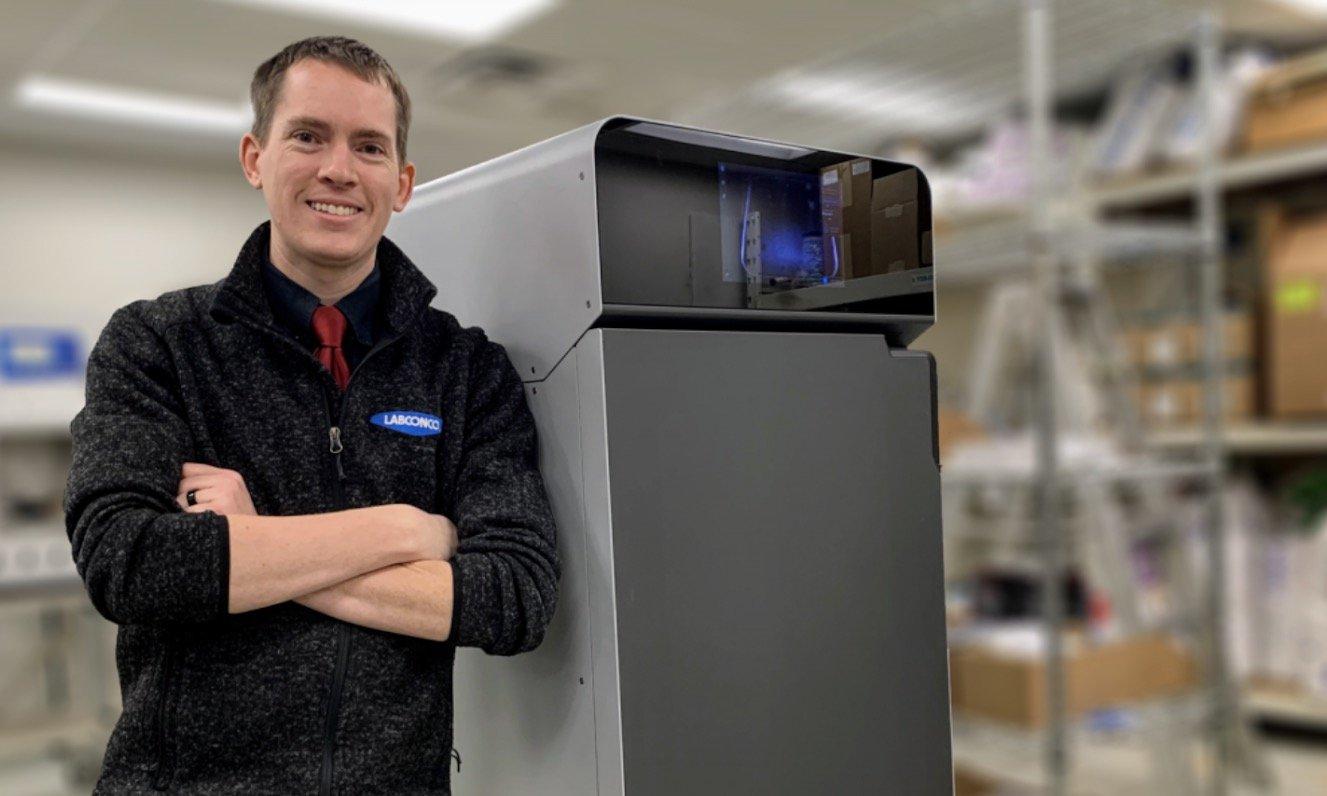
2020 年初,在 Labconco 的第一次会议上,Brent Griffith 提及 3D 打印技术而让整个会议室鸦雀无声。团队会议的部分内容是讨论新产品 Logic Vue 的小盘桩,该部件必须由注射成型制成。由于该产品是新品,供应量尚未确定,因此在上市第一年中,这种售价 15000 美元以上的模具可能只需要生产 100 个部件。由此产生的高单件成本促使该小组寻找新的解决方案。“我开口说:‘要知道,我可以使用 3D 打印技术制造这个部件,并且明天就能完成我们预计一年的工作量。’ 整个会议室鸦雀无声,”Labconco 的产品工程师 Brent Griffith 说道。
当时,Labconco 公司内部尚未购置任何 3D 打印机。第二天,当 Griffith 带着使用家中打印机所打印的几个部件版本回到公司时,3D 打印的商业价值不言而喻。
如今,Griffith 为 Labconco 管理着一个不断发展壮大的实验室,其中拥有三台 Fuse 1+ 30W 选择性激光烧结 (Selective Laser Sintering, SLS) 打印机、Fuse Sift 和 Fuse Blast、一台 Form 3L 立体光固化 (Stereolithography, SLA) 打印机和几台熔融沉积成型 (Fused Deposition Modeling, FDM) 打印机,并为食品检测、药品开发、肿瘤诊断和法医学等一系列行业制造实验室设备。Griffith 现在每周都要打印数百个部件,可用于改进加工或模制组件的性能、在供应链受阻影响生产时作为权宜之计,并为 Labconco 众多新产品的开发阶段提供帮助。
有力案例
在 Griffith 利用第一个 3D 打印盘桩组件证明了商业案例的可行性之后,他开始为办公室的工程师打印其他部件,以支持他们的开发工作,迅速就排起了长队。Griffith 表示:“很快就忙起来了。”
为了明确 3D 打印的其他应用,他和工程师 Austin Orme 开始对 Labconco 产品中使用的数千种部件、工具和组件进行审核。Griffith 表示:“我们的具体任务是找到一台机器,它具有出色的成型体积,能制造出真正的高品质部件,并能同时满足原型和生产需求。我们很快就发现,一台机器无法提供成功所需的多种能力和灵活性,并不足以完成工作。” 实验室最终添加了六台打印机,包括三台 Fuse 1+ 30W SLS 打印机和一台 Form 3L 大幅面 SLA 打印机。
“之所以购买 Form 3L,是因为我们希望获得 Formlabs 的树脂材料库。我知道这将为我们带来灵活性并创造新机遇。并且结果完全符合我们的预期。”
Brent Griffith,产品工程师
由于 Form 3L 可以使用多种材料,而且三台 Fuse 系列打印机可以实现中高产量,Griffith 能够改进现有产品,节省数以万计的模具制造成本,加快现有项目的开发速度,并按需更换部件。
替换、改进、扩展:Labconco 的 3D 打印应用
SLS 填充传感器:替换模制装配件
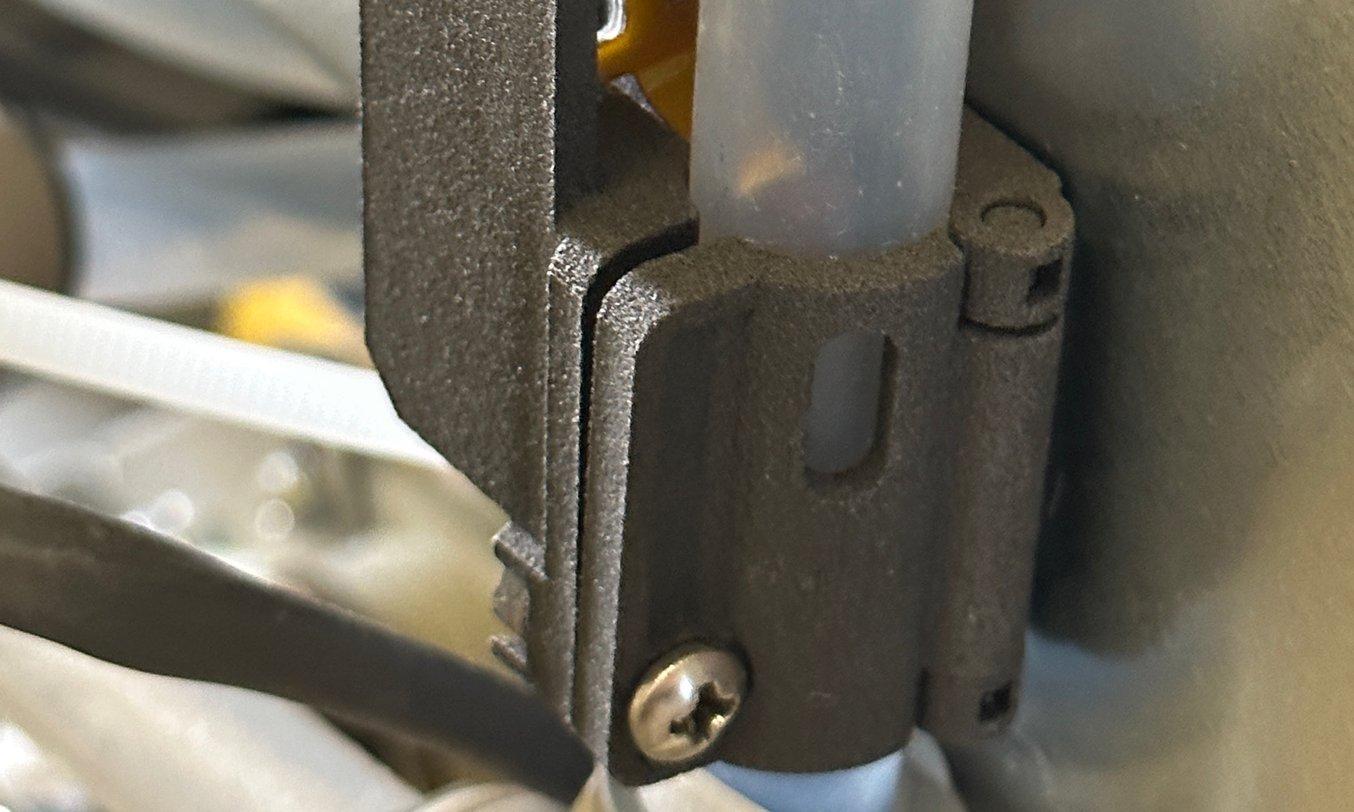
Labconco 产品工程师 Tim Grove 在看到 Nylon 12 Powder 标准样品部件后,设计出了这种具有功能铰链特征的填充传感器组件。该特征支持将部件打印为单个组件,而非多件式装配,从而减少了人工操作时间和材料成本。
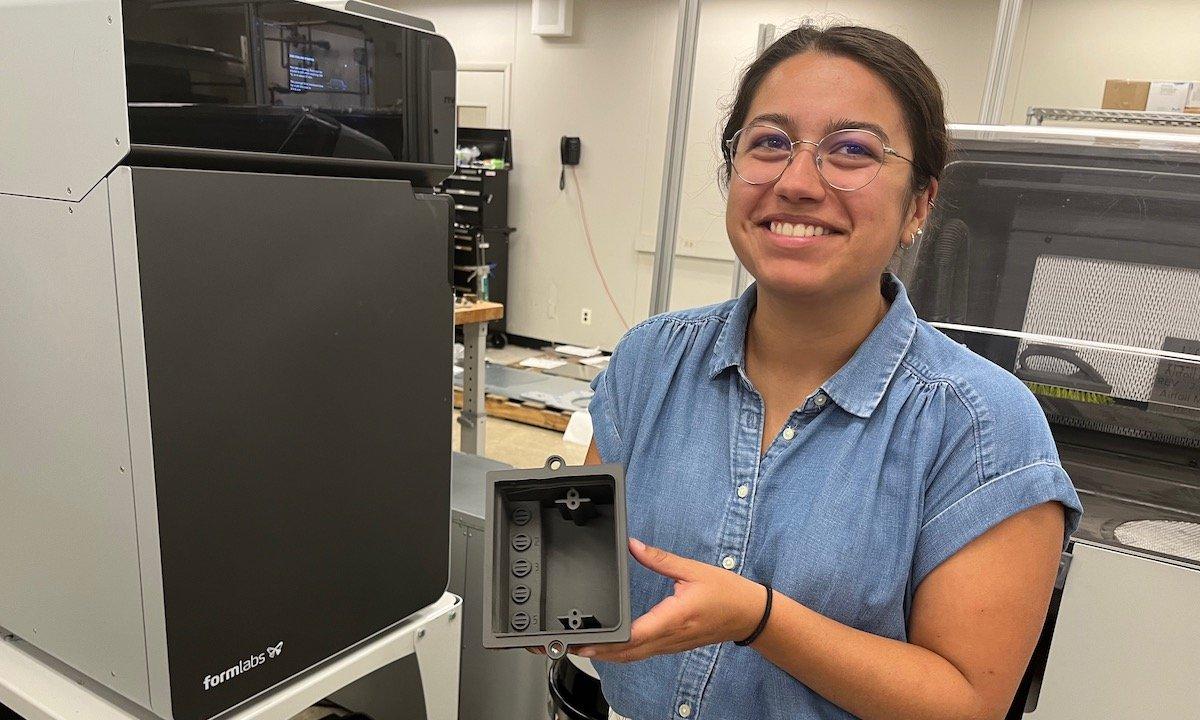
由于 Labconco 的产品工程团队能够有效地扩展他们的 3D 打印空间,因此许多团队成员都可以使用 Fuse 系列 SLS 打印机等工业技术。Griffith 表示,现在 Labconco 的多个部门都开始考虑如何将 3D 打印技术纳入其典型的工作流程中,以降低成本、提高灵活性并隔离供应链。
Labconco 的玻璃制品清洗机产线在工程设计方面取得了突破性进展,包括增材制造 (Additive Manufactured, AM) 部件。其中一个组件就是填充传感器支架,用作溢出保护的备用件。该组件的传统生产方法是,使用注射成型制造两个独立的部件,然后使用销钉将两个部件固定在一起进行组装。
然而,Labconco 公司的产品工程师 Tim Grove 意识到,通过 SLS 3D 打印技术进行制造可以节省成本和时间。受 Formlabs 自有的 Nylon 12 Powder 标准样品部件中所用铰链设计的启发,Grove 开始重新构思填充传感器支架,旨在简化装配并消除与订购多种工具相关的费用。
通过与 Griffith 进行迭代合作,Grove 制作了该部件的多个版本,并确保功能完美和性能完整。
“从打印机中取出后,铰链就能够正常工作了,随时可以投入使用。如此一来,既节约了成本,又提高了生产的灵活性。对我们而言,Fuse 的 Nylon 12 Powder 是一种很出色的中间聚合物。我们明确了该材料的多个应用领域,效果非常好。”Griffith 表示。
SLS 填充传感器 | 组件数量 | 装配人工操作时间(每 50 个组件) | 每件成品成本(包含人工) | |
---|---|---|---|---|
模制 | 3 | 1 小时 | 4.45 美元/ea + 模具制作 | |
SLS 3D 打印 | 1 | 0 | 2.56 美元/ea |
SLA 鼓风机叶轮:解决供应商淘汰问题
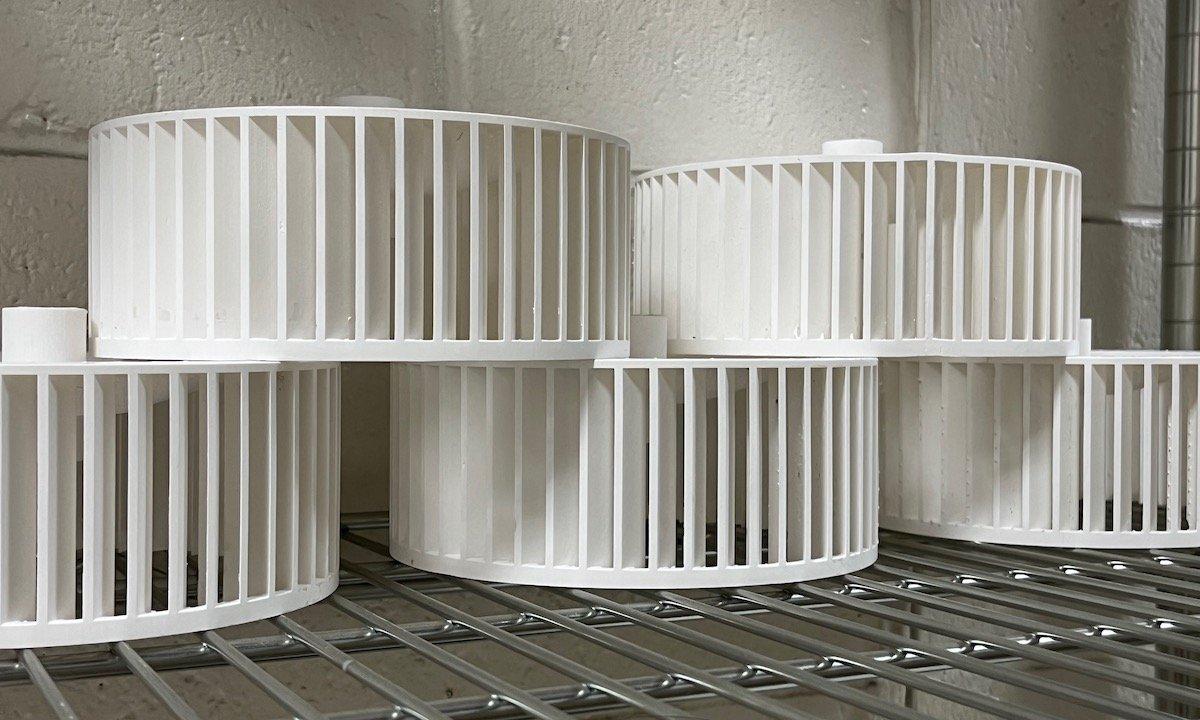
该组件用于 Labconco Kjeldahl 谷物分析产品中,以前均采购自外部供应商,直至供应商决定淘汰该部件。Griffith 对该组件进行了逆向工程设计,然后连续一个多月每天都在 Form 3L 中使用 Rigid 10K Resin 打印新版本,重建替换组件的库存,并避免了供应链问题。
在 Labconco 用于分析谷物的 Kjeldahl 设备上,团队正在与一家外部供应商合作生产一种用于制作关键鼓风机叶轮组件的模具。由于数量较少,供应商决定在模具使用寿命到期后淘汰该部件。
Labconco 面临诸多挑战,包括寻找新供应商、等待设计和生产新模具以及成型运行,还有高昂的材料和人工成本。“我们研究了十几种不同的解决方案,但没有一种能达到我们的要求,尤其是在化学兼容性方面。因此,我最终制作了一个副本,对其进行逆向工程设计、优化,并使用 Rigid 10K Resin 进行打印。经过测试以确保组件能保持稳定后,我们认为这是最佳解决方案,” Griffith 说道。
新购置的大幅面 SLA 打印机 Form 3L 及时交付,使得他们可以连续 40 天打印逆向工程的鼓风机叶轮,从而重新建立该部件的库存。
“Rigid 10K Resin 一直是制造多个组件的首选材料。其化学兼容性符合我们对酸的要求,特别是在存在蒸发硫酸的情况下。通过改用增材制造技术,我们在验证供应商和不合格的材料方面,节省了数百个小时。在这方面而言,这是一个掷地有声的商业案例。”Griffith 说道。
SLA 鼓风机叶轮 | 成本 |
---|---|
初始模制 | 178.77 美元 |
重新设计并使用 Rigid 10K Resin 打印 | 52.65 美元 |
SLS 轴承保持架分离器:从 500 美元到 20 美元
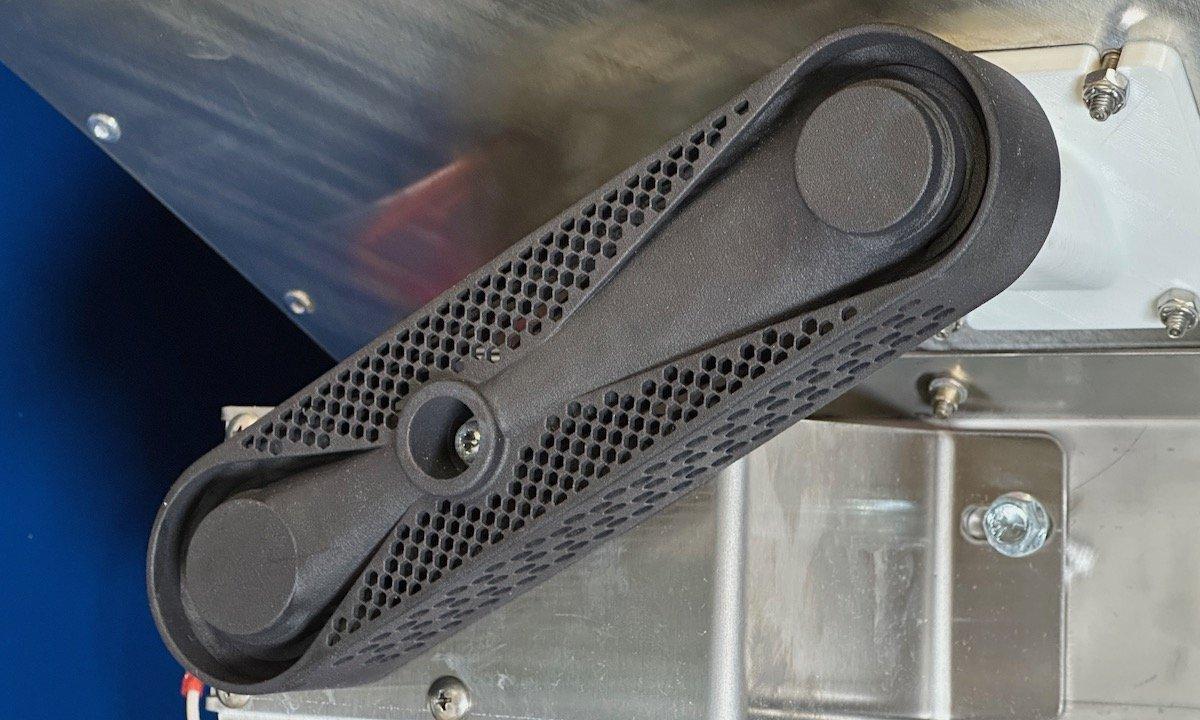
Griffith 原本计划打印出与该组件完全相同的部件,而外部机械师对此的报价为约 500 美元。相反,他运用在宾夕法尼亚州立大学增材制造和设计项目中学习的原理,重新设计了部件,充分利用了 SLS 3D 打印技术提供的几何可能性。新部件的成本约为 21 美元,帮助 Labconco 节省了数百美元,并将周转时间缩短到两天以内。
虽然有些部件可能相对简单,但如果采用传统制造方法仍然成本高昂。针对用于将两个轴承分开以防止轴承相互拉扯的分离器,一位机械师其进行了报价,即约为 500 美元。该部件用于制造新产品,而 Labconco 已经证明了其在 3D 打印实验室中的用例。Griffith 立即开始使用 Fuse 1+ 30W 打印分离器,并将价格降低到 45 美元左右,约为机械师外包报价的十分之一。
优化的脚步并未就此停下。Griffith 运用了他在宾夕法尼亚州立大学增材制造与设计专业攻读研究生期间所学的原理,将该流程从 1:1 替代重新构建为整体优化改造。
“我一直在学习如何利用增材制造的机会性和限制性。与其发问‘我们能使用增材制造吗?’不如思考:‘我们应该使用增材制造吗?’ 在这种情况下,我们可以制造出 1:1 替代品,但如此一来,我们未能发挥出 AM 的优势。Fuse 系列打印机几乎没有真正的几何限制,借助这些设备,我可以疯狂地尝试新事物。”
Brent Griffith,产品工程师
他尝试使用衍生式设计减少整个部件所需的材料,同时保持分离器的安全功能,以确保操作人员的人身安全。一天之内,他就完成了设计的修改和优化,与此同时,Labconco 开始在内部使用 SLS 3D 打印部件,单件成本约为 20 美元。
“3D 打印在几何形状方面为我们带来了巨大的优势。如果减轻部件重量或应用不同的设计技术,我们就能以前所未有的方式组合部件。我们可以在内部进行制造,并节省大量资金,”Griffith 说。
SLS 轴承保持架分离器 | 成本(包含人工) | 周转时间 |
---|---|---|
加工 | 485.82 美元 | 2-3 周 |
1:1 SLS 替换件 | 43.50 美元 | 29 小时 |
针对 SLS 优化 | 21.08 美元 | 28 小时 |
测试中的 SLS 部件:减少组件数量并改进功能
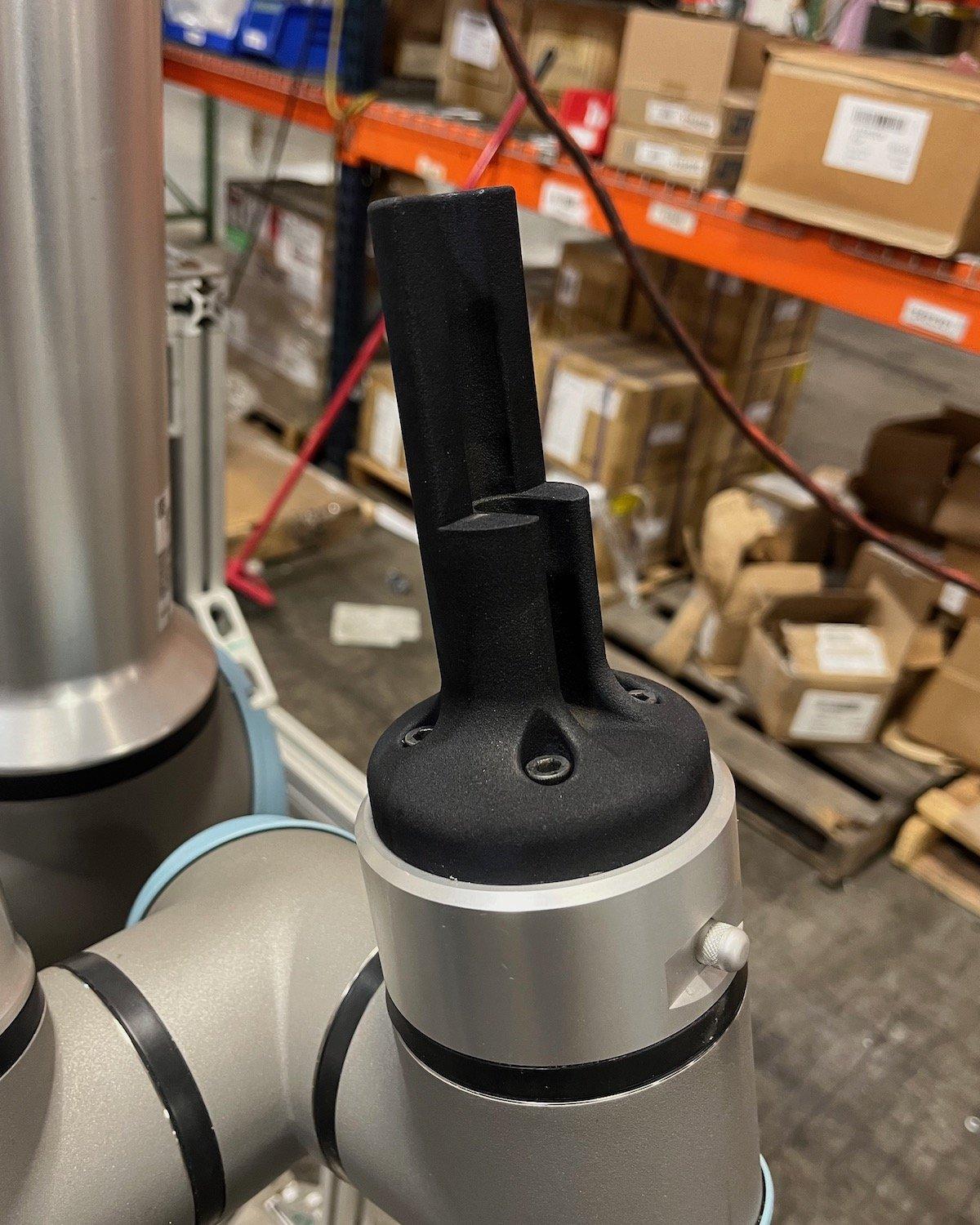
为了帮助 Labconco 顺利过渡到将实践任务与机器人驱动器相结合的混合工作流程,Griffith 及其团队设计了定制模具和执行器,然后使用 Nylon 12 Powder 在 Fuse 系列打印机中打印出来。
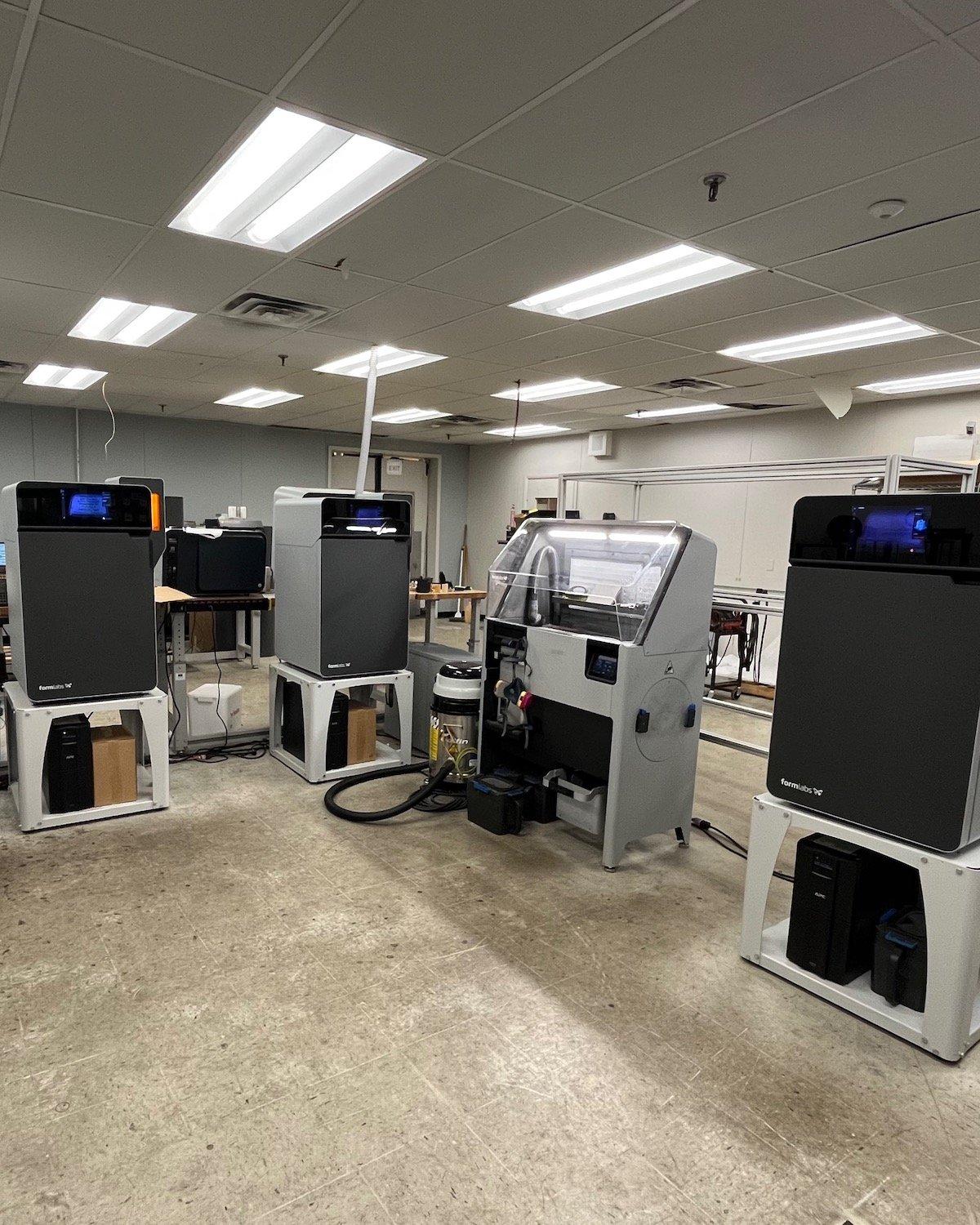
Fuse 系列 SLS 3D 打印机体积小、能耗低,这意味着如果 Griffith 和团队计划扩大此类坚固耐用的 SLS 部件的应用范围,他们可以通过扩大 SLS 操作规模来实现这一目标。
Labconco 并未停下过追求卓越的脚步,该公司还对其旗舰产品之一生物安全柜的关键部件进行了测试。这些安全柜基于特定的气流模式和 HEPA 过滤器,对保护人员和柜内处理的产品至关重要。为确保获得最高水平的性能,这些过滤器在完工出厂之前,都要经过严格的测试和认证。
过去,这种测试过程严重依赖人工操作,因此存在变化性和局限性。然而,Labconco 采用了一种变革性方法,利用机器人系统的强大功能,以无可挑剔的精度对每个过滤器进行自动化扫描。在转而使用自动化的过程中,必须为用于执行测试的机械臂开发定制模具和末端执行器。传统的制造方法不仅成本高昂,而且可能需要数月时间;由于所需部件数量较少,因此在 Fuse 系列机器上进行 3D 打印以制造部件是这种变革性方法的重要一环。
通过使用 Fuse 1+ 30W 自行生产 SLS 部件,Labconco 显著提高了这些组件的日利用率,进而增强了产品安全测试的准确性和可靠性。Labconco 采用增材制造技术不仅简化了操作,还能确保其产品的安全性和性能。
执行器组件 | 成本 |
---|---|
加工 | 508.32 美元 |
SLS 3D 打印 | 73.44 美元 |
通风柜组件:中批量 SLS 生产,敏捷性增强
Labconco 是首家实现通风柜生产商业化的公司,如今这已成为其最重要的产品部门之一。通风柜是大型化工、制药或农业企业不可或缺的设备。
其中一个组件就是机械式窗扇制动器,用于防止用户将通风柜罩扇打开超过指定点(从而节省能源成本),该组件以前采用注射成型制成。大量订购单一模具生产的产品限制了 Labconco 为大客户修改或定制订单的能力。模具会磨损,而且在更换模具时,供应商有时并不那么可靠。为了解决供应链问题,他们开始使用 Fuse 1+ 30W 打印这些窗扇制动器,现在 Griffith 每周使用 Nylon 12 Powder 生产 50 到 100 个此类组件。
“如果采用模塑方法制造部件,就无法轻易进行任何修改。虽然这种情况并不常见,但我们过去也曾使用过注射成型的部件,结果却让我们大伤脑筋,因为在我们拿到部件并将其投入使用后,它们就开始断裂或无法正常工作。工程师们现在意识到,如果转向使用 3D 打印制作一些部件,那么在需要时重新设计就不会那么麻烦,而且更改的选择余地也会更大。不能总是用金钱来衡量这一点,而且我认为增材制造还有很多‘无形’的好处,但通常被人们忽视了,”Griffith 表示。
将 3D 打印技术引进公司内部的另一个优势是,帮助刚进入职场的年轻员工树立信心。摆脱了订购新模具所需的绝对完美要求,他们更愿意尝试新事物或提出新想法。“年轻工程师们并没有 20 年的工作经验,他们无法通过查看部件就能保证‘这个能行’。借助 3D 打印的能力,他们可以进行一些尝试,甚至尝试很多事物,如果失败了,也不会有太大损失,甚至不会有任何损失,这只会增强他们的能力。让他们专注于针对任何特定问题找到最具创造性的最佳解决方案,这正是我们希望他们在工作中的思考维度,而 3D 打印技术就是其中的重要组成部分,”Griffith 表示。
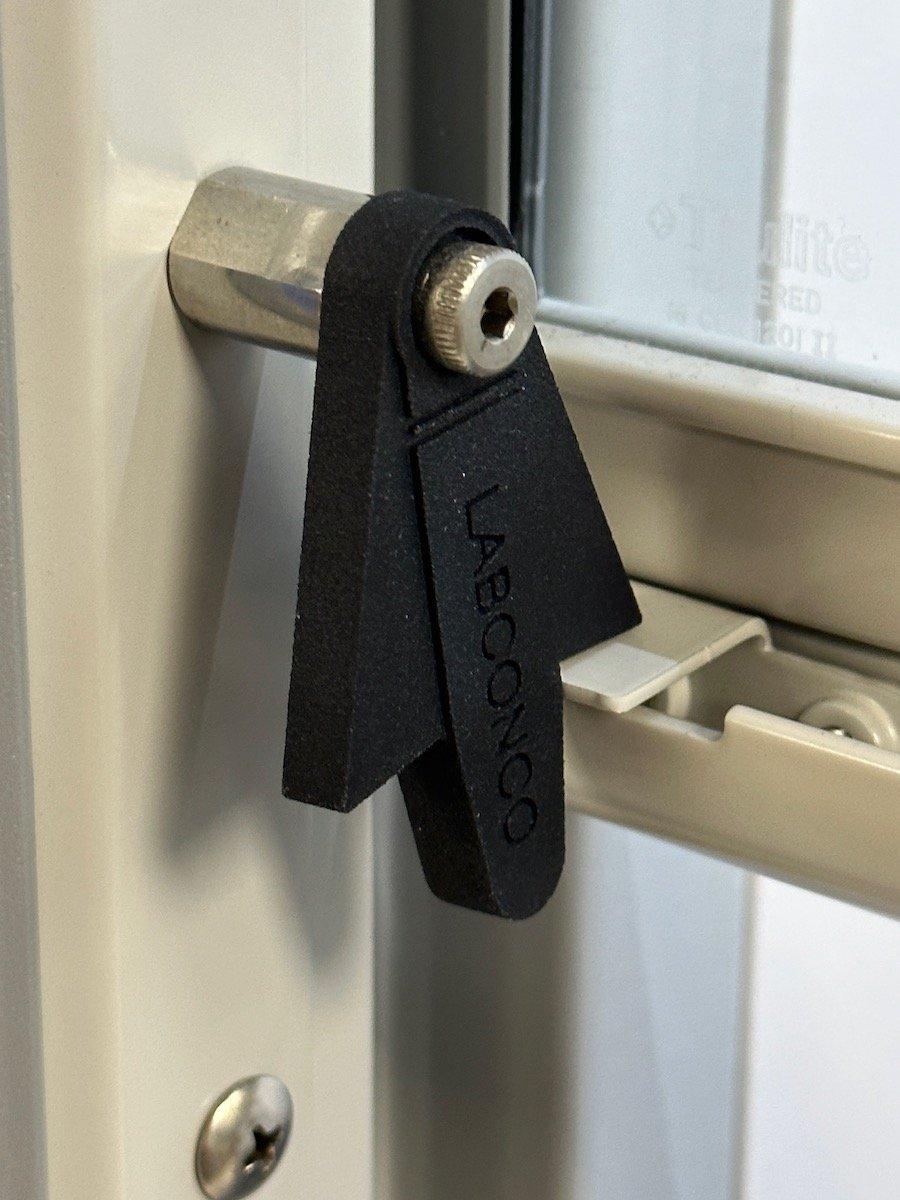
Griffith 每周在 Fuse 1+ 30W 中使用 Nylon 12 Powder 生产 50 到 100 个此类窗扇制动器组件,避免了受困于一个模具工作流程的成本和风险。
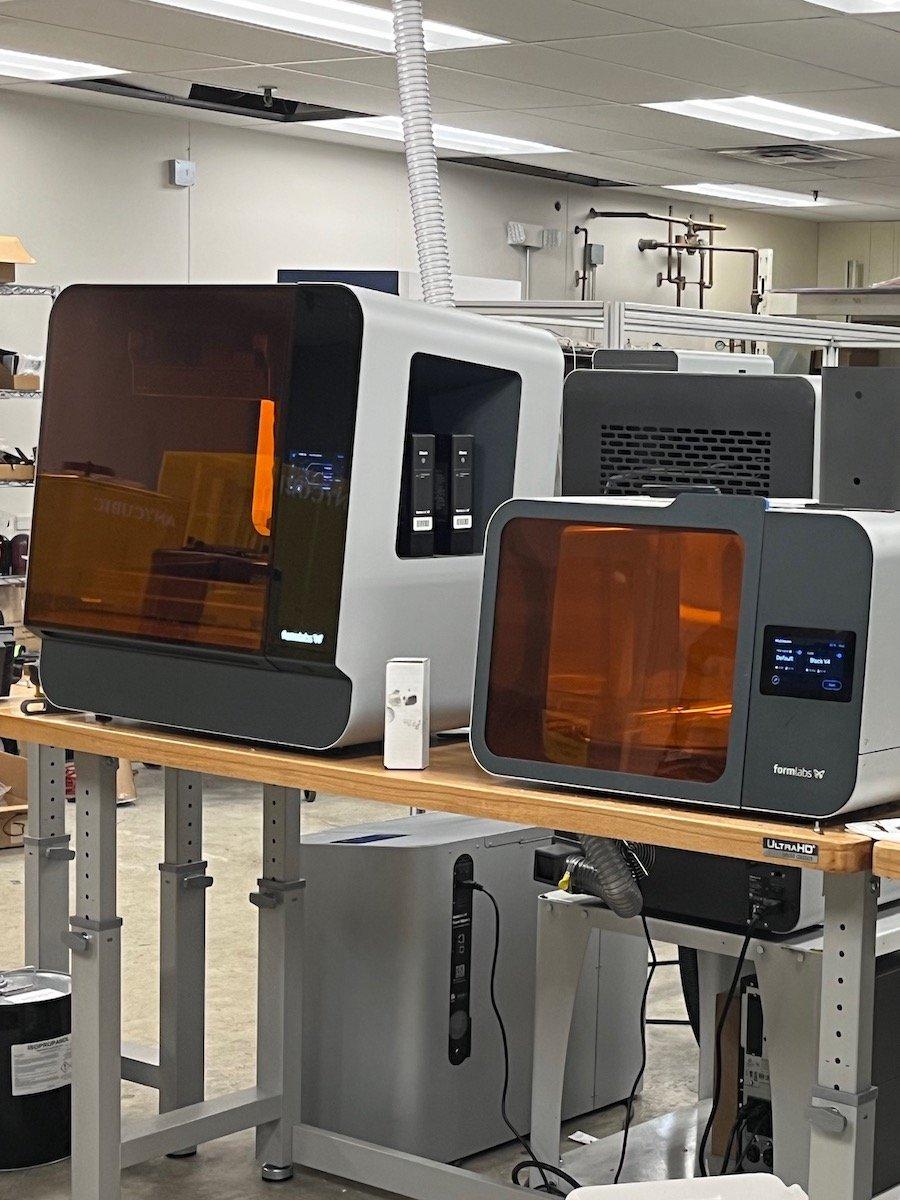
SLS 和 SLA 打印机(如图所示的 Form 3L 和 Form Cure L)的易用性意味着,新入职的年轻员工可以对新技术充满信心,并有能力提出新的想法。
Labconco 的 Fuse Blast 完善了 SLS 生态圈
由于 SLS 部件的周产量超过 100 个,介质喷砂和清洁等手工后处理程序需要花费数小时,而这些时间更应该用于价值更高的设计和工程任务。Griffith 说:“公司希望我们集中精力寻找新机会,重新设计部件,使其更加出色,并降低成本,而不是站在那里手动清洁所有这些部件。”
除了高成本的自动喷砂系统,Labconco 还引入了 Fuse Blast,从而完善了其 Fuse SLS 生态圈。只需十分钟的设置时间,Griffith 就能对两个完整 Fuse 系列成型室内的部件进行自动清洁和介质喷砂处理。“安装非常简单......它的尺寸几乎与我们的手动喷砂系统相同。因此,如果拥有充足的人员和空间来安装手动喷砂系统(每家拥有 SLS 的公司都应如此),你就会有足够的空间来安装 Fuse Blast,不会有任何问题,”Griffith 表示。
更出色的部件质量和性能
Labconco 的需求团队立即注意到了表面光滑度和部件质量的不同。
“Fuse Blast 立即带来了巨大的变化,每一位原型制造工程师在拿到我交付给他们的部件时,都开始意识到部件有所不同,甚至无需我告诉他们我们已经实现了自动化后处理。他们立即就注意到了,部件上的残留粉末量减少、触感更光滑柔顺、外观也更出众。这使部件的质量发生了肉眼可见的变化。”
Brent Griffith,Labconco 产品工程师
光滑的表面和无任何粉末残留对部件性能产生了意想不到的影响,SLS 打印部件在 Fuse Blast 中经过清洁后,使成品机器运行得更加顺畅。Griffith 说:“实际上,我们生产的一些组件的性能略有提高,因为它们更干净了,特别是体现在我们其中一个产品的初始调试运行阶段中。”
后处理结果与他们使用的另一种高成本自动喷砂系统的清洁结果几乎完全相同。“我无法用肉眼分辨出两者之间有什么区别。[Fuse Blast] 的效果和能力绝对物有所值,”Griffith 继续说。
后处理时间缩短,设计优化时间延长
Fuse Blast 的自动化不仅仅是消除了手动喷砂处理的时间,还减少了 Griffith 及其团队在 Fuse Sift 上花费的时间。过去,在 Fuse Sift 中花费更多的时间可以通过缩短手动喷砂处理时间来获得收益。现在,即使部件完全被粉末包裹,Fuse Blast 通过自动周期运行,也能提供洁净部件。“我不太关心 [Fuse Sift] 清理的粉末量,因为我对 Fuse Blast 的能力充满信心。在 Fuse Sift 中彻底清洁部件已经不能节省时间了。如果在 Fuse Sfit 中进行更彻底的清洁,那么我们回收的粉末量与为此投入的人工成本相比,根本不值一提,”Griffith 说。
对于周产量稳定在 50 个的部件而言,Griffith 的团队需要进行手动喷砂处理,并用清管器清理每个部件上的三个孔。借助 Fuse Blast,他可以在设定好自动周期后离开,20-30 分钟后回来,就会得到一组完全洁净的部件。“Fuse Blast 是一款出色的设备。它在清洁孔洞方面非常出色,这可能就是我们节省时间的一大法宝,”Griffith 说。
扩大 3D 打印任务规模
Griffith 和他的同事系统地研究了 3D 打印技术,初次审核就证明了他们购置的前六台机器的使用可行性。随着持续节约成本、减少劳动力以及改进其大量组件目录设计,他们正在寻求扩大其 3D 打印能力。
“每当一个部件出现在我的办公桌上时,我的第一个问题就是:‘我们是否还能改进这个部件,AM 技术是否可以有所帮助?’ 我认为寻找这些机会是我们能够脱颖而出的原因,也是我们在许多组件制造过程中节省最多资金或削减最多成本的原因,”Griffith 说。
这些好处对于整个公司来说都是显而易见的,借助内部小批量制造的强大能力,与特定或利基应用客户合作的团队可以胸有成竹地提出颇具成本效益的解决方案。“即使客户只需要 5 个、10 个或 50 个定制部件,我们通常也能以经济高效的方式满足需求。我们能够对市场需求做出快速反应,”Griffith 表示。
从让整个会议室陷入沉默的第一个用例开始,Griffith 已经为各种规模的制造商建立了商业案例,使用 SLA 和 SLS 3D 打印技术进行内部生产可以实现全新应用,提高业务成功率、优化产品性能、避免供应链中断,以及降低成本。
如需了解更多有关 SLS 和 SLA 内部应用的信息,请与我们的制造销售团队预约咨询。