如今,每三辆下线的新车中就有一辆至少有一个部件由 Brose 生产,Brose 是全球五大家族汽车供应商之一。100 多年前,Brose 公司由 Max Brose 在德国柏林创立,如今已从一家汽车配件贸易公司发展成为机电一体化系统的市场领导者。他们的产品(主要是座椅、举升门和车门总成)专用于世界上最大的汽车公司设计和生产流程:为宝马、沃尔沃、福特、奔驰、吉普等汽车巨头设计和生产产品。
Brose 的稳步增长以及与这些原始设备制造商的长期成功合作,部分归功于公司对持续创新和改进的承诺。3D 打印是 Brose 设计和终端制造流程中多项举措的核心,并帮助 Brose 适应和应对快节奏汽车行业的所有变化。
我们访问了位于密歇根州奥本山的 Brose North America(其美国总部)以及位于密歇根州新波士顿的 Brose New Boston(其最大的终端制造工厂之一),了解他们如何将功能强大的立体光固化 (SLA) 和选择性激光烧结 (SLS) 3D 打印机投入使用。该领域的增材制造技术领导者-座椅部门原型经理 Matthias Schulz 向我们讲述了 Brose 如何在整个流程中使用 3D 打印技术,从设计到制造,再到在紧迫的时间内为原始设备制造商生产终端部件。
“我们目睹汽车行业发生了日新月异的变化,尤其是在过去的五年中。新产品的开发时间大大缩短。这就要求我们采取相应的行动,也就是进一步应用增材制造技术。这符合我们的利益,因为它还能缩短模具等的准备时间,并帮助我们在以后的生产中更快地交付部件。”
Matthias Schulz,Brose North America 座椅原型经理
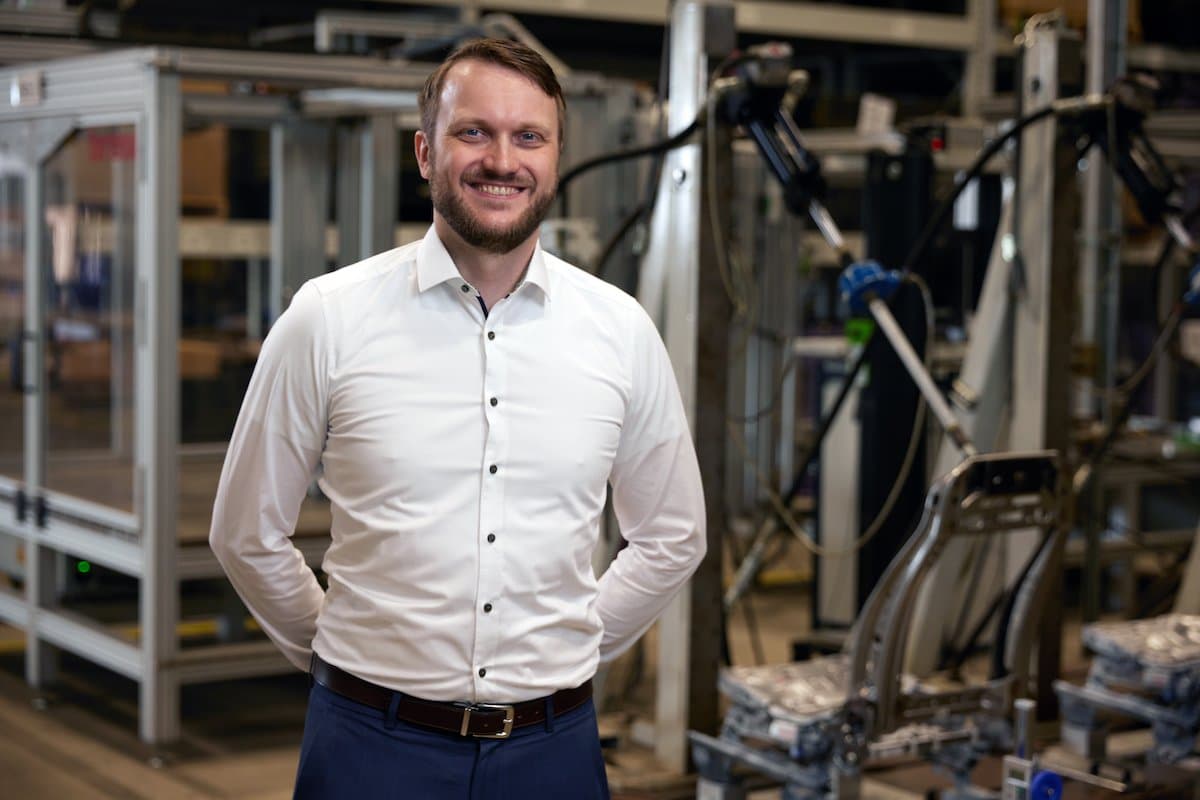
网络研讨会点播:Brose 将 SLS 用于终端汽车生产
在本次网络研讨会点播中,Brose North America 座椅原型经理 Matthias Schulz 演示了 Brose 如何将 SLA 和 SLS 技术应用于从快速焊接夹具到 25 万个成品部件的生产流程中。
原型超越一次性产品
3D 打印技术非常适合并常用于原型制造应用。虽然 Brose 确实采用了一系列熔融沉积成型 (FDM)、SLA 和 SLS 3D 打印机来制造原型,但其产量并不一定能满足概念验证部件的需求。对 Brose 来说,原型的一般产量接近 500 或 1000。
“3D 打印的使用规模在扩大。‘原型制造’意味着我们必须打印几百个部件,具体产量主要与必须进行的测试数量有关。不仅要满足内部和外部标准,还要满足联邦要求。当然,这就要求我们不仅要完成一定数量的部件,还通常要为原型打印七八百个部件,”Schulz 说。
海外订单量使 SLA 成为最佳选择:橡胶座椅长度调节阻尼器
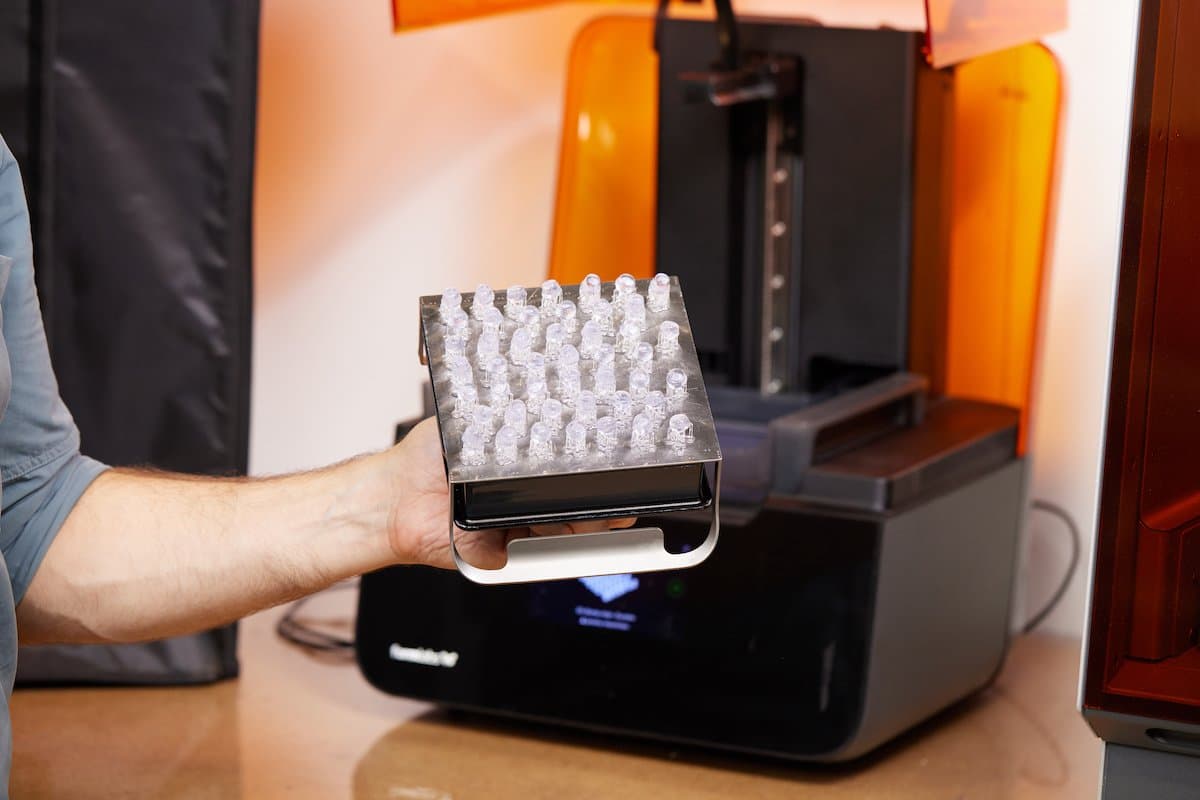
这些原型是小型阻尼器,用于降低金属座椅总成撞击座椅框架的声音并减少撞击感。从海外订购这些阻尼器的最低订货量为数百万件,因此 Schulz 及其团队使用 Form 系列打印机打印了这些阻尼器进行测试。
在一个项目中,原型团队需要使用安装在座椅总成中的软硅胶阻尼器。当座椅在其框架上向前移动时,该部件可以抑制声音,并改善座椅总成移动的触觉和声学反馈。如果从 Brose 的海外系列供应商处订购这些部件,最低订购量要达到数百万个,而 Brose 只需要几百个用于初步设计测试。
除了订购数百万个部件并将其运往海外的高昂成本外,周转时间也长达数周,此外,还需要储存数百万个不需要的部件,从而造成浪费。Brose 并没有订购部件,而是利用现有 CAD 在 Form 4 上快速 3D 打印了几百个部件。这些部件在一周内就准备就绪,该解决方案降低了整个项目的总体成本,缩短了交付周期。
“我们使用 Form 4 打印这些阻尼器,其成本远远低于将这些部件空运到这里以及因为按最低订货量订购而产生的库存,因为这需要订购数百万个此类部件。我们可以迅速获得这些部件,无需等待。”
Matthias Schulz,Brose North America 座椅原型经理
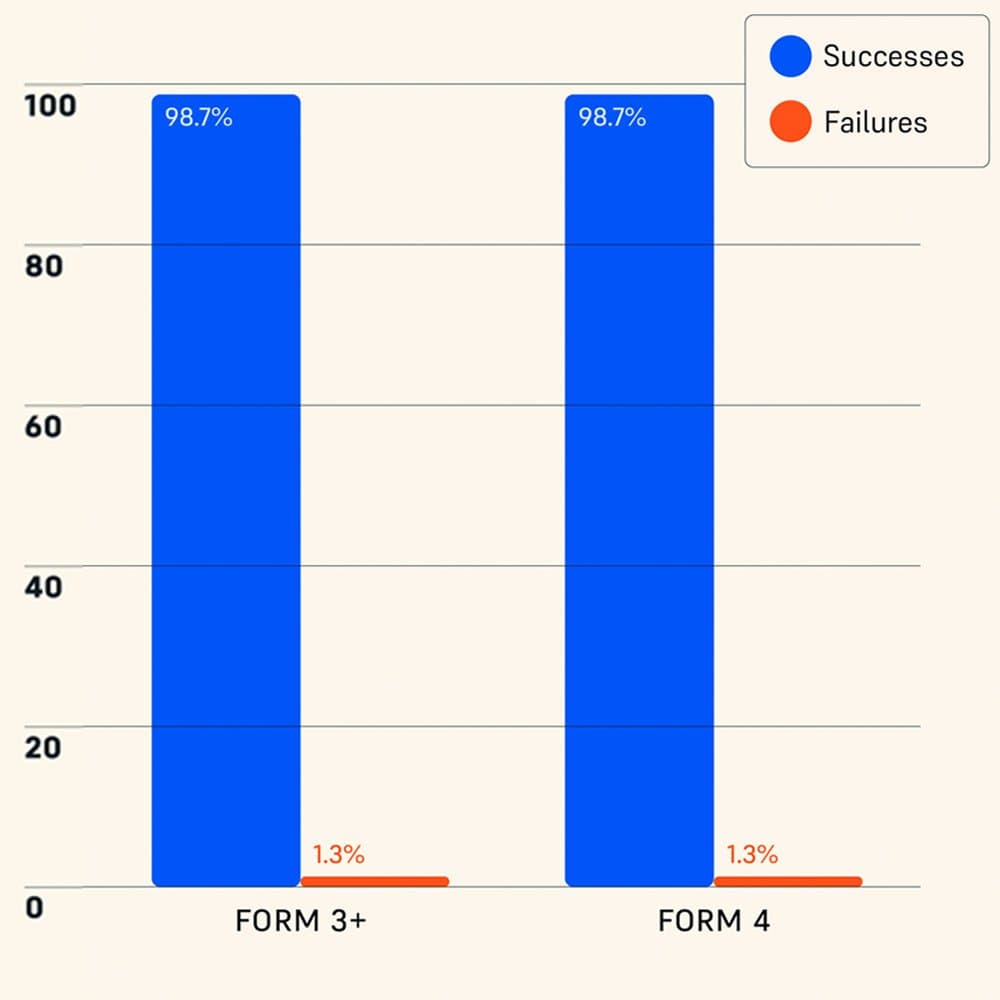
经独立测试的 Form 4 和其他树脂 3D 打印机的可靠性
据一家全球领先的独立产品测试机构测定,Formlabs Form 4 的打印成功率高达 98.7%。请在我们的白皮书中阅读测试方法的完整说明并查看测试结果。
将 SLA 和 SLS 结合用于大批量原型制造
随着部件的复杂性、尺寸和所需体积增加,Brose 转而使用三台 Fuse 系列 SLS 3D 打印机来制作原型和产品。SLS 3D 打印技术具有自支撑打印床,可实现充分打包的批量生产,烧结尼龙的强度和机械性能使该技术成为成品部件的理想选择。在最近的一个项目中,Brose 的增材制造技术团队同时使用了 SLA 和 SLS 技术来制作座椅悬挂垫的原型。
他们在 Form 系列 SLA 3D 打印机上使用 Durable Resin 打印了透明的柔韧部件,并在 Fuse 系列打印机上用 Nylon 12 GF Powder 打印了垫子的连接管。每个垫子原型有六个 SLS 部件和三个 SLA 部件,团队总共组装了 150 个完整的垫子,作为完整座椅总成的一部分进行测试。
利用内部的快速原型制造工具,Brose 能够在不使用工具或外包的情况下设计、测试和迭代座椅总成产品的重要部件。“有时,SLA 和 SLS 的组合就是解决方法,比如这个座椅悬挂垫。二次成型模具非常复杂且昂贵,因此我们设计了可以搭扣在 SLS 线上的部件,并将 SLA 部件以“原始状态”安装在线上,然后进行固化,”Schulz 说。
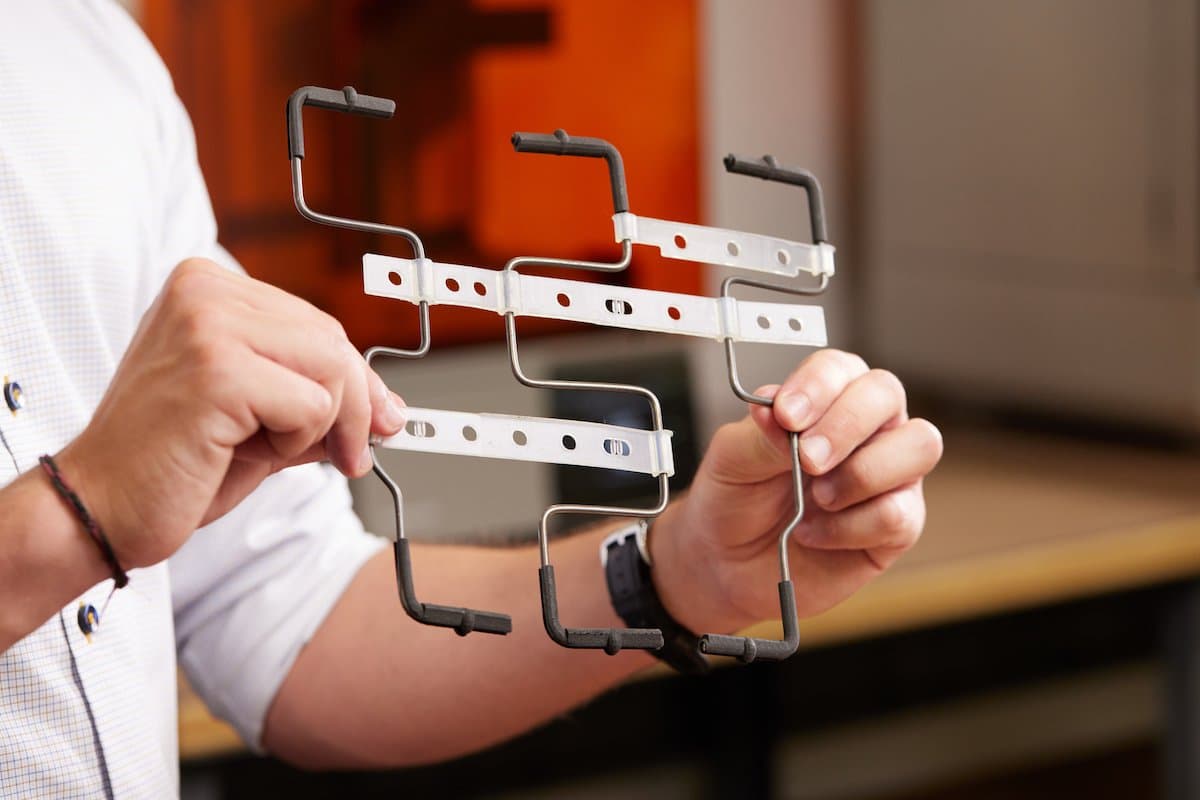
这款座椅悬挂垫既包含 SLA 部件(Durable Resin,半透明材料),也包含 SLS 部件(Nylon 12 GF Powder,深灰色材料)。测试需要 150 个此类完整装配,包括 900 个 SLS 部件和 450 个 SLA 部件。
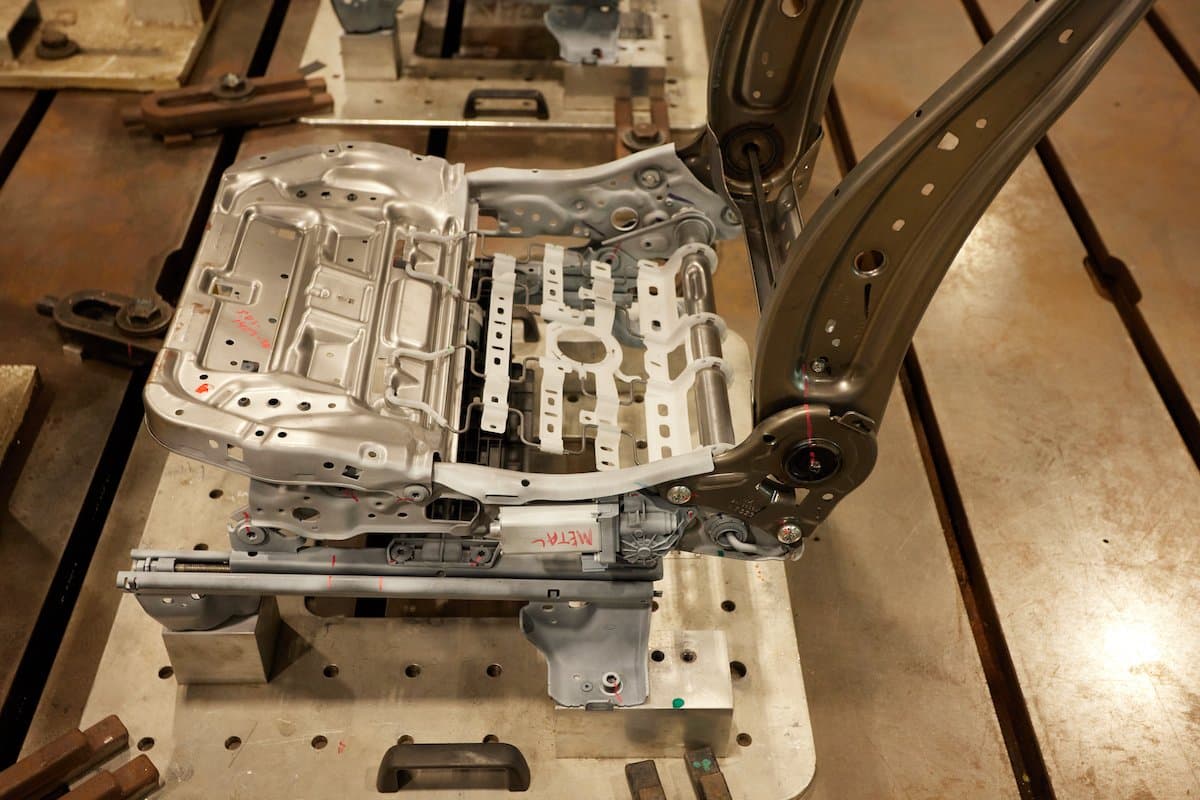
原型和成品生产版本(如上图)都要经过疲劳测试,以便模拟多年的使用情况。
制造辅助工具简化生产
在 Brose,增材制造技术不仅用作原型制造工具,还作为 2022 年启动的“工厂应用增材制造技术”计划的一部分,Brose 正在将这项技术整合到所有部门。汽车制造过程不间断且高度受控,流程的每一环节均经精简和优化,以提高效率、安全性和产品卓越性。
Form 4L 当天完成机器人焊接固定装置
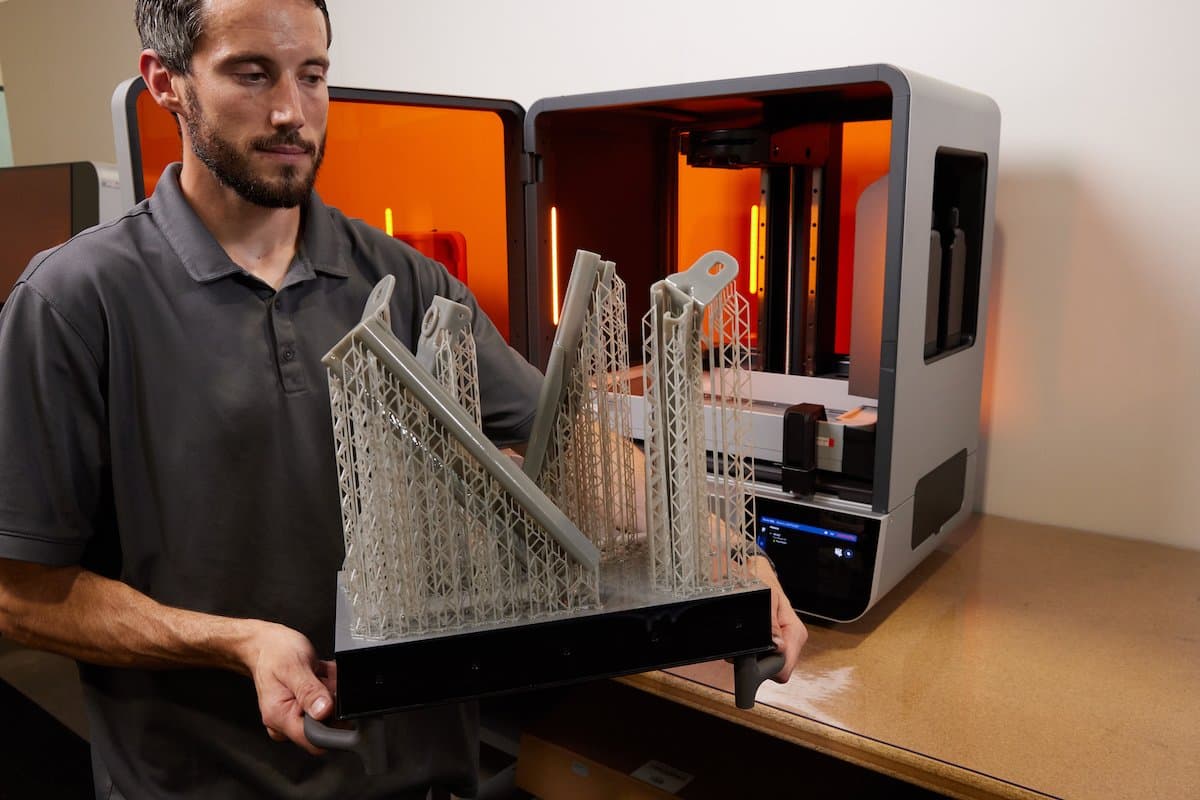
Form 4L 使当天生产大尺寸部件成为可能,比如使用 Fast Model Resin(快速模型树脂)打印的焊接配合固定装置。
在汽车供应链的每个阶段,金属部件都是整个产品的关键组成。这可以理解,毕竟焊接是装配过程的重要一环。在 Brose North America,Brose 的增材制造技术团队负责操作 SLA 和 SLS 打印机,他们的焊接机器人需要在不同的产品线之间不断切换。在工厂里,焊接机器经编程只操作一条产品线,但在总部,他们有两台机器人负责焊接每条不同产品线的座椅原型。
每次机器人需要切换到新的产品线时,焊接部门就必须重新对其参数进行编程。使用原型金属导轨对焊接机器人进行编程的成本很高,而且在焊接站准备编程设备时,往往无法获得这些原型金属导轨。3D 打印提供了一种快速、经济的解决方案,同时满足了这些安装部件的生产速度和尺寸精度要求。
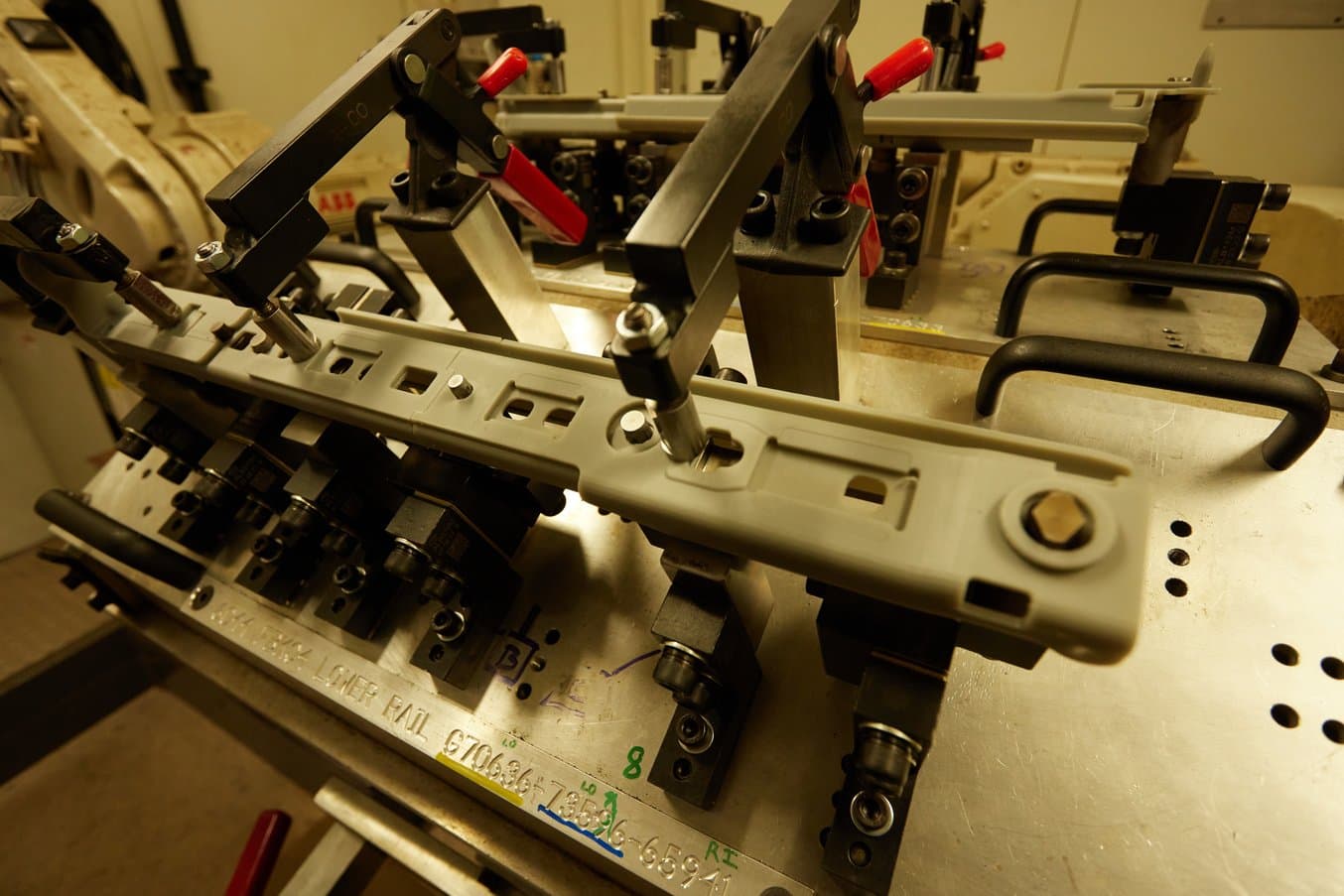
该座椅部件用 Fast Model Resin 在 Form 4L 上打印而成,并经清洗、固化后组装到机器人焊接机上,整个过程只用了不到三个小时。因此,团队可以通过编程,使机器人快速运动。
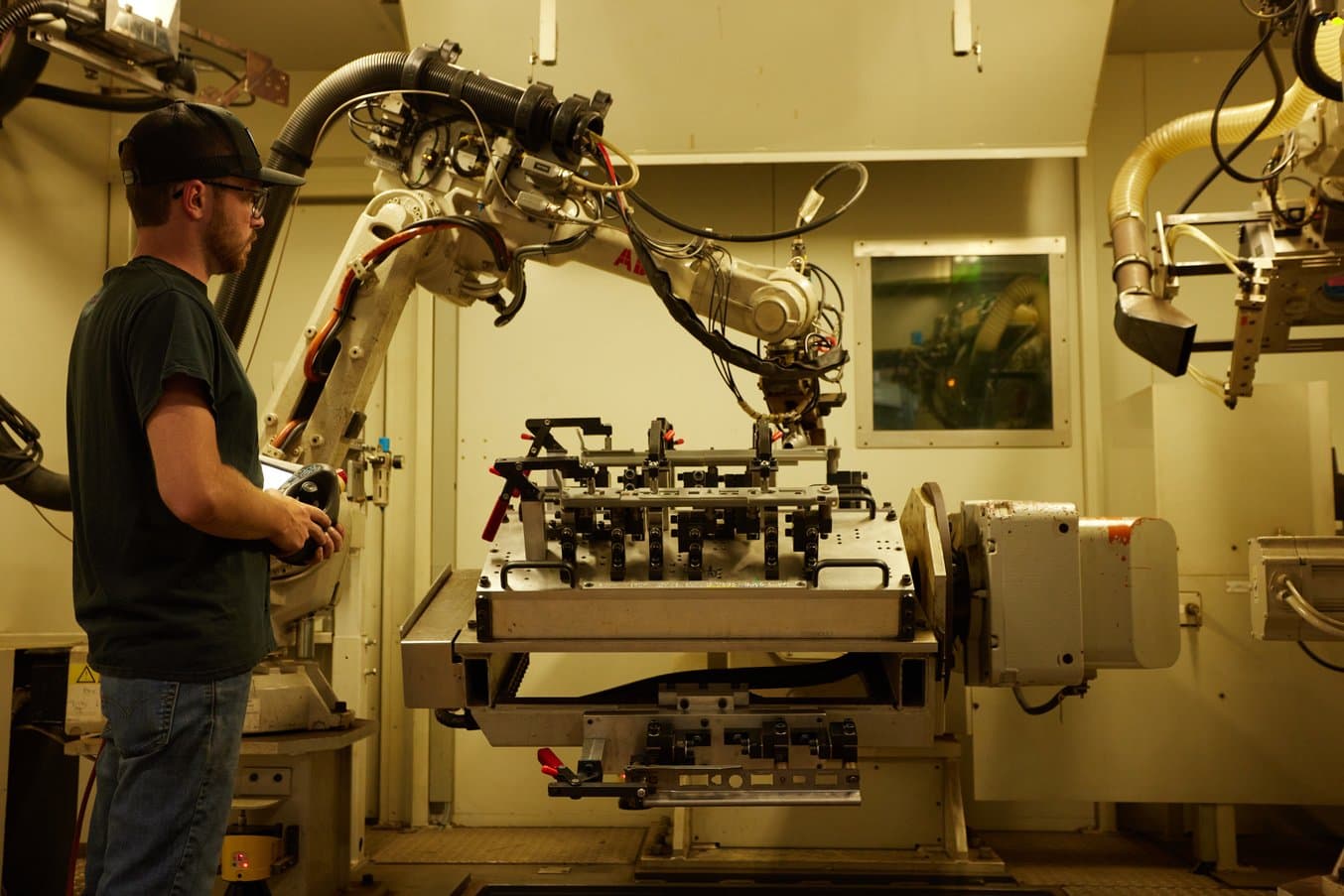
诸如此类配合固定装置可以帮助焊接团队在不同产品线之间快速高效地过渡。这些固定装置精度高、价格低廉,而且可以无限复制,以便在需要更改或更换时使用。
周二上午,Brose 团队打开了新到的 Form 4L 大幅面树脂 3D 打印机。设置过程仅需 30 分钟,他们很快就能使用 Fast Model Resin 打印出大型焊接安装部件。这些部件分为四部分,几乎占满了整个成型体积。尽管尺寸很大,Form 4L 还是在不到 2 小时的时间内完成了打印,经过快速清洗和后固化,45 分钟后,该固定装置就安装到了焊接机器人上。
“新型 Formlabs Form 4L 支持快速打印大型部件。例如,我们使用 Form 4L 为焊接单元打印安装部件只需几个小时,而无需过夜。如此一来,Brose 焊接专家就可以在金属冲压部件到达之前对机器人进行编程。借助新型 Fast Model Resin,我们可以比以往更快地获得所需的细节和刚度。”
Matthias Schulz,Brose North America 座椅原型经理
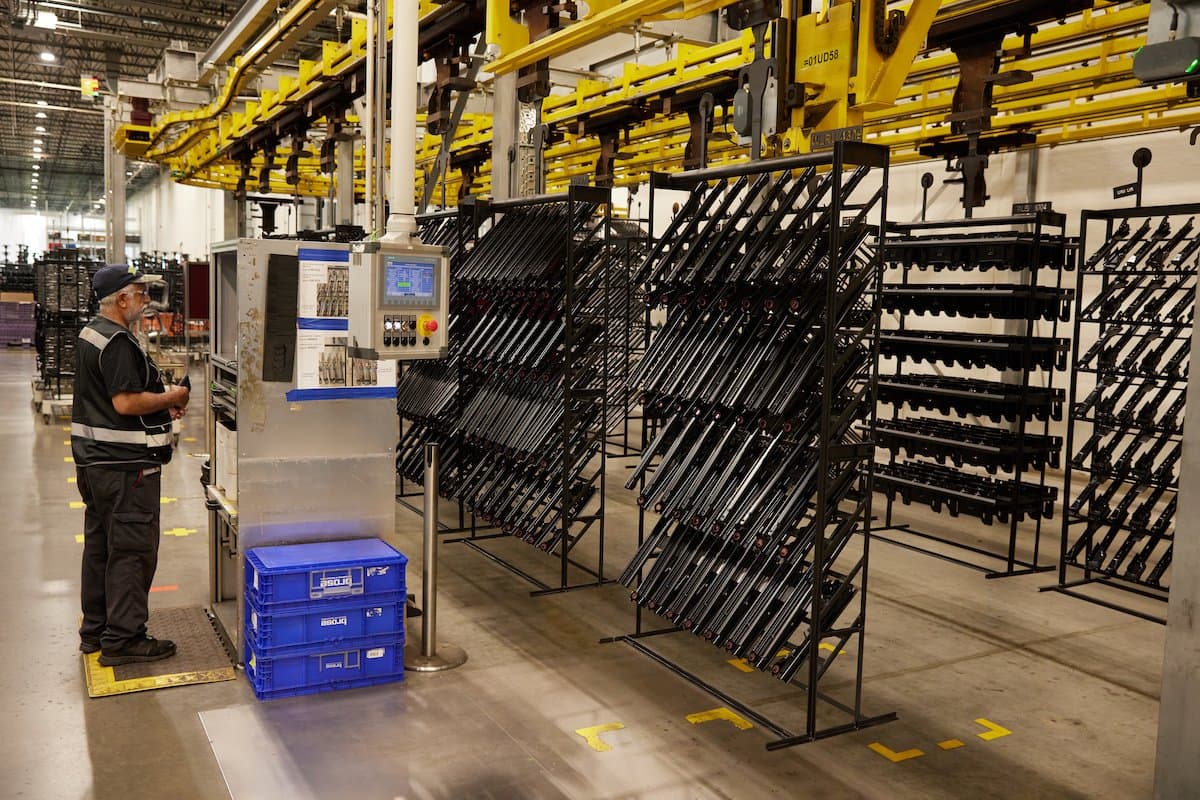
在 Brose New Boston,数以千计的座椅导轨(如上图所示)焊接在一起,形成座椅总成的基座。焊接参数测试是制造过程中不可或缺的一部分。
Brose North America 总部通过原型和 3D 打印安装部件确定的焊接参数,实现了焊接座椅框架的批量生产。上图中的座椅导轨将在 Brose New Boston 使用大型机器人焊接机进行组装。
线路末端 (EOL) 连接器降低 Brose New Boston 运营成本
Brose 的新波士顿工厂位于底特律市中心以西约 30 分钟车程的地方,该团队利用 3D 打印技术制造出定制的制造辅助工具,从而简化了装配流程。3D 打印部件在集成到生产中之前需要经过严格的测试,一旦获得批准,将有助于减少浪费、缩短生产时间并保持机器稳定运行。
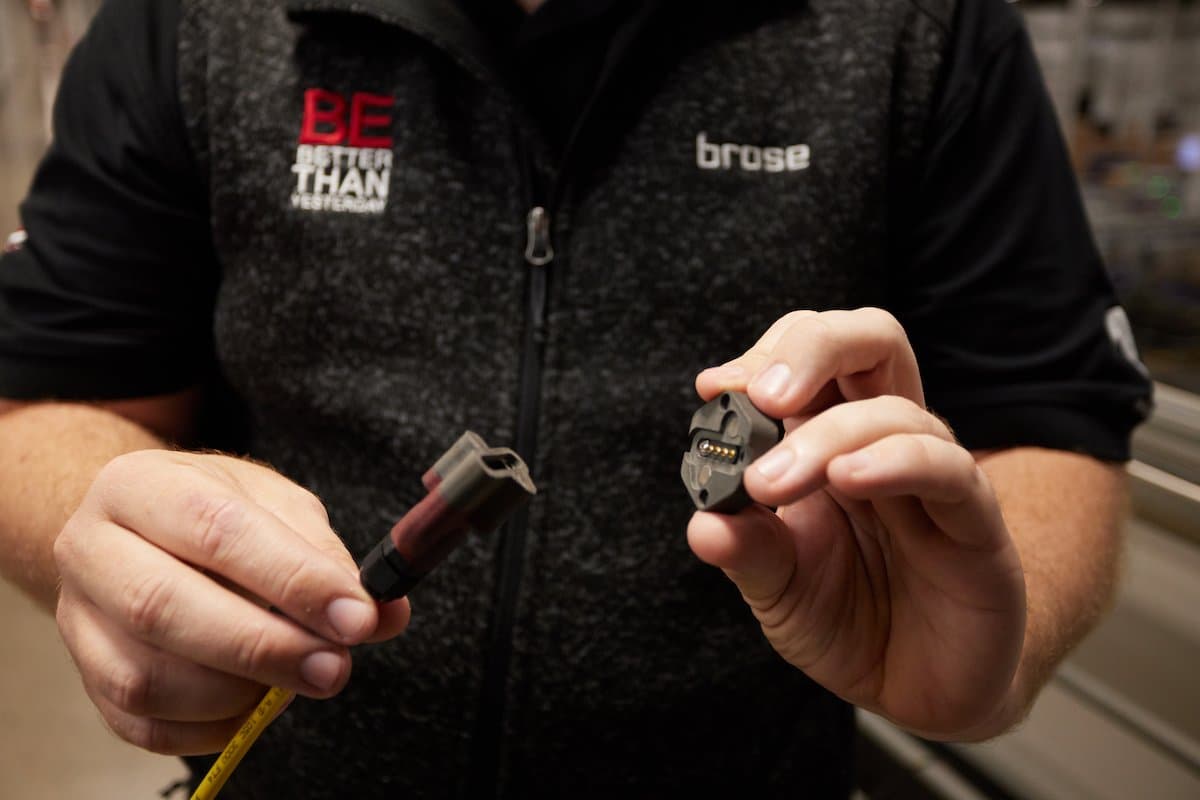
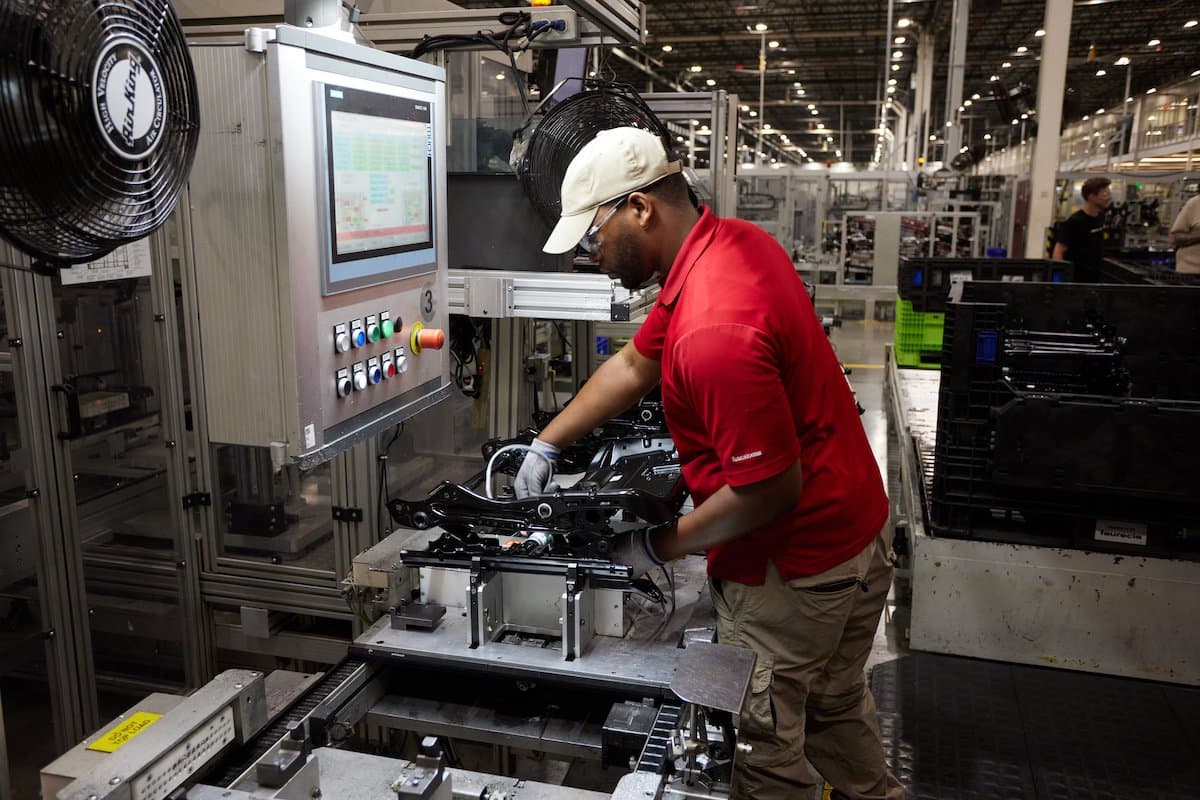
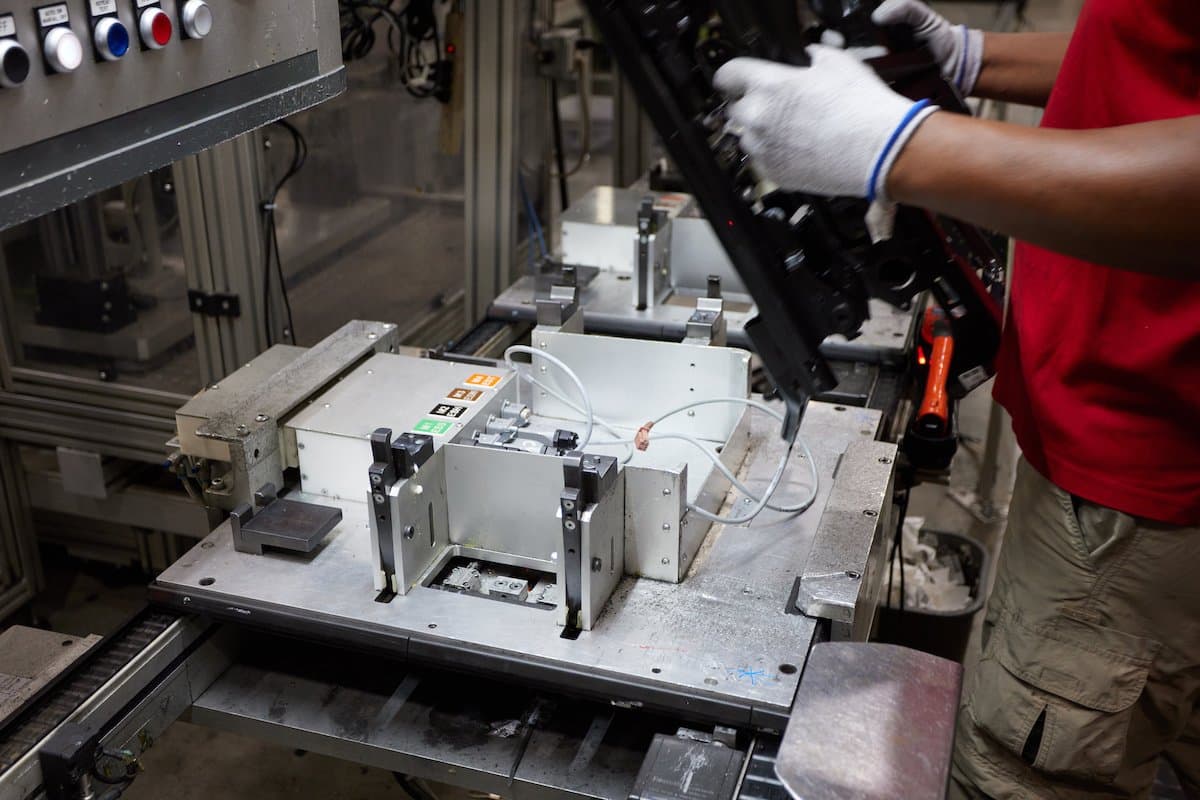
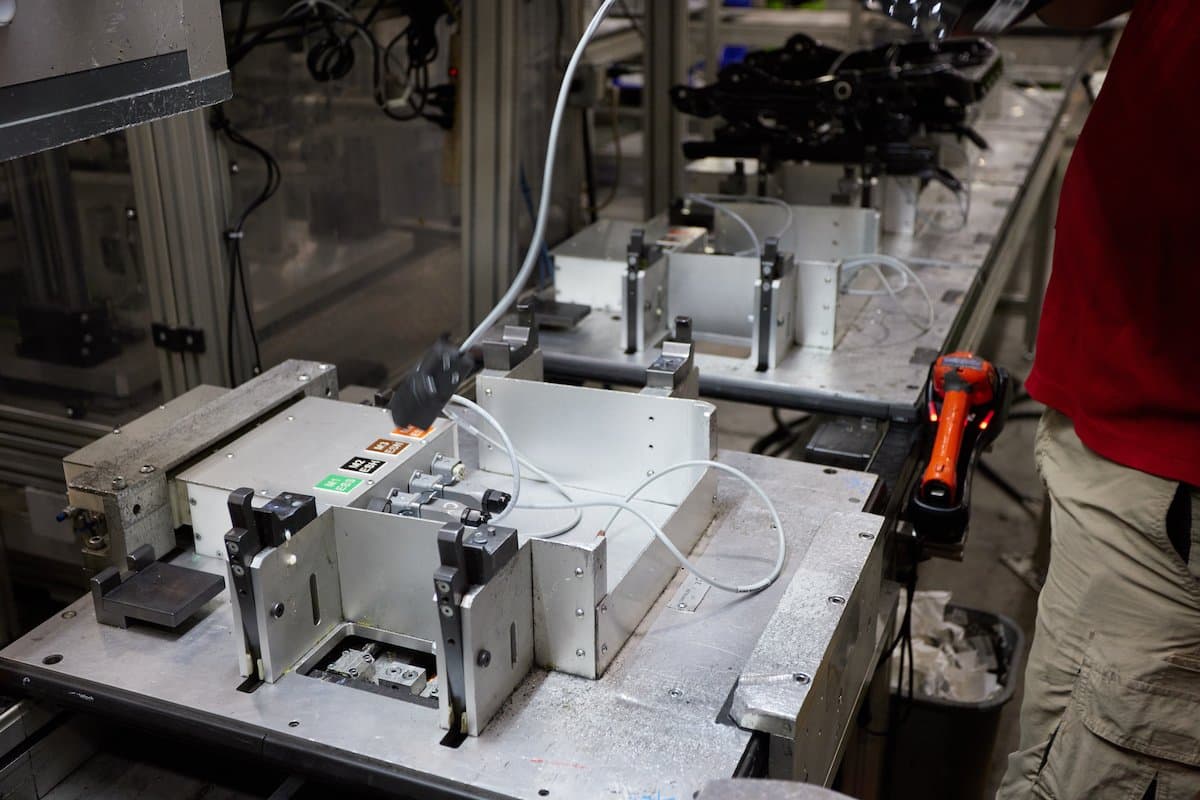
这种线路末端 (EOL) 连接器在座椅总成流程的最后阶段使用。技术人员将座椅框架连接到电源并进行最后检查后,将其取下,进入下一个流程阶段。很多时候,技术人员会忘记电气连接,在拆卸座椅时会折断电线,造成几百美元的装配线损失,并导致生产暂停。
增材制造技术团队与新波士顿团队合作设计了一种磁性连接线。它可以很容易地连接到生产线和座椅框架上,但如果技术人员在没有手动取下连接线的情况下拉开座椅框架,连接线就会断开,不会造成任何损坏。“我们使用 3D 打印制造辅助工具来减少机器的磨损,从而更快地在生产线上进行维修。这减少了生产中的停机时间,也帮助我们提高了整体产量,”Schulz 说。
终端汽车部件的批量间隙生产
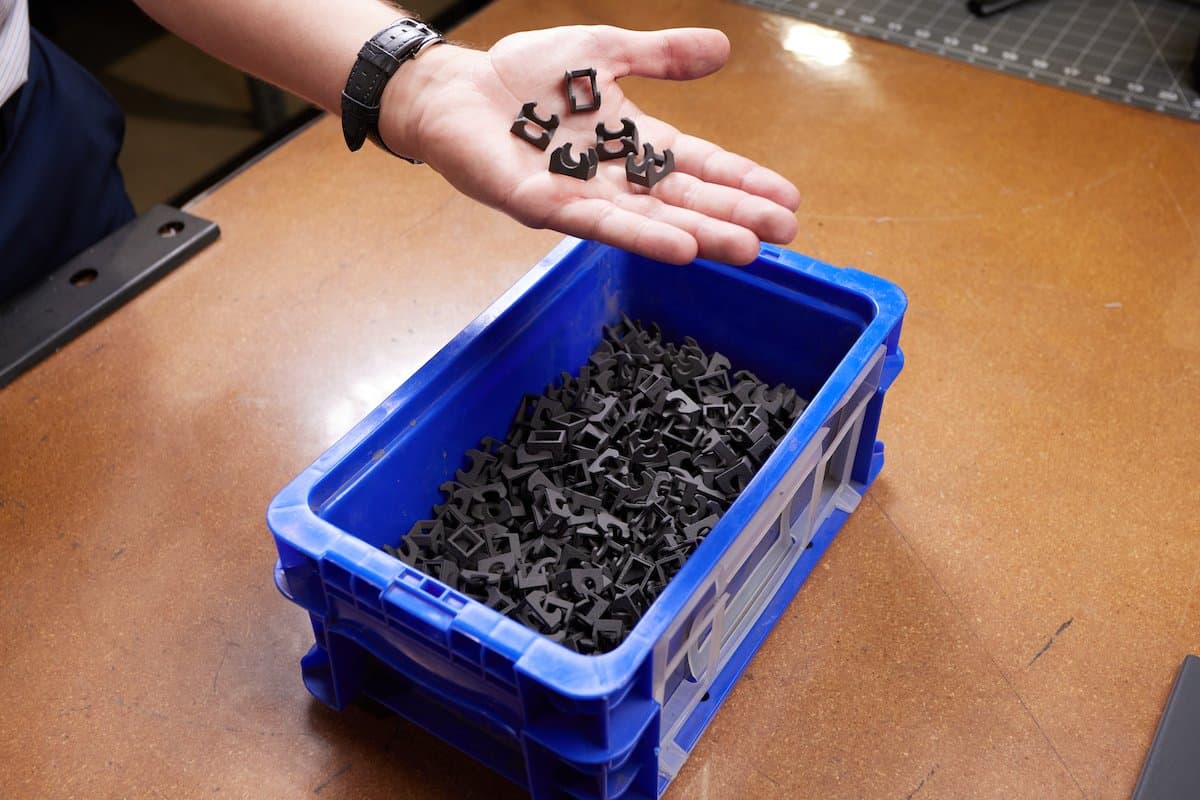
Brose 将为宝马 X7 的座椅总成 3D 打印了 25 万个此类固定夹。
正如 Schulz 所说,汽车行业的变化日新月异,尤其是在过去五年中。电动汽车的兴起、对定制功能日益增长的需求以及对供应链的担忧,促使原始设备制造商加大对增材制造技术的投资,旨在将其作为一种可靠的生产替代方案。
“确实有越来越多的客户要求采用增材制造技术。对于终端客户来说,这也是客户界面的一部分,他们希望自己的汽车更具个性化,因此原始设备制造商对增材制造技术的需求也日益增加,”Schulz 说。
3D 打印终端部件,尤其是在高度管制的汽车行业,并不总是可行的。Brose 增材制造团队确保只有在硬件和材料的质量能够可靠地提供高性能部件时,他们才会转向终端生产。
“我们决定在此与 Formlabs 联手合作。之所以这样做,是因为材料的可用性和打印的一致性都有了显著提升,现在这项技术已经可以在汽车行业大显身手了。我们面临的问题是客户对安全和耐用性方面的担忧,尤其是原始设备制造商。我们正在努力排除这个问题。通过与 Formlabs 合作,我们已经证明了部件可以像在目前的宝马 X7 上那样正常运行。”
Matthias Schulz,Brose North America 座椅原型经理
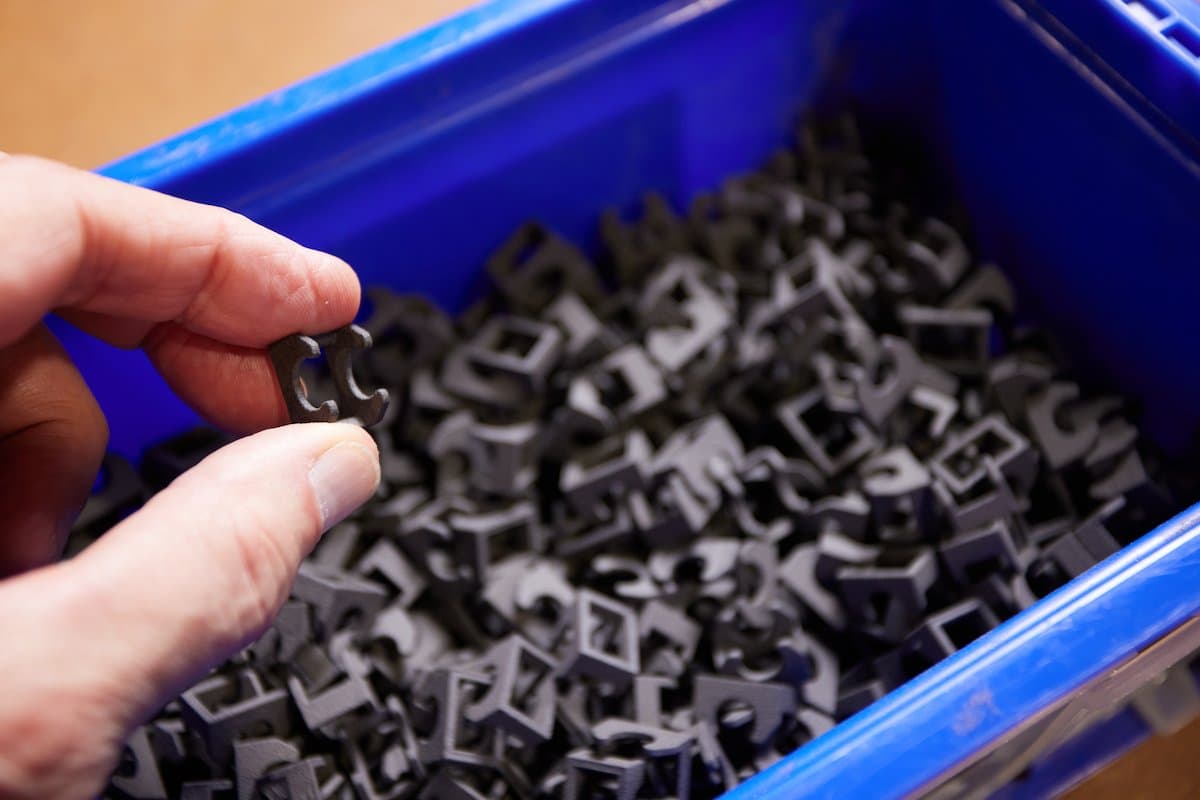
应用:宝马 X7 座椅部件
工作流程:3D 扫描、迭代,然后在 Fuse 系列 SLS 3D 打印机上进行 3D 打印,用于终端生产。
生产量:25 万
成型详细信息:
- 打印机:Fuse 1 和 Fuse 1+ 30W
- 材料:Nylon 12 GF Powder
- 构建量:每成型室内 1440 个部件
- 每月打印部件数量:1.6 万个
为什么选择 3D 打印?
- 间隙打印,以便为工具的可用性留出过渡时间。
Brose 将 3D 打印用于终端生产,作为传统制造的一种经济、快速的替代方案。当原始设备制造商需要部件或对现有部件进行改动时,如果该部件无法以足够快的速度进行工具化和批量生产,Brose 的增材制造部门就会对其进行 3D 打印适用性评估。其中很大一部分工作是逆向工程和扫描现有部件。
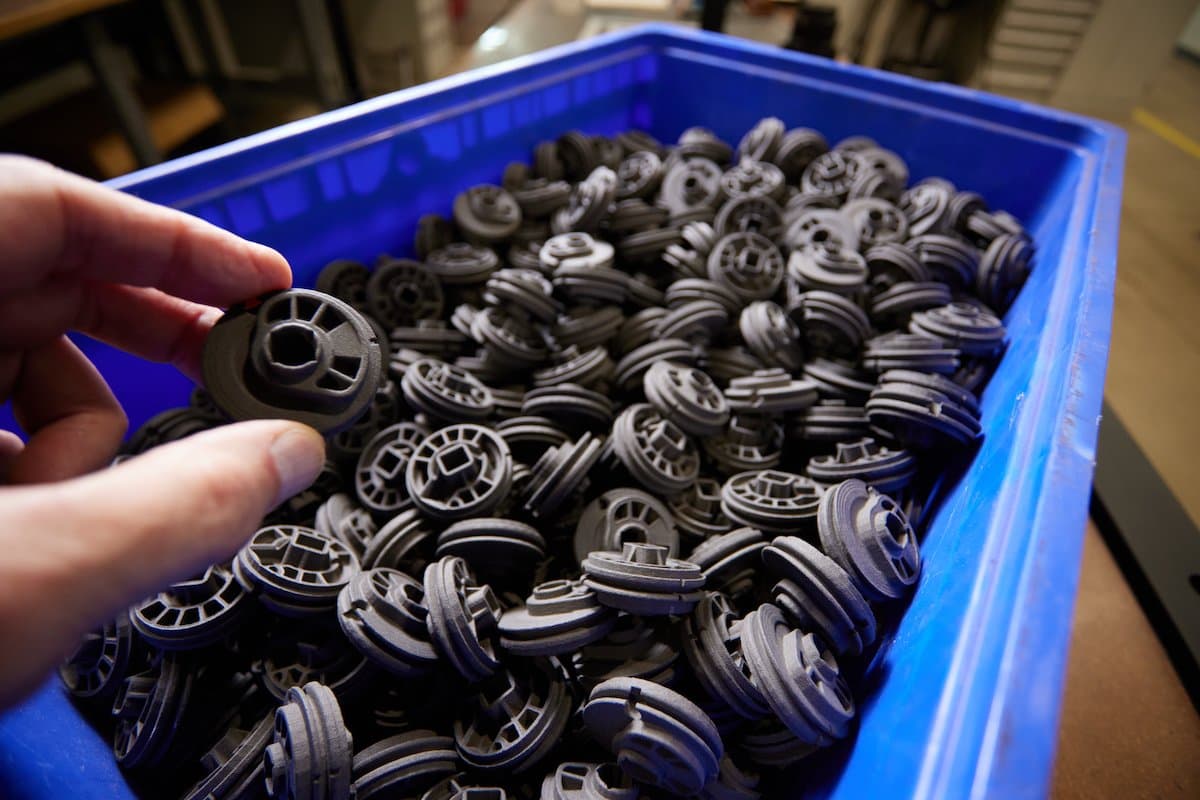
应用:鲍登管释放器
工作流程:3D 扫描、迭代,然后在 Fuse 系列 SLS 3D 打印机上进行 3D 打印,用于终端生产。
打印量:2 万
成型详细信息:
- 打印机:Fuse 1 和 Fuse 1+ 30W
- 材料:Nylon 12 GF Powder
- 产量:每个成型室 144 个部件,每周打印 1000 个部件
为什么选择 3D 打印?
- 间隙打印,以便为工具的可用性留出过渡时间。
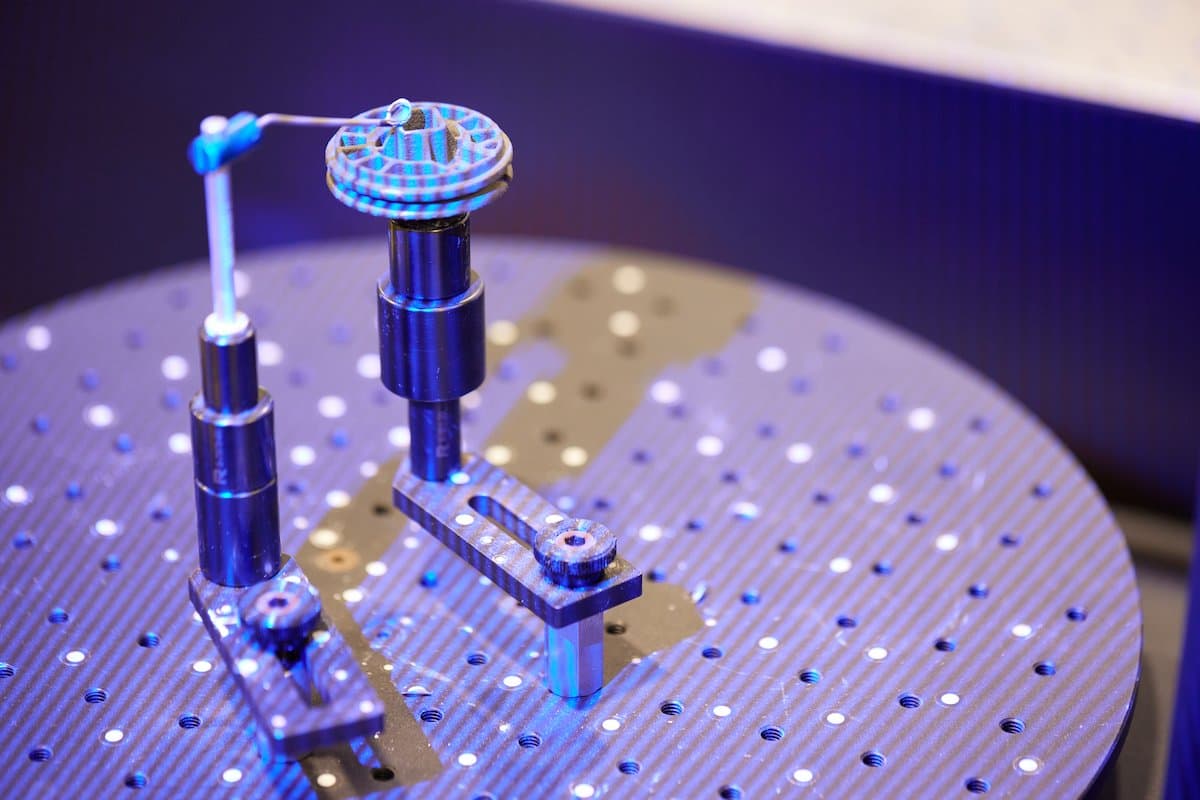
Brose 经常会扫描现有部件或以前的迭代产品,以便在 CAD 中进行修改,并在同一天对更新版本进行 3D 打印。
该部件为鲍登管释放器,2 万个此类部件由 Brose 使用 Fuse 系列 SLS 3D 打印机机组打印制成,并安装在一家大型知名原始设备制造商的最终座椅总成中。
“Brose 决定在公司内部使用 Formlabs 的 SLS 技术,因为该技术可以十分快速地进行 3D 打印,而且与 SLA 相比,SLS 的后处理要求更低。我们可以大批量打印,对于间隙打印或其他与 OEM 相关的终端客户部件来说非常必要,”Schulz 说。
三台 Fuse 系列 SLS 3D 打印机不间断生产原型、制造辅助工具和成千上万的成品部件,可靠性和一致性是关键。该团队选择使用 Nylon 12 GF Powder,因为其尺寸精度高,与注射尼龙非常相似,即使在大批量生产时也能保证尺寸精度。每次完成完整构建后,对 Fuse 1 或 Fuse 1+ 30W 进行快速维护检查仅花费 15 分钟左右,从而确保了生产的连续性和高效性。
“Formlabs 深谙如何制造一台易于维护的打印机。设备非常可靠,几乎没有出现过一次打印失败,因此我们可以致力于打印更大批量的部件,并有信心将其投入生产,”Schulz 说。
从 0 到 60:3D 打印机在汽车行业加速发展
Brose 致力于不断改进,这促使他们投资于增材制造和自动化等新技术,以简化流程并为每位客户提供创新解决方案。随着 3D 打印技术在公司中发挥越来越大的作用,Schulz 等佼佼者致力于寻找新的方法来利用其快速周转和(经常)降本优势。
借助 Form 4、Form 4L 和 Fuse 系列等快速、强大的工具,原型制造、制造辅助工具和成品部件可以在数小时或数天内完成,而非数周或数月。“Formlabs 是我们的最佳合作伙伴。我们需要的是一站式解决方案,用以大批量生产部件,同时减少工程支持。Formlabs 的软件、支持和打印机都非常适合我们。”
如需了解有关汽车行业 3D 打印的更多信息,请访问我们的网站。如需亲身了解 SLA 或 SLS 3D 打印的质量,请索取样品部件。