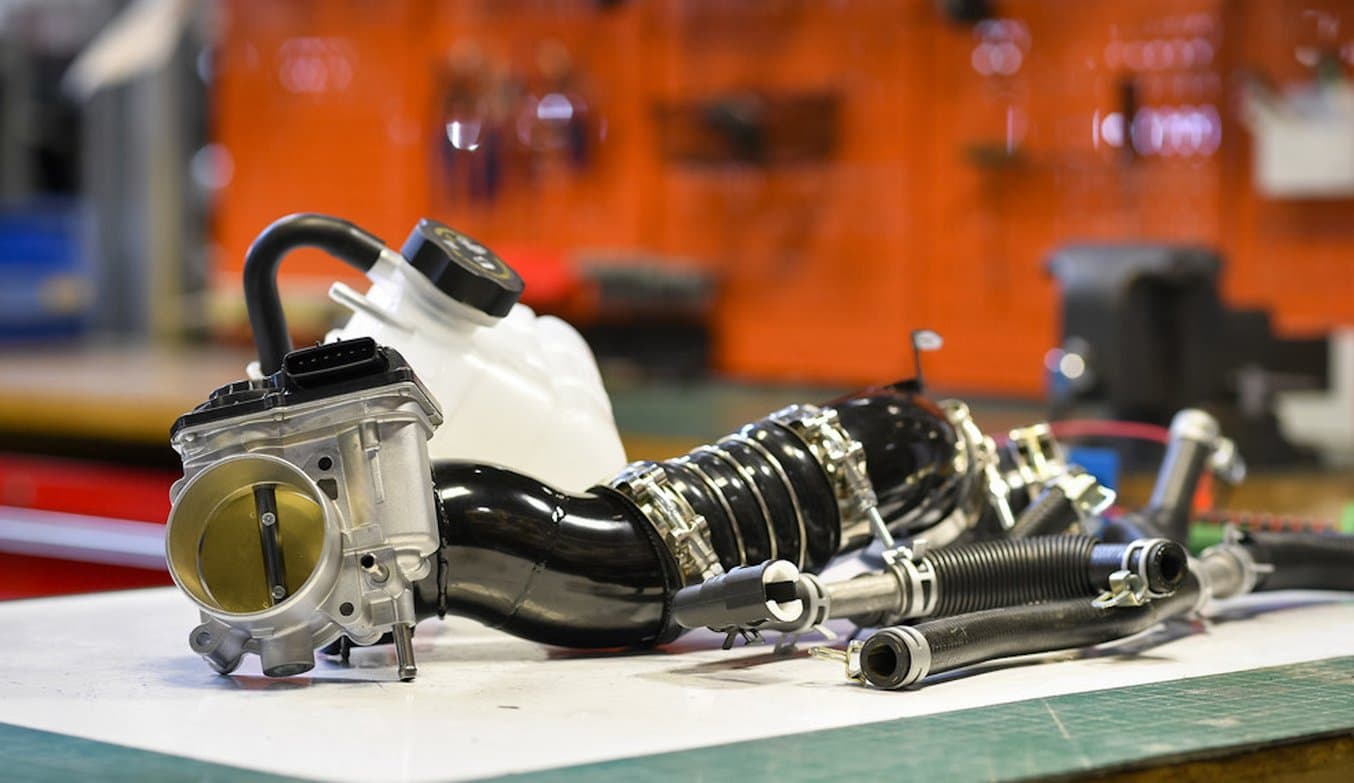
在过去的两年里,受全球电脑芯片短缺、物流受阻和工厂停产的影响,新车和二手车价格飙升。有车一族在他们的爱车过保后如果没有换车计划,为了确保车辆仍然可以正常驾驶,必须对其进行维护和定期保养。汽车制造商通过经销商来销售部件并提供各种服务,但他们也受到供应链问题的困扰,对于私家车主来说,4S 店的服务并不像修理厂那样经济实惠。
Dorman Products 是一家拥有百年历史的汽车售后部件制造商,为轻型和重型车辆提供配套部件。他们已经转向使用 3D 打印技术,以加快生产进度并提高产品质量。Dorman Products 在两个工厂配置了十二台 3D 打印机,依靠这些设备,他们能够满足原始设备制造商 (OEM) 不断推出新车型的需求。
Dorman 的增材制造主管 Chris Allebach 和机械设计团队经理 Eric Tryson 运用 Form 2、Form 3 和 Form 3L 立体光固化 (SLA) 打印机以及多台 FDM 打印机,快速制作出新部件的原型,并针对验证过程创建定制夹具和固定装置。
“OEM 的团队有时会在新车上市前两年就开始设计单个部件。我们需要寻找各种办法来确保我们的替代部件发挥可靠的性能,同时保证其能够尽快上市。采用 3D 打印技术进行设计迭代和实时修改,为我们开辟了一条全新的成功之路。认识到该项技术可以制造出高质量部件后,更加坚定了我们继续使用该技术的信心,”Allebach 表示。
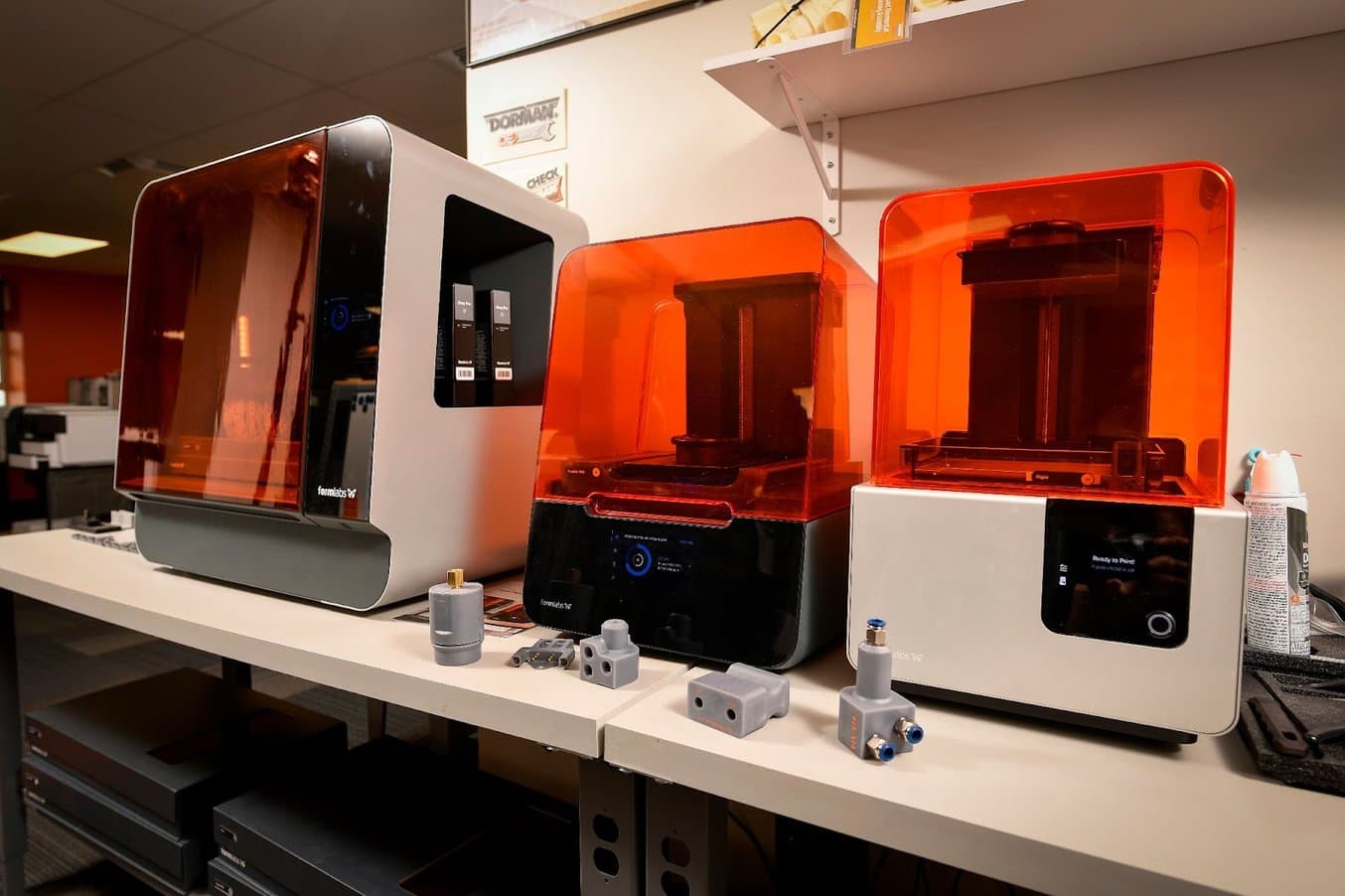
Dorman 的工程师使用 Form 2、Form 3+ 和 Form 3L 打印机。
制造 10 万余种各式产品
Dorman 拥有海量的产品-他们管理着一个包含 118000 个不同类型部件(截至 2021 年 12 月 25 日)的庞大数据库,这些部件全部由他们自行设计,涵盖数百种不同款式的车辆;“我们的产品系列极为丰富,几乎覆盖了汽车的方方面面,按照过往经验,我们每年会推出大约 4000 到 5000 款新部件,”Tryson 说道。
Dorman 的产品范围非常广泛,从钥匙遥控器和发动机主要组件,到复杂的电子模块和重型卡车部件一应俱全。Dorman 分析 OEM 部件的缺陷,并进行逆向工程,甚至有时会完全重构和改进原有设计。他们经常会去寻找原厂部件,有时甚至购买整辆汽车,以便全面了解整个车辆系统并验证改进的设计。
在设计过程中,首先需要进行数字重建,以便能够修改设计。然后,这些部件被送往 Dorman 的计量实验室,在实验室中使用非接触式激光扫描或接触式探头获取部件的高精度测量数据。随后,基准数据被发送回 Allebach 和 Tryson 的团队,他们使用 Solidworks 进行部件的逆向工程。
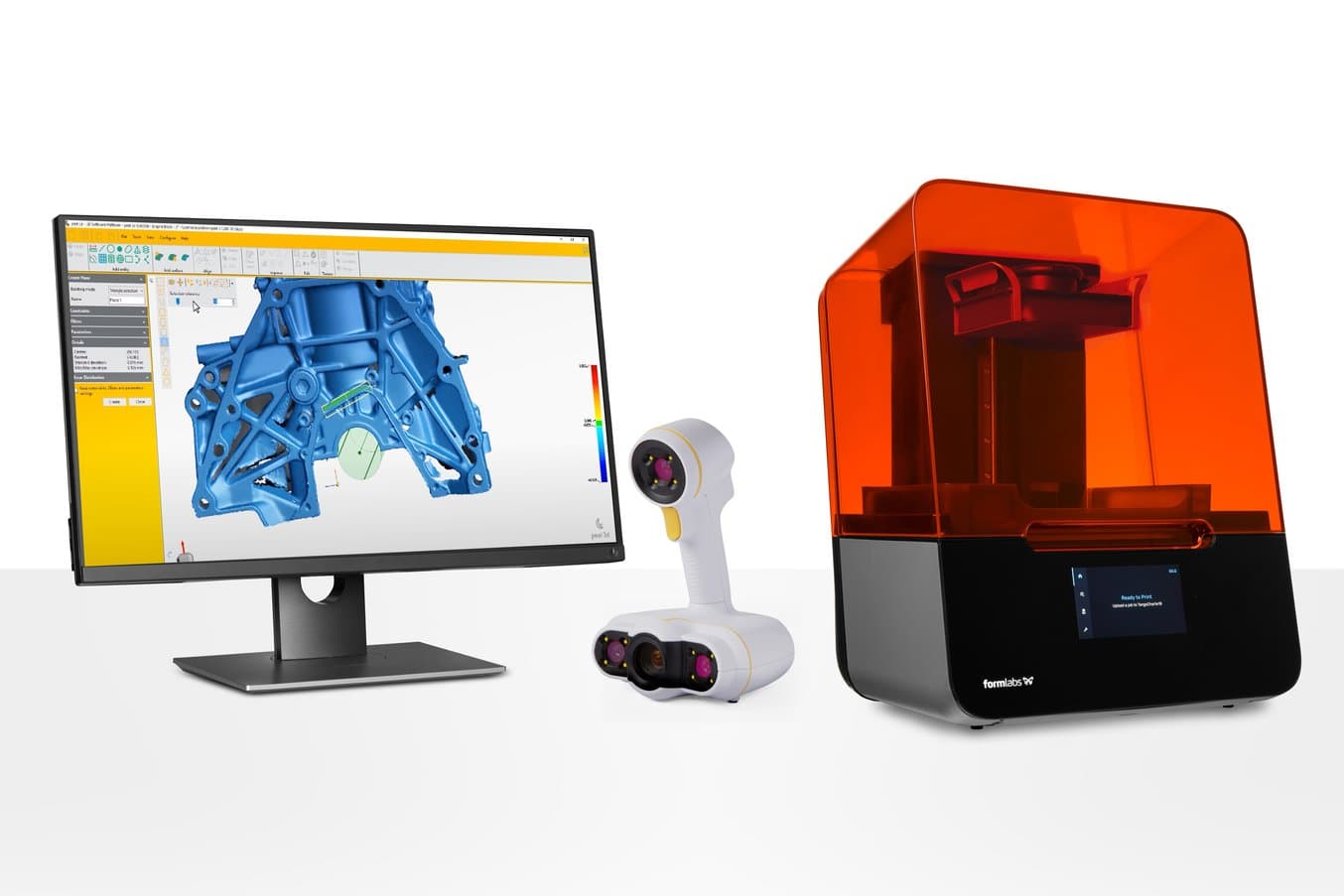
“我们进行快速原型制造,便于设计师进行复查,确保几何形状和尺寸正确,然后我们制作另一个 3D 原型,将其发送给产品工程师进行审查。他们希望亲自用肉眼观察部件,检查部件与车辆的配套部件之间的匹配度,”Tryson 表示。
但 Allebach 和 Tryson 团队的目标并不仅仅是替换原厂部件。在 Dorman 的 OE FIX™ 产品系列中,他们尝试改进原始设计。“不仅仅是进行逆向工程,我们还分析和确定部件产生缺陷的原因,以及如何进行改进。这可能涉及到材料的更换,或者设计变更。如果正在进行重新设计,我们希望首先进行原型制造,然后进行功能测试,”Tryson 表示。
OE FIX™ 部件原型制造
以某个发动机组件为例,大量车主报告该部件发生故障。原厂部件由塑料制成,但会在长时间发动机高温的作用下出现开裂。Dorman 团队分析该部件,安排计量团队进行扫描,并决定使用铸造铝重新设计它。使用另一种材料对产品进行重新设计并不仅仅是材料原样更换这么简单-这个部件必须适合压铸工艺。为了确保部件在重新设计后性能没有下降,他们需要尝试各种原型,并对每个迭代设计进行测试。
“完成设计迭代只需数小时,这样每天就可以完成两个迭代,对于产品开发具有重要意义。在采用 3D 打印技术之前,我们只能寄希望于第一次就获得预期结果。否则,往往会耗费数周甚至数个月的时间进行重复工作,”Tryson 表示。
Dorman 在内部进行原型制造后,他们就可以立即进行功能测试,以验证该部件仍然具有同等性能。
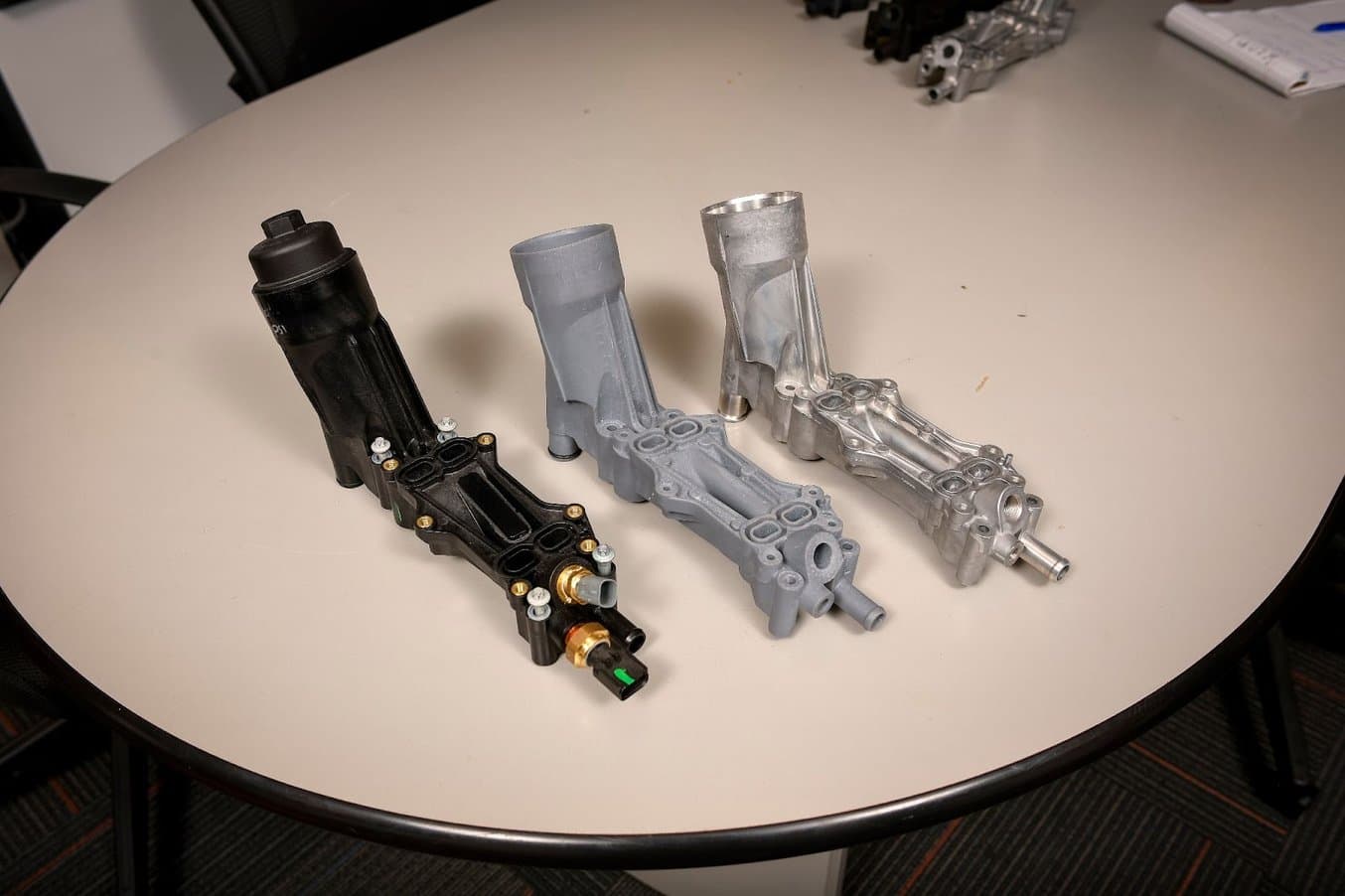
大量车主报告此发动机部件故障,此处展示的是 Dorman 重新设计的迭代结果。
验证过程
由于每个产品的功能各不相同,因此每个测试方案和验证过程都是独一无二的。即使两个不同部件的验证过程都需要进行流体流动测试,由于几何形状不同,仍然需要不同的固定装置来将两个部件固定就位。
Formlabs 打印机的一个主要功能就是制造测试固定装置。从 Elastic Resin 到 Rigid 10K Resin 的各种软硬材料均可打印。从生产周期和成本的角度来看,优势明显。
Chris Allebach,Dorman Products 增材制造主管
在将 3D 打印机纳入他们的工作流程之前,制造定制固定装置导致开发进度迟缓。对于诸如 Dorman 等公司来说,需要满足 OEM 每年不断推出新车型的需要,行动迟缓意味着失去市场机会。
每个产品的配套固定装置各不相同,无法批量订购,导致经济高效的注射成型方法无用武之地。唯一的选择就是昂贵又耗时的机加工。他们必须确保设计完美无缺,然后将其发送给第三方,并等待数周收到结果,然后才能完成对部件的验证工作。
“对于固定装置和量规,我们必须借助机加工厂的帮助,而这需要耗费五到六周的时间。从成本的角度来看,每个部件的成本增加 5 到 10 倍,而且几何形状受到传统制造技术的限制。现在,有了 3D 打印机,我们在制作产品原型的同时,可以开发测试固定装置和量规,所以当确定最终设计时,我们也可以用固定装置进行测试。我们始终掌握着产品开发的主动权,”Allebach 说。
加压软管测试中,一个验证过程需要两个 3D 打印的测试固定装置。一个固定装置用于封闭软管一端,并通过其注入流体,以确定其承压极限。另一个固定装置用于仿真匹配的几何形状,在实际应用中,就是位于汽车发动机舱下方的大型散热器。将 3D 打印范围限定于散热器的配套部分能够赋予测试团队更大的操作空间,同时也意味着他们可以将该部件发送到其制造流水线,模拟真实场景进行验证测试,作为额外的质量控制过程。
“如果配套部件是一个巨大的散热器,无需购买多个部件并发货,而只需要其中一小部分即可。通过这种方式,我们只需制造需要的部件,进行批量生产,然后分发。最后,如果部件损坏,只需几美元,我们就可以打印出一个新部件,”Tryson 表示。
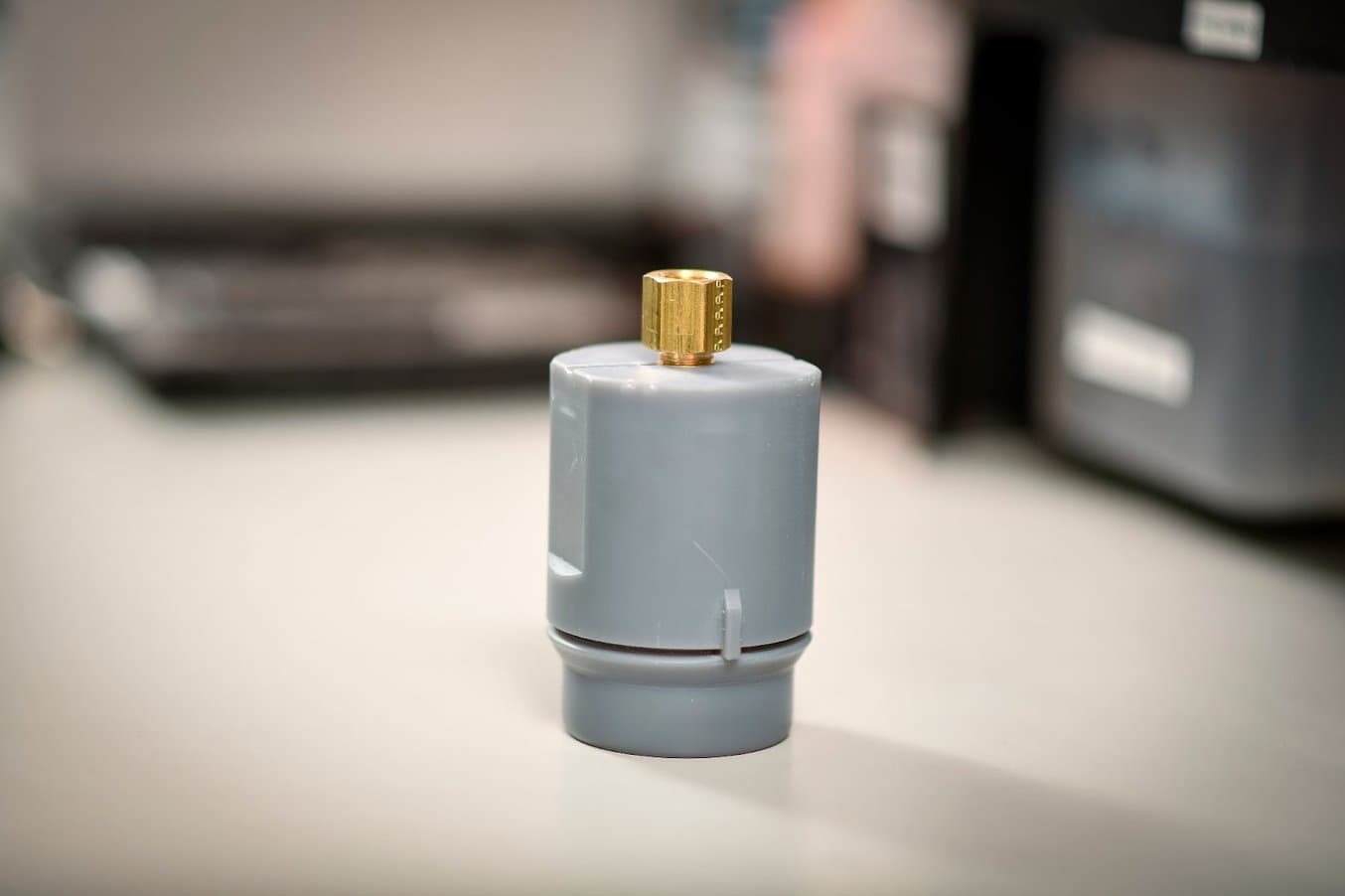
加压软管测试的两个测试固定装置之一。
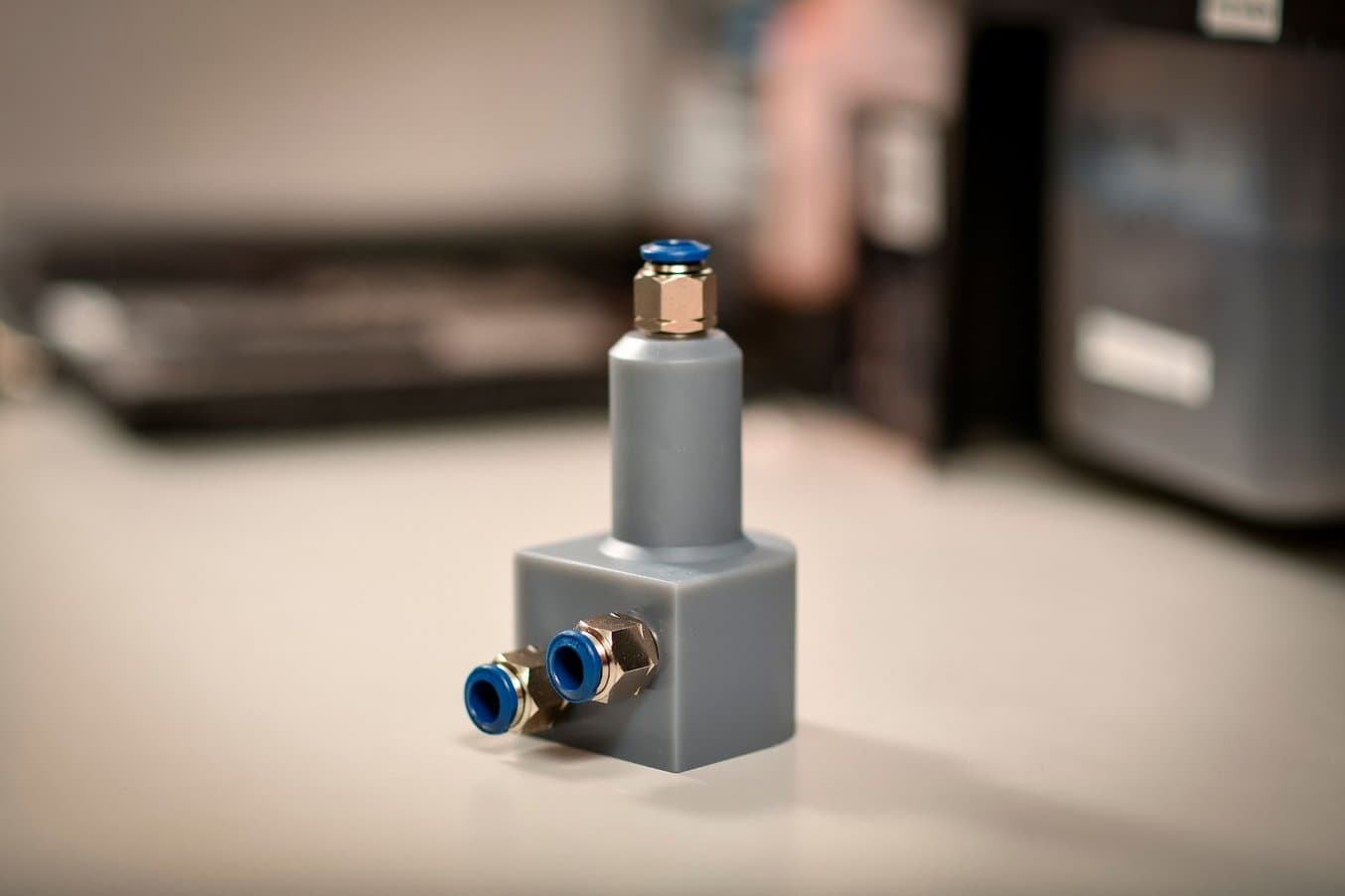
定制固定装置用于仿真匹配的几何形状,无需整个散热器即可测试其配合。
合格/不合格测试的精密公差
在这些产品投放市场并安装在客户的车辆中之前,Dorman 团队需要准确了解这些部件的尺寸变化公差,因此他们会进行尺寸分析,以确定部件是“合格”还是“不合格”。在某些情况下,可能需要达到精密公差,Tryson 和 Allebach 不确定在 3D 打印量规上是否能够实现此种公差,直到他们使用 Form 3+ 和 Form 3L 打印机获得了满意的结果。
“由于公差要求得以满足,我们使用 Formlabs 打印机制造了大量通止规。当工程师过来告诉我们,需要直径达到 ±0.05mm 的公差时,我曾认为 3D 打印无法制造用来检查部件尺寸的通止规,但是我们成功打印了直径公差为 0.025mm 的通止规。使用 Form 3L 可以实现如此精密的公差是我万万没有想到的,”Allebach 说道。
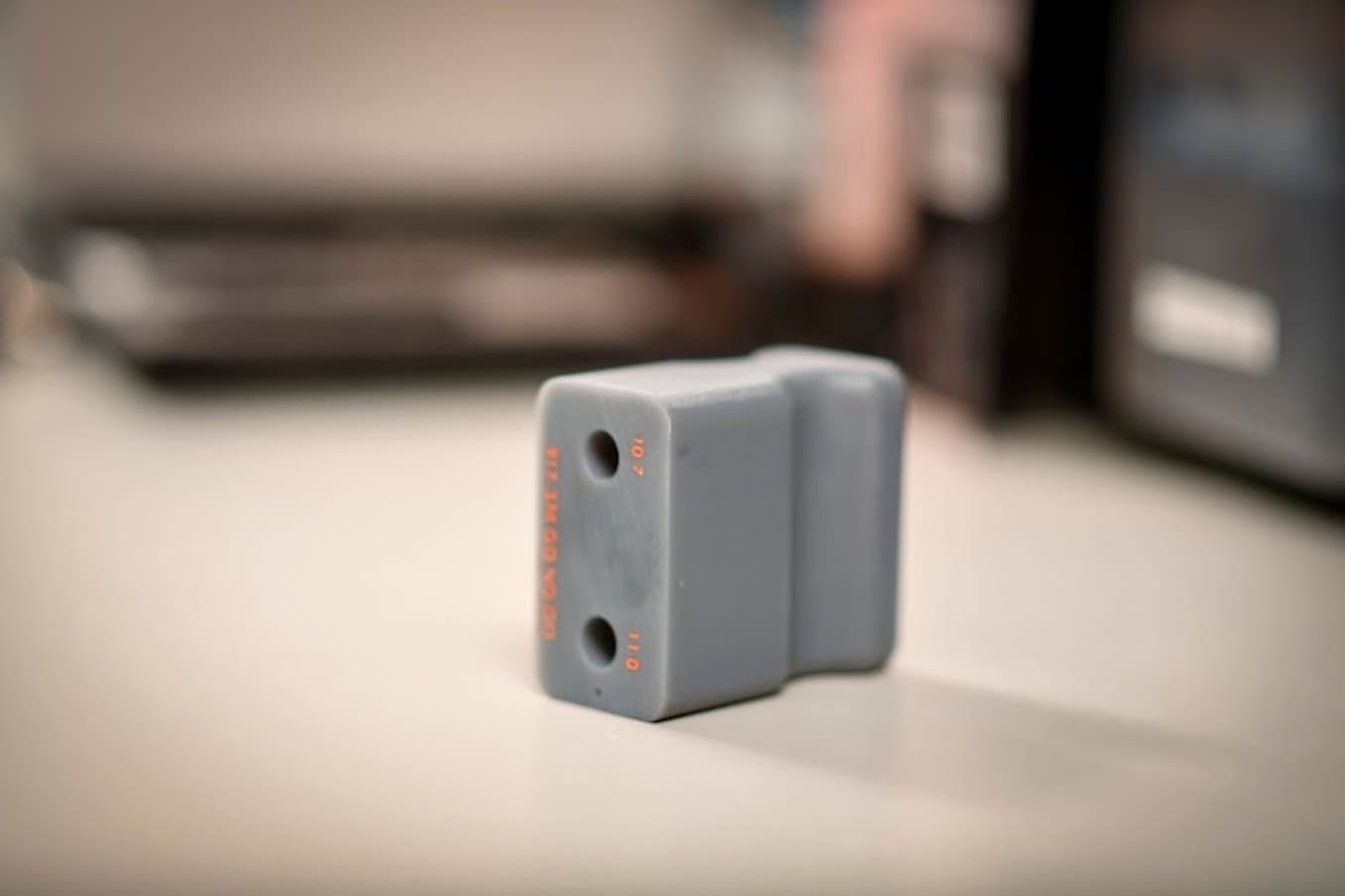
使用 Grey Resin 打印的通止规。
使用硅胶 3D 打印生产用于压力测试的密封垫
当团队对组件进行压力测试以验证新设计时,他们需要能够密封特定的端口和表面。然而,他们有时并不具有用于密封每个部件的配套几何形状,因此必须大胆创新,投入大部分精力用于制造定制密封垫和固定装置。
采用传统加工方式时,他们会在实验室中测量部件尺寸,制作金属模具,然后使用模具在压床上切割定制的密封垫。“这种方式就像从一张面饼上切割饼干一样。从我们实验室技术人员的角度来看,这样做在材料使用和时间利用方面非常低效,”Allebach 说道。
采用 3D 打印技术可以极大地缩短生产时间并降低成本,尤其是考虑到生产大量新组件的情况时,优势明显。“我们打印了数百个定制密封垫,供节气门测试人员密封节气门的两端,并进行流量测试,”Allebach 表示。
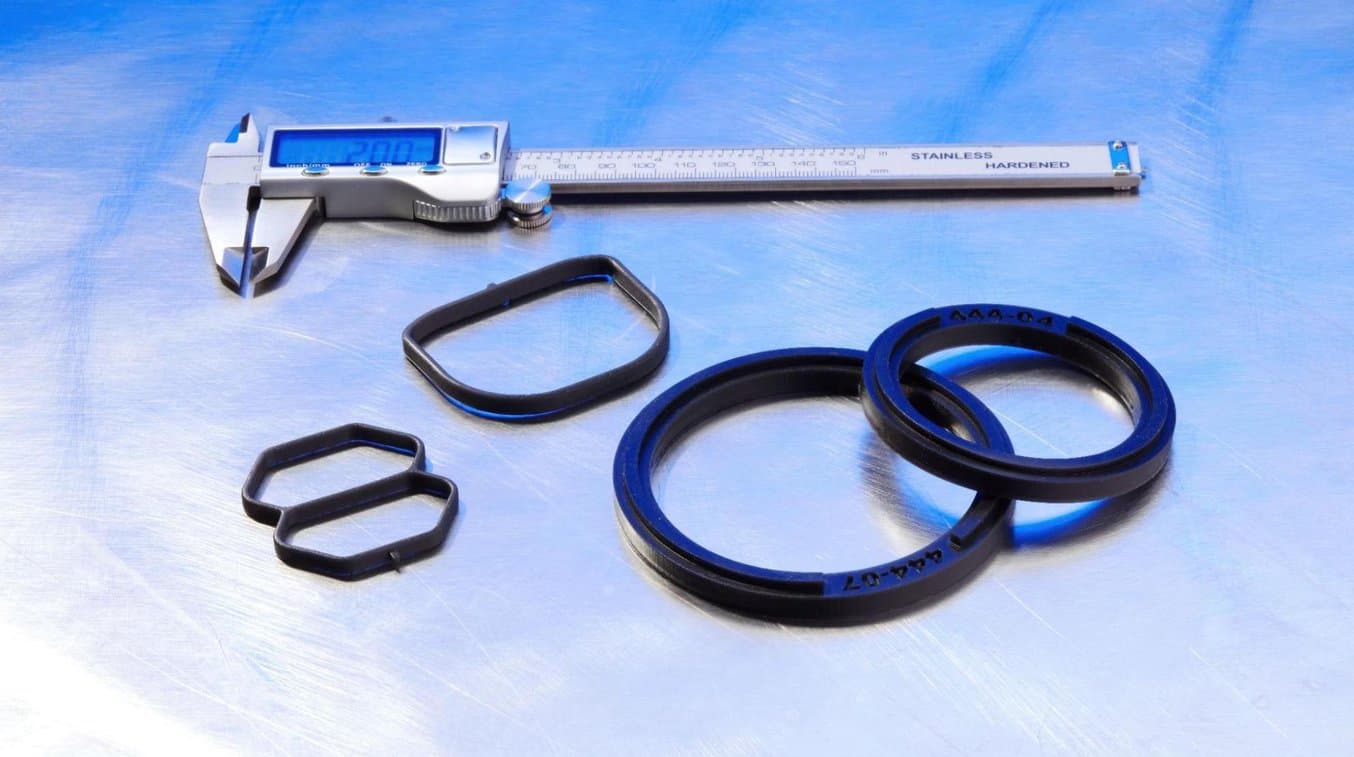
Dorman Products 使用 Silicone 40A Resin 3D 打印的定制密封垫。
虽然 Formlabs 的类硅胶 Elastic 50A Resin 有时适用于这个用途,但最新推出的 Silicone 40A Resin(硅胶 40A 树脂)作为市面上首款商用纯硅胶 3D 打印材料,具有更广阔的应用空间。“[与类硅胶 3D 打印材料相比],Silicone 40A Resin 的耐用性发生了质的飞跃,本质上,它是一种硅胶树脂,但它的性能像注射成型硅胶一样出色,完全超出了我的预期,”Allebach 说道。
耐化学腐蚀和耐高温性是他们选择 Silicone 40A Resin 的两个关键因素。他们对 3D 打印的部件进行了为期两个月的化学测试,包括油、洗涤液和紫外线环境测试,然后进行了压缩形变测试。回弹和其他机械性能足以满足他们的要求。
用于验证测试的密封垫
周转时间 | 成本 | |
---|---|---|
使用机械加工的金属模具切割硅胶板 | 每组 2 周 | 每组 250 美元 |
使用 Silicone 40A Resin 进行 SLA 3D 打印 | 每组 3 小时 | 每组 12 美元 |
“能够制造定制密封垫以便用于在热时效炉中进行测试、在模拟发动机舱环境下进行密封测试,或能够在空气、水、冷却液、机油等各种实际使用场景中进行测试,这对我们来说非常重要。”
Chris Allebach,Dorman Products 增材制造主管

推出 Silicone 40A Resin
在本次网络研讨会中,我们的 3D 打印专家将向您详细介绍 Silicone 40A Resin 的主要优势和应用,并展示该树脂的材料特性和工作流程。
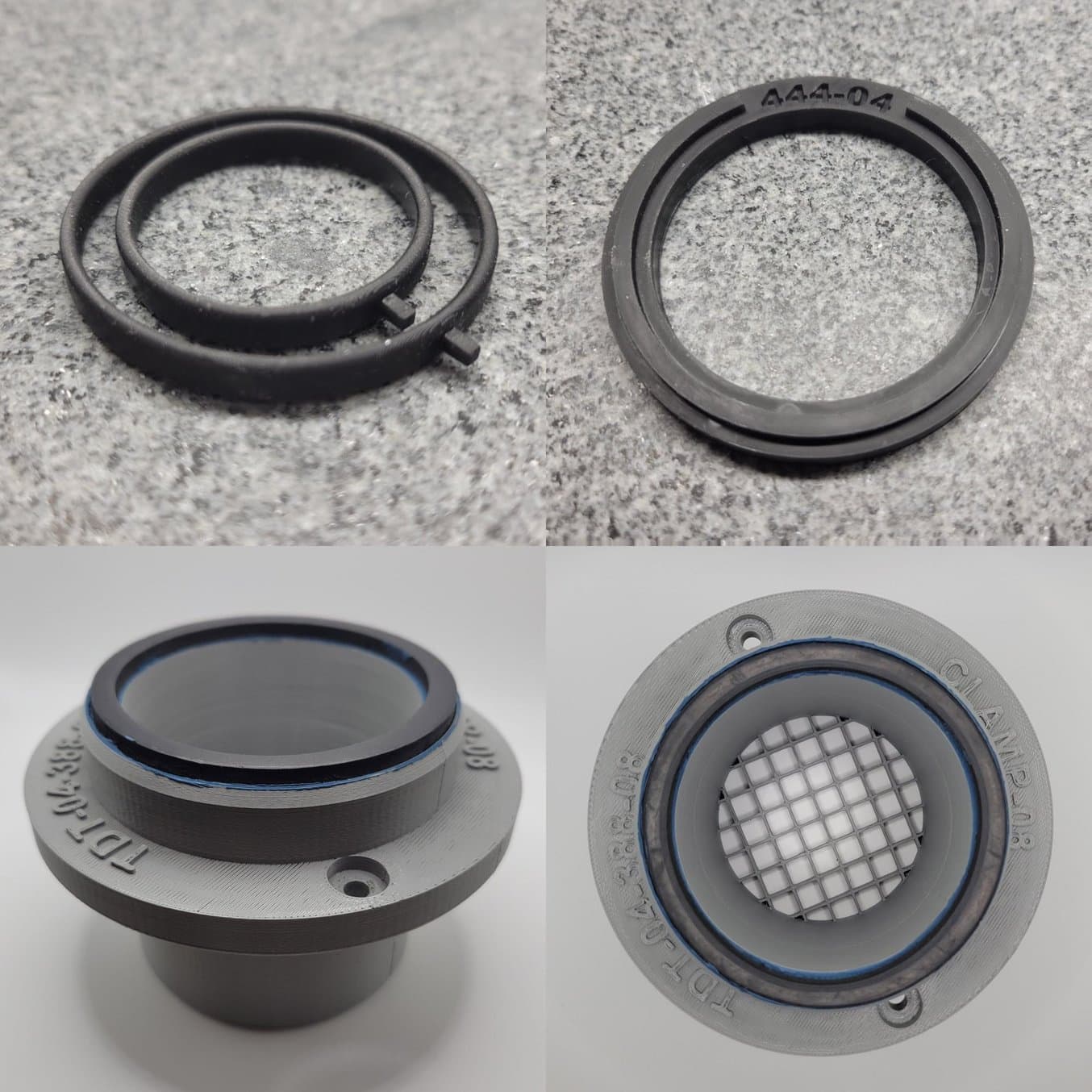
定制进气歧管垫圈和 3D 打印的气流测试适配器。
Allebach 对弹性 3D 打印材料所展现出来的设计自由度非常满意。
“该树脂具有极佳的打印能力。我完全没有想到,如此柔软的材料居然可以打印出极佳的精细特性。对于那些超出我们制造能力范围的部件,我们尝试使用 Silicone 40A Resin 进行打印。这些部件以往均通过注射成型制成。我们切切实实地突破了可打印性的极限。我简直不敢相信小型几何打印部件的质量可以出色至此。每个人对材料的触感和回弹性能拍手称快。”
Chris Allebach,Dorman Products 增材制造主管
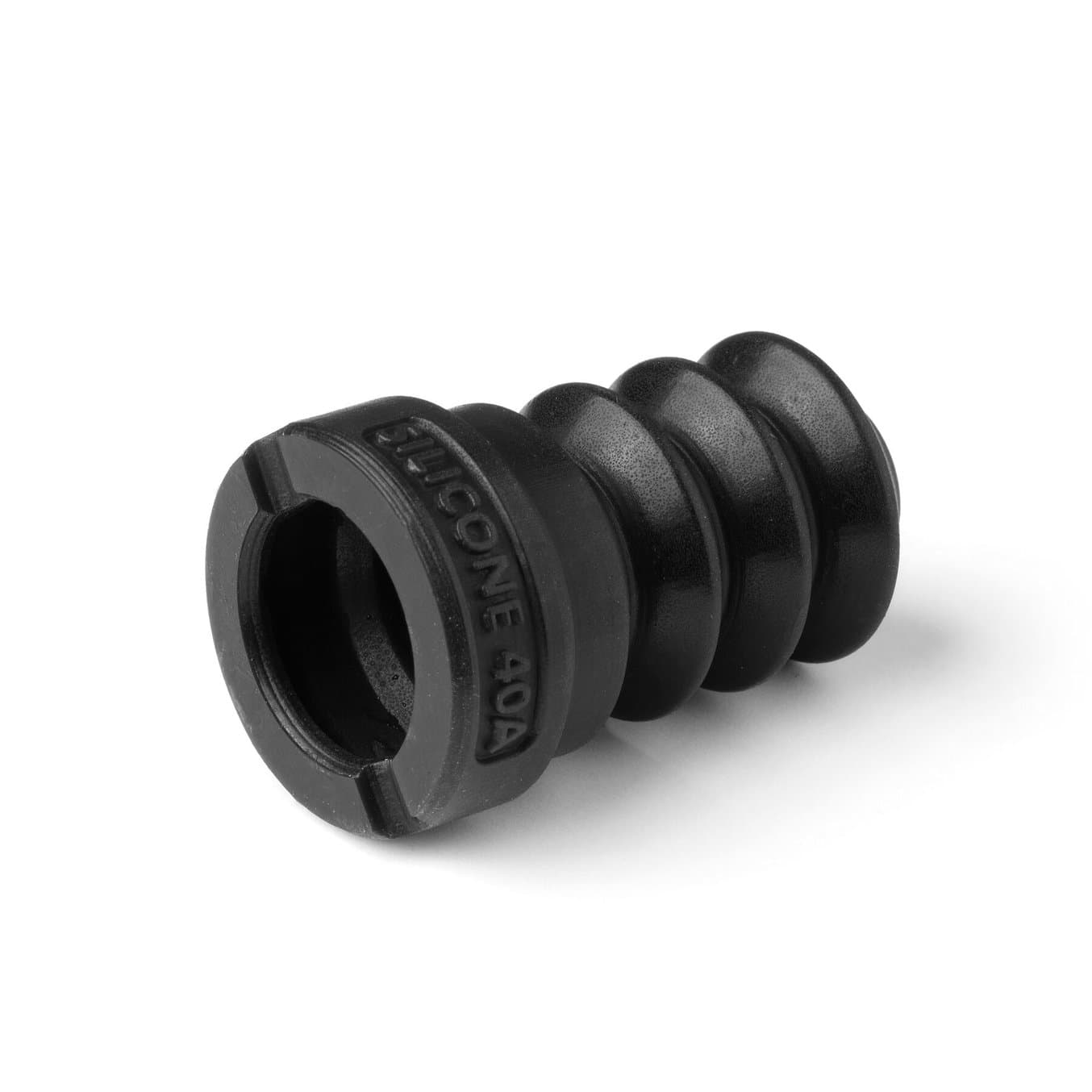
令人难以置信的完美金属部件
Tryson 和 Allebach 在将部件发送给 Dorman 市场和销售团队之前,通常会对部件进行一些额外的后处理。对于最终将以金属形式进行批量生产的部件,他们会在 SLA 打印的部件上进行后处理,然后将其交给市场部门。最近,他们使用 Grey Pro Resin 为底盘团队打印了一些球头螺栓,然后在交给市场部门之前,对它们进行了电镀(由 Repliform INC 进行电镀)。唯一的问题是-表面光洁度过于完美!“市场团队说,‘这些部件通常采用锻造或铸造方式,然后再镀锌。如果我们使用这个新部件,它的外观更完美,’”Allebach 表示。
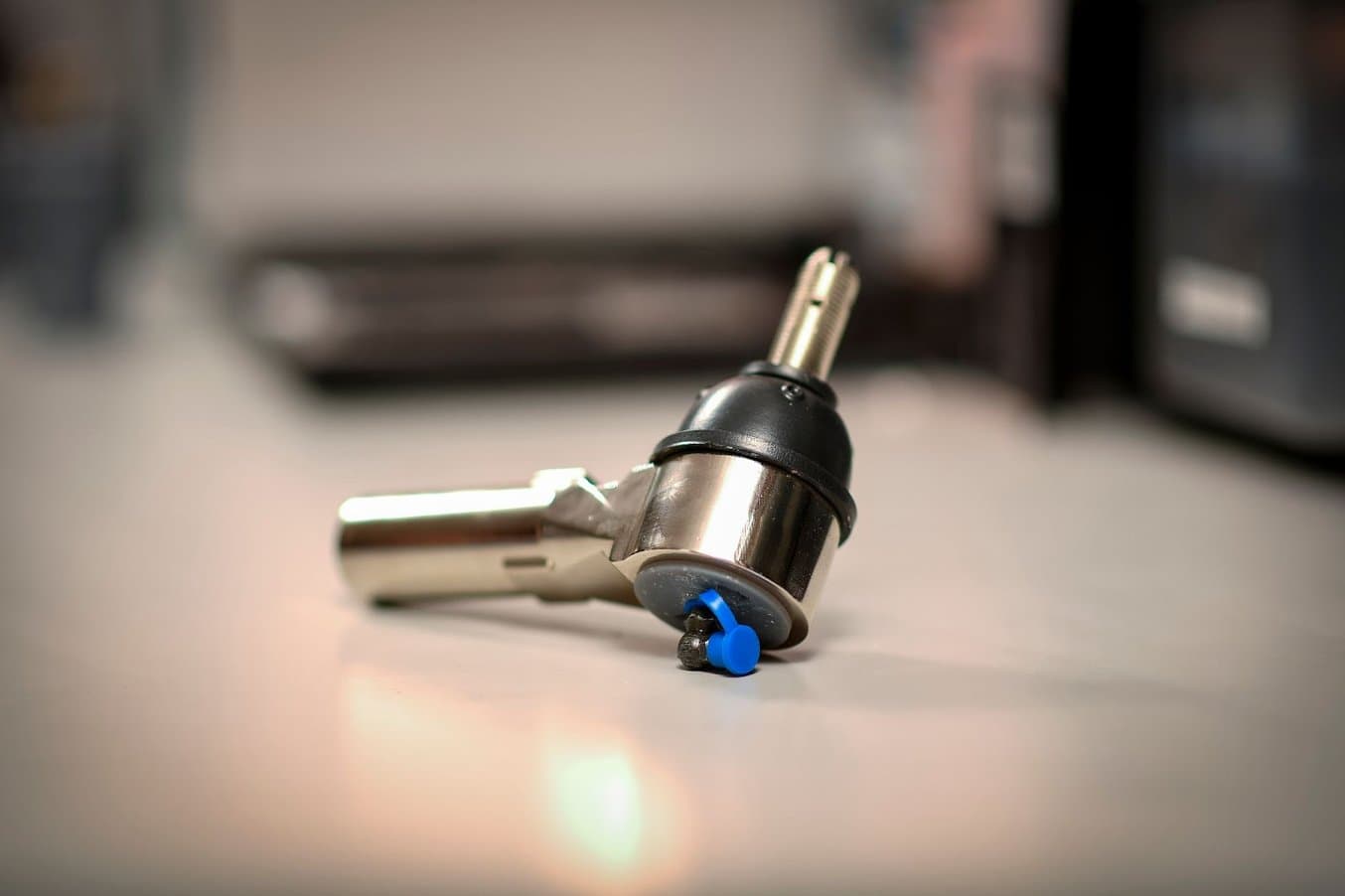
一个经过电镀处理的装配件。
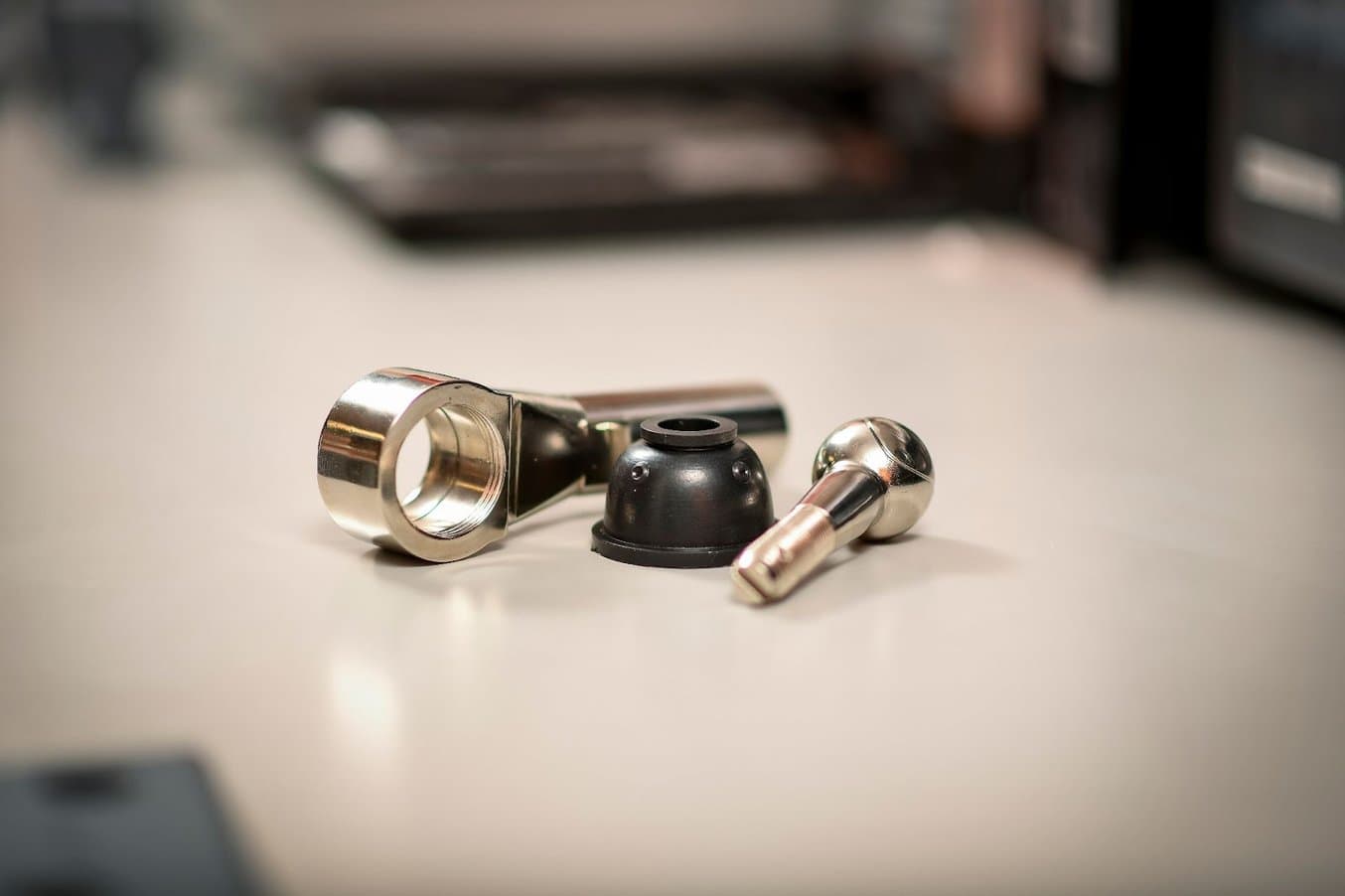
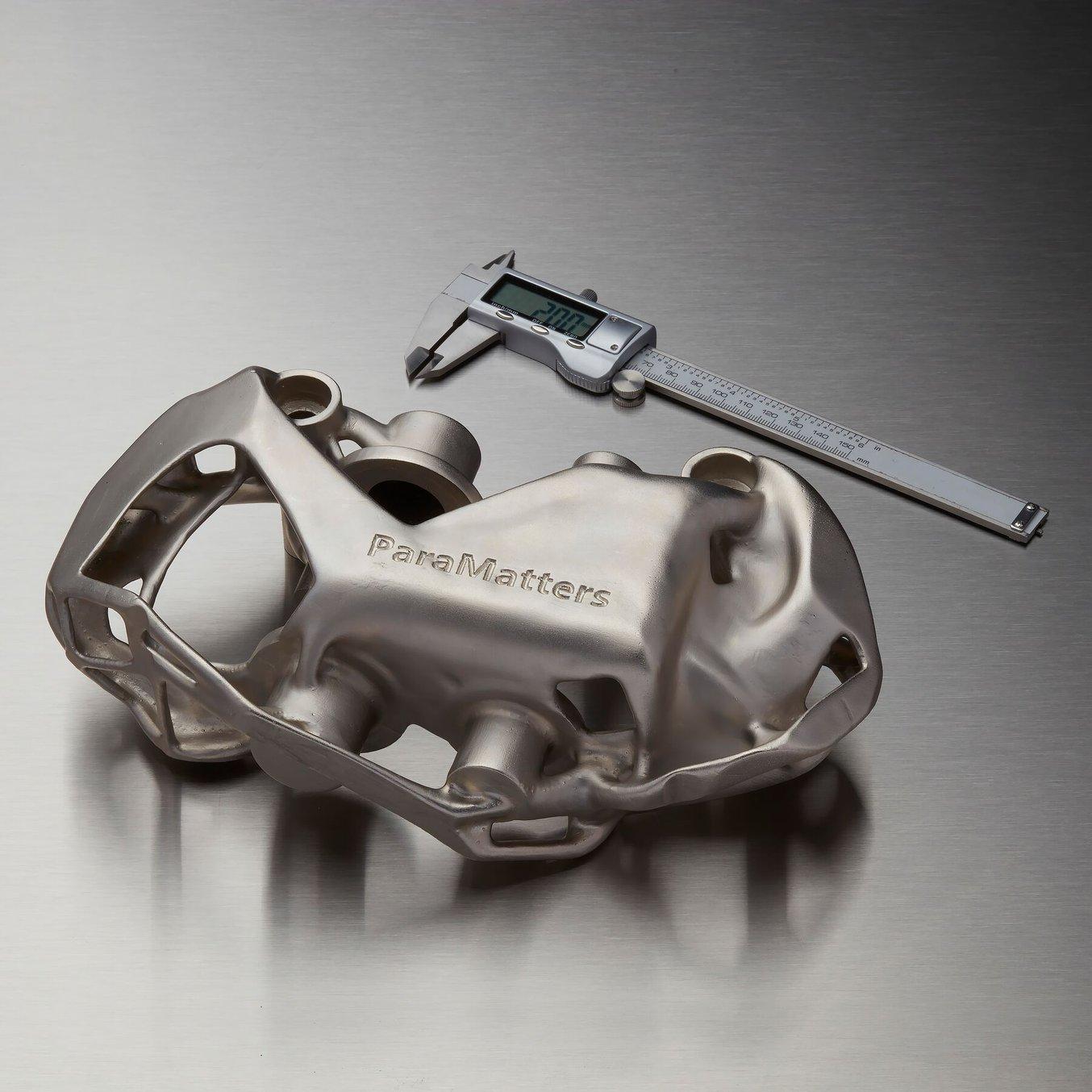
实现金属强度:SLA 部件的电镀策略和用例
请继续阅读下文,了解工程师如何将金属添加到树脂 3D 打印件,以及为何混合金属部件具备令人惊叹的应用特性,包括(但不限于)出色的最终使用强度和耐用性。
功能强大的工具轻松实现投资回报
自从十年前 Dorman 购置了第一台 FDM 打印机,Allebach 和 Tryson 陆续购买了更多打印机,不断增强现有设备的性能,并在 Formlabs SLA 打印机上使用完整的材料库。
尽管 Dorman 的全球年销售额接近 13.5 亿美元(截至 2021 年 12 月 25 日),但购买设备仍需要合理的理由。“出于产品表面光洁度和尺寸精度方面的考虑,我们决定选择 Form 2 打印机,对于我们而言,它在两个月内就能收回成本。进行成本或投资回报率评估时,我们发现无需花费两年时间,任何一台 Formlabs 打印机都可以在数月内获得投资回报。这让我们的领导层确信 3D 打印是一项值得投资的技术,”Tryson 坦言。
正是这种信心,使得 Tryson 和 Allebach 在一年多前投资购买了他们的第一台大幅面打印机 Form 3L。就像他们的其他打印机一样,Form 3L 每天运行 10-12 个小时,有时还会连夜运行。由于他们使用材料库中的各种树脂,能够匹配各种大小部件的机械性能使他们的工作流程更加高效。
只需 1 万美元就可以打印大型 SLA 部件令人难以置信。这是目前市场上绝无仅有的。对于我们而言,打印若干部件所节省的成本和时间就能快速收回打印机的投资。
Eric Tryson,Dorman Products 机械设计团队主管
3D 打印技术展望
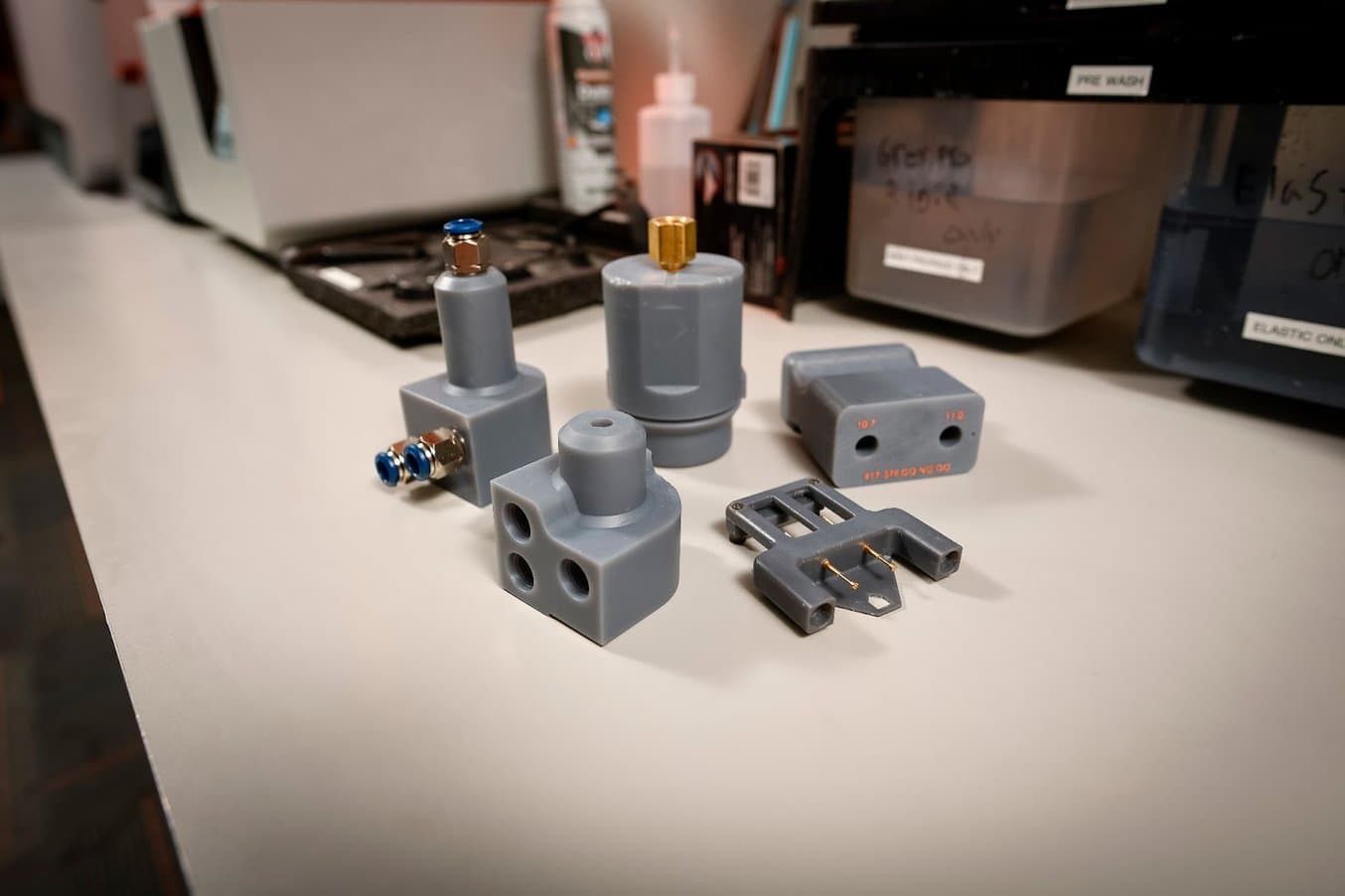
供应链困局似乎并不会很快得到解决,而且新车和二手车的价格仍然很高。随着越来越多的 OEM 转向电动汽车制造,新车型上的部件变得更轻,针对新的(通常是增材制造)制造技术进行优化,并采用新型材料制造。无论是原始设计还是售后,增材制造技术对汽车行业越来越重要。Dorman Products 在这个赛道中已经遥遥领先,但 Allebach 和 Tryson 仍然希望继续扩大优势。
“我们可以轻松设计和制造部件,通常不受传统制造过程的限制,我们一直在将经验传授给其他部门:添加凹槽或脊线并不会像机械加工那样增加成本。这使得他们完全可以按照自己的意愿设计固定装置,不再有任何顾虑,”Allebach 表示。
凭借稳固的投资回报率,并且 FDM 和 SLA 技术在该公司已经普及,团队下一步打算引入粉末床打印技术。“我们将 FDM 作为权宜之计,通过 SLA 获得了高精度和耐久性,但当涉及到高性能、低产量的功能性组件时,我们期望使用粉末床打印技术,”Tryson 表示。