工程原型需要进行广泛的功能和可用行性测试,以了解部件或装配件在受到应力和现场使用条 件的影响时的运转情况。3D 打印则能够为打造可承受热应力、化学应力和机械应力的高性能原 型提供工程塑料。有了 3D 打印,设计不必止步于生产开始时。通过Formlabs中国立体光刻3D打印,工程师可以创建小批量生产,定制一次性解决方案,以及用于工程、设计和产品 验证测试(EVT、DVT 和 PVT)构建的子组件,以测试可制造性。
迪嘉智造是一家大型注塑解决方案提供商,每年为250多家客户提供服务。随着3D打印技术的普及,迪嘉尝试通过利用3D打印注塑成型模具,缩短时间、降低成本,并取得了初步成效。迪嘉为了满足客户小批量生产的需求,经过不断研究和创新,利用3D打印注塑成型模具将大约100件的小批量注塑成型部件的周转时间大大缩减,从四周缩减为三天!
大多数情况下,注塑成型所用的模具都是由钢或铝等金属材料制成。但对于小批量生产来说,制作金属模具既昂贵又耗时,成本非常高。通过3D打印,可以解决在传统生产模式中,小批量生产成本高的问题。与加工铝模具相比,利用 Formlabs 3D打印机制造小批量注塑成型模具可以节省成本、劳动力和时间,并能与公司现有的 Babyplast 工业级注塑成型机无缝搭配使用。
迪嘉对多种材料进行测试。其中包括了Formlabs 的 Rigid 10K 树脂材料,它是一种玻璃填充树脂,非常坚硬、坚固并且耐热、耐化学腐蚀,符合注塑模具所需要的性能。此外,使用 Form 3 搭配 Rigid 10K Resin 打印的部件具有光滑的哑光表面,从而使注塑成型件的表面洁净光滑。
3D打印技术帮助迪嘉极大的缩短了周转时间。按照传统工艺,采用CNC加工的金属模具进行注塑成型需要3–4周的时间,而迪嘉的生产车间有多台3D打印机和注塑成型机,只用3天的时间就能交付数百个工件。
迪嘉使用Formlabs中国立体光刻3D打印工作流程参考:
1、测试
对ABS、PP、PC+ABS和PC材料的注塑成型部件进行了测试。
2、打印模具以及后处理
在设计好模具之后,迪嘉的工作人员用一天的时间打印模具及进行后处理,在装配车间用差不多半小时的时间组装模具,然后开始在注塑成型机上进行注塑成型。
3、注塑成型
注塑成型开始后,每个部件大约需要3分钟时间彻底完成。迪嘉将每个模具限定为大约进行100次注塑,如果是较大批量的订单则打印多个模具。这样,在较短的时间内,就能完成订单的生产
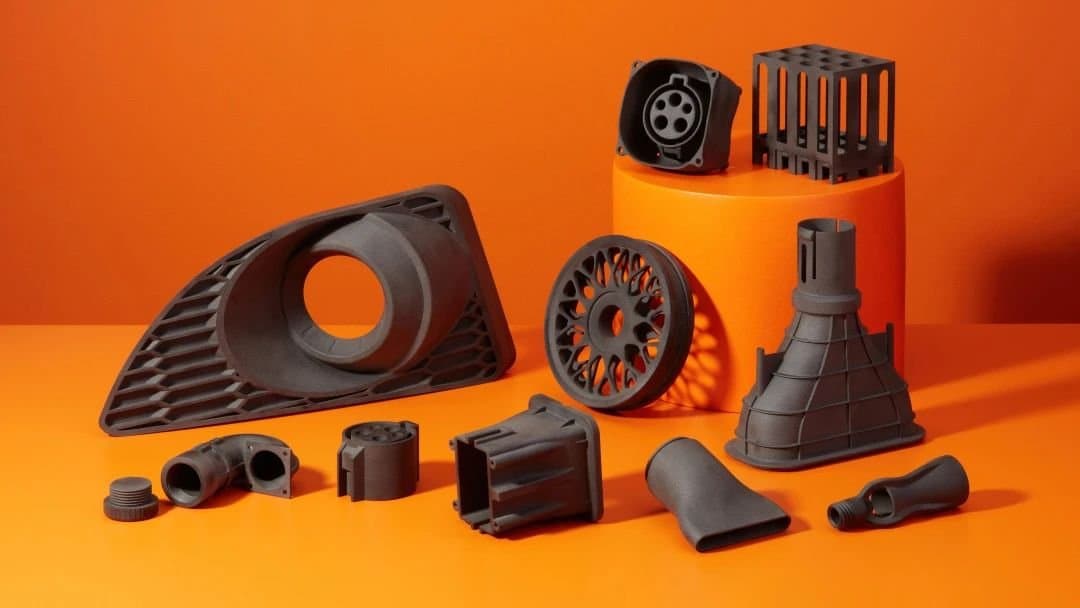