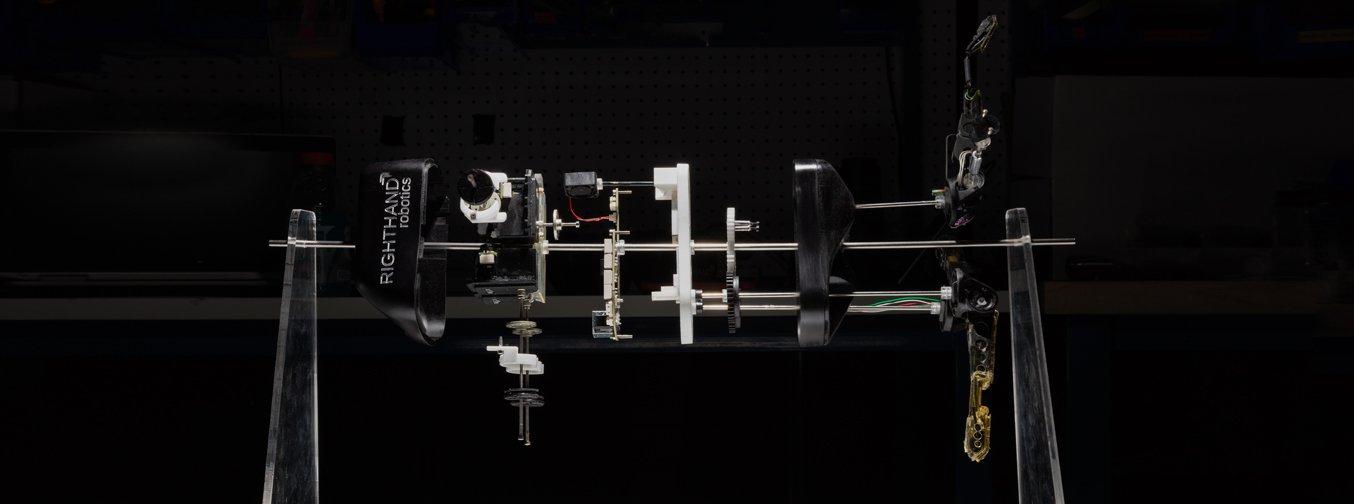
塑料是生产最终使用部件和产品时最常用的材料,从消费品到医疗器械都能看到塑料的身影。塑料是一种用途广泛的材料,其中包括数千种聚合物可供选择,每种聚合物都有其特定的机械性能。但塑料部件是如何制造的呢?
业界已开发出多种塑料制造工艺,涵盖丰富的应用、部件几何形状和塑料类型。对于任何从事产品开发的设计师和工程师来说,熟悉当今可供选择的制造方案以及部件制造的未来发展方向都至关重要。
本指南概述了最常用的塑料部件制造工艺,并为您提供指南以便针对应用选择最佳方案。
如何选择合适的塑料制造工艺
在为您的产品选择制造工艺时,请考虑以下因素:
外形结构:您的部件是否具有复杂的内部特征或严格的公差要求?根据部件的几何设计,制造方案可能会受到限制,或者可能需要进行重大的可制造性设计 (DFM) 优化,以保证生产过程的经济性。
生产量/成本:您计划生产的部件总量或年产量是多少?一些制造工艺在模具和设置方面的前期成本很高,但每个部件的生产成本很低。相比之下,小批量制造工艺的启动成本较低,但由于周期时间较长、自动化程度较低并需要人工操作,随着产量增加,每个部件的成本将保持不变或者仅略有降低。
周转时间:您需要以多快的速度生产部件或成品?一些流程会在 24 小时内生产出首批部件,而某些大批量生产流程的模具准备和设置则需要数月的时间。
材料:您的产品需要承受多大的应力和应变?最适合给定应用的材料由许多因素决定。必须在成本与功能和美学需求间取得平衡。思考具体应用的理想特性,并将其与给定制造工艺中可用的选择进行对比。

点击此处下载该信息图的高分辨率版本。

塑料类型
通过不同的基本化学成分、衍生方式和添加剂,可以制成数千种不同的塑料,涵盖广泛的功能和美学特性。
为简化寻找最适合给定部件或产品的材料的过程,我们首先看看两种主要的塑料类型:热塑性塑料和热固性塑料。
热塑性塑料
热塑性塑料是最常用的塑料类型。相比于热固性塑料,其最大的不同是能够在不发生显著降解的情况下经历无数的熔化和凝固循环。热塑性塑料通常以小颗粒或板材的形式提供,这些材料通过各种制造流程加热并形成所需形状。这些流程中没有发生化学键合,因此是完全可逆的,这使得热塑性塑料的回收、熔化和再利用成为可能。
热塑性材料的常见类型:
- 丙烯酸树脂 (PMMA)
- 丙烯腈丁二烯苯乙烯 (ABS)
- 聚酰胺 (PA)
- 聚乳酸 (PLA)
- 聚碳酸酯 (PC)
- 聚醚醚酮酮 (PEEK)
- 聚乙烯 (PE)
- 聚丙烯 (PP)
- 聚氯乙烯 (PVC)
热固性塑料
不同于热塑性塑料,热固性塑料在固化后将永久保持固态。热固性材料中的聚合物在由热、光或适当辐射引发的固化过程中会发生交联。该固化过程中会形成不可逆的化学键。热固性塑料在加热时会发生分解而不是熔化,并且冷却后不会再变形。热固性塑料无法回收或恢复为基本成分。
热固性材料的常见类型:
- 氰酸酯
- 环氧树脂
- 聚酯
- 聚氨酯
- 硅胶
- 硫化橡胶
制造工艺类型
3D 打印
专业级 3D 打印机直接通过 CAD 模型创建三维部件,其方法是逐层构建材料,直至形成完整的物理部件。
制造工艺
- 打印设置:使用打印准备软件在打印机成型体积内部定向和布局模型、添加支撑结构(如果需要),并将支撑的模型切成不同的层。
- 打印:打印工艺取决于 3D 打印技术的类型:熔融沉积成型 (FDM) 工艺需要熔化塑料长丝,立体光固化 (SLA) 工艺需要固化液态树脂, 选择性激光烧结 (SLS) 工艺需要熔化塑料粉末。
- 后处理:打印完成后,从打印机上取下部件,清洁或清洗部件,进行后固化(取决于使用的技术),并去除支撑结构(如果适用)。
3D 打印机不需要使用模具,并且针对新设计的设置时间非常短,因此,与传统制造工艺相比,其生产定制部件的成本可以忽略不计。
3D 打印流程通常比批量生产流程更慢、劳动强度更高。
随着 3D 打印技术不断进步,单件成本持续下降,在中小型应用领域开辟了更广阔的天地。
3D 打印 | |
---|---|
外形结构 | 高自由度 |
周转时间 | 少于 24 小时 |
周期时间 | 从一小时以内到几小时不等,具体取决于部件尺寸和体积 |
设置成本 | $ |
单件成本 | $$$ |
批量 | 中小批量应用(约 1-1000 件) |
大多数塑料制造工艺都需要昂贵的工业机械、专用的设施和熟练的操作人员,但 3D 打印能够让公司轻松地在内部打造塑料部件并快速制造原型。
用于创建塑料部件的紧凑型桌面或立式 3D 打印系统价格合理、占地空间小并且无需特殊技能,能够帮助专业工程师、设计师和制造商将迭代和生产周期从几天或几周缩短为几小时。
材料
市场上存在多种类型的 3D 打印机和 3D 打印技术,具体可用材料因技术而异。
3D 打印材料 | |
---|---|
熔融沉积成型 (FDM) | 各种热塑性材料,主要包括 ABS 和 PLA |
立体光固化 (SLA) | 热固性树脂 |
选择性激光烧结 (SLS) | 热塑性材料,通常为尼龙及其复合材料 |
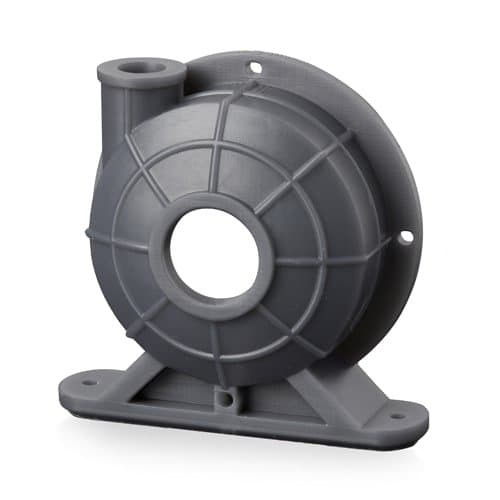
CNC 加工技术
CNC 加工包括铣床、车床和其他计算机控制的减材制造工艺。这些工艺以金属或塑料实心块、棒或杆作为原材料,通过切、镗、钻、磨等方式去除多余材料实现成型。
与大多数其他塑料制造工艺不同,CNC 加工是一种减材制造工艺,通过使用旋转工具加工固定部件(铣床)或使用固定工具加工旋转部件(车床)去除多余材料。
制造工艺
- 任务设置:CNC 机床需要一个用于生成和验证刀具路径(CAD 到 CAM)的中间步骤。刀具路径会控制刀具经过的位置、移动速度以及刀具的更换。
- 加工:刀具路径将发送至用于启动给定减材制造工艺的机器。根据最终产品需要制成的形状,可能需要将工件安置在便于刀头触及的新位置。
- 后处理:制造完成后,对部件进行清洁、去毛刺和修整。
机械加工是小批量塑料部件应用的理想选择,这些应用要求严格的公差和难以成型的几何形状。典型应用包括原型制造以及滑轮、齿轮和衬套等成品部件。
CNC 加工的安装成本为低至中等,可以利用多种材料生产出交付周期很短的高质量塑料组件。
与 3D 打印相比,机械加工过程对部件的几何约束更多。加工的部件越复杂,单件成本越高。多个部件面上的凹槽、通孔和纹理都会增加部件成本。
加工过程需要允许使用工具,并且某些几何形状(如弯曲的内部通道)很难或不可能通过传统的减材制造形成。
CNC 加工技术 | |
---|---|
外形结构 | 中等自由度 |
周转时间 | 少于 24 小时 |
周期时间 | 从一小时以内到几小时不等,具体取决于部件尺寸、设计和复杂度 |
设置成本 | $$ |
单件成本 | $$$$ |
批量 | 小到大批量应用(约 1-5000 件) |
材料
大多数硬塑料都可以进行加工,但难度各有不同。较软的热固性塑料需使用专用模具在加工过程中支撑部件,而填充塑料可能具有研磨性,会降低刀具寿命。
部分常用于加工的塑料为:
- 丙烯酸树脂 (PMMA)
- 丙烯腈丁二烯苯乙烯 (ABS)
- 聚酰胺(尼龙)(PA)
- 聚乳酸 (PLA)
- 聚碳酸酯 (PC)
- 聚醚醚酮酮 (PEEK)
- 聚乙烯 (PE)
- 聚丙烯 (PP)
- 聚氯乙烯 (PVC)
- 聚碳酸酯 (PC)
- 聚苯乙烯 (PS)
- 聚甲醛 (POM)
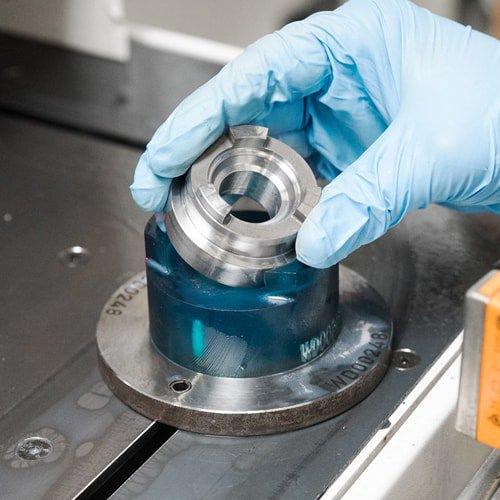
聚合物铸造
聚合物铸造工艺使用具备反应活性的液态树脂或橡胶填充模具,使其在模具中发生化学反应并固化。用于铸造的典型聚合物包括聚氨酯、环氧树脂、硅胶和丙烯酸树脂。
制造工艺
- 制模:模具涂有脱模剂以加快脱模,并且通常预热至材料特定温度。
- 铸造:将合成树脂与固化剂混合,然后倒入或注入模具,使其填充模腔。
- 固化:铸件会在模具中固化,直至凝固(加热模具可加快某些聚合物的固化速度)。
- 脱模:打开模具,取出固化的部件。
- 修整:切去或磨去飞边、浇道和缝隙等铸造瑕疵。
与硬模具相比,由乳胶橡胶或室温硫化 (RTV) 硅胶制成的柔性模具价格低廉,但由于聚氨酯、环氧树脂、聚酯和丙烯酸树脂发生的化学反应会使模具表面降解,因此只能生产有限数量(约 25 至 100 件)的铸件。
RTV 硅胶模具甚至可以重现最微小的细节,生产出高质量的铸件。立体光固化 3D 打印是直接通过 CAD 设计为模具创建母模的常用方法,部分原因在于其高分辨率和形成精细特征的类似能力。
聚合物铸造的价格相对低廉,初始投资很低,但用于浇铸的热固性聚合物通常比相应的热塑性聚合物更昂贵,并且铸件的成型需要大量劳动力。每个铸件都需要手动进行后处理,因此,与注射成型等自动化生产方法相比,其最终的单件成本很高。
聚合物铸造通常用于原型制造、短期生产以及某些牙科和珠宝应用。
聚合物铸造 | |
---|---|
外形结构 | 高自由度 |
周转时间 | 24 小时以内到几天不等 |
周期时间 | 几分钟到几天不等,具体取决于固化时间 |
设置成本 | $ |
单件成本 | $$ |
批量 | 小批量应用(约 1-1000 件) |
材料
- 聚氨酯
- 环氧树脂
- 聚醚
- 聚酯
- 丙烯酸树脂
- 硅胶
旋转成型
旋转成型工艺(也称为旋转模塑)主要用于生产大型空心部件,其成型方法是使填充有热塑性塑料粉末的空心模具围绕两个轴旋转,并同时加热模具。热固性塑料也有相应的旋转成型工艺,但相对并不常见。
制造工艺
- 装料:将塑料粉末装入模腔,然后安装模具的其余部分,闭合模腔进行加热。
- 加热:加热模具直至塑料粉末熔化并附着在模具壁上,同时沿两个垂直轴旋转模具,以确保形成均匀的塑料层。
- 冷却:缓慢冷却模具,并使模具保持运动,以确保部件表面在完全凝固之前不会下垂或塌陷。
- 移除部件:将部件从模具中分离,修剪所有飞边。
相比其他成型技术,旋转成型需要的模具价格更低,因为该工艺使用离心力而不是压力来填充模具。这些模具可使用环氧树脂或铝进行制造、CNC 加工、铸造或成型,其成本更低,并且速度比其他成型工艺的模具快得多,尤其适用于大型部件。
旋转成型可制造出壁面厚度近乎均匀的部件。一旦模具和流程设置完毕,相对于部件尺寸而言,该成型方法的单件成本非常低。也可以向模具中添加预先加工好的工件,如金属导螺杆、内部管道和特定结构。
这些因素使旋转成型成为短期生产或替代吹塑进行小批量生产的理想之选。典型的旋转成型产品包括罐子、浮标、大型集装箱、玩具、头盔和独木舟船体等。
旋转成型在设计上受到一些限制,成品的公差较宽松。由于整个模具必须进行加热和冷却,因此该工艺的周期时间长且劳动强度大,限制了其在大批量应用中的效率。
旋转成型 | |
---|---|
外形结构 | 中等自由度,非常适用于大尺寸空心部件 |
周转时间 | 几天到几周不等 |
周期时间 | 通常不到 1 小时 |
设置成本 | $$$ |
单件成本 | $$ |
批量 | 中批量应用(约 200-5000 件) |
材料
旋转成型最常用的材料是聚乙烯 (PE),80% 的应用中均使用该材料,这主要是因为 PE 在室温下很容易磨成粉末。
旋转成型常用的塑料包括:
- 聚乙烯
- 聚丙烯
- 聚氯乙烯
- 尼龙
- 聚碳酸酯
真空成型
制造工艺
- 固定:将塑料板材夹在框架内。
- 加热:将板材和框架移至加热元件附近,使塑料变得柔韧。
- 真空处理:放低框架,使塑料在模具上展开,同时激活真空环境,吸除塑料与模具之间的所有空气,使部件成型。
- 冷却和脱模:部件在模具上成型后,必须冷却一段时间后再进行脱模。有时需使用风扇和喷雾等冷却系统来缩短周期时间。
- 修整:部件脱模后,用手或 CNC 机床切去多余的材料。
与其他成型技术相比,真空成型所涉及的力和压力较低,因此模具成本也较低。对于短期生产和定制部件,通常使用木材、塑料或 3D 打印树脂制作模具。如果是大批量生产,制造商则会使用更耐用的金属模具。
鉴于热压成型和真空成型机械的可选范围非常广泛,并且有实现高端自动化的可能性,热压成型非常适用于从定制产品、原型制造到批量生产等各类应用。然而,该工艺仅提供有限的形状自由度,并且只能用于制造具有相对较薄的壁面和简单几何形状的部件。
真空成型部件通常包括产品包装、淋浴盆、车门内衬、船体和定制类产品(如牙科矫治器)。
真空成型 | |
---|---|
外形结构 | 自由度有限,仅可制造无复杂几何形状的薄壁部件 |
周转时间 | 24 小时以内到几周不等 |
周期时间 | 几秒到几分钟不等,具体取决于使用的机械 |
设置成本 | $-$$$$ |
单件成本 | $-$$$ |
批量 | 任意批量 |
材料
大多数热塑性塑料均可用于热压成型,在材料选择方面十分灵活。
热压成型常用的塑料包括:
- 丙烯酸树脂 (PMMA)
- 丙烯腈丁二烯苯乙烯 (ABS)
- 聚对苯二甲酸乙二醇酯-1, 4-环己烷二甲醇酯 (PETG)
- 聚苯乙烯 (PS)
- 聚碳酸酯 (PC)
- 聚丙烯 (PP)
- 聚乙烯 (PE)
- 聚氯乙烯 (PVC)

注射成型
注射成型 (IM) 的工作原理是将熔融的热塑性塑料注射到模具中,是批量生产塑料部件时最常用的工艺。
制造工艺
- 模具安装:如果模具包含镶件,则手动或自动添加镶件。由液压机闭合模具。
- 塑料挤压:小塑料颗粒在加热室中熔化并通过螺杆挤出。
- 成型:将熔融的塑料注入模具。
- 冷却和脱模:部件在模具中冷却,直至足够坚固,可以通过机械或压缩空气排出。
- 后处理:去除部件上的浇道、流道和所有飞边(如适用),这些瑕疵通常会作为模具开口的一部分自动去除。
注射成型的模具非常复杂,需要遵循严格的公差制作,以生产高质量的部件。由于该工艺涉及高温和高压,这些模具均由硬化钢等金属加工而成。较软的铝制模具成本较低,但磨损更快,因此通常用于强度更低的生产流程。
注射成型可用于生产高度复杂的部件,但有些几何形状会显著增加成本。以下可制造性设计 (DFM) 指南有助于保持模具成本可控。新的注射成型模具可能需要几个月才能制作完成,其成本可能高达五到六位数。
尽管初始成本高且上升曲线缓慢,注射成型依然是大批量应用的不二之选。一旦模具准备就绪并投入运行,只需几秒钟的周期时间就可以生产出数百万个高质量部件,且生产成本远低于其他制造工艺。
注射成型 | |
---|---|
外形结构 | 中到高自由度 |
周转时间 | 2-4 个月 |
周期时间 | 秒数 |
设置成本 | $$$$$ |
单件成本 | $ |
批量 | 大批量应用(超过 5000 件) |
材料
几乎任何类型的热塑性塑料均可用于注射成型。如需使用热固性塑料制造部件,则选用一种被称作反应注射成型 (RIM) 的类似方法。
注射成型常用的塑料包括:
- 丙烯酸树脂 (PMMA)
- 丙烯腈丁二烯苯乙烯 (ABS)
- 聚酰胺 (PA)
- 聚对苯二甲酸乙二醇酯-1, 4-环己烷二甲醇酯 (PETG)
- 聚苯乙烯 (PS)
- 聚碳酸酯 (PC)
- 聚丙烯 (PP)
- 聚乙烯 (PE)
- 聚氯乙烯 (PVC)
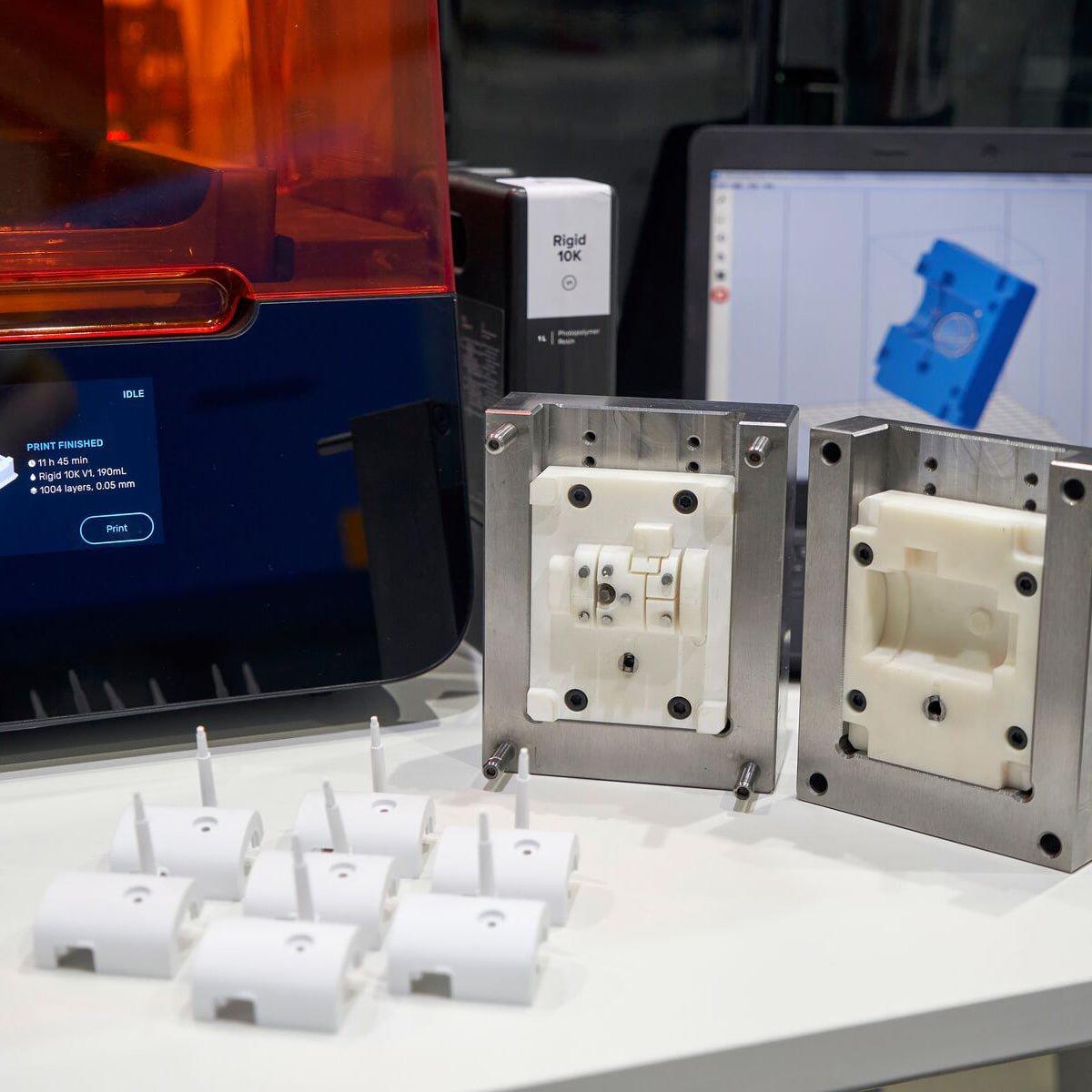
使用 3D 打印模具完成小批量快速注射成型
有关在注射成型工艺中使用 3D 打印模具以减少成本和备货时间的指南,以及 Braskem、Holimake 和 Novusr Application 的真实案例研究,请下载我们的白皮书。
挤出
挤出成型的工作原理是推动塑料通过模粒。模粒的形状与最终部件的横截面形状相同。
制造工艺
- 塑料挤压:加热塑料,并使用螺杆推动塑料通过加热室。
- 成型:塑料在力的作用下通过模粒,形成部件的最终形状。
- 冷却:冷却挤出的塑料。
- 切割或缠绕:将连续挤出的部件卷起或切成较短长度。
与 CNC 或注射成型等工业流程所用的机器相比,挤压机械相对便宜,因为其复杂度较低,并且不需要特别高的机器精度。由于形状简单,模粒也较便宜,挤出成型的模具成本仅为注射成型的几分之一。
挤出成型与注射成型十分相似,是一个近乎连续的过程,因此挤出成型部件的价格非常低。
挤出成型仅可制造具有连续轮廓的形状,如 T 形截面、I 形截面、L 形截面、U 形截面以及方形或圆形截面。典型应用包括管道、软管、吸管和窗框的成型。
挤出 | |
---|---|
外形结构 | 形状受限,通常为较长的连续形状 |
周转时间 | 周数 |
周期时间 | 几秒(或持续不停) |
设置成本 | $$$ |
单件成本 | $ |
批量 | 中到大批量应用(超过 1000 件) |
材料
可对几乎所有热塑性塑料进行挤出成型,包括:
- 丙烯酸树脂 (PMMA)
- 丙烯腈丁二烯苯乙烯 (ABS)
- 聚酰胺 (PA)
- 聚对苯二甲酸乙二醇酯-1, 4-环己烷二甲醇酯 (PETG)
- 聚苯乙烯 (PS)
- 聚碳酸酯 (PC)
- 聚丙烯 (PP)
- 聚乙烯 (PE)
- 聚氯乙烯 (PVC)
吹塑
吹塑是一种用于制造空心塑料部件的技术,工作原理是在模具内向受热的塑料管中充气,直至形成所需形状。
制造工艺
- 模具安装:小塑料颗粒熔化并在空心管中成型,称为型坯或预制件(取决于吹塑的具体子类型)。
- 成型:型坯被夹在模具中,并通过压缩空气进行充气,直至形成模具内部的形状。
- 冷却和脱模:部件在模具中冷却,直至足够坚固可以排出。
吹塑所需的压力远低于注射成型,这有助于降低模具成本。吹塑与注射成型十分相似,是一个可以全自动进行的连续过程,因此其生产率很高且单位成本很低。
吹塑是大规模生产空心塑料产品最为常用的工艺。典型应用包括瓶子、玩具、汽车组件、工业部件和包装。
吹塑 | |
---|---|
外形结构 | 自由度优先,仅可制造无复杂几何形状的薄壁空心部件 |
周转时间 | 周数 |
周期时间 | 秒数 |
设置成本 | $$$$ |
单件成本 | $ |
批量 | 大批量应用(超过 5000 件) |
材料
吹塑工艺可使用各种热塑性材料,最常见的例子有:
- 聚对苯二甲酸乙二醇酯 (PET)
- 聚丙烯 (PP)
- 聚氯乙烯 (PVC)
- 聚苯乙烯 (PS)
- 聚碳酸酯 (PC)
- 丙烯腈丁二烯苯乙烯 (ABS)
利用 3D 打印快速制造塑料部件
塑料制造工艺正在不断发展,由于设备、材料和规模经济的改进,从一种技术转型到另一种技术的拐点也在不断变化。
3D 打印是一项较新的技术,但已迅速趋向成熟,随着硬件和材料的改进以及单件成本的持续下降,该技术将向更广泛的中小型应用开放。
进一步了解领先制造商如何利用 3D 打印节省资金并缩短从设计到生产的交付周期。