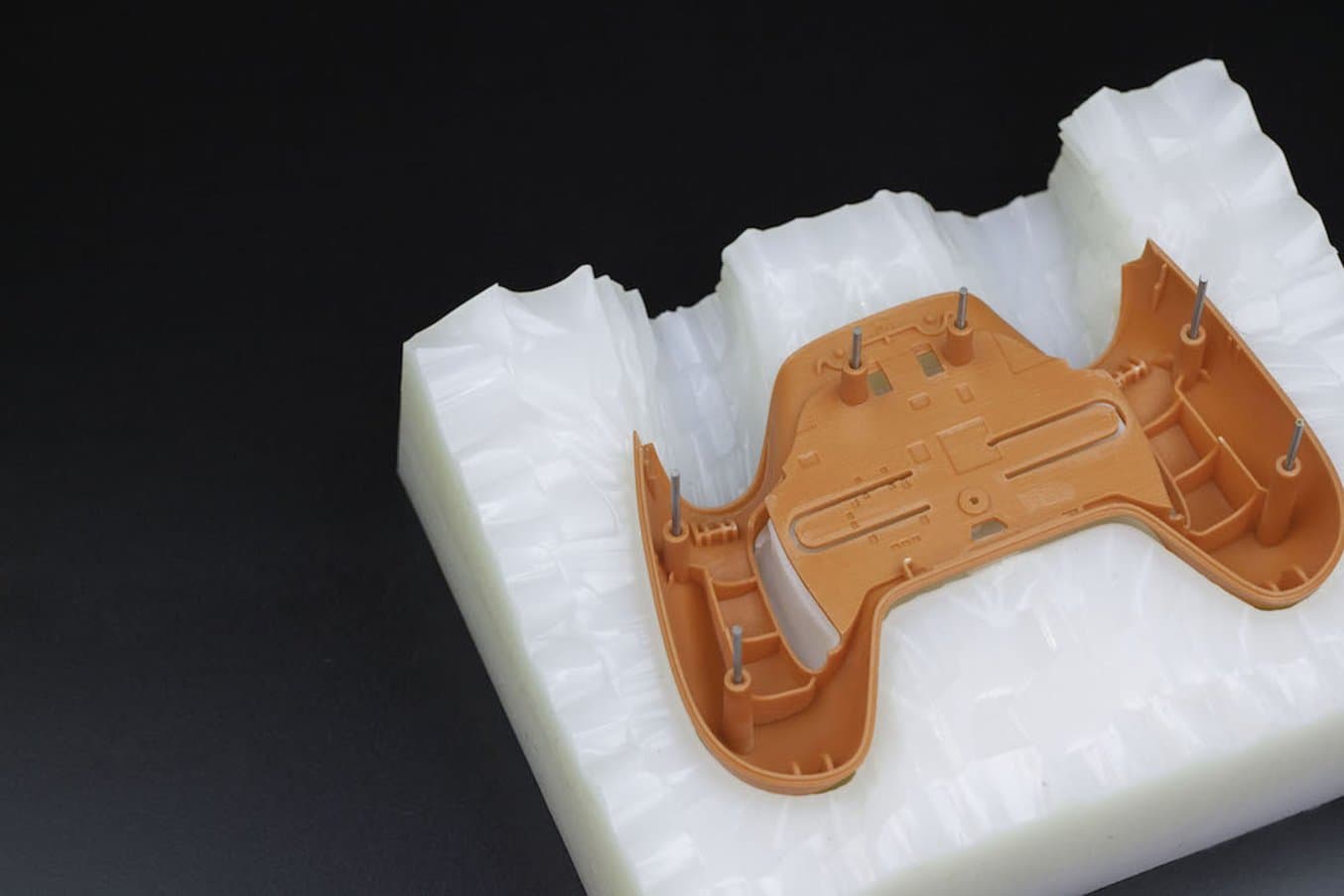
使用聚氨酯铸造制作的原型。来源:Fictiv
真空铸造是一种常见的制造方法,可用于小批量生产市场测试原型、个性化产品、量身定做的医疗器械等。
本指南将深入探讨真空铸造工艺的具体细节、与其他生产技术的比较、最佳聚氨酯铸造设备以及如何为真空铸造制作 3D 打印模型。
什么是真空铸造或聚氨酯铸造?
真空铸造是一种类似于注射成型的制造工艺,即将聚氨酯树脂铸造在两个硅胶半模之间的型腔中。
此工艺通过在模型周围铸造硅胶模具来复制主模型。此过程需要高度专业技能,将模具分为两半、移除主模型,然后添加浇口和通风系统。随后,模型制作人员将聚氨酯基树脂浇注到所得的型腔中,并在真空下固化,以防止气泡侵入。
其结果是:高度精确地再现原物。
注:在美国,真空铸造也称为聚氨酯铸造。本文将交替使用这些术语。
真空铸造应用
真空铸造工艺适用于小批量制造接近生产级品质的物品。
该工艺可制造出与最终产品几乎别无二致的高精细模型。这使得聚氨酯铸造模型在投资者推介会、贸易展览和商业摄影中表现出色。由于一个硅胶模具可以生产大约 50 个铸件,真空铸造还支持公司推出首批产品,以便进行早期市场测试。
如果项目需要更多的产品,客户有多种不同的选择:
-
同一主模型可重复用于制作多个硅胶模具。
-
多个主模型可用于制作多型腔模具。
-
模具制造商可以使用高温硫化 (High-Temperature Vulcanization, HTV) 硅胶或橡胶代替室温硫化 (Room-Temperature Vulcanization, RTV) 硅胶。这增强了模具的耐用性,每套模具的使用寿命可延长至 300-500 个铸件。
从制作主模型到获得铸件产品只需 10 天左右的周转时间,真空铸造不仅适用于快速原型制造,也适用于过渡生产,而无需像注射成型、热压成型和旋转铸造等工业级制造工艺那样进行大量的前期投资。
由于真空铸造能制造出具有完美表面光洁度的极精细模型,而且材料种类繁多,机械性能各异,因此适用于小批量生产成品,例如:
-
定制医疗器械,如义肢、矫形器和助听器
-
汽车部件:仪表板、旋钮、仪表、徽章、引擎盖装饰、照明透镜、进气歧管
-
消费电子产品:外壳、控制器、用户界面面板、传感器集成
-
机器人和工业机械的关键部件和备件
-
消费品:限量版太阳镜、钢笔、手机壳
-
乐器
-
科学仪器
-
运动器材配件
-
艺术品、雕像、比例模型、道具
真空铸造也是复制现有物品的一种常见解决方案,在此过程中无需采用复杂的逆向工程工作流程。这些物品通常十分稀有或已停产,如雕塑、化石、历史文物、古董、收藏品和工艺模型,并且没有 CAD 模型或其他形式的设计图。
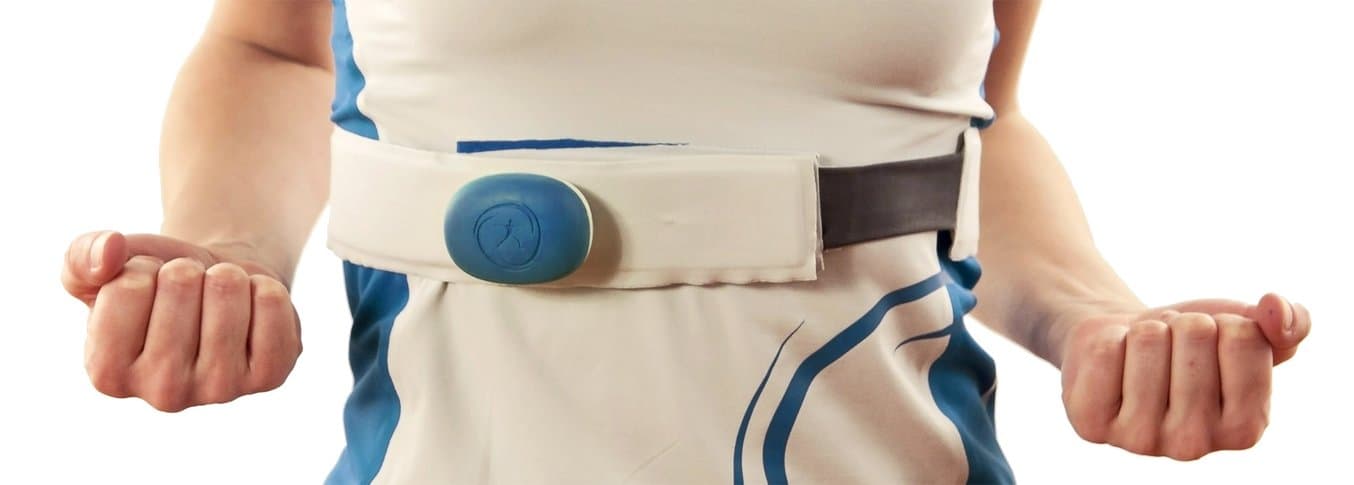
用于可穿戴呼吸传感器的电子外壳,通过真空铸造利用硅胶二次成型。来源:IDZone 产品设计公司。铸造:Venture Rapid Technologies。
聚氨酯铸造与备选方案对比
真空铸造与注射成型对比
产品设计师和工程师通常会转向使用 3D 打印技术进行设计验证,然后立即选择注射成型技术进行生产验证。但问题在于注射成型模具的成本,这些模具由高级钢材经 CNC 加工制成,可生产数百万个部件,但根据部件的大小和复杂程度,其成本可能在 5000 美元到 10 万美元之间。
因此,低级模具通常被用作硬模具制作的中间步骤。铝制模具仍可确保高达 1000-5000 次的成型周期,而成本却大大降低。由于软模具制作工艺速度更快,而且可以简化模具设计,因此与注射成型模具相比,周转时间大约缩短了一半。
根据所需的数量和部件质量,可以选择塑胶模或使用 3D 打印模具进行小批量注射成型。使用 Formlabs SLA 打印机制作 3D 打印模具的成本通常低于 100 美元,可生产 100 多件模具,且质量不会出现明显下降。
然而,产品开发人员往往忽略了一个事实:真空铸造通常是从原型制造过渡到生产的更明智方法。在所有早期原型制造方法中,树脂铸造工艺与注射工艺最为相似。此外,它还具有很高的成本效益;模具成本在 200 美元到 1000 美元之间,单价一般在 10 美元到 100 美元之间。
用于聚氨酯铸造的硅胶模具具有与注射模具类似的构造:均为两件式模具(一个是型芯,另一个是型腔),液化材料注入两件模具之间,形成最终产品。不过,两者也有一些不同之处:
-
注射成型中,在高压和高温下通过料斗和螺杆将熔融聚合物推入型腔。真空铸造则在低温下进行。所用材料并非熔融塑料,而是液态树脂,这些树脂在真空状态下被吸入模具,就像植物茎干内部的毛细作用一样。因此,虽然许多不同的树脂可以模仿各种聚合物,却无法使用最终的注射材料制作原型。
-
经过烤炉固化后,部件仍需进行长达一周的后固化,并且仍然容易受到紫外线辐射和高温的影响。
-
由于模具为柔性,因此部件的尺寸和形状存在限制。尽管如此,仍有一些特殊技术可以实现预期之外的效果。例如,分阶段铸造是指使用金属进行支撑来抵消重力,以便使用三件式或四件式模具铸造细长部件。
-
相对于注射成型,真空铸造更擅于处理不同的壁厚,因为铸造材料不会经历加热-冷却循环,从而减轻了部件变形。
-
硅胶模具支持在部件设计中大量减少倒凹。不过,在测试注射成型时,建议尽量采用注射成型设计,并在最终产品中加入所需的拔模角度。
-
真空铸造几乎不会产生废料,而注射成型则会因废品率、残留物和生产过剩而损失高达 20% 的聚合物。
真空铸造模型与从注射模具中取出的最终产品之间的高保真度足以支持工程师优化制造设计。如此一来,他们可以预览优质产品,而不必因为注射成型厂合同制造,让高层管理人员承担巨额固定成本。
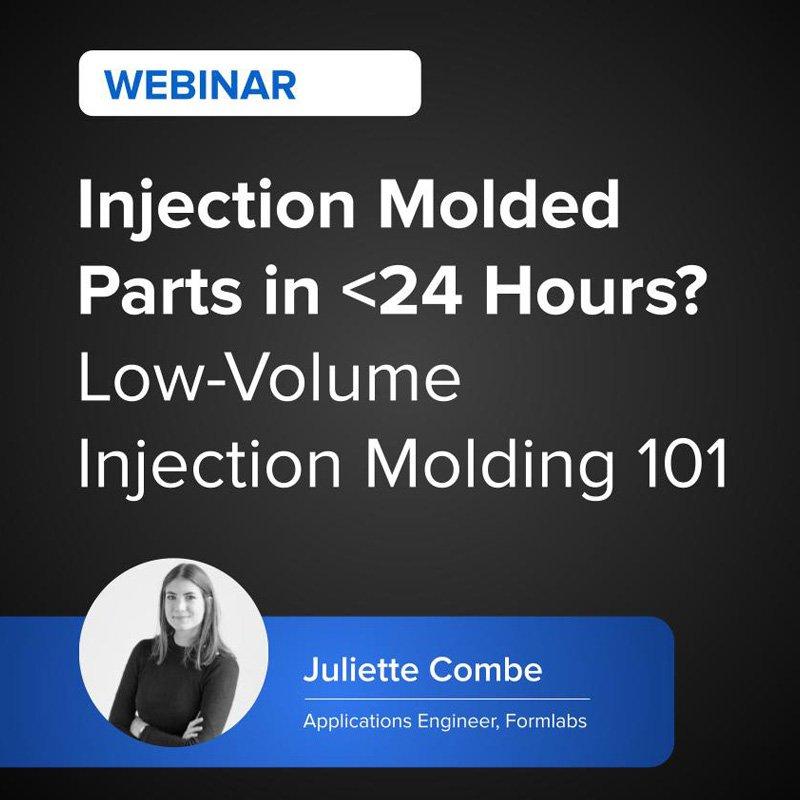
想要在 24 小时之内获得注射成型部件吗?小批量注射成型 101
在本次网络研讨会中,我们将向您展示如何在注射成型过程中使用立体光固化 (SLA) 3D 打印模具来降低成本、缩短周转时间并提高上市产品质量。
真空铸造与 3D 打印对比
人们普遍误以为 3D 打印仅限于制造一次性产品。恰恰相反,它是小批量制造成品部件的可行方法。越来越多的企业投资建立内部打印农场。这种 3D 打印机队列可以处理数百甚至数千件产品的小批量生产。
选择进行 3D 打印还是真空铸造时的主要考虑因素是产品的几何形状。真空铸造的明确目的是模拟注射成型部件。作为全尺寸注射成型的低投入替代方案,它甚至可以在包覆模中结合柔性和刚性材料,或通过嵌件成型直接在原型中添加金属部件。对于制造小批量可注射成型的部件而言,真空铸造比 3D 打印更具成本效益。
真空铸造的另一个优势是可以比 3D 打印更快、更便宜地制造出更大的部件。支持的模具尺寸最长约为 50cm,铸件重量可达 1.5kg。
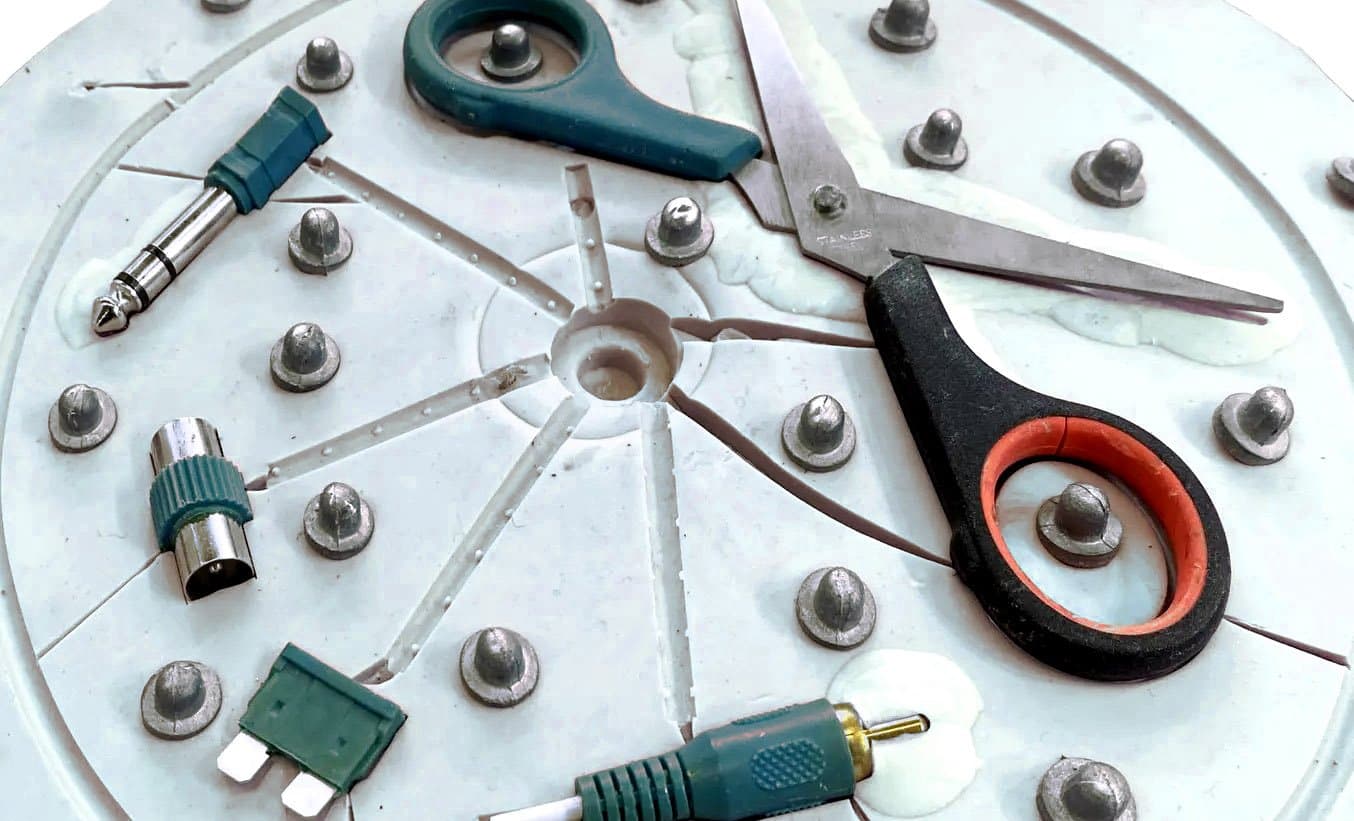
在硅胶模具中使用金属嵌件进行真空铸造。
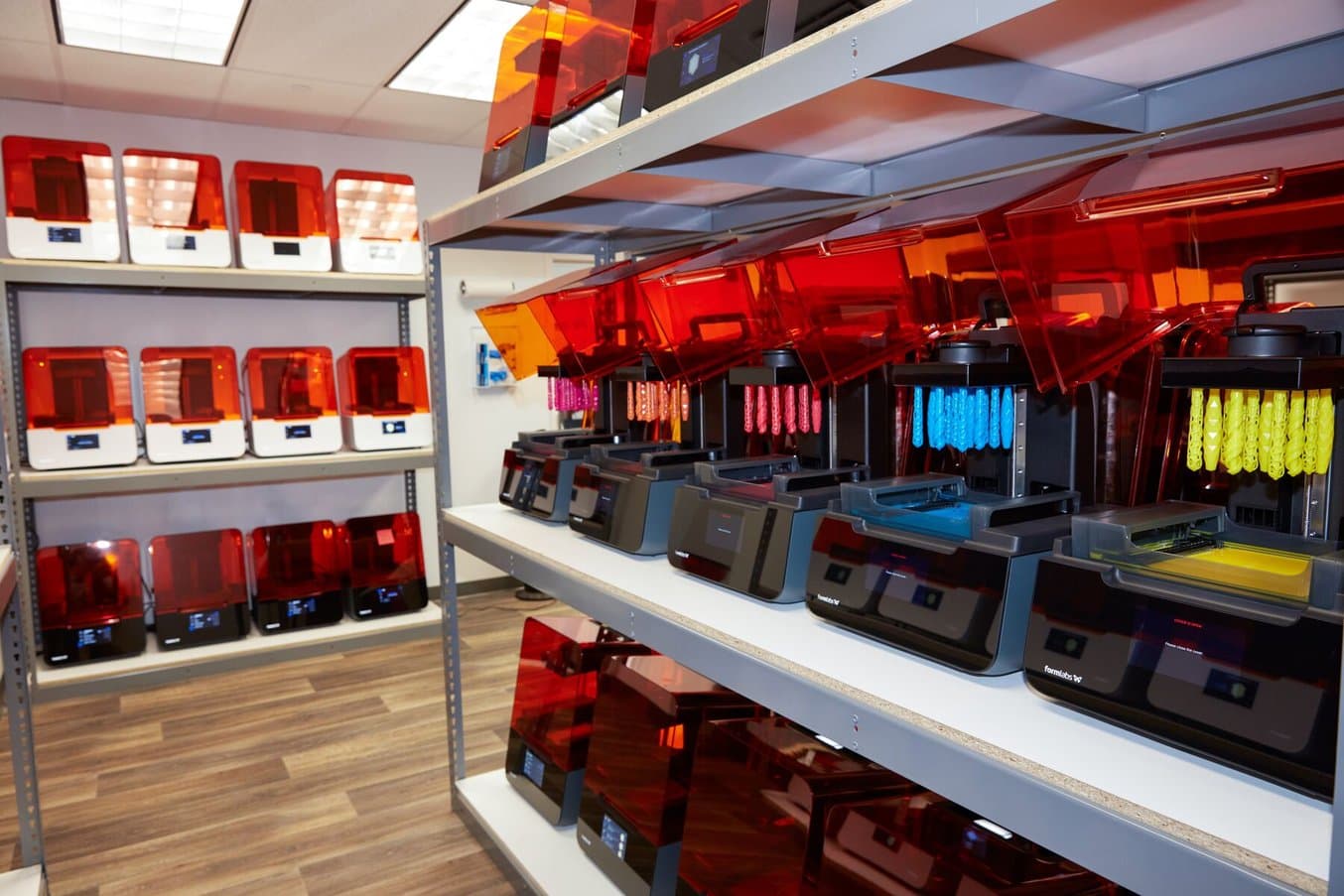
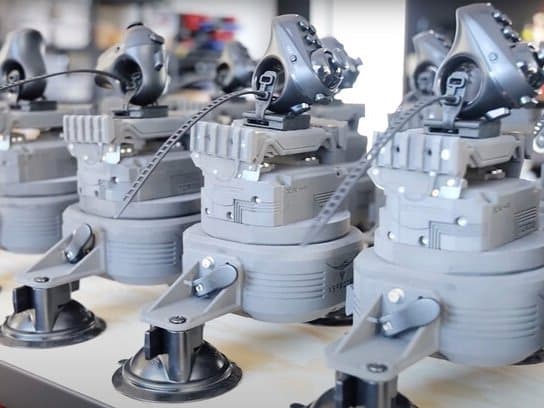
3D 打印压力测试部件的最终用途应用
本白皮书介绍了 Formlabs 用于成品部件生产的 3D 打印硬件和材料解决方案,包括案例研究和压力测试结果,以验证 3D 打印材料对最终用途应用的适用性。
对比:真空铸造与备选生产方法对比
以下是不同制造技术的优缺点:
真空铸造 | 注射成型 | 3D 打印 | 快速模具制作 | 机加工 | 手工制作 | ||
---|---|---|---|---|---|---|---|
设计自由度 | ★★★☆☆ | ★★☆☆☆ | ★★★★★ | ★★☆☆☆ | ★★★★☆ | ★★★☆☆ | |
部件尺寸 | ★★★★☆ | ★★★★☆ | ★★★☆☆ | ★★★☆☆ | ★★★★☆ | ★★★★★ | |
产量 | ★★★☆☆ | ★★★★★ | ★★★☆☆ | ★★★★☆ | ★★☆☆☆ | ★☆☆☆☆ | |
材料范围 | ★★★☆☆ | ★★★★☆ | ★★★★☆ | ★★★★☆ | ★★★★★ | ★★★☆☆ | |
投资成本 | ★★★☆☆ | ★☆☆☆☆ | ★★★☆☆ | ★★☆☆☆ | ★★★★★ | ★★☆☆☆ | |
单件成本 | ★★★★☆ | ★★★★★ | ★★★☆☆ | ★★★★☆ | ★★★☆☆ | ★★★☆☆ | |
周转时间 | ★★★★☆ | ★☆☆☆☆ | ★★★★★ | ★★★☆☆ | ★★★★☆ | ★★☆☆☆ |
真空铸造过程
真空铸造是一项高技能工艺,包括四个步骤。
1. CAD 设计
设计师或工程师使用 Fusion 360 或 SolidWorks 等 CAD 软件环境创建待生产物体的数字图像。在进行聚氨酯铸造设计时,应牢记以下指导原则:
-
壁厚在 1.5mm 至 4mm 之间。绝对最小厚度为 1mm。
-
加强筋可薄至壁厚的 60%。
-
使用大于 3mm 的大半径。
-
避免垂直壁,以提高部件强度。
-
在两个相配合的外壳之间构建 0.5mm 的凹槽,以优化产品外观。
-
螺丝孔壁厚应等于孔径。
-
雕刻字母的最佳深度为 0.25mm。
完成后,将 CAD 模型导出为 STL 格式,以便制作模型。
2. 制作母模
母模属于阳模,可用于铸造获得复制品。由于硅胶真空铸造模具提供母模的精确复制品,因此 3D 打印模型必须准确体现原始 CAD 模型,尤其是在超光滑表面质量方面。良好母模的一些次要特征包括硬度、耐化学腐蚀性和耐高温性以及耐久性,以防止随着时间的推移而退化。
CNC 铣削母模曾是标准方法,但其生产成本高且耗时,在孔、通道、内部半径和有机表面方面也存在限制。而 3D 打印是最先进的替代方法,也是目前制作母模的主流方法。
多种 3D 打印机类型可供主流客户和商业客户选择,但聚氨酯铸造最常用的工艺是 SLA 和 SLS 3D 打印。
SLA 3D 打印生产的部件表面光滑度最高,是真空铸造模型的理想选择。虽然使用正确的设置即可获得非常光滑的 SLA 打印件,但仍需要进行一些打磨和抛光,以去除支撑结构,达到绝对完美的表面效果。一些先进的材料(如 Rigid 10K Resin)还具有卓越的机械性能、耐高温性和耐用性。
使用尼龙进行 SLS 3D 打印可获得坚固、耐高温且精确的产品。由于此技术不需要支撑结构,因此也非常适合制造复杂特征,如薄壁、雕刻细节、卡扣、铰链以及嵌套或互锁部件。对于用于聚氨酯铸造的母模而言,SLS 3D 打印部件的表面光洁度略显粗糙,因此可以通过介质喷砂或振动滚磨来降低表面粗糙度。
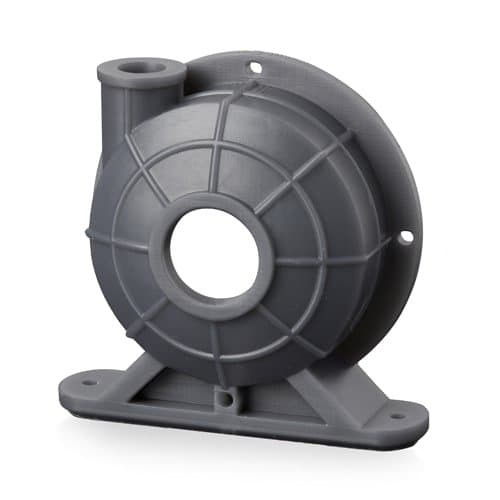
3. 制作模具
这是此过程中最耗费人力的阶段,制模人员使用三聚氰胺板和热胶制作型箱。然后用少量的 CA 胶水将母模固定在底部。有时,还需要使用旋转工具在母模上设计的边缘处制作凹槽,以额外进行固定。
为了使两部分模具之间的分型线紧密贴合,需要填满母模和底板之间的所有孔洞。苯乙烯块和 Plastalina 建模粘土是进行填充的首选材料。然后,添加定位销和套合定位栓,以便与另一半模具完全对齐。
将双组分硅胶充分混合后,在真空室中进行铸造和脱气。但在此之前,制模人员要巧妙地使用酸性刷子和硅胶混合物填补母模上的所有细小缝隙,以防止出现气孔,然后再倒回硅胶,形成模具的前半部分。
固化数小时后,从型箱中脱出半模并将其翻转。制模人员可熟练地安装丙烯酸通气口、冒口和浇口,以制作模具后半部分。将脱模剂喷涂在硅胶顶部,并刷涂较深的区域。然后,再构建新模盒,以类似的方式铸造下半部模具。
准备真空铸造时,将模具从型箱中取出,均匀地喷涂一层 E236 聚氨酯脱模剂。将两个半模重新组合成一个整体,并重新插入定位销和定位键进行对齐。
4. 真空聚氨酯铸造
在此步骤中,通过在真空室中进行铸造来复制原始母模。首先,将模具粘贴在木板上,并将排气孔和铸造漏斗添加到模具上。
测量双组分树脂并与着色剂混合,以进行着色。然后,将铸造材料在真空室中脱气几分钟。
现在即可铸造聚氨酯混合物。当型腔完全填满时,冒口就会显示出来。在 70˚C 的温度下固化后,打开模具,即可获得原始模型的复制品,且保留了所有细节和表面纹理。
最后的定型工作包括修剪边缘溢料、使用 1000 号砂纸进行额外抛光,以及烤炉固化以提高部件的材料性能。
专业提示
上述步骤主要适用于薄壁原型,如电子产品外壳、存储容器,以及其他希望避免在产品 A 面出现明显分割线的情况。
对于其他要求不高的产品,只需将母模封装在硅胶块中,然后手动切割分型即可。切割以正弦波的方式完成,这需要一些经验和灵活性。
以下是提高聚氨酯铸造效果的最佳做法:
-
直接在模型上使用喷雾脱模剂时应小心,因为这种脱模剂可以渗入表面形成轻微纹理,而这种纹理会在铸造时显现出来
-
将树脂预热至 40˚C,最好在使用前一天预热,并时常翻转瓶子以防止结晶。
-
防止水分渗入树脂瓶,因为水分会成为聚氨酯的吹膨剂。一种方法是在使用后立即向瓶中回充氩气。
-
混合双组分化学品时,务必使用双杯混合法。直接从第一个容器中倒入势必会产生未混合的条纹,并破坏铸件。
-
在拆卸型箱供将来使用时,使用外用酒精来松动热胶。
-
将注料口安装在产品的一角,使其与部件各部分的平均距离最短。这样可确保所有区域均可注满。
-
为防止形成气泡,应从单点浇注,并在有大量细节的易损区域周围浇注,切勿直接在这些区域顶部浇注。
-
浇口位置应较低,通气口位置应较高。
-
添加金属粉末可使饰面明亮夺目,也可考虑使用聚吡咯或石墨粉增强导电性。
-
在混合聚氨酯时,要在表面上方留出足够的空间,因为液体混合物会在真空室中起泡并上升,如同在微波炉中加热棉花糖一样。
-
使用专业级真空铸造机可加快铸造过程并获得更可靠的结果。
真空铸造机
由于工艺复杂,大多数公司都将工作分包给第三方聚氨酯铸造服务提供商。
对于那些计划在公司内部进行真空铸造的企业来说,专业真空铸造机是一个不可或缺的解决方案,可将原型制造工作提升到全新水平,并加快量产进程。2 天内可制作多达 50 个铸件,每个铸件均可根据需要采用不同的材料和颜色。
真空树脂铸造机是一种冰箱大小的装置,可自动完成从混合到铸造再到固化的整个过程。操作人员可以控制型腔增压、搅拌速度、加热杯和烤炉加热等参数。最新系统可编程,因此操作人员可以创建自定义序列,以优化特定材料和产品类型的铸造周期。
真空铸造机有不同的尺寸,以适应各种模具尺寸。除树脂外,大多数机型还可用于铸造注射级尼龙、陶瓷、蜡甚至低熔点金属合金。
聚氨酯铸造机是试生产的理想选择,因为其抽真空速度较快,并能最大限度地减少人工劳动。但缺点是价格昂贵。珠宝真空铸造机的尺寸要小得多,一般只需数千美元。
以下是一些真空铸造机的最佳选择:
-
雷尼绍 5/01 PLC:最大模具尺寸 530 × 450 × 420mm,价格约 4.5 万美元。更大的 5/04 型号支持的模具最大尺寸为 750 × 750 × 900mm,可使用更多材料,如玻璃纤维增强尼龙和蜡,但价格几乎翻倍。
-
SLM VCM 04:最大模具尺寸为 750 × 750 × 900mm,铸造体积为 2.2L,包括尼龙和蜡铸造。
-
MCP 5/01:最大部件尺寸 400 × 400 × 400mm。MCP 提供许多较大的机型选择,包括部件尺寸为 560 × 600 × 600mm 的 MCP 003、部件尺寸为 900 × 750 × 600mm 的 4/04 和部件尺寸为 1300 × 750 × 800mm 的 4/05。这些机器完全可编程,并且可使用蜡、硅胶、尼龙和聚氨酯树脂进行铸造。它们还可用于 3D 打印注射模具。
-
Scott AM 1000:最大模具尺寸 500 × 450 × 425mm,铸造重量 1kg。4000 型的最大模具尺寸为 750 × 750 × 900mm,铸造重量为 5kg。除树脂外,这些设备还可用于陶瓷和金属的真空熔模铸造。
-
Multistation CSV 340:最大模具尺寸为 340 × 340 × 435mm,铸造体积为 600mL。CSV500 型适用的最大模具尺寸为 500 × 500 × 635mm,最大铸造体积为 1L。
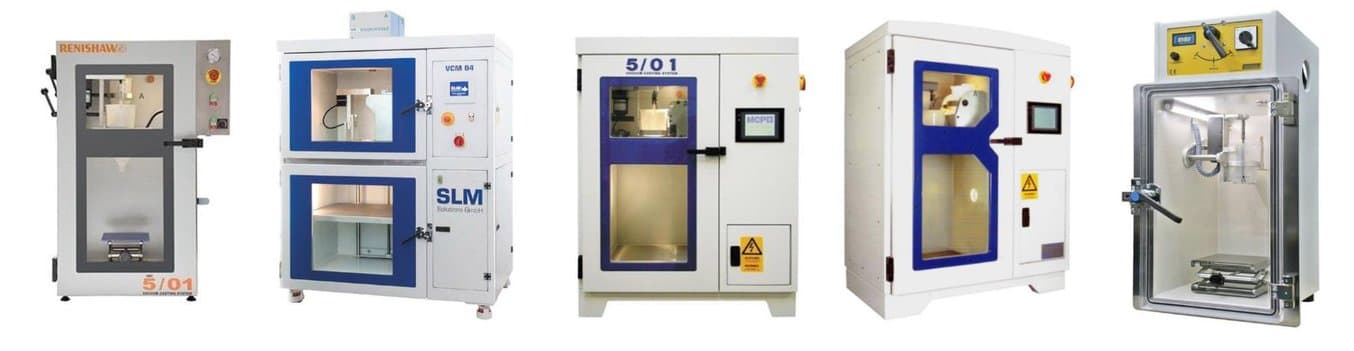
雷尼绍、SLM、MCP、Scott AM 和 Multistation 的真空铸造机。
真空铸造机与压力室对比
如需获得低成本的替代方案,完全可以自制一台真空重力铸造机。由于模具内哪怕只残留一个气泡都有可能毁掉整个铸件,因此脱气是树脂铸造过程中的一项基本挑战。
为了将混合物中的气泡全部排出,在制作 DIY 真空铸造机时,有两种防气泡工具可供选择:真空室或压力罐。
真空室为桶状,可用于在制作模具前去除硅胶中的空气。由于抽真空方法慢于高压方法,真空室只适用于固化时间为 20 分钟或更长时间的慢固化树脂。
真空室设有两个控制杆:一个用于进气口,另一个用于真空泵。此外还配备压力表,用于检查是否达到真空,还有透明的亚克力盖,用于检查脱气情况。与塑料盖相比,钢化玻璃盖不会随着时间的推移而破裂,因此物有所值。
压力罐需要使用空气压缩机,因此价格稍高。但另一方面,它们可以说是制造无气泡树脂混合物和铸件的最佳选择。与真空室不同的是,真空罐可以与模具一起使用,适用于工作窗口期较短的速凝树脂,而且生产的铸件内 100% 无残留空气。
真空室的优势在于可用于多种应用,如石膏、混凝土或木材灌注的脱气过程,而压力罐通常只用于硅胶批量脱气。
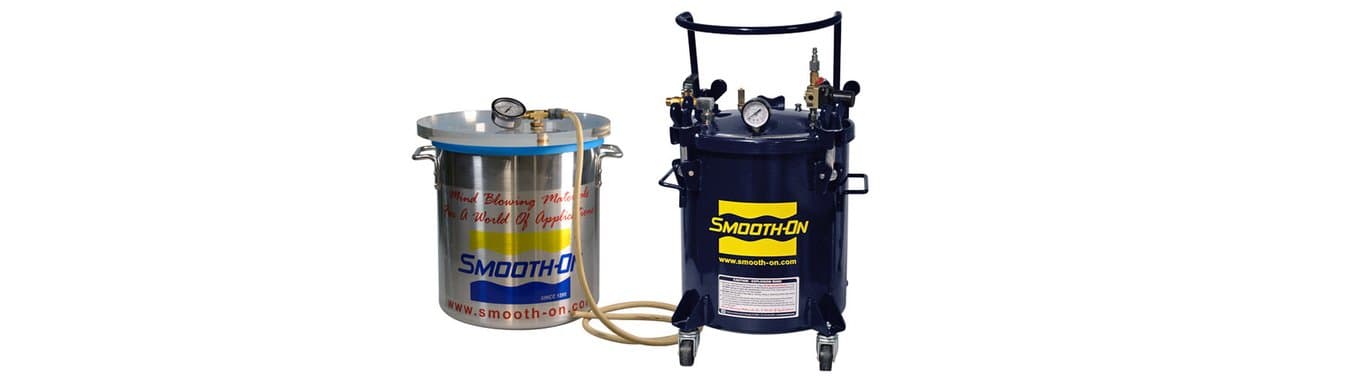
真空室(左)和压力罐(右)。
真空铸造材料
硅胶模具材料
铸造硅胶可分为锡固化硅胶和铂固化硅胶。锡固化硅胶又称冷凝固化硅胶,收缩率在 1%-4% 之间。虽然模型制造商会尽力补偿收缩率,但对于高公差应用,最好使用更高质量的铂固化硅胶或高温硫化 (HTV) 橡胶。
邵氏硬度为 40-50A 的硅胶制造的模具经久耐用,可重复使用数十次,同时便于脱模,甚至可用于因反向气流问题而反锁在刚模内的部件。建议使用半透明硅胶,以便观察模具内的气孔、气泡、杂质等一切情况。
一些优质的双组分硅胶品牌包括 SmoothOn、Elastosil、V-Sure 和 Silicones and More (S.A.M.)。直接从海外化工厂订购也能降低价格,同时还能根据买方的具体规格提供专业品质的产品,尤其是大宗订单。
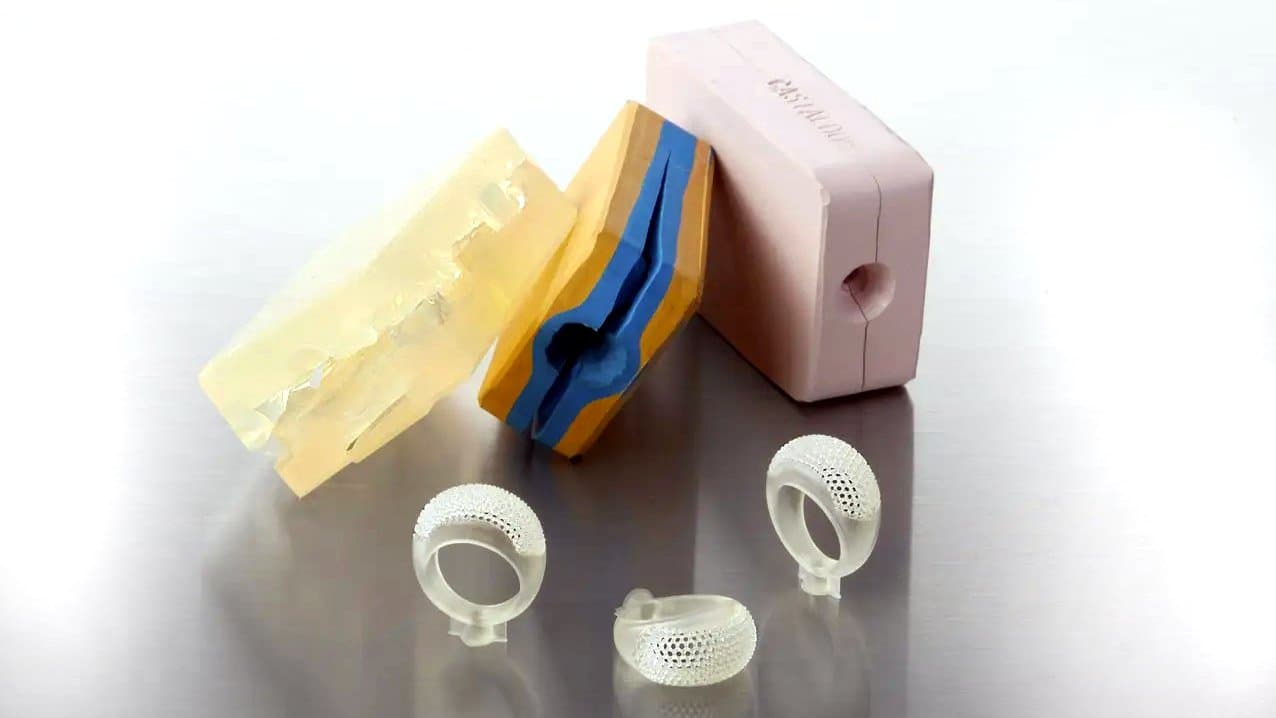
RTV 和 HTV 珠宝模具用于珠宝行业的生产过程,可捕捉复杂的丝线细节。
铸造聚氨酯树脂
真空铸造材料种类繁多,在柔韧性、弹性、刚度和硬度方面具有不同的特性:
-
类 ABS 的通用树脂
-
类玻璃填充尼龙的材料,具有优异的刚性
-
弹性类 TPE 材料,适用于可穿戴设备、手柄、按钮、垫圈和密封件等应用
-
类 PC(聚碳酸酯)
-
半透明或无水铸造聚氨酯(类 PMMA)
-
类 POM 或类 PU 耐热材料
还有一些特殊的聚氨酯铸造材料,如玻璃、蜡、环氧树脂、陶瓷、复合材料,以及食品级、导电、低密度和阻燃材料。一些知名品牌包括 FastCast 聚氨酯铸造树脂、Smooth-On 和 SRC 特种树脂。
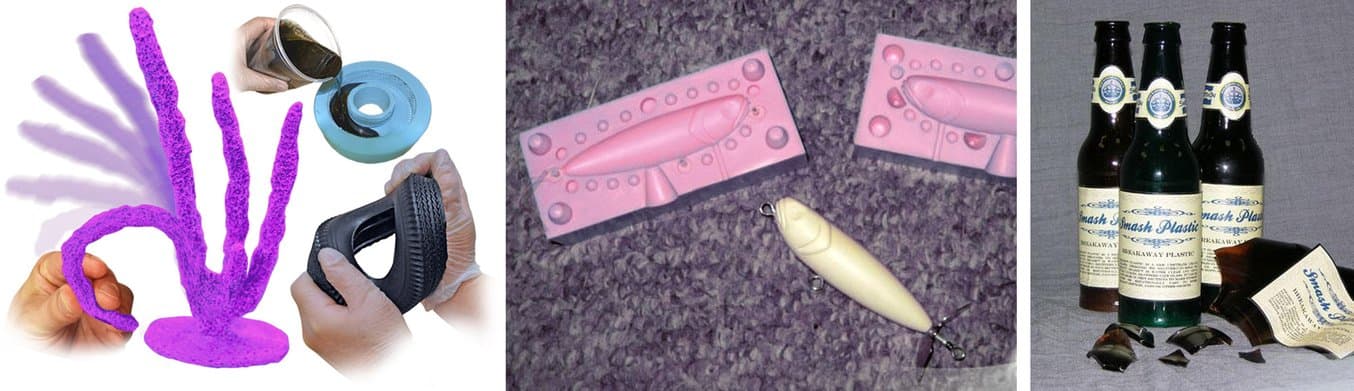
各种类型的聚氨酯树脂,从橡胶状到漂浮状再到玻璃状。
案例研究:使用 3D 打印模型进行聚氨酯铸造
Calibur Fencing
真空铸造非常适合用于预生产,以便在投资注射模具进行大规模生产之前测试并调整最终产品。Calibur Fencing 就是一个成功的案例,这是一种用于击剑记分的无线可穿戴设备。
设计师从简单原型开始测试设备的功能,然后采用 FDM 打印技术制作大致模型,以确定合适的外形尺寸。最终,Formlabs Form 3 SLA 打印机在制作代表成品的高质量原型时发挥了不可或缺的作用。
然后,团队使用 SLA 3D 打印部件作为模型,并将其运送给真空铸造服务提供商,以便为客户生产并测试设备,并在质量控制的同时快速获得成品。
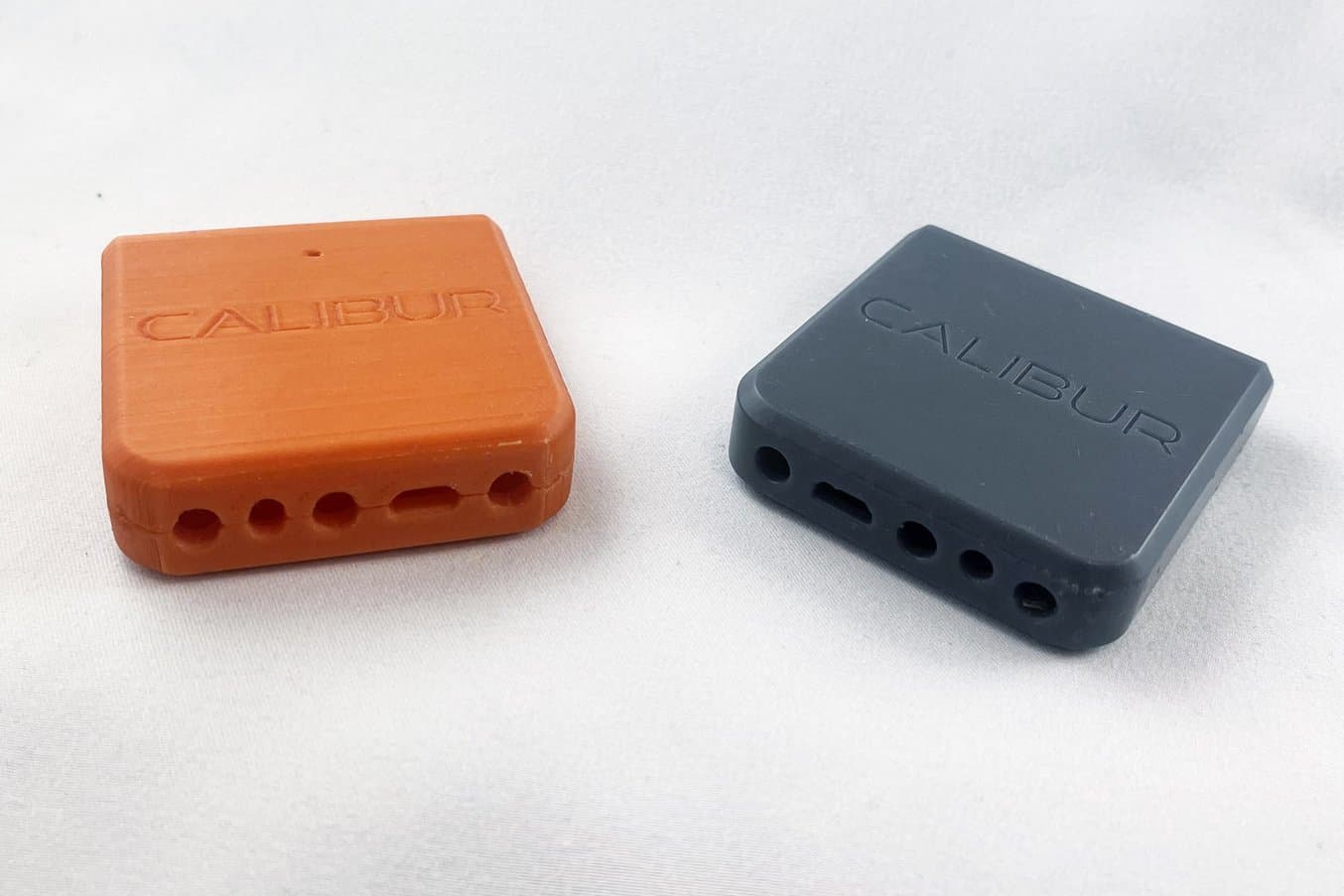
Calibur 的团队使用 FDM 3D 打印制作了首个模型,然后使用 SLA 3D 打印来制作逼真的功能性原型。
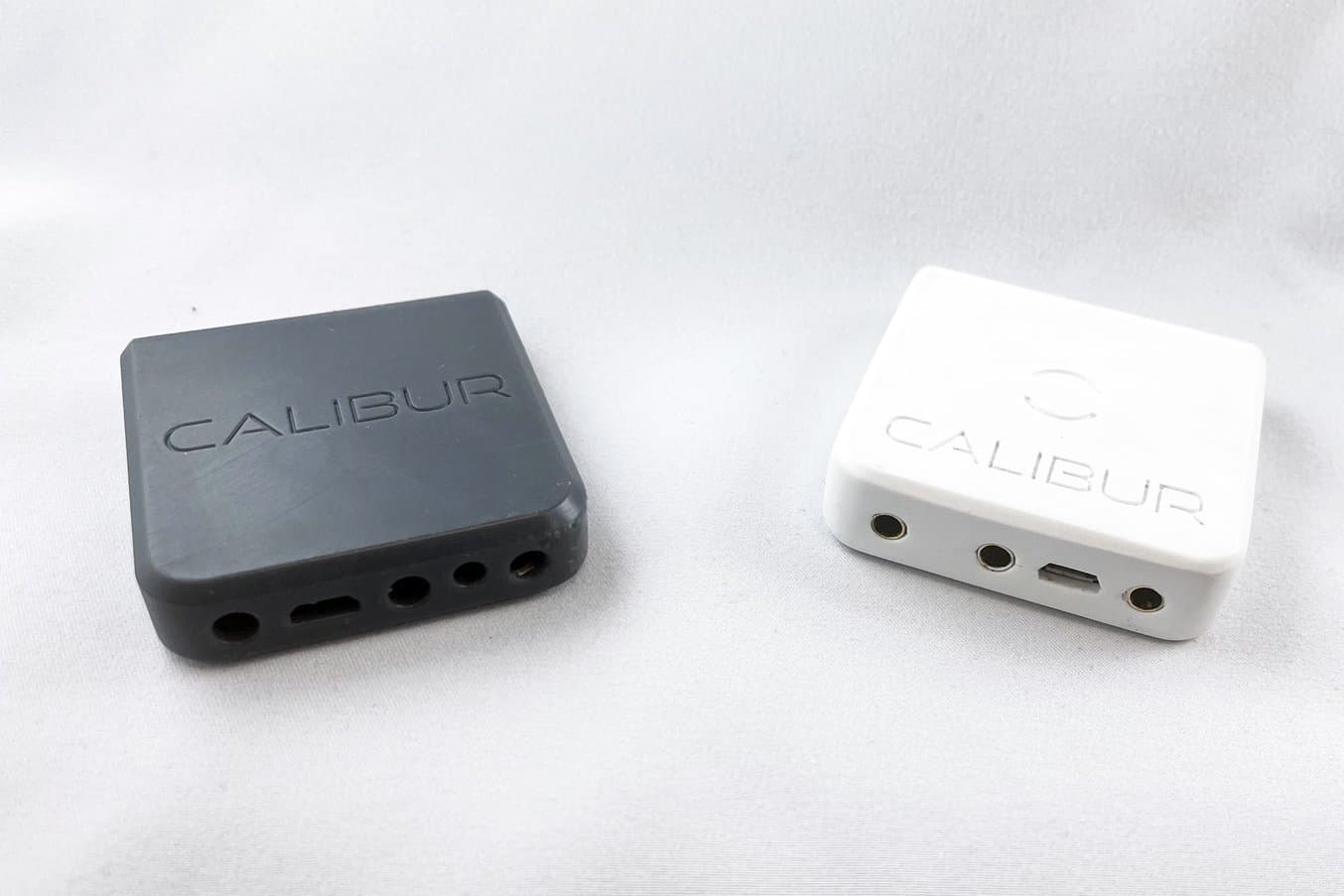
然后,该团队将 SLA 3D 打印部件用作真空铸造首批小批量成品测试装置的模型。
Louisville Slugger
Louisville Slugger 创新中心的团队发现,微小的事情也能产生重大的影响。他们从 1884 年起就开始生产棒球棒,深知如何使挥棒速度更快、力量更大。
Slugger 创新中心的员工坚持采用分析方法进行运动设计,并在 Formlabs 3D 打印解决方案的帮助下创造了一种握把附件。阶梯状的几何形状可以帮助击球手完美地握住球棒,从而实现最有力的击球。
与其他案例一样,Slugger 设计团队发现,在内部同时拥有 3D 打印和真空铸造能力可以加快设计迭代,同时快速积累经验。在 Form 3 SLA 打印机上以 50μm 层高打印的精细原型模型可用于创建阳模。聚氨酯铸造的强大能力使他们能够制作出经久耐用的可测试模型,其质量接近于硅胶注射成型的最终产品。
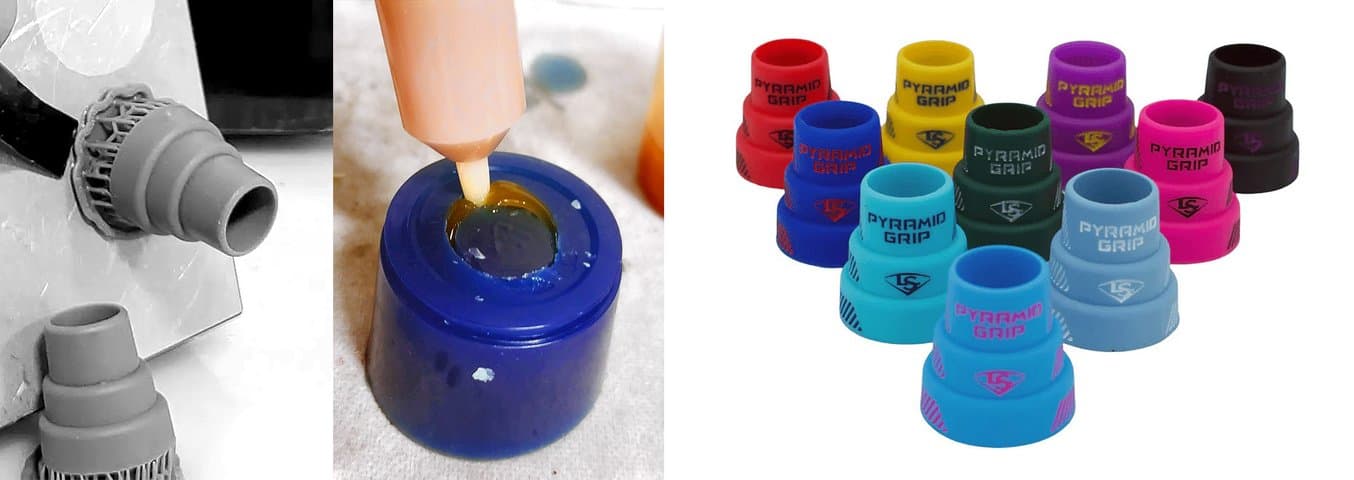
从 3D 打印阳模到内部铸造再到获得成品。
SiOCAST
SiOCAST 在将 3D 打印与树脂铸造相结合方面有着独特的经验。随着 MMORPG 网络游戏和 RPG 桌面游戏的兴起,对定制微缩模型的需求也迅速增长。该公司没有采用成本高昂的旋转铸造工艺,也没有采用真空铸造硅胶模具,而是开发了一种已经荣获专利的树脂注射系统,以与定制开发的机器和 HTV 橡胶模具配合使用。
他们的专有材料 SiOres 甚至能与温度高达 240˚C 的液化热塑性树脂结合使用。SiOCAST 机器比传统的树脂铸造速度快 20 倍,利用自动化和旋转多型腔模具,每小时可生产多达 1000 个部件。
所有母模均使用 Formlabs SLA 打印机进行 3D 打印,并使用 Formlabs 的自动清洗和固化系统 Form Wash 和 Form Cure 进行后处理。SLS 3D 打印技术可以生产可重复使用的浇道,进一步加快了工艺流程,每次铸造可生产多达 64 个微缩模型。
注射成型由于需要处理更严格的条件和粘性材料,因此偶尔会出现错误,而这些真空铸造模型无一例外都是原始模型的完美复制品,可以满足许多玩家的数字灵魂需求。
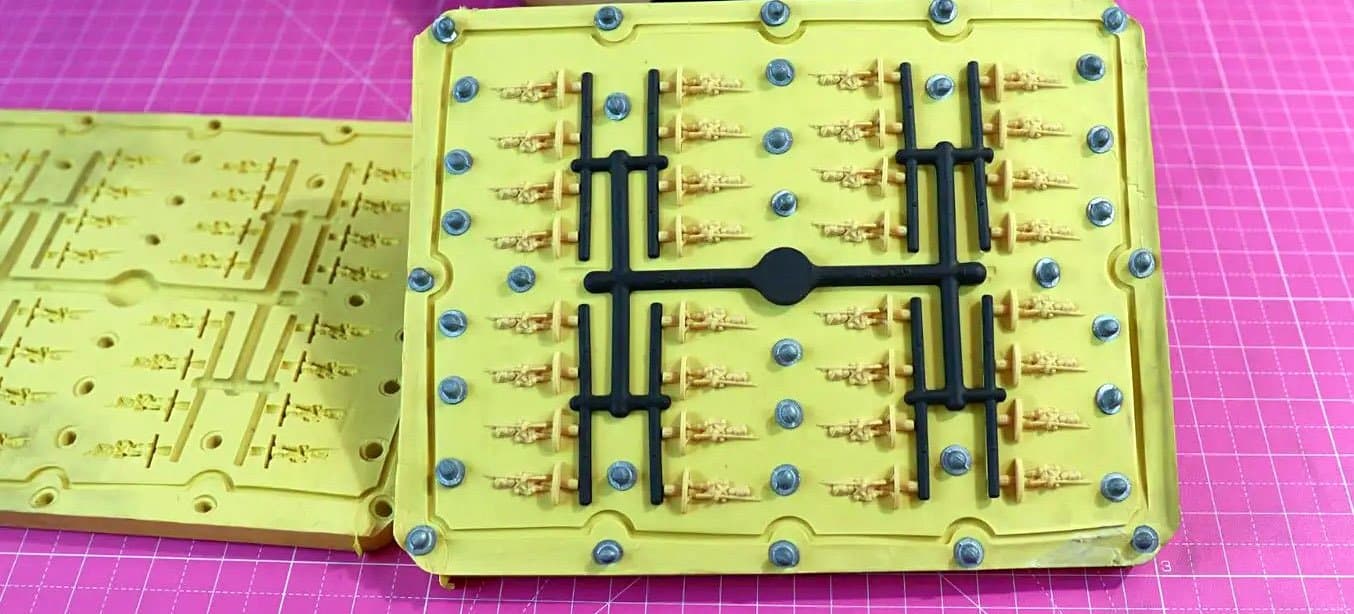
SiOCAST 使用专有 HTV 硅胶、SLA 母模和可重复使用的 SLS 尼龙浇道来批量复制微缩模型,最多可复制 1 万个。
开始使用真空铸造和 3D 打印
真空铸造是一种理想的产品成型工艺,无需工业级生产方法所要求的大量前期投资。可用于创建原型、外观性模型、预生产系列以及成品,几乎适用于任何应用。只要产品的几何形状可脱模,并符合真空铸造的特定设计准则,铸造模型就是母模的精确复制品。
真空铸造还得益于 3D 打印技术的最新发展,因为 3D 打印技术能够制作出高度精细、表面极其光滑完美的母模,可与真空铸造工艺完美配合。
但与 3D 打印不同的是,DIY 真空铸造不易于在内部完成,需要遵循严格的程序。凭借高精度、简单的工作流程和较短的交付周期,3D 打印为原型制造和小批量生产提供了真空铸造的可行替代方案。