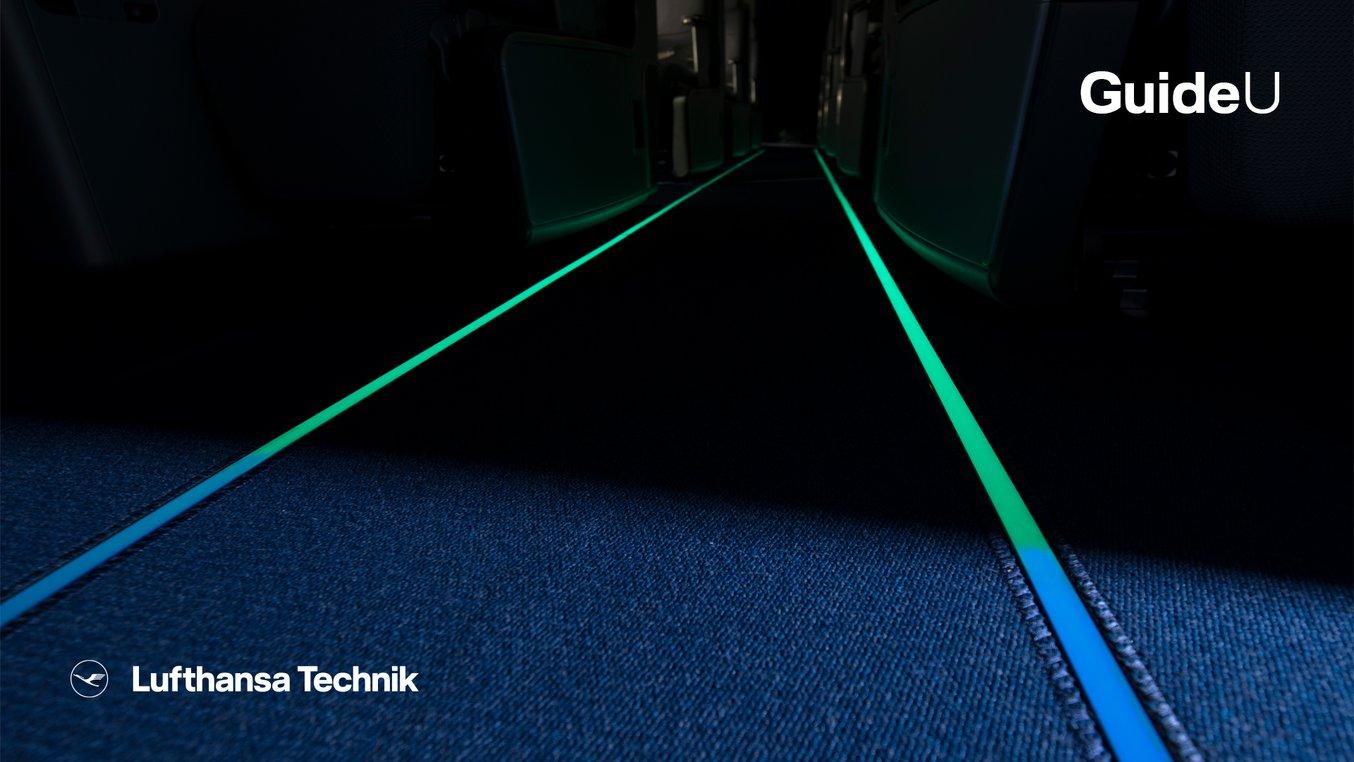
Lufthansa Technik AG 是汉莎集团的子公司,不仅负责汉莎航空的维护和维修,还向空客、波音等主流设备制造商 (OEM) 销售航空产品和飞机零部件。
其中一条产品线是飞机内部的逃生路线标记,它是借助 3D 打印 制造辅助设备,以创新的方式制作的。
在采访 Lufthansa Technik AG 的项目工程师 Ulrich Zarth 时,我们谈到了该公司如何在生产中使用这些 3D 打印工具作为消耗品,以及 3D 打印如何使流程优化更加灵活。
空客、波音公司都在采用的逃生路线标记
作为全球最大的航空 MRO(维护、维修和大修)供应商之一,Lufthansa Technik 广泛使用增材制造。自 2018 年以来,公司内的一个跨部门机构一直负责开发用于制造航空航天产品的各种 3D 打印工艺,以及用于3D打印生产的工具和设备。这些飞机零部件的最大客户主要是空客、波音等大型设备制造商。
Lufthansa Technik 使用 3D 打印的产品之一是用于飞机内部的 Guide U 逃生路线标记。这些创新的地板标记是发光的,这意味着它们配备了自发光的彩色颜料,这些颜料由普通的客舱灯充电,并在没有电的紧急情况下可以在黑暗中继续发光。飞机地板上一排排座位上的自发光条显示了紧急情况下通往紧急出口的通道。
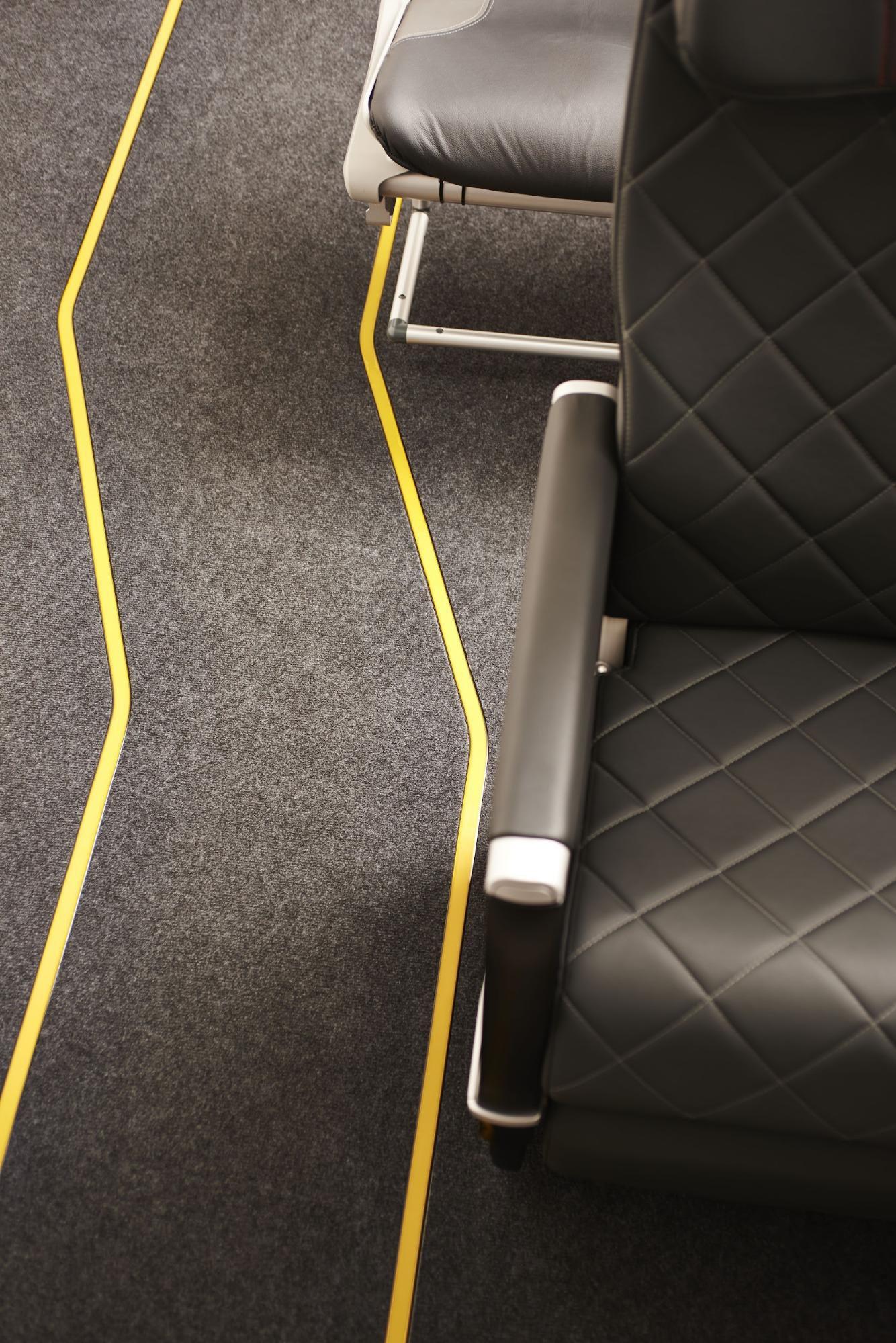
Guide U灯带安装在飞机上作为逃生路线标记。
该专利系统已于 2021 年 11 月在德国汉堡的 Lufthansa Technik 内部生产。
3D 打印的喷嘴作为生产使用的耗材
为了创建这些逃生路线标记,Lufthansa Technik 的团队利用 3D 打印生产的制造辅助设备。在测试了不同的方法后,选择了立体光刻 (SLA) 3D 打印,将喷嘴用作制造过程的工具组件。
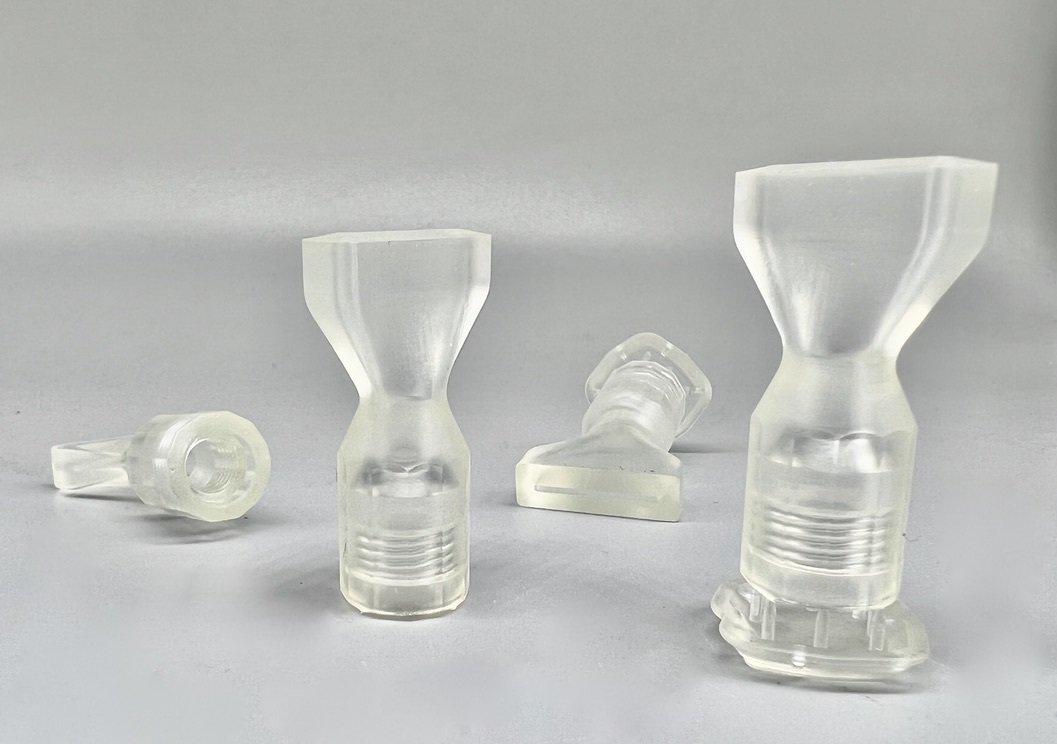
喷嘴,由Clear Resin制成,带有一体式螺纹(最右侧的组建仍带有支撑结构)。
一个特殊的要求是将此喷嘴视为消耗品。3D 打印喷嘴是一种具有成本效益的替代制造辅助工具,否则这些辅助工具将使用机械加工或注塑成型等传统工艺生产。喷嘴使用Clear Resin通过 SLA 3D 打印生产,满足工具必要的质量和精度要求。该解决方案使 Lufthansa Technik 能够每天更换喷嘴以优化生产过程。
“如果你想要快速精确的获得几何形状的零件,特别是使用塑料材料,我会一直使用 3D 打印。”
Ulrich Zarth
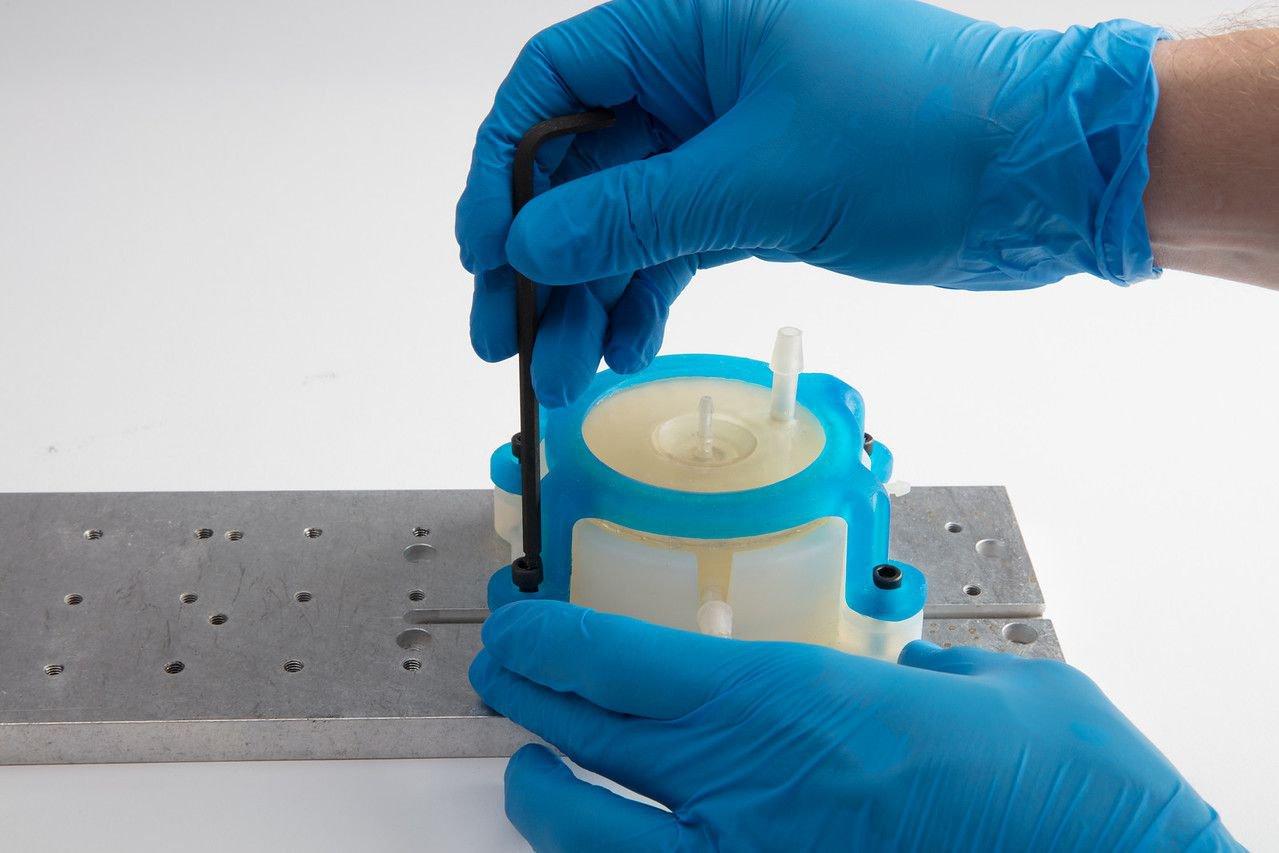
SLA 3D 打印具有较好尺寸精度和更高的灵活性
该生产工具是与 Formlabs 合作伙伴 myprintoo 合作在 Form 3L 上打印的。Form 3L 中的大面积构建平台允许在一次打印运行中生产 72 个喷嘴。相比之下,在 Formlabs SLA 3D 打印机的较小版本上, Form 3+将能够在一次构建中打印 25 个喷嘴。Form 3L 在不牺牲喷嘴打印精度的情况下,在应用程序的生产中节省了大量时间。
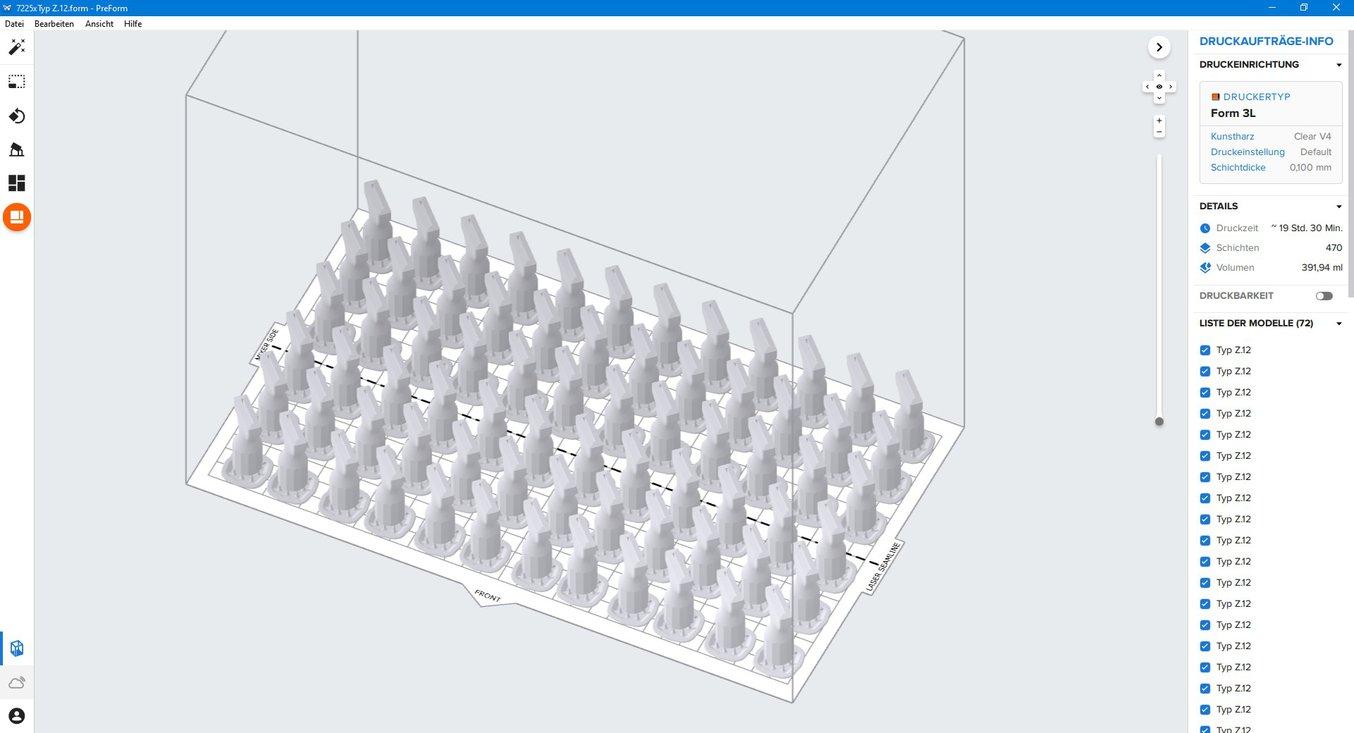
在 Form 3L 上生产 72 个喷嘴,打印时间为 19.5 小时。
“我们在迭代过程中跟踪工具的构造,对层厚度、打印方向甚至部分组件几何形状进行任何调整,从而确保工艺可靠性和打印质量,”myprintoo 的 Jonathan Wulf 解释说.
打印完成后,喷嘴可用于Guide U灯带的生产过程,无需任何超出标准后处理的步骤。对几种 Formlabs 材料进行了测试,最终选择了 Clear Resin,它除了提供适当的稳定性和表面质量外,还有助于 Lufthansa Technik 不断优化其生产流程。
作为负责的项目工程师,Zarth 与 Formlabs 的合作伙伴 myprintoo 密切合作,迭代了五个版本的喷嘴。由于 myprintoo 的 3D 打印部件提供快速可靠的服务和交付,偶尔仍会进行设计更改以优化流程。
“我们用一个下午就注意到了这次合作最大的好处是快速调整和迭代。例如,过程中的某些事情没有按应有的方式进行;在晚上就对喷嘴模型进行了调整,第二天我们就可以使用新喷嘴进行打印了。”
Ulrich Zarth
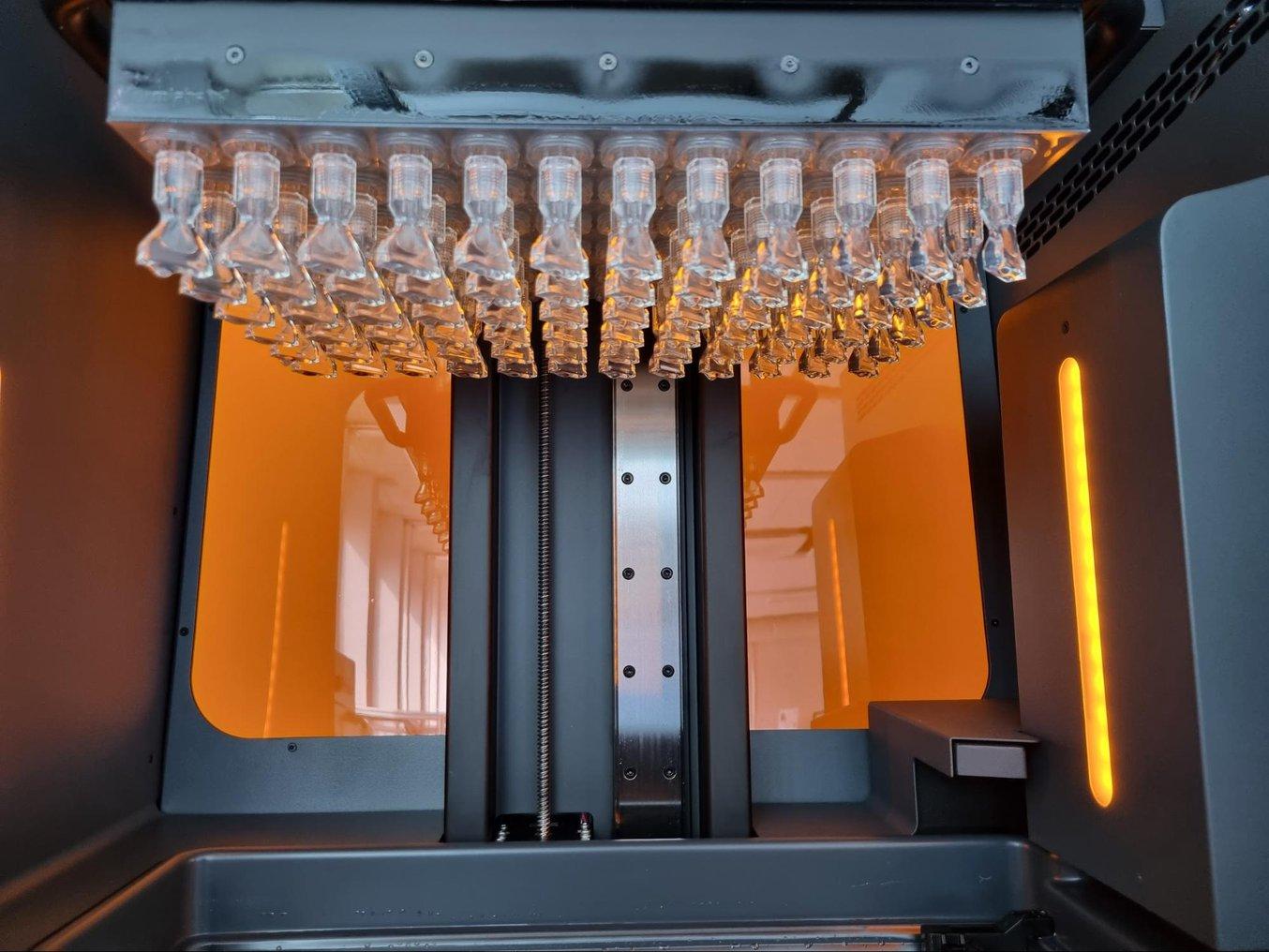
Lufthansa Technik 通过Form 3L,使用Clear Resin制作的喷嘴。
使用 3D 打印对生产进行灵活的流程优化
Zarth 和他的团队通过内部 3D 打印这个小型组件,在生产过程中节省了大量时间和金钱。与制造此类工具的传统方法相比,他们还能够避免过高的最低订购量,并在工艺优化中保持显著的灵活性。
“理论上,我们也可以注塑我们的零件。但我们永远不会在喷嘴的形状和调整方面如此灵活。这就是我看到 3D 打印的巨大优势,”Zarth 解释道。
此外,与 FDM 3D 打印相比,SLA 3D 打印已被证明是该应用的高质量解决方案。
3D 打印生产工具作为传统工艺的替代品
许多公司使用注塑成型、CNC 加工或其他传统工艺为塑料和金属的生产工艺制造工具,这些工艺通常外包给外部供应商,因此交货时间长、成本过高和起订量高。
根据应用及其要求,这些过程可以用 3D 打印工具代替。Lufthansa Technik 生产 Guide U 逃生路线标记的喷嘴是 SLA 3D 打印支持的更便宜、更灵活的替代方案的一个例子。
“我们在生产中使用3D打印制作的工具作为消耗品,这一应用潜力可能许多人在3D打印的未来还没有看到。”
Ulrich Zarth