围的粉末床会提供支撑。由于没有传统成型或切割工艺中常见的支撑结构、浇口或对拔模角度和底切的限制,SLS 3D 打印提供了几乎无限的设计自由度,能够实现以前成本过高甚至无法生产的复杂设计。
制造方面的限制不再妨碍产品设计师创造最实用、贴合、时尚的设计。3D 打印眼镜能够比以往任何时候都更快地响应消费趋势,使品牌能够抓住新兴细分市场中的商机。

复杂的 3D 打印镜腿设计,传统工具很难或根本无法高效制作。
定制化和个性化
同样,由于没有工具要求或最小订购量,产品个性化终于触手可及,可以选择定制尺寸和设计,为客户提供独一无二或更适配的产品。
3D 打印已用于实现矫形器、活动人偶、听力学等领域的产品定制化,一般来说,消费者觉得产品真正提升到更实用或更吸引人的程度,才是最大的成功。如今,人群的年龄、种族和面部特征差异巨大,产品设计师正逐渐摆脱 “一刀切” 的思维,迈向个性化时代。
“有了 3D 打印,我可以立即完成。如果熟悉 CAD 设计,就可以轻松地对 3D 模型进行调整,将其上传到软件,然后直接打印。但如果用铣削工艺,我总得开发专门的昂贵工具来固定机器里的零件。”
Marcus Marienfeld,眼镜设计师和制造商
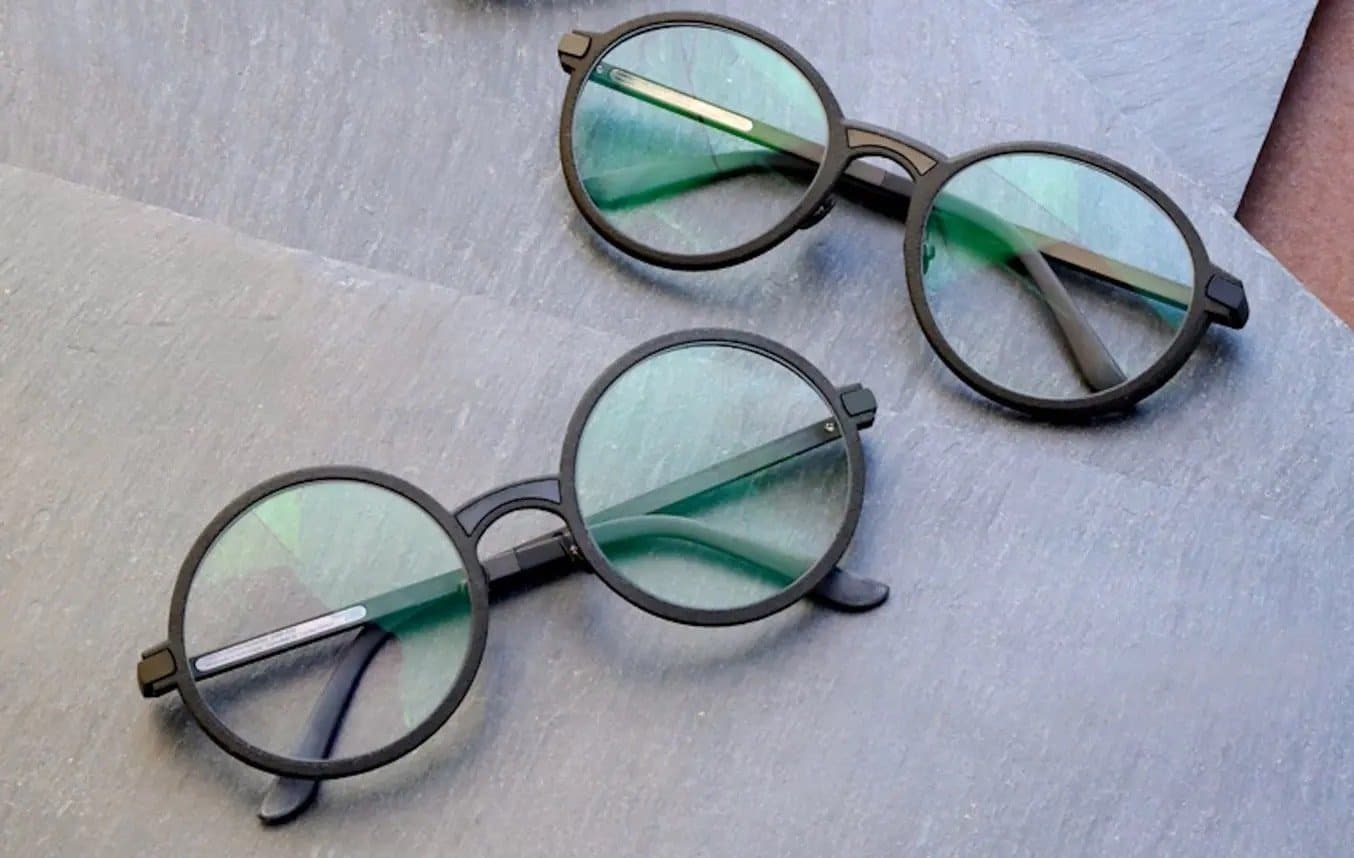
瑞士眼镜制造商 Marcus Marienfeld 利用 Fuse 1+ 30W SLS 3D 打印机生产成品 3D 打印眼镜,包括定制产品。
如何制造 3D 打印眼镜
设计
使用 3D 打印制造成品眼镜具有独特的优势和挑战。在本节中,我们将介绍部件纹理、铰合选项、设计无法成型的几何结构以及定制化。

这些镜框采用 Nylon 12 Powder 3D 打印而成,并通过水浴染成黑色和栗色。
纹理
增材制造部件为逐层形成,这意味着某些表面可能会有明显的层线。可以通过部件定向优化、部件设计和额外的后处理来减少层线,以平滑表面。众所周知,在镜框和镜腿表面添加浮雕或凹入纹理是一种在 3D 打印成品上掩盖层线的策略。
Formlabs 建议浮雕高度至少为 0.35mm,凹入深度至少为 0.15mm,以确保对任何层线进行充分遮蔽。最后,部件层线可以作为增加抓力和摩擦力的工具,防止镜腿在脸上打滑。
铰合选项
3D 打印眼镜铰合主要可以通过四种方式实现:
- 传统螺丝
- 热固性嵌件
- 卡扣
- 即打即用铰链
铰合螺纹可以添加到 3D 打印部件的设计中,但传统眼镜螺纹通常太小,无法稳定处理。确保使用至少 M6(公制)或更大尺寸的螺纹。

用打印螺纹和金属螺钉组装的眼镜。
Nylon 11 Powder、Nylon 12 Powder 和 Nylon 12 White Powder 都可以使用热固性嵌件和螺纹攻丝,与其他选择相比,它们更持久耐用。在此阅读分步指南。
最后,由于没有支撑结构,SLS 3D 打印可以使用即打即用几何形状。设计和打印镜框时,镜腿已经安装好,无需再组装。Formlabs 建议在小于 20mm 的特征上留出 0.3mm 的间隙2,在大于 20mm 的特征上留出 0.6mm 的间隙2。在此阅读完整 SLS 设计指南。
无法成型的几何结构

Nylon 11 Powder 镜腿设计采用了 nTopology 软件中的晶格选项。

Fuse 1+ 30W 打印机打印的镜框和镜腿,由 Alvaro Planchart 设计和制造。
3D 打印主要应用于时尚前沿领域,该技术支持设计师创建无法成型、无法切割的眼镜设计。诸如图中所示的镜腿等无法成型的几何结构,有助于发掘用户表达的新领域,也可以实现组件的极度轻量化,从而提高用户的舒适度。
3D 打印
用于制造眼镜的 3D 打印机
Fuse 系列 SLS 生态圈凭借其可靠的硬件、工业级材料和直观的用户界面,为眼镜生产提供了一个易用的可扩展生产解决方案。以下部分将介绍使用 SLS 3D 打印生产眼镜的具体提示和技巧。

Fuse 系列 SLS 生态圈由 Fuse 1+ 30W 打印机、Fuse Sift 粉末回收站和自动化 Fuse Blast 介质喷砂和抛光解决方案组成。
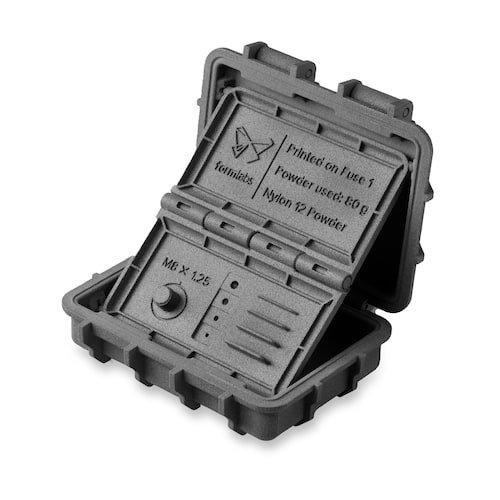
3D 打印镜框材料
Fuse 系列提供三种足以用于眼镜生产的候选材料:Nylon 11 Powder、Nylon 12 Powder 以及 Nylon 12 White Powder。这三种材料都是热塑性塑料,就像醋酸纤维一样,这意味着眼镜店可以在打印后加热镜框和镜腿,使其更贴合面部轮廓。
在与醋酸纤维、TR90 和聚碳酸酯的功能性表现进行对比时,这三种 SLS 材料都极具可比性,Nylon 11 Powder 因其优异的断裂伸长率和可持续性优势而受到一些客户的青睐。
醋酸纤维素 | Grilamid TR90** | Nylon 11 Powder | Nylon 12 Powder | Nylon 12 White Powder | |
---|---|---|---|---|---|
极限拉伸强度 | 30MPa | 60MPa | 49MPa | 50MPa | 47MPa |
拉伸模量 | 1700MPa | 1500MPa | 1600MPa | 1850MPa | 1950MPa |
断裂伸长率 | 30% | 50% | 40% | 11% | 8% |
弯曲强度 | 40MPa | 不适用 | 55MPa | 66MPa | 56MPa |
在实际功能测试中,Nylon 11 Powder 表现出令人印象深刻的延展性和抗冲击强度:
在制造接触自然环境的长效、可持续产品时,还应考虑其他环境和材料性能。
醋酸纤维素* | Grilamid TR90** | Nylon 11 Powder | Nylon 12 Powder | Nylon 12 White Powder | |
---|---|---|---|---|---|
ISO 10993-10:2010/(R)2014,刺激和皮肤安全测试 | 无刺激性 | 无刺激性 | 无刺激性 | 无刺激性 | 无刺激性 |
生物基含量 | 生物基 >50% | 不适用 | 100% 生物基 | 不适用 | 不适用 |
密度 | 1.3 g/cm3 | 1.0 g/cm3 | 1.0 g/cm3 | 0.99 g/cm3 | 0.95 g/cm³ |
吸水率 | 2.3% | 3% | 0.07% | 0.66% | 1.40% |
溶剂兼容性,盐水(3.5% 氯化钠),24 小时重量增量 | 不适用 | 不适用 | 0.1% | 0.2% | 0.1% |
在 0.45MPa 下的热变形温度 (HDT) | 75°C | 100°C | 182°C | 171°C | 177°C |
易燃性,UL 94 第 7 部分 | 不适用 | HB | HB | HB | HB |
*来源:https://www.makeitfrom.com/material-properties/High-Plasticizer-CA
**来源:https://www.picoplast.nl/uploads/bab8c3f16780cb5b51b67be4baece673Grilamid%20TR90%20LX%20-%20MDS%20-%20EN.pdf
由于 Nylon 11 Powder、Nylon 12 Powder 和 Nylon 12 White Powder 密度低、吸水率低、耐高温和阻燃性强,因此可考虑用于功能性更强的应用领域,如工厂车间或现场使用的防护眼镜,从而制造出能承受强烈环境条件的轻型镜框。
最后,Formlabs Nylon 11 Powder 是一种 100% 生物基的可再生材料,因为它的原料来自具有可持续性的蓖麻籽,与某些石油衍生塑料相比,是一种更环保的选择。与 Nylon 12 Powder 相比,Nylon 11 Powder 的碳影响减少了 60%。如需 Nylon 11 Powder 的完整生命周期分析 (LCA) 报告,请联系 Formlabs。
表面光洁度
表面光洁度与模型设计有很大关系,不同的定向会产生不同的表面光洁度。Formlabs 进行了大量部件定向测试,发现使用 Nylon 11 Powder、Nylon 12 Powder 和 Nylon 12 White Powder 时,以 45 度角方向打印镜框可以在示例圆形框架设计中获得最佳的美学表面光洁度。朝向成型室底部的部件一侧均会具有略微光滑的表面光洁度。

Formlabs 发现,以相对成型室底部 45° 角的方向打印镜框有助于确保获得最平滑、最均匀的表面光洁度。
成型容量
以 45 度角定向时,Fuse 1+ 30W 成型室可容纳 77 个示例镜框。这种情况下,截至 2023 年 3 月,使用 Nylon 12 Powder 时,打包密度为 11%,成型时间为 11 小时。Formlabs 在持续改进打印设置。如需对自己的文件进行分析,以确定成本、打印时间和投资回报率,请联系我们的团队。

77 个镜框在 Formlabs 的打印准备软件 PreForm 中打包,该软件可以自动打包文件,以实现最佳打印密度并缩短打印时间。

PreForm 还可以计算材料成本,包括烧结粉末和部件周围的未烧结粉末,从而用于粉末总成本分析。
Nylon 12 Powder | Nylon 11 Powder | |
---|---|---|
每次构建的部件数量 | 77 | 60* |
打包密度** | 10% | 11% |
打印时间 | 11h | 22h 30min |
最大年产量 | 36960*** | 14000*** |
部件数量减少后,打印时间缩短至 24 小时以内,从而提高了生产吞吐量。Nylon 11 Powder 也能一次打印 77 个镜框,但打印时间大于 24 小时。
** 在此阅读有关打包密度和刷新率的更多信息。
*** 假设每天打印一次,每周 5 天,每年 48 周。要求使用第二个成型室来快速更换和开始新的打印。
后处理选项
Nylon 11 Powder 和 Nylon 12 Powder 这两种粉末的自然外观效果均为不透明灰色,表面光洁度比抛光醋酸纤维粗糙。Nylon 12 White Powder 的表面光洁度同样较为粗糙,呈蓝白色调。为了达到更接近传统醋酸纤维或 TR90 眼镜的光洁度,应考虑各种后处理方案。

PA11 打印镜框,从左到右依次为:打印后未处理、振动滚磨、蒸汽平滑、染黑、染蓝、白色 Cerakote 涂层。
准备部件表面
与传统醋酸纤维镜框通常要在木质介质中进行滚磨一样,3D 打印镜框在振动滚磨机中滚磨几个小时后,表面效果也会大幅改善。在使用带有润滑剂的陶瓷介质时,Formlabs 发现表面粗糙度降低了 80%,从而获得了光滑的触感。Formlabs 所用为 Mr. Deburr 300DB 振动滚磨机,这是一种低成本、易使用的选择。
时间 | Nylon 11 Powder 表面粗糙度降低程度 | Nylon 12 Powder 表面粗糙度降低程度 | |
---|---|---|---|
陶瓷* | 8h | 80.87% | 82.43% |
有机物质** | 24h | 80.53% | 82.77% |
*陶瓷角切三角形,边长尺寸为 ¼ 英寸,使用 Kramco 1010 后处理化合物
**核桃壳磨料 14/30 目中粒度

PA11 打印镜框;(下)振动滚磨;(左中)Cerakote 涂层;(右中)蒸汽平滑;(上)Cerakote 涂层。

部件在核桃介质中滚磨,以平滑表面。
着色选项

染料仍然可以渗透到 Nylon 12 Powder 和 Nylon 11 Powder 的深灰色区域,但着色效果可能会稍显暗淡发沉。
利用水浴染色系统为部件着色是一种简单而经济的选择。将部件浸没在带有染色剂的加热水浴中,染色剂会渗透到部件的所有表面,永久性地改变部件的颜色。虽然灰色粉末(Nylon 11 Powder 和 Nylon 12 Powder)可以染色,但用 Nylon 12 White Powder 进行打印是确保获得一系列鲜艳色彩的最佳方法。
对于 SLS 3D 打印部件,市面上也有工业级的染色方案,比如 Dyemansion 公司的机器。不过这类机器的成本可能高达数万美元,对于小批量生产或原型制造来说,可能并不划算。如需了解更多有关 Nylon 12 White Powder 成品部件的经济高效的染色方法,请观看我们与工程师兼产品设计师 Ken Pillonel 共同推出的网络研讨会。
Formlabs 还利用 Cerakote 涂层,既提高了部件的机械性能,又实现了多种配色。Cerakote 是一种薄膜陶瓷涂层,厚度从 0.00635mm 到 0.0254mm 不等,无需底漆。
应用这种涂层后,SLS 3D 打印部件的耐化学腐蚀性和耐刮擦性将会得到改善。Cerakote 还可用于实现光亮的表面光洁度,颜色从粉色到金属色,应有尽有。此外,涂层添加完成后,部件可以通过激光成像获得有趣的图案或携带信息,如徽标或序列号。
通过可定制的光泽固化时间表,Cerakote 还可用于实现光泽表面效果。

Nylon 11 Powder 打印镜框,并涂有 Cerakote H 系列涂层。
SLS 3D 打印部件也可以实现水电浸渍。同样,上漆和移印工艺也与 SLS 技术兼容。
最后,蒸汽平滑工艺可以对 SLS 3D 打印部件表面进行化学密封和平滑处理。蒸汽平滑工艺可提供类似注射成型的表面效果,大大改善表面粗糙度以及防潮和防细菌滋生的能力,同时还能实现光亮的表面光洁度。
Formlabs 利用增材制造技术 (AMT) 来蒸汽平滑眼镜部件。此外,还可以在蒸汽平滑之前或之后在水浴中对部件进行染色,从而使新部件的颜色更加光亮。

蒸汽平滑镜框。
亲身体验
虽然 Formlabs 已探索并开发了许多后处理选项来改善 SLS 3D 打印部件的表面光洁度,但仍有许多未知途径值得一探究竟。许多客户都成功地订购了免费的定制眼镜样品部件,然后运用专有后处理技术(不同的滚磨介质、上漆、涂层等)来实现独特外观。
请联系我们的销售团队,免费订购您自己设计的样品,或订购标准 Nylon 11 Powder、Nylon 12 Powder 或 Nylon 12 White Powder 样品部件,用于尝试保密或专有的后处理技术。
3D 打印在眼镜行业的其他用途
除了生产能力之外,Fuse 1+ 30W 系统的多功能性还能通过其他应用为眼镜行业创造价值。
原型制造
Fuse 系列和 Form 系列系统均可用于眼镜原型制造,以测试尺寸、贴合度和整体设计。
在 Fuse 1+ 30W 系统中选择尼龙材料,制造可长时间佩戴和测试的功能性原型。选择 Form 4 或 Form 4L 系统制造美观性原型,展示类似醋酸纤维和聚碳酸酯的半透明设计。SLA 打印原型造可以连续佩戴数周,但不适合长期佩戴,除非添加紫外线阻隔涂层。

Plastinax 使用 Form 系列 SLA 打印机为半透明材料制造外观性原型。
用户测试
利用 Fuse 1+ 30W 创建可在使用寿命和用户测试期间进行测试和评估的眼镜,以快速获得反馈并迭代尺寸和设计。

Plastinax 利用 Fusion 360 设计定制化镜框,然后直接在 Fuse 1+ 30W SLS 3D 打印机上打印出来。

Nylon 12 Powder 镜框由 Plastinax 设计和打印。
智能眼镜
借助 3D 打印,可以不费吹灰之力地实现复杂设计。添加电子设备的外壳或可穿戴设备所需的复杂组件不会对 3D 打印机造成任何负担。在为智能眼镜创建复杂附件时,可以考虑使用 SLS 3D 打印,否则昂贵的多件式打印模具将难以制造这些附件。
夹具和固定装置
由于耐冲击性强,Nylon 12 Powder、Nylon 12 White Powder 和 Nylon 11 Powder 非常适合用于制造定制夹具和固定装置。Formlabs Nylon 系列粉末足够坚固,在超过 90kg 的压力下,一些用于传统镜框和镜腿的金属(如钛)材料会发生弯曲。

由 Marcus Marienfeld 设计的 SLS 3D 打印 Nylon 11 Powder 压机工具,用于弯曲镜框和镜腿,已拧入肘杆式压力机。

短期注射成型和真空成型
使用 Form 4 或 Form 4L SLA 3D 打印机和 Rigid 10K Resin 生产注射成型模具在许多行业都很常见。由于 Rigid 10K Resin 具有较高的耐热性和出色的表面光洁度,因此可用于镜框和镜腿的小批量注射成型,以及生产真空成型包装的模具制作。

使用 Rigid 10K Resin 制作的 3D 打印注射成型模具。

使用 Rigid 10K Resin 制作的用于热压成型包装的 3D 打印模具。
建立商业案例
通过 3D 打印打造企业或研发新品系列的难度不断降低,成本效益也随之日益增加。一台 Fuse 1+ 30W 3D 打印机每年可生产超过 1.9 万个镜框,或按照未优化的五天生产计划,每年可生产 5 万余个镜腿。
Nylon 12 Powder 镜框* | 单件成本** | |
---|---|---|
1 台 Fuse 1+ | 36960 | 1.27 美元 |
5 台 Fuse 1+ | 184800 | 联系我们了解定价 |
10 台 Fuse 1+ | 369600 | 联系我们了解定价 |
Nylon 12 Powder 镜腿* | 单件成本** | |
---|---|---|
1 台 Fuse 1+ | 87840 | 0.29 美元 |
5 台 Fuse 1+ | 439200 | 联系我们了解定价 |
10 台 Fuse 1+ | 878400 | 联系我们了解定价 |
* 假设每周工作五天,每周打印五次,每年工作 48 周。
**材料成本设置为 69 美元/千克,折扣为 30%,此为该打印批量的典型客户优惠价格。

这些镜腿(左侧和右侧)具有理想的打印效率,其打包密度为 31%,确保所有未烧结的粉末均可回收至下一轮成型,显著降低单件成本。

这些镜框的打包密度不如镜腿,导致刷新率稍差且单件成本略高。但即便如此,单台打印机每年仍能经济高效地生产近 37000 副镜框。
方案 1:掌控生产
生产 3D 打印眼镜最有效、最具成本效益的方法是拥有生产设备。这就需要购买 Fuse 系列 SLS 生态圈。
垂直整合 3D 打印生产的好处包括实现更快的投资回报率、更严格的质量控制、在同一台机器上敏捷地改变设计并从原型制造转到生产,以及将生态圈用于其他目的的能力,如创建夹具和固定装置。
Fuse 系列 SLS 生态圈旨在尽可能便于用户使用,具有即插即用的特点,大多数用户只需几个小时就能了解设备操作方法。同样,该生态圈对设施的要求极低,可以快速安装,并随着需求的增长易于扩展。
还需注意的是,并不是每增加一台 Fuse 1+ 30W 打印机,就需要一台新的 Fuse Sift 或 Fuse Blast。大多数客户将打印机与后处理站的比例控制在 4:1。完整的 Formlabs SLS 打印生态圈包括 Fuse 1+ 30W、Fuse Sift 后处理装置、Fuse Blast 介质喷砂机、两个成型室、两个树脂盒、20kg Nylon 12 Powder 材料以及两年的专家客户支持,所需的费用为 64190 美元。

利用 Fuse 系列,随着需求的增长,可以轻松高效地扩大生产规模。
方案 2:外包给服务机构
全球许多服务机构具有不同程度的一站式解决能力,有些服务机构仅能处理 3D 打印组件,有些则提供设计、打印、后处理和包装服务。
与服务机构合作时,单件成本可能会更高。不过,对于那些没有空间或资金来投资生产设备的人员,或者希望进行小批量实验的人员来说,服务机构不失为一个好的选择。

服务机构可以作为初步测试和概念验证的良好选择。
开启 3D 打印眼镜之旅
眼镜制造是 SLS 3D 打印技术的一个极具潜力的应用领域。眼镜制造商会在大到材料选择,小到镜头厚度的微米级差异上做出调整。随着 3D 打印技术的分辨率、精确度、材料多样性和后处理工艺越来越先进,该技术为设计和制造眼镜提供了一种颇具成本效益的方法。
通过 Fuse 系列 SLS 生态圈,眼镜设计师和制造商能够以前所未有的速度完成原型制造,无需外包或依赖工具制造商,即可生产出成品。SLS 3D 打印可以帮助企业整合设计到生产的整个工作流程,降低成本并提高效率。
如需了解有关 Fuse 系列的更多信息,请访问我们的网站。如需亲自测试我们的 Nylon 系列粉末,请申请免费的 SLS 3D 打印样品部件。