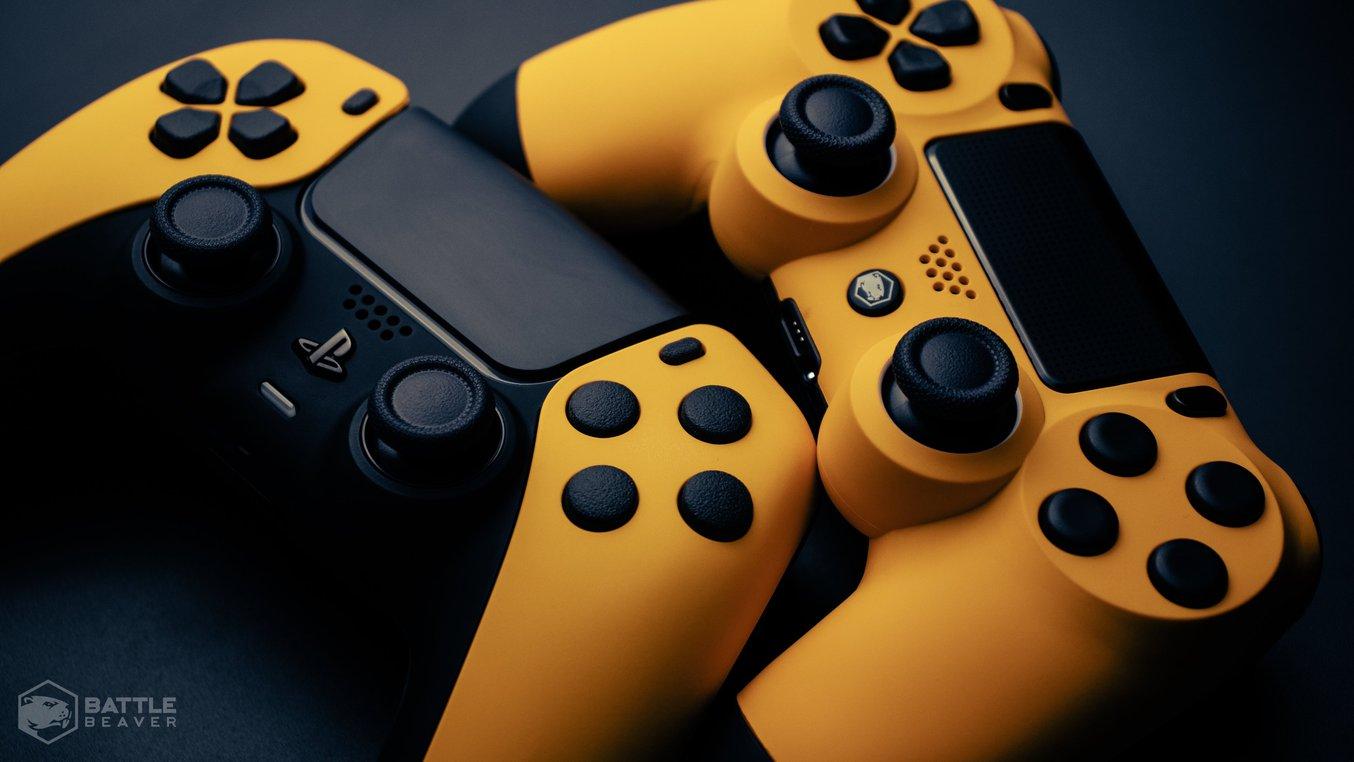
使用 Fuse 1 打印的按钮手柄(左),以及使用注射成型制作的按钮手柄(右)。
Battle Beaver Customs 致力于通过定制游戏手柄提供卓越的游戏体验。改进后的手柄具备更高的响应速度和更好的竞技效果,能够帮助玩家提高游戏潜力,在一系列游戏中取得最好的成绩。
Battle Beaver Customs 在内部为工程师配备了 3D 打印机,其中包括 FDM 机器、Form 2 SLA 打印机和 Fuse 1 SLS 打印机。最近,该团队用 Fuse 1 取代了内部手柄部件的外包工作,开始在内部制造成品部件。此举将周转时间缩短了数周,并使 Battle Beaver Customs 免受供应链问题的影响。
在这篇文章中,我们将了解 Battle Beaver Customs 研究与设计主管 Michael Crunelle 如何持续提供市场领先的游戏手柄。
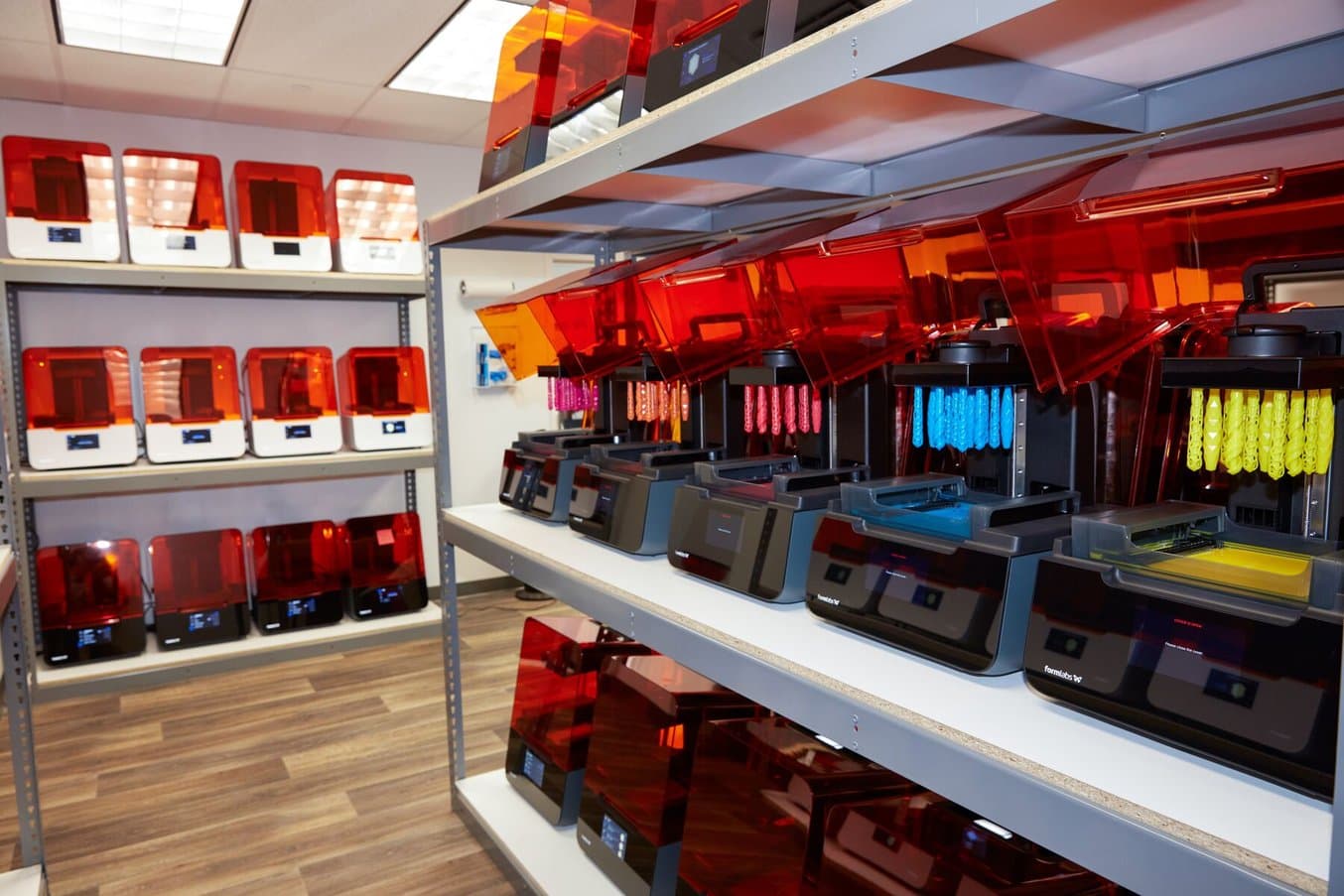
击败竞争对手,成功抢占市场
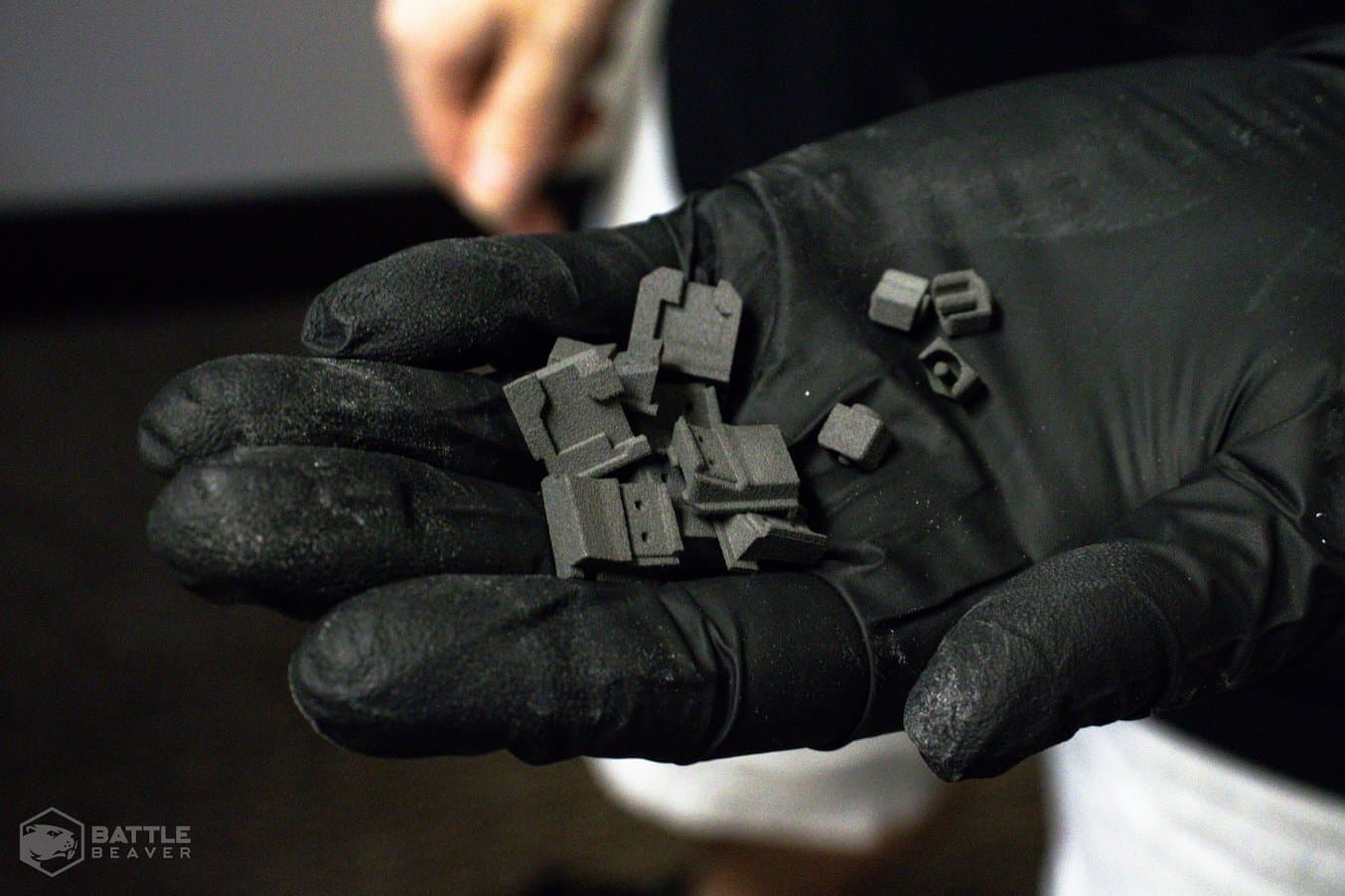
Battle Beaver Customs 高性能手柄的内部部件。
在一款游戏机的生产周期中,游戏手柄会经历多次内部重新设计。Battle Beaver Customs 等定制手柄制造商对此感到十分头疼,因为他们旧的支架和按钮设计可能不再适合新的手柄。
通过使用 Fuse 1 进行快速原型制造,Battle Beaver Customs 能够快速改进支架和按钮设计。在打造定制消费品时,更短的周转时间可以为希望领先于对手的企业带来竞争优势。Crunelle 表示,“从提出概念到生产成品部件,Fuse 1 能够帮助我们快速进行更改,加速开发流程,让我们可以远远领先于竞争对手。”
最近,他们在内部重新设计了 Playstation 5 手柄,Crunelle 加班加点制作新的支架,并表示:“在 Playstation 4 的生命周期内,[索尼]已经对 Playstation 手柄的内部结构进行了四次重新设计,而 Playstation 5 手柄也已经迭代至第二版了。这意味着我们必须改变内部平台的设计方式。对于 PlayStation 5 手柄,我们在 48 小时内就设计并打印出了新的平台,并顺利完成了改装工作。这项工作通常需要花费数周或数月的时间,但现在时间已经不再是问题了。”
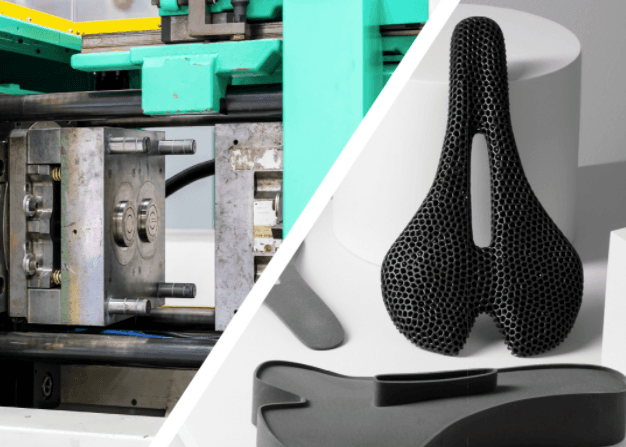
用经济实惠的内部 SLS 打印取代(外包)注射成型
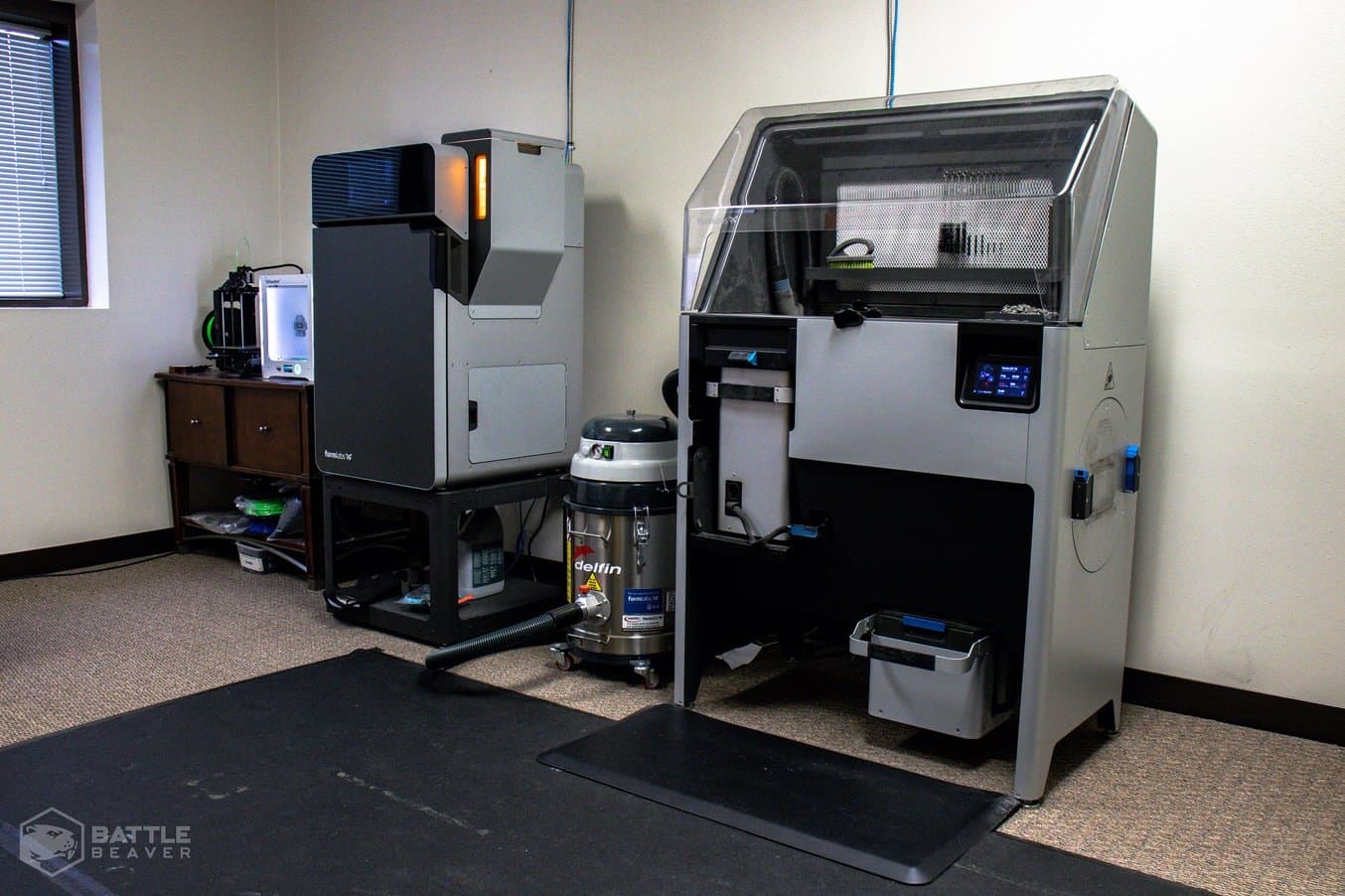
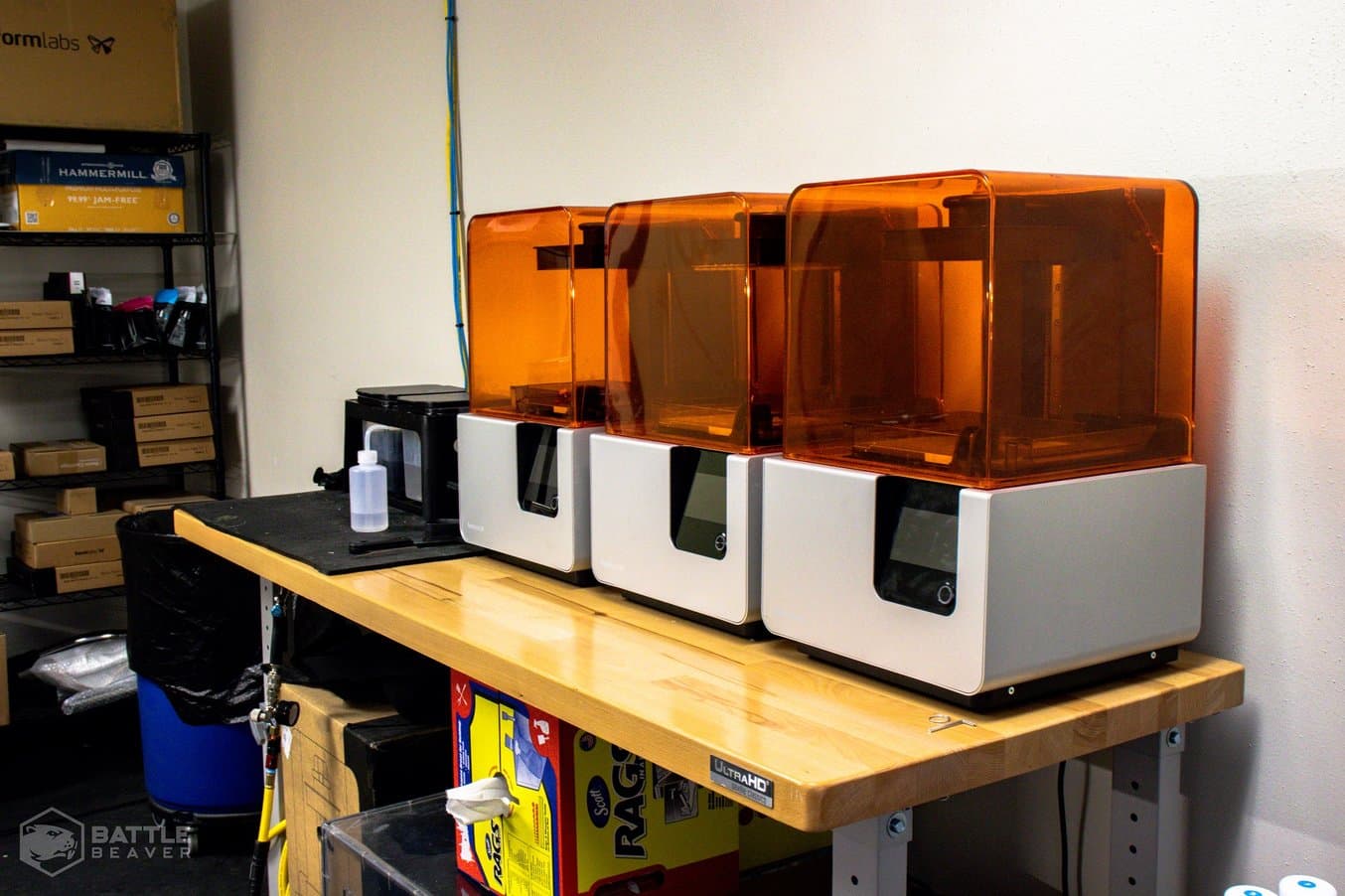
尽管该团队已转而使用 Fuse 1 来完成大部分生产任务,但仍保留了一批 Form 2 SLA 打印机来进行原型制造和一些成品部件的生产。
Crunelle 最初在 eBay 上购买了一台 Form 1+,后又将其升级为由三台 Form 2 打印机组成的机组。
据 Crunelle 称,该公司仍在使用 Form 2 打印机制造 SmartPad d-pad 替代品和一些需要光滑表面的外部部件。但由于尼龙粉末具有其他特性,该材料在内部手柄改装中占据了主导地位,Crunelle 说:“与树脂部件相比,尼龙粉末部件更便于使用环氧树脂和胶水。此外,尼龙粉末的热容量也很大。在靠近烙铁尖端时,部件并不会熔化。”
借助 Fuse 1,Battle Beaver Customs 已将所有内部支架和部件的生产转移到公司内部。在此之前,这些部件均需利用注射成型技术在中国生产,并运送至美国。每个 Fuse 1 成型室可容纳 500-800 个部件,因此团队可以按需进行批量生产,一台 Fuse 1 就可以完全取代他们的外包订单。
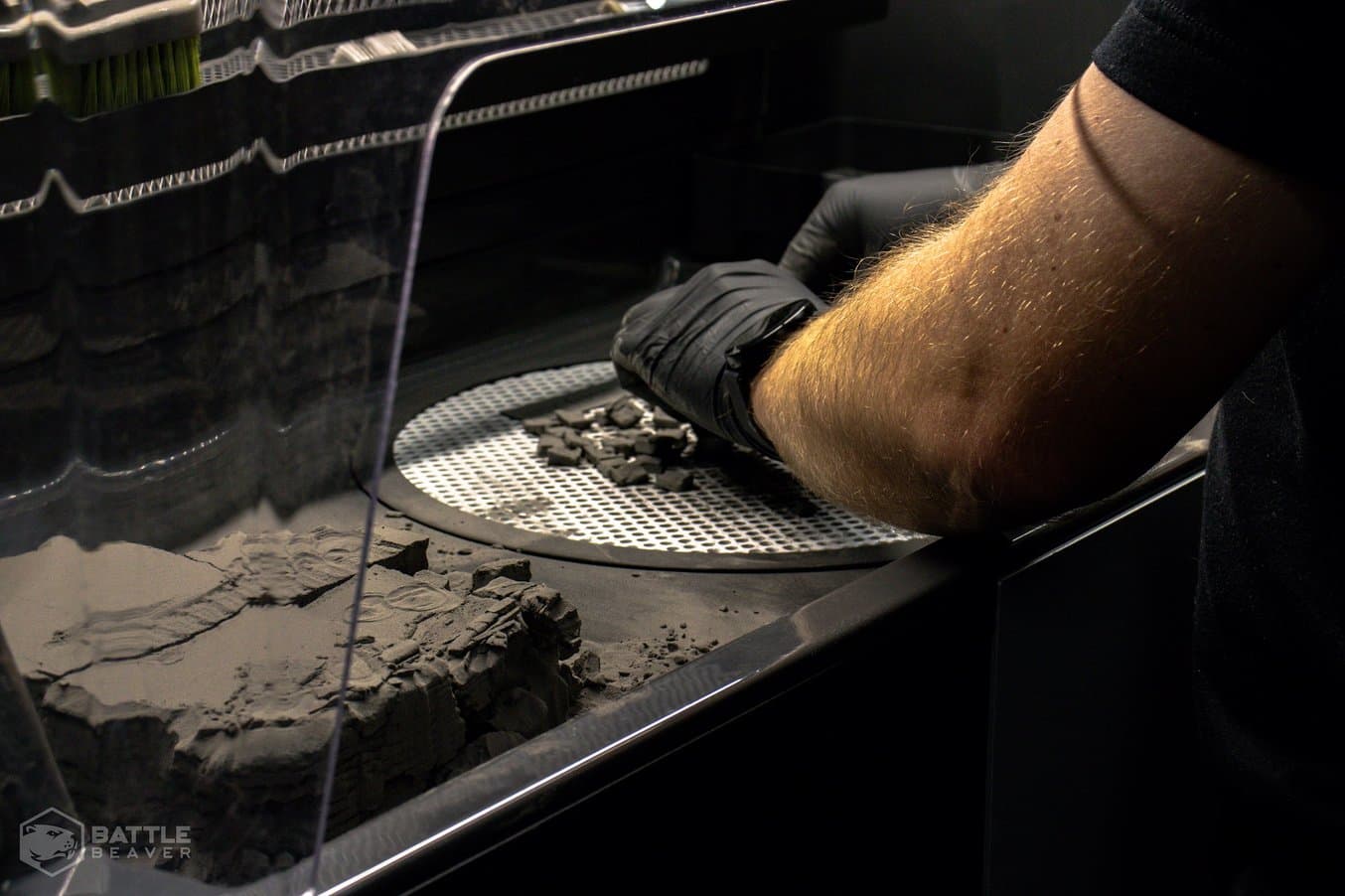
将部件放置在 Fuse Sift 中,然后在使用前进行介质喷砂处理。
通过内部 3D 打印,团队将周转时间缩短了数周,并可避免受到供应链问题和周转时间过长的影响。将新内部部件的上市时间从六个月缩短到数天,这种生产优化的另一种优势在于降低了创造新产品的风险,从而有可能在未来促进创新并开发产品变体。
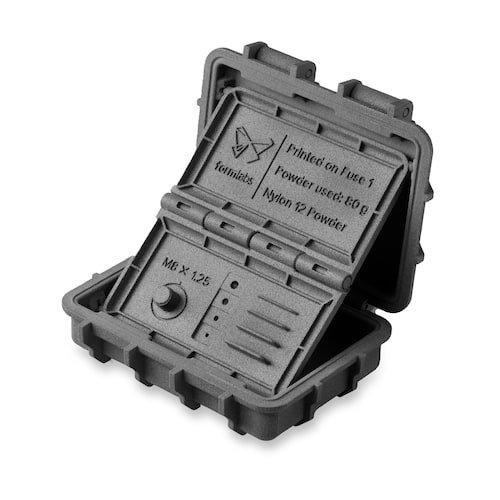
按需生产过时部件
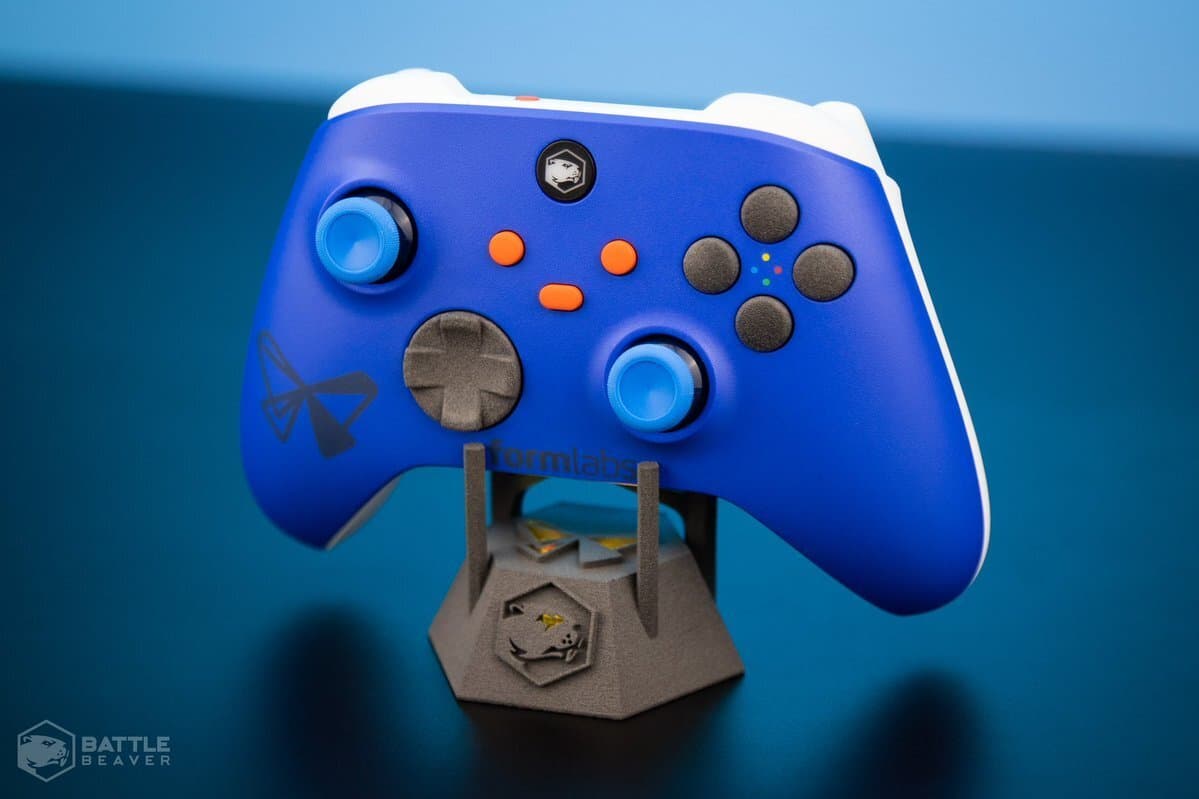
使用 Fuse 1 打印的 SLS 部件组装而成的定制 Formlabs Xbox 手柄。
此外,随着公司可支持在内部制造的手柄数量不断增加,内部 3D 打印技术还可以小批量生产过时部件。如果客户需要改装旧版手柄,Crunelle 可以加载相应的 STL 文件,打印出所需部件,然后交付给客户。由于降低了维护过时部件的相关成本,该公司现在可以生产多种产品。Crunelle 表示,“Fuse 1 可以自由打印不同的结构,我们可以根据需要进行更改,而不必担心支付模具制作费用。” 以前,受限于成本和制造时间,Battle Beaver Customs 只能针对有限数量的传统手柄型号提供支持。
最后,内部 SLS 3D 打印的一个意外优势在于其多功能性可以实现出人意料的项目。鉴于 Battle Beaver Customs 每批生产部件数量超过 500 个,进行介质喷砂处理可能非常耗时。Crunelle 使用 Fuse 1 打造了一个定制支架,并购买了可安装在喷砂装置内部的电机。这样,部件就可以自动旋转 20 分钟,从而节省了大量时间并减少了后处理的繁琐操作。
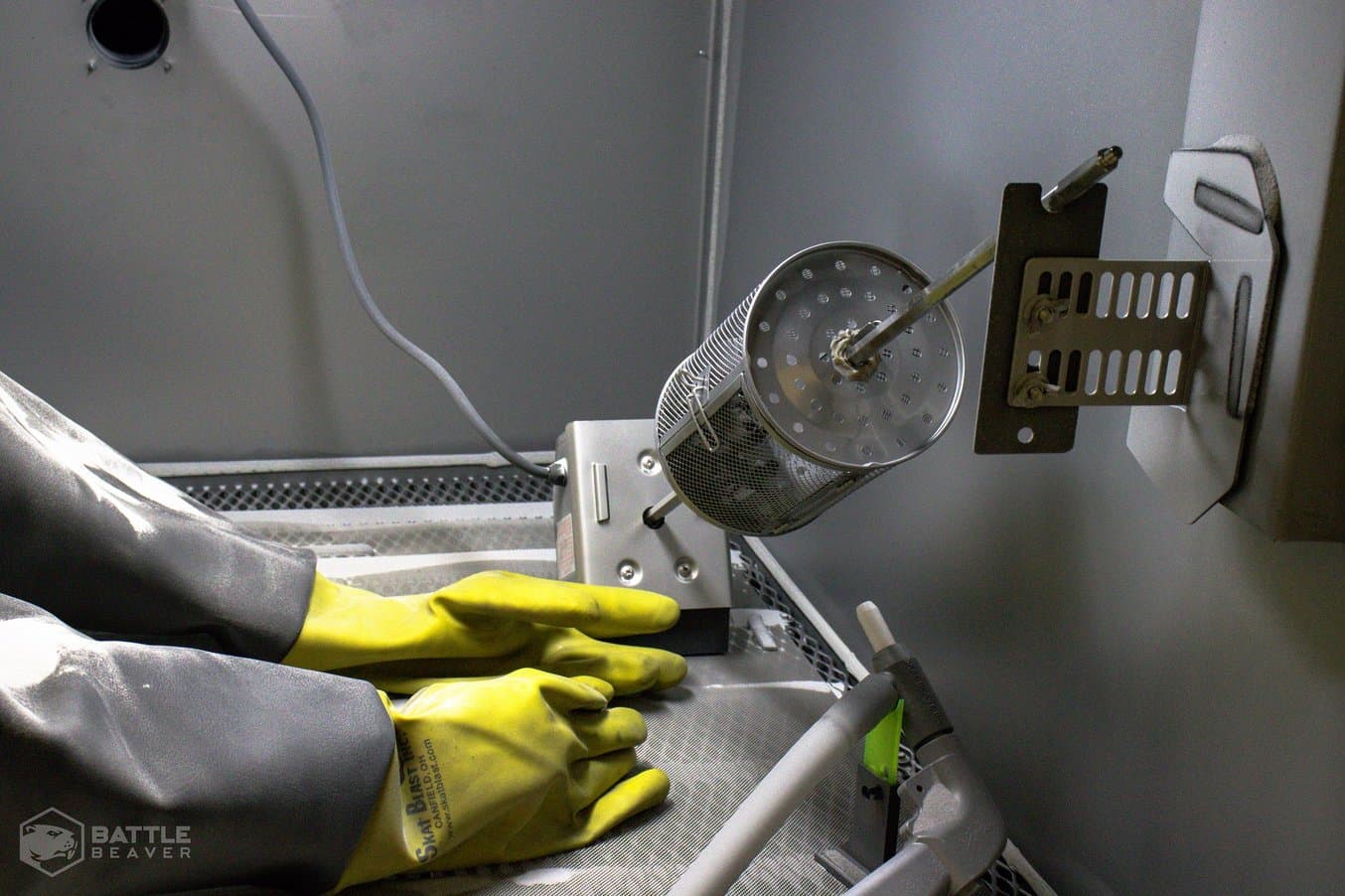
该团队打印了自己的支架,从而实现了介质喷砂过程的自动化。
Crunelle 是第一批购得 Fuse 1 的客户之一。将近 12 个月后,这台打印机已经完全融入了他的工作流程中,他说:“经过近一年的打印,这台打印机已经成为了我们工具箱中的又一得力工具。”
如需了解有关 Battle Beaver Customs 的更多信息,请在 Twitter 上关注他们。