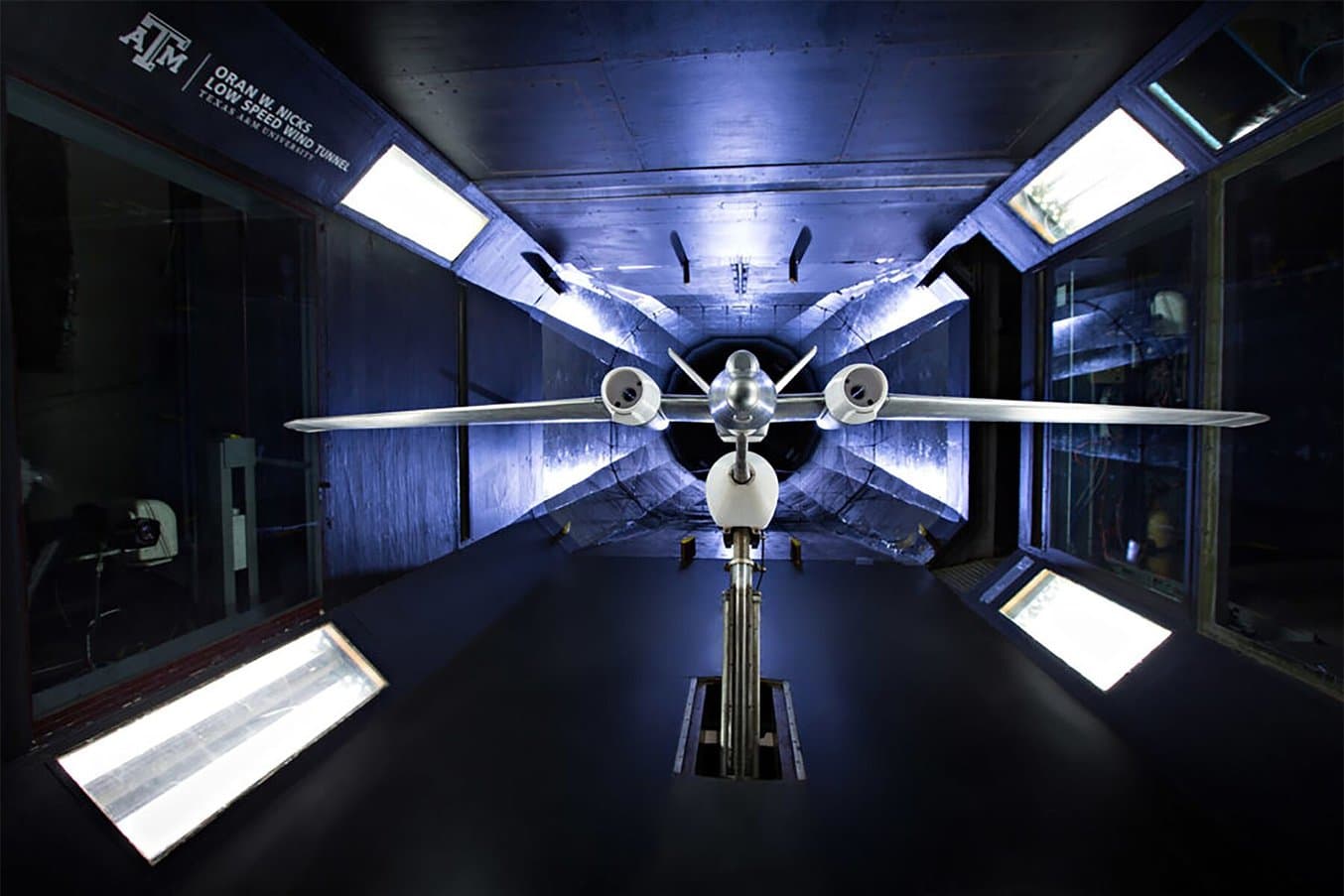
增材制造(又称 3D 打印)在航空航天领域有诸多应用,不仅仅涉及设计到制造过程。
3D 打印或增材制造技术发明之初,航空航天业是最早的商业采用者之一。事实上,许多原始设备制造商、供应商和政府机构使用 3D 打印技术已有数十年之久;最新一代的商用飞机上就有 1000 多个 3D 打印部件。
然而,传统工业级 3D 打印机都过于昂贵,只有规模最大、资金最雄厚的机构才能负担得起。在过去 10 年中,我们可以发现高性能 3D 打印机的价格也在大幅下降,材料科学的创新使许多更高性能的应用成为可能。在价格合理的情况下,3D 打印机的身影现在可以出现在较小的组织机构中,也可以在大型组织机构的新分支机构中大展拳脚,而在以前,3D 打印机只能在集中式原型制造车间中使用。随着越来越多的最终用户采用增材制造技术,Formlabs 3D 打印机的高精度 3D 打印可促使更多的航空航天工程师和研究人员不断突破应用边界。
请继续阅读,了解 3D 打印在从设计到制造等环节中推动整个航空航天行业创新的九个重要方式。
用于航空航天产品开发的高精度 3D 打印
1. 用于火箭功能测试的 3D 打印快速原型
Gravity Industries 正在开发一款外观酷炫的喷气服,让使用者如同身处科幻电影中。他们的喷气服可应用于直升机无法到达或安全降落的搜救等应用场景。多种 3D 打印技术的结合使用加快了其原型和测试过程,包括一些确定热固性光敏树脂是最佳选择的测试。
试飞员兼首席设计师 Sam Rogers 在 Form 3 上使用 Clear Resin 制作部件,并将这些部件用于开发涡流冷却火箭发动机点火器的设计方案。这种透明材料非常适合测试环境,并方便 Rogers 观察到测试装置内部的燃烧模式。
在设计测试过程中,Rogers 设计了模块化燃烧室,以便可以混合和匹配不同版本的燃烧室和喷嘴。借助“涡流氧气防护罩”将最高热量隔绝在燃烧室壁外,每个树脂部件都能持续数秒钟。该时间长度足够工作人员在每次试射中观察点火模式。
如果 Rogers 用金属来实现他的几十种不同设计方案,成本将非常高昂。相反,由于测试时间很短,而且部件的材料成本很低,他能以最小的开支和最短的准备时间完成高性能的设计方案。
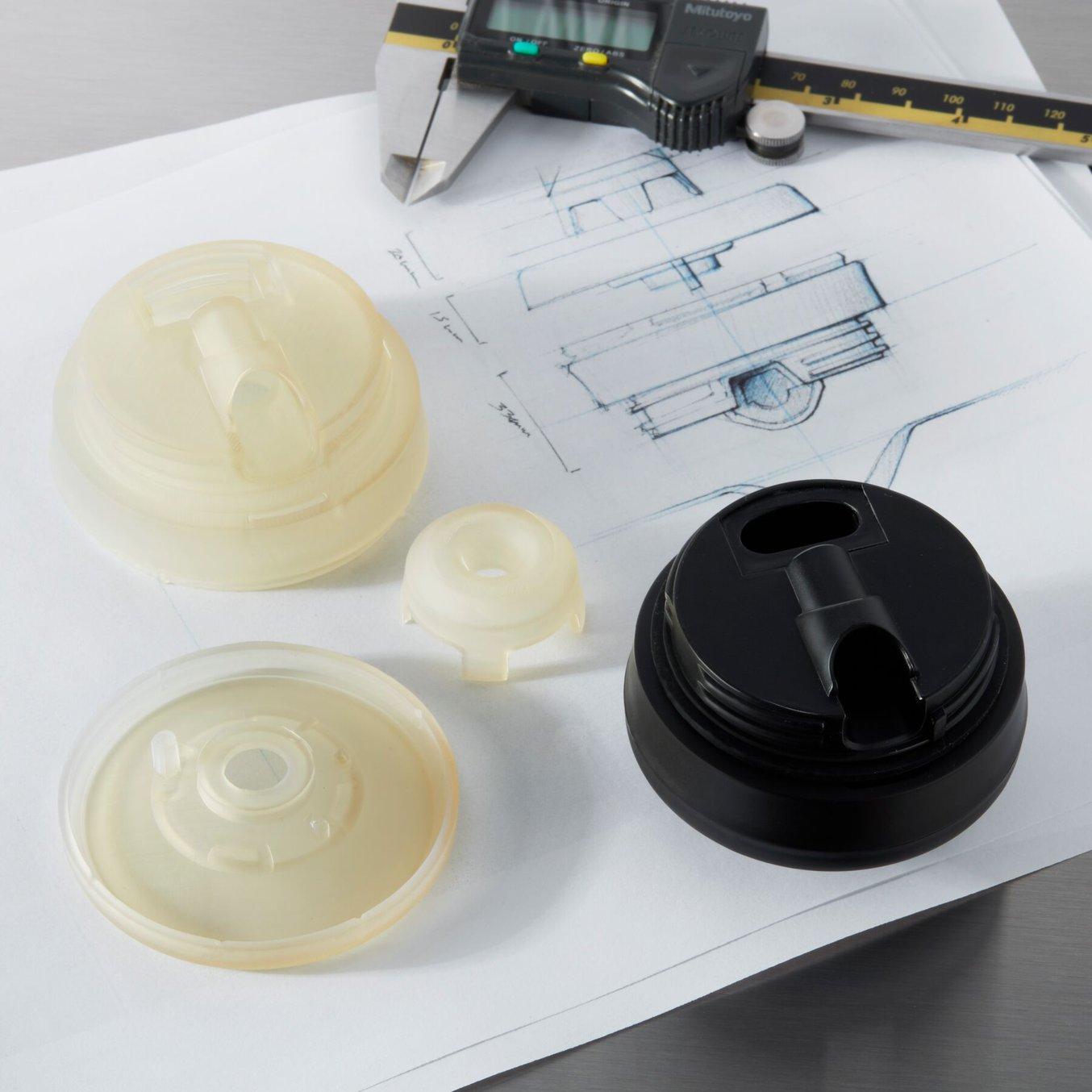
2. 使用 3D 打印创建复杂的火箭部件
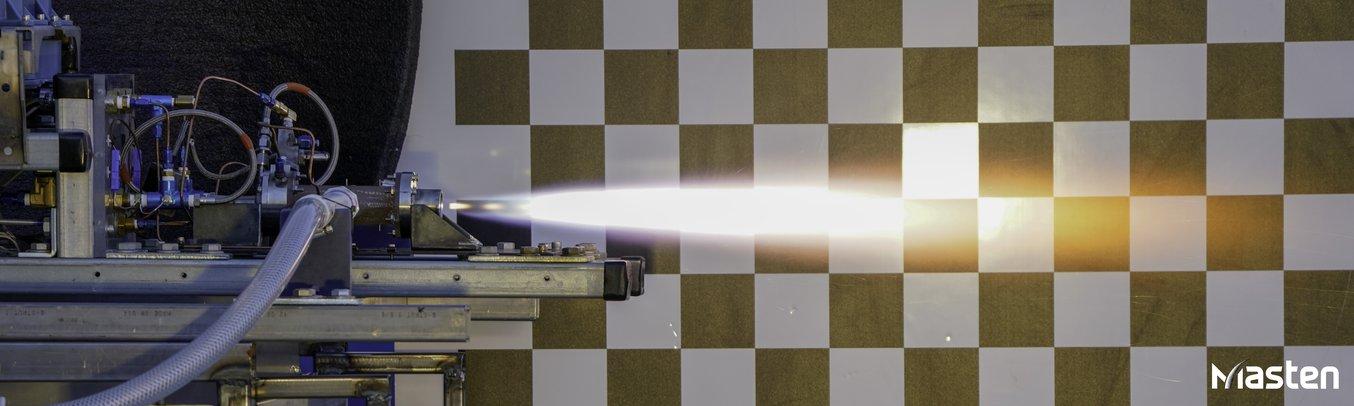
Masten Space Systems 公司利用 3D 打印技术来生产复杂的火箭部件。
Masten Space Systems 专注于研发垂直起落火箭。Masten 于 2014 年开始使用 3D 打印制作火箭发动机;他们先从小型测试推进器开始,最终在 2016 年将规模扩大到生产 25000 磅推力的 Broadsword 发动机。他们使用塑料和金属进行增材制造。据 Masten 公司的研究和测试工程师 Kimberly Devore 介绍,该公司结合使用传统的机械加工和 3D 打印技术来生产火箭发动机。虽然 Masten 仍使用一些传统制造方法来生产其旧版发动机,但他们已经开始使用 3D 打印技术来提高设计灵活性和生产速度。
“[3D 打印]的优势在于,你完全可以随心所欲地完成建模工作,而且不需要像传统机械加工那样反复迭代。事实上,你可以按照所需所想进行设计。很多时候,在传统加工中,你可能需要完成一些相当基础的工作。并且需要为所增加的每一个额外特征另行支付费用,”Devore 表示。
但对于 3D 打印来说,增加复杂性以提高性能并不需要花费额外成本,而且也无需承担风险。由于制造多件产品的速度相对较快,成本也相对较低,因此他们能够尝试新事物。“实现快速迭代非常重要。”
3. 使用 3D 打印技术制作航空航天工具原型
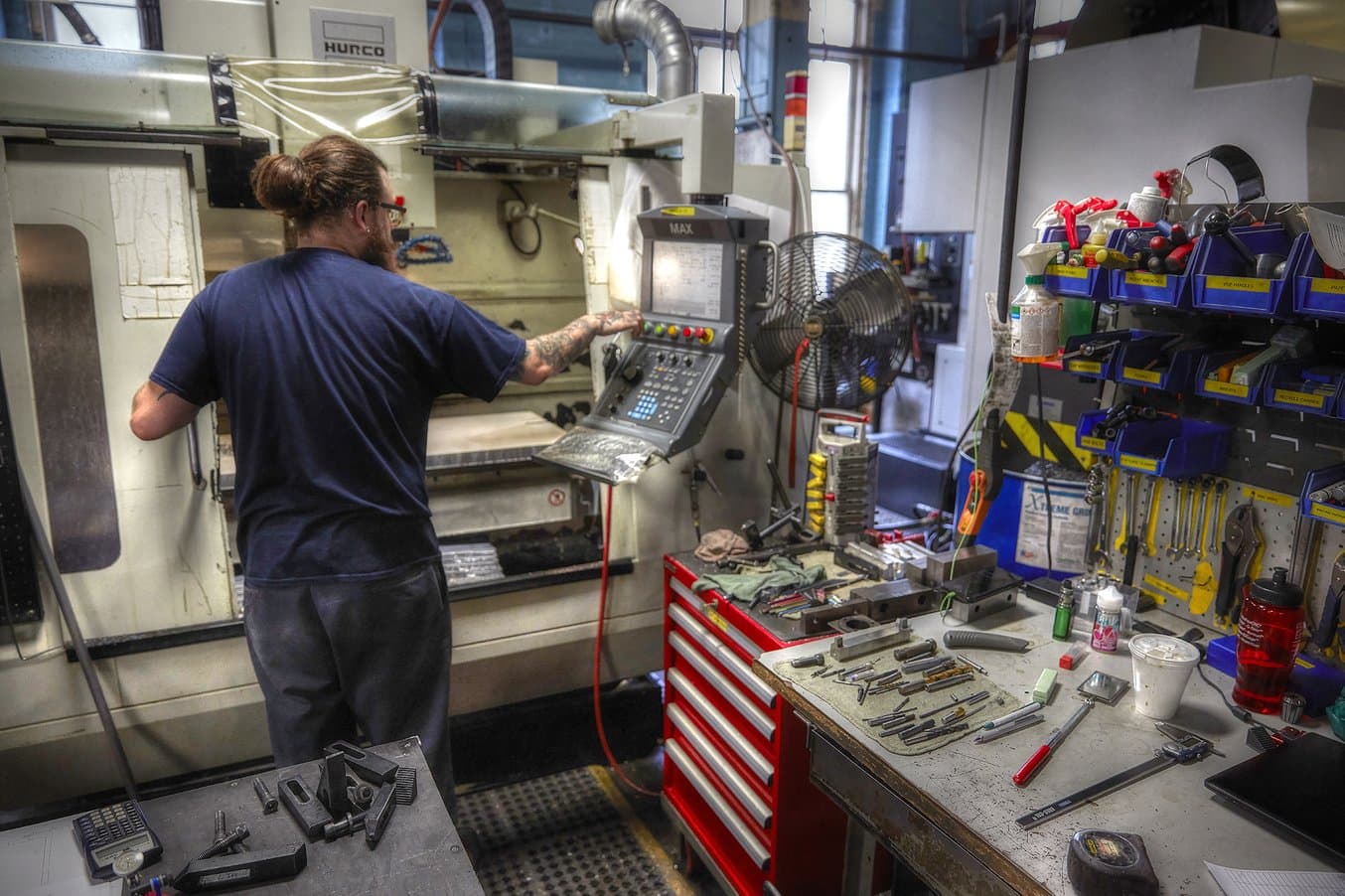
CNC 机床编程需要技术和时间。如果部件无需是金属制品,那么 3D 打印将是一种能以更快的速度和更低的成本制造出原型或生产工具的实用工具。
A&M Tool and Design 主要为航空航天、光学和机器人制造相关部件和定制机器。多年来,除了可靠的传统技术和改装解决方案外,该工作室还引进了包括 3D 打印在内的一系列新设备,从而实现了现代化。A&M Tool 的机械工程师 Ryan Little 研究了哪种 3D 打印机最符合他们的需求,并最终选择了 Formlabs 3D 打印机。
为了制作原型,该工作室开始使用 3D 打印来测试装配和功能。3D 打印技术使 Little 及其团队能够更快地制造部件,而且可以将打印设置为夜间运行并在第二天使用打印出的部件,从而充分利用全天时间。3D 打印技术尤其适合生产那些耗时耗钱,用 CNC 机床生产不够划算的几何形状。
Little 说道:“打印机几乎就是 CAD 以外的另一种辅助工具。我们针对不同类型的模具制作了大量原型。如果没有 Form 2,许多原型在加工之前就只能存在于 CAD 软件中,还有些部件会由于可操作性不高而永远无法被制造或设计出来。”
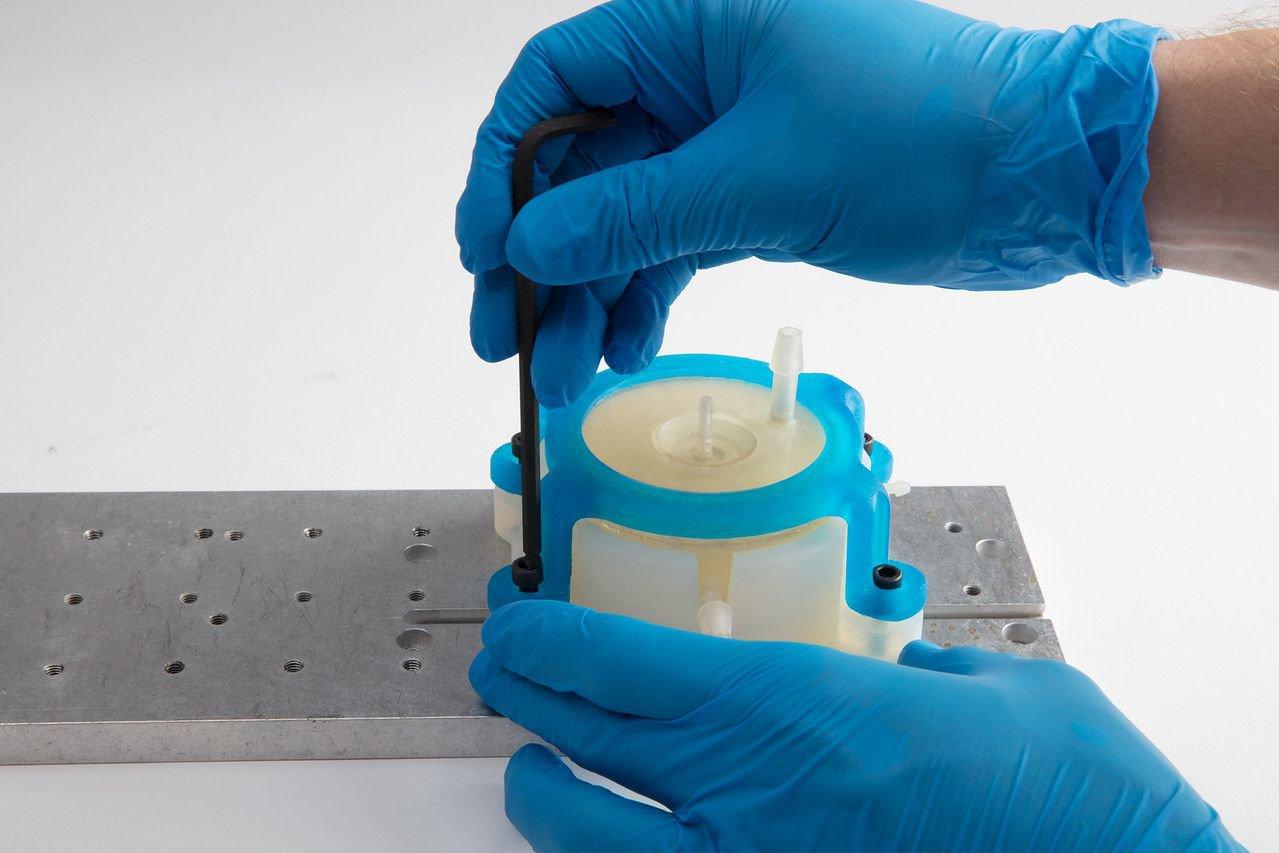
借助 3D 打印技术设计夹具和固定装置
对于制造商而言,最大限度地提高生产速度,并制造出高质量的部件是成功的关键。使用夹具和固定装置使制造和装配过程变得更加简单可靠,有助于在缩短生产周期的同时,保障工人安全。
用于航空航天制造的高精度 3D 打印
4. 使用 3D 打印定制模具制作飞机部件以节省成本
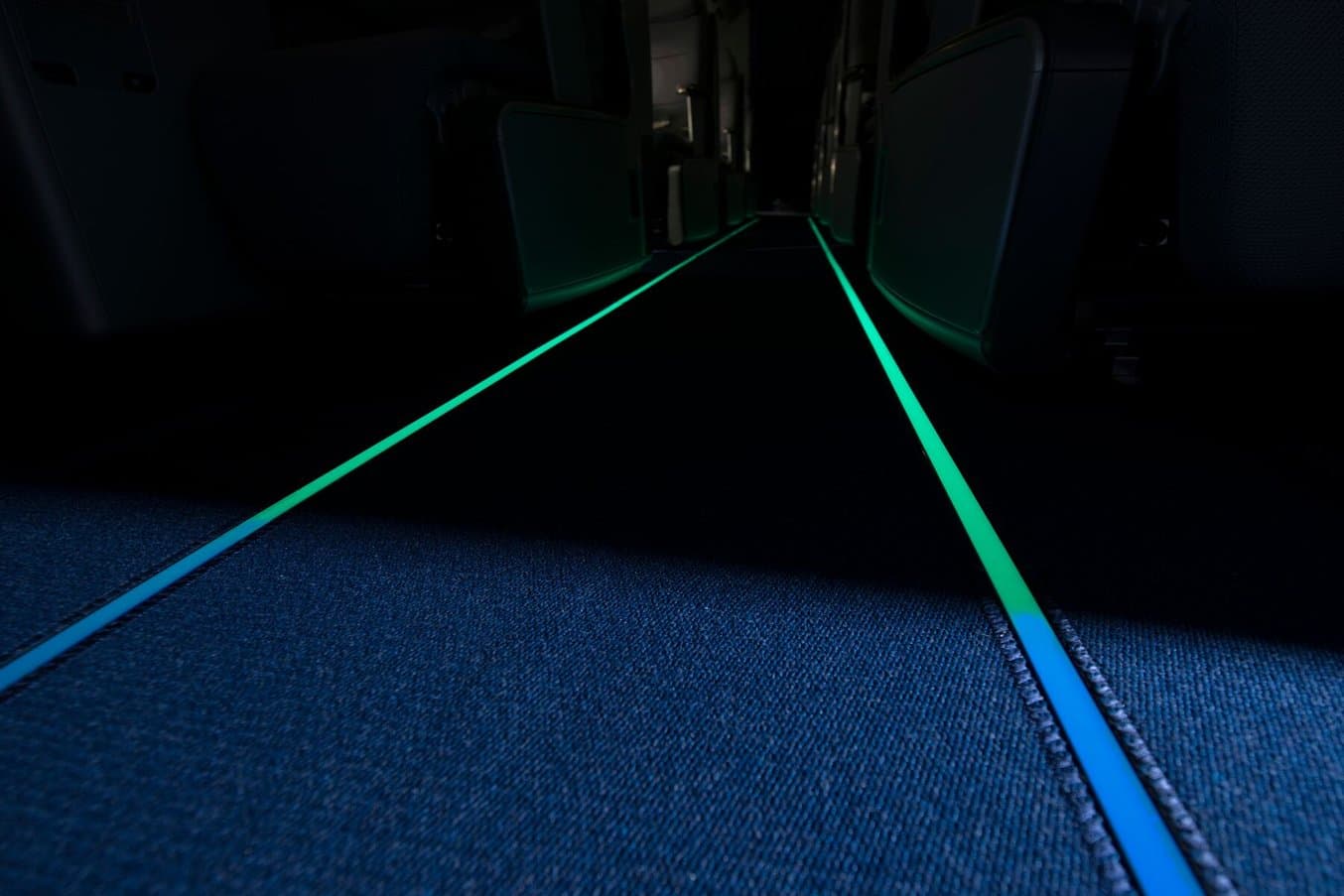
Lufthansa Technik 3D 打印了挤出喷嘴以生产此类自行发光的逃生路线标记。
Lufthansa Technik 是世界上最大的航空供应商以及维护、维修和大修 (MRO) 服务提供商之一。其专有的 Guide U 逃生路线标记专为飞机客舱内的售后安装而设计。这些创新性地板标记可以自行发光,其中使用了自发光彩色颜料,可以吸收普通客舱灯光,以保证其能够在紧急情况下于黑暗环境中继续发光。
在生产前,我们对几种工具材料和加工工艺进行了测试。测试结果表明,3D 打印定制挤出喷嘴是最具成本效益的灵活制造方法。“理论上说,我们也可以通过注射成型制作部件。但如此一来,我们就永远无法如此灵活地塑造并调整喷嘴。这就是 3D 打印所呈现出的巨大优势,”Guide U 项目工程师 Ulrich Zarth 解释道。
该生产工具是与 Formlabs 合作伙伴 myprintoo 合作使用 Form 3L 打印而成。Form 3L 中的大面积构建平台支持在一次打印运行中生产 72 个喷嘴。在测试了几种 Formlabs 材料后,他们最终选择了 Clear Resin,该材料除了具有适当的稳定性和表面质量外,还有助于 Lufthansa Technik 不断优化其生产流程。
“如果想要快速打印具有复杂几何形状的部件并保证精确度,3D 打印始终都是最佳选择,这款工艺在塑料行业尤其适用。”
Ulrich Zarth,Lufthansa Technik AG 项目工程师
Zarth 及其团队实现了此小型组件的内部 3D 打印,从而在生产过程中节省了大量时间和金钱。与制造此类工具的传统方法相比,他们还能够避免过高的最低订购量,并在工艺优化中保持显著的灵活性。
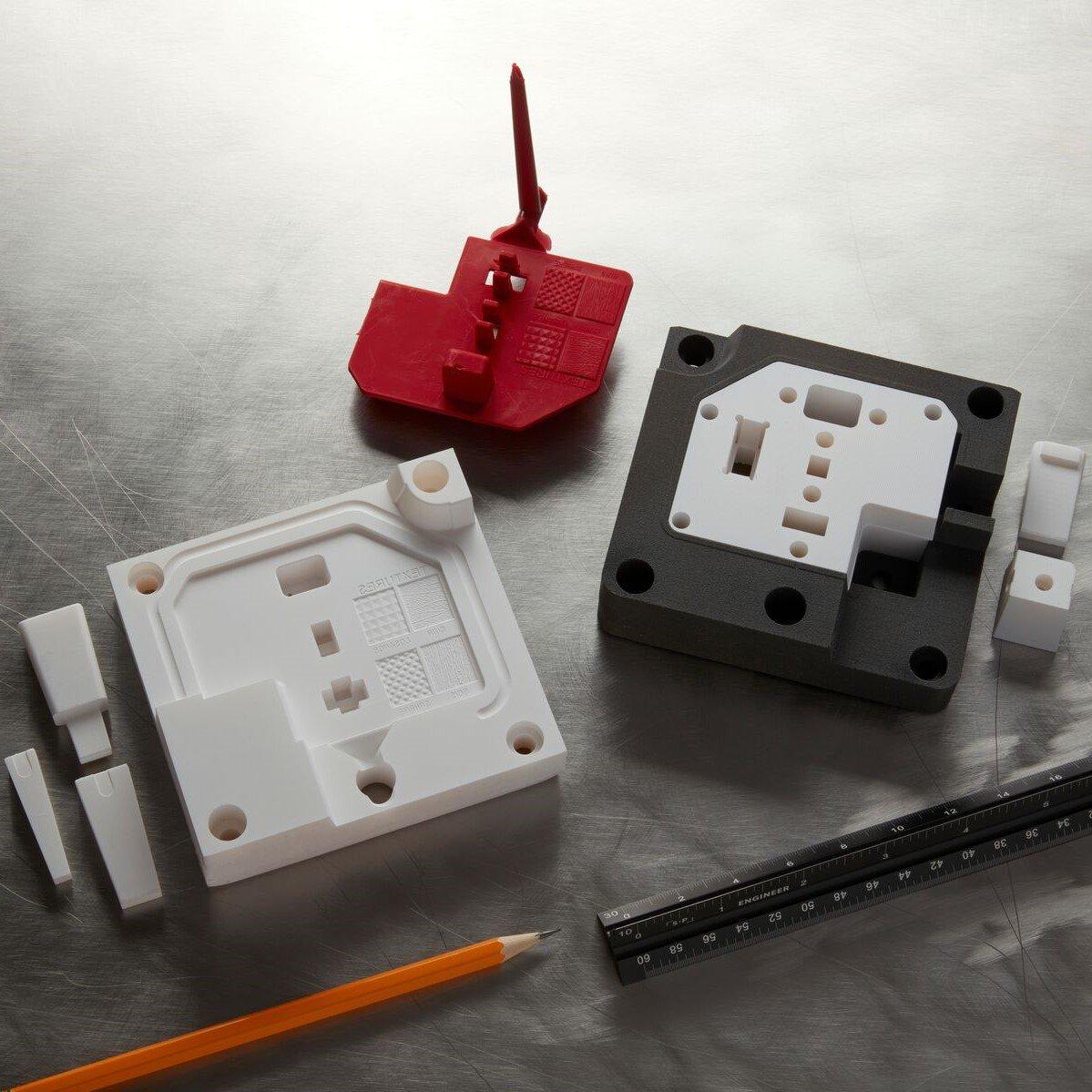
5. 使用 3D 打印遮蔽夹具缩短航空航天制造时间
AMRC 的集成制造小组与工业合作伙伴合作,汇集先进技术并开发集成系统。该研究小组参与了欧洲最大航空航天制造商空中客车公司的一个项目,其中涉及碳纤维、铝和钛组件的高公差钻孔和加工。AMRC 项目工程师 George Sleath 表示:“钻完一个孔后,我们需要把第一个孔盖上才能继续钻孔,以免产生的废料交叉污染第二个孔。”
研究小组首先尝试使用了铝片和小橡胶 O 型环,但这并不能彻底解决问题。另外还有两个问题:需要多种尺寸的盖子,而且他们只有十天时间来采购 500 个盖子,才能在截止日期前完成任务。
由于定制产品的周转时间如此之短,除了 3D 打印外,几乎所有其他制造方案都不可行。由于当时不确定 AMRC 的内部能力,Sleath 向三家外部打印机构询价,但报价都很高。
“随后,我与设计和原型制造部门的 Mark Cocking 进行了交谈,询问我们是否可以在内部制造部件。实际上,我在 24 小时内都没有收到他的回复,但在我收到他的回复时,他却说:‘没问题,打印进度已经过半了’。24 小时内就生产了 250 个钻孔盖,周转时间真是惊人”,Sleath 表示。
最后,Cocking 设法在两天内完成了所有部件的生产,且盖子在现场的表现完全符合预期。“安装人员都反馈部件非常好。绝大多数部件的性能完全符合预期,在操作过程中并无损坏,”Sleath 说。
6. 电镀 3D 打印成品航空航天部件
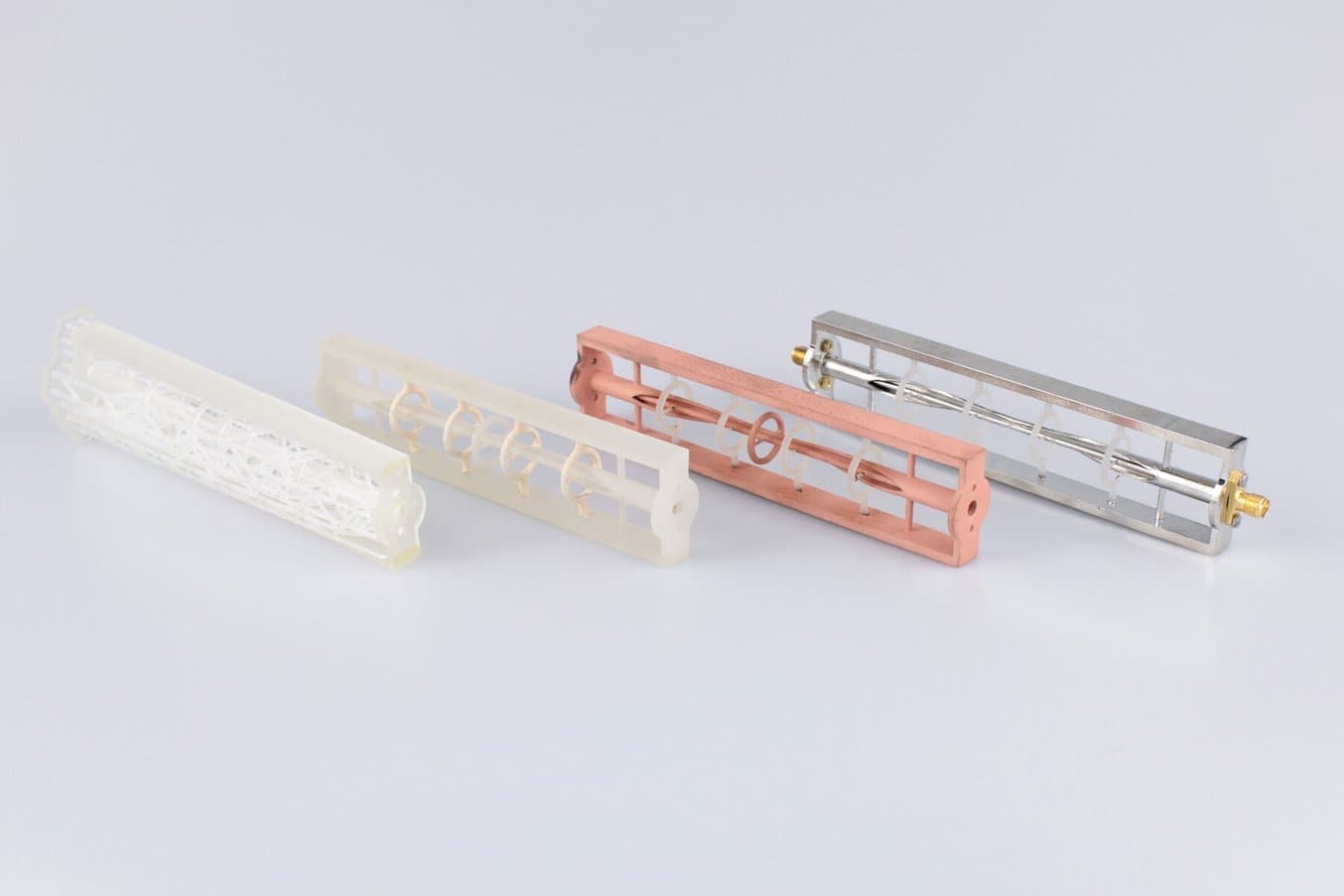
3D 打印成品部件可帮助 Elliptika 更快地设计出新型天线,并在此过程中节省成本。
Elliptika 专注于设计和开发射频 (RF) 和微波产品以及解决方案。该公司设计出了定制滤波器和天线,可用于汽车、国防、医药和教育行业的研发活动。射频设计师 Gwendal Cochet 和 Alexandre Manchec 需要实现复杂的几何形状、保持低成本并快速交付设计。为了实现这些严格的参数,他们并没有局限于传统制造技术。
Elliptika 的团队研究了不同的增材制造工艺,并发现立体光固化 (SLA) 3D 打印技术可提供具有光滑表面的打印部件,堪称电镀的最佳搭档。“部件 3D 打印完成后,我们需要移除支撑、清洁部件表面,并进行固化。然后,我们将利用化学工艺在打印部件表面镀上薄薄的一层(约 3µm)铜。最后,我们需要对部件进行表面处理,例如为其添加更厚的一层锡。
凭借 Formlabs 3D 打印机,Elliptika 公司仅进行了两次打印就实现了正向投资回报率。从外部供应商处购得一个部件的成本约为 3000 欧元;而在公司内部利用 3D 打印和电镀制作一根天线的材料和人工成本仅为 20 欧元。
他们的工作节奏也随之加快了。运用这些传统的制造技术,生产一根天线可能需要花费长达三个月的时间。“凭借内部 3D 打印,我们可以在两天内得到工作部件。一天用来打印,一天用来电镀,而且效果很好。因此,用时大幅减少,”Cochet 先生表示。
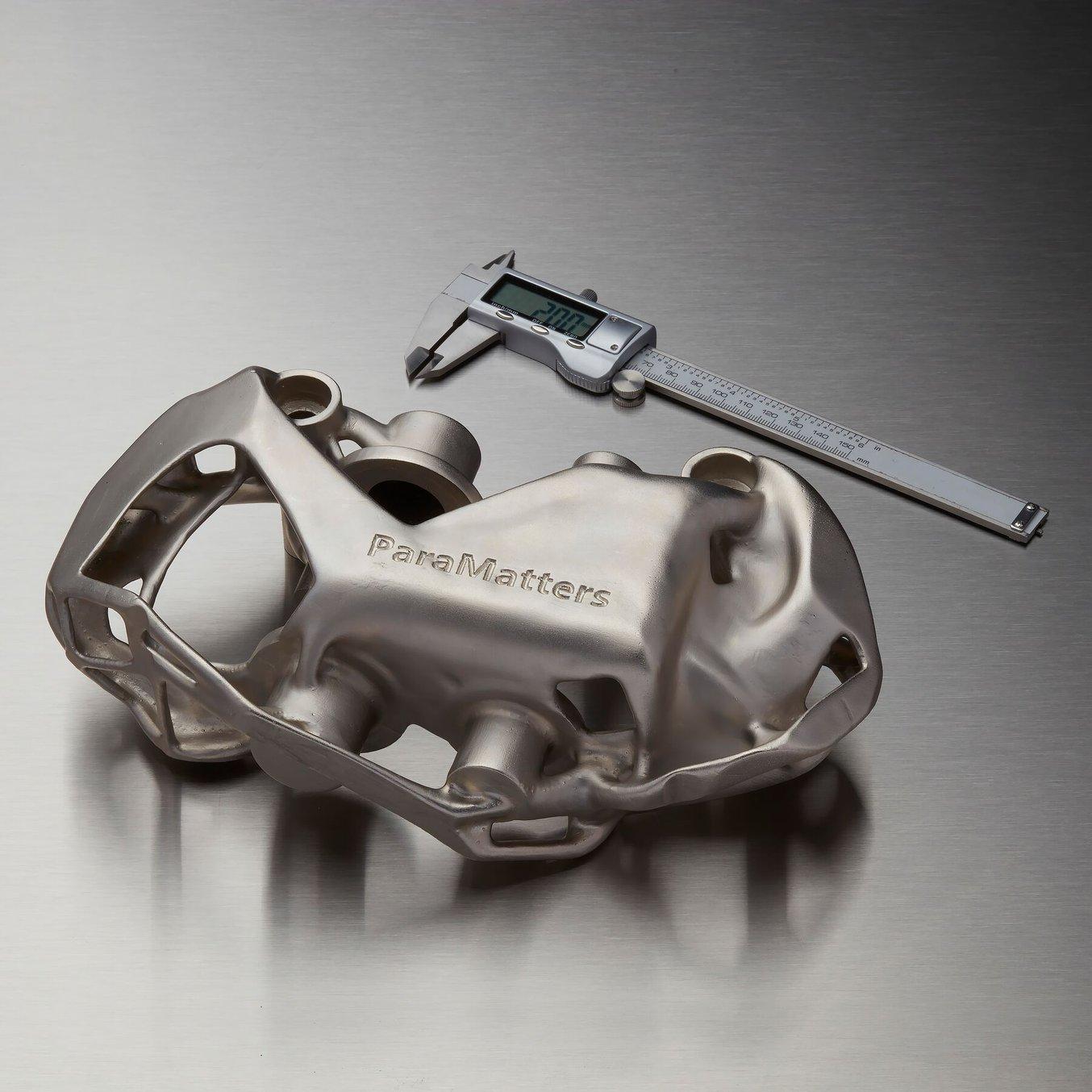
实现金属强度:SLA 部件的电镀策略和用例
请继续阅读下文,了解工程师如何将金属添加到树脂 3D 打印件,以及为何混合金属部件具备令人惊叹的应用特性,包括(但不限于)出色的最终使用强度和耐用性。
教育和研究领域的 3D 打印技术
7. 在太空中测试 3D 打印部件
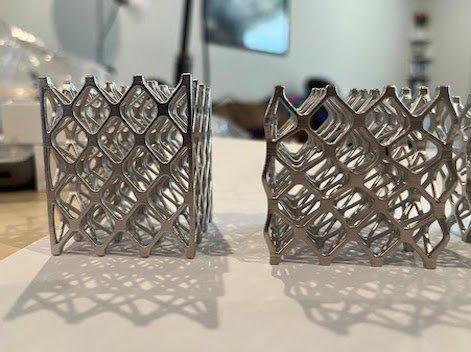
测试前电镀 Rigid 10K Resin 晶格压缩样品(左)和测试后顶部受力的样品(右)
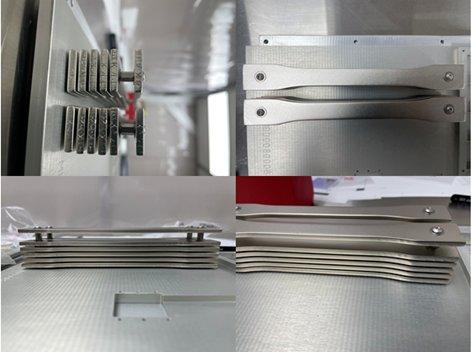
送至 ISS 的电镀 Rigid 10K Resin 3D 打印部件。
美国国家航空航天局 (NASA) 的研究人员正在研究电镀 SLA 部件在太空中的性能。NASA 戈达德太空飞行中心的工程师设计了支架,并由 Formlabs 3D 打印机打印出支架,在完成电镀后,搭乘 2022 年夏季 SpaceX 公司的商业补给服务 (CRS-25) 任务送往太空中的国际空间站 (ISS)。
使用 Alpha Space 的国际空间站测试平台 Materials International Space Station Experiment (MISSE-16),样品将暴露在空间站外部的极端环境中,随后被送返地球进行进一步测试。研究结果将反馈给 NASA 和其他航空航天制造商,便于他们考虑如何将增材制造纳入潜在的未来产品计划。
8. 3D 打印风洞测试部件
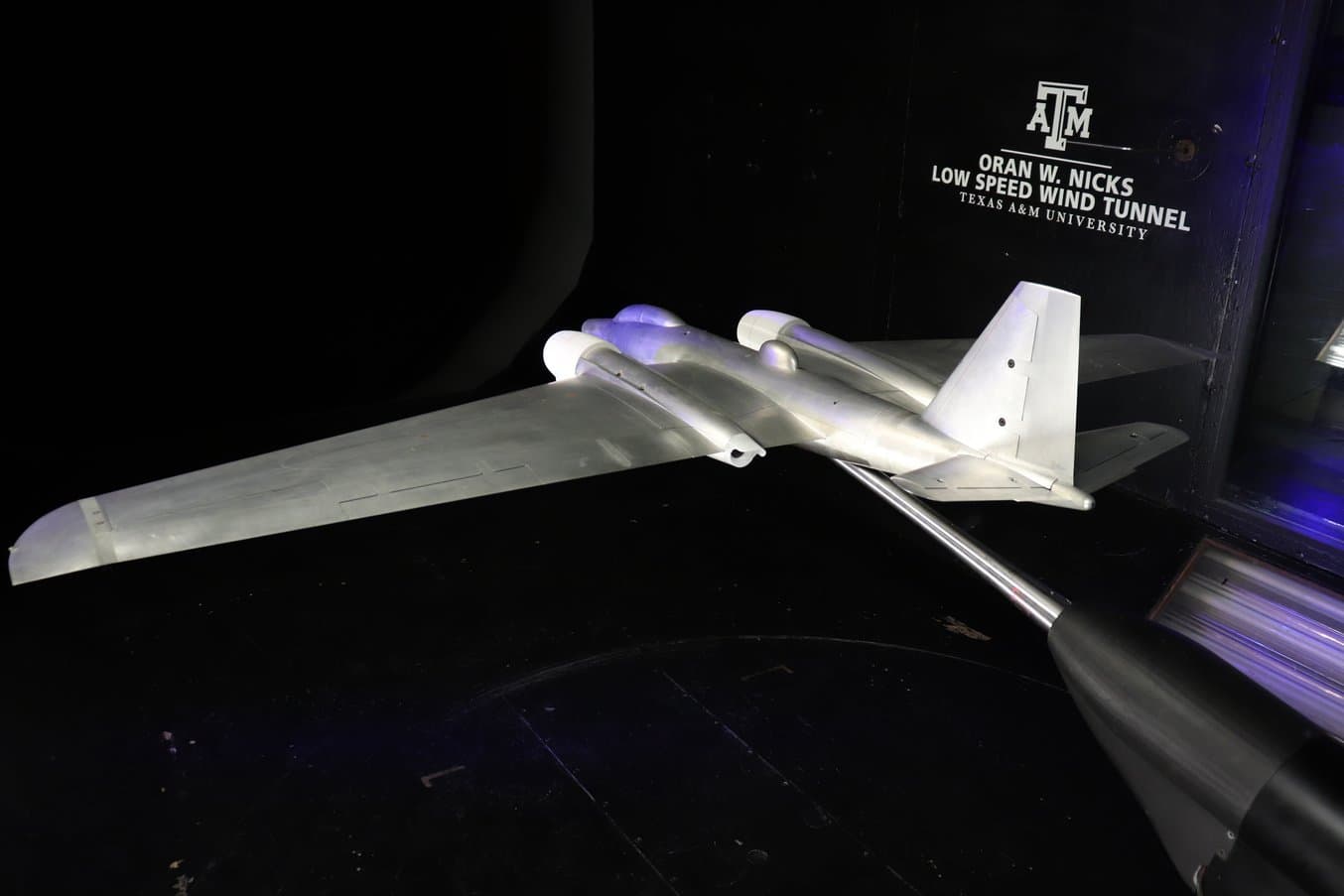
高性能 3D 打印部件可以安装在风洞中的飞机比例模型中。
世界各地的教师和学生都在风洞测试中使用 Formlabs 3D 打印机,为他们的研究提供信息。
得克萨斯农工大学的 Oran W. Nicks 低速风洞可针对各种项目进行风洞测试。得克萨斯农工大学风洞管理员兼工程师 Lisa Brown 帮助研究人员制定测试计划、设计模型和创建有助于收集相关数据的代码。她的团队使用 3D 打印技术制作比例模型,以便对各种物体进行测试。
Brown 回忆说,在一个项目中,其团队的研究主题是摆动直升机叶片,并在测试中引入了 3D 打印技术。Brown 说道:“如果直升机的速度和叶片摆动速度足够快,那么在叶片前缘实际上会产生冲击波。这并不应该出现在直升机飞行过程中。因此,我们实际上能够在低速隧道中观察到这些冲击波,这真的很令人兴奋。我们打印了一个内置传感器的小型插件,可以放置在机翼前缘。整个模型就是带有小型插件的铝制机翼,而且我们可以更换这个小型插件。”
如需了解 Brown 的材料选择及其原因,请阅读我们的案例研究。
在大西洋的另一侧,卡尔斯鲁厄理工学院 (KIT) 的风洞也在测试 3D 打印部件。博士生 Lars von Deyn 在研究预测湍流的方法。他的工作有可能为材料和设计选择提供参考,从而减少流动摩擦。
为了制作测试部件,von Deyn 将目光投向了 3D 打印技术。他说:“我想研究那些很难用机械加工工艺生产的结构。” 他选择了 Form 3L,理由是该打印机具有很大的构建面积,这意味着他可以用更少的单个部件覆盖风洞测试区域,从而减少模型中断。
请参阅我们的案例研究,了解他的实验结果。
9. 使用 3D 打印技术培训下一代工程师
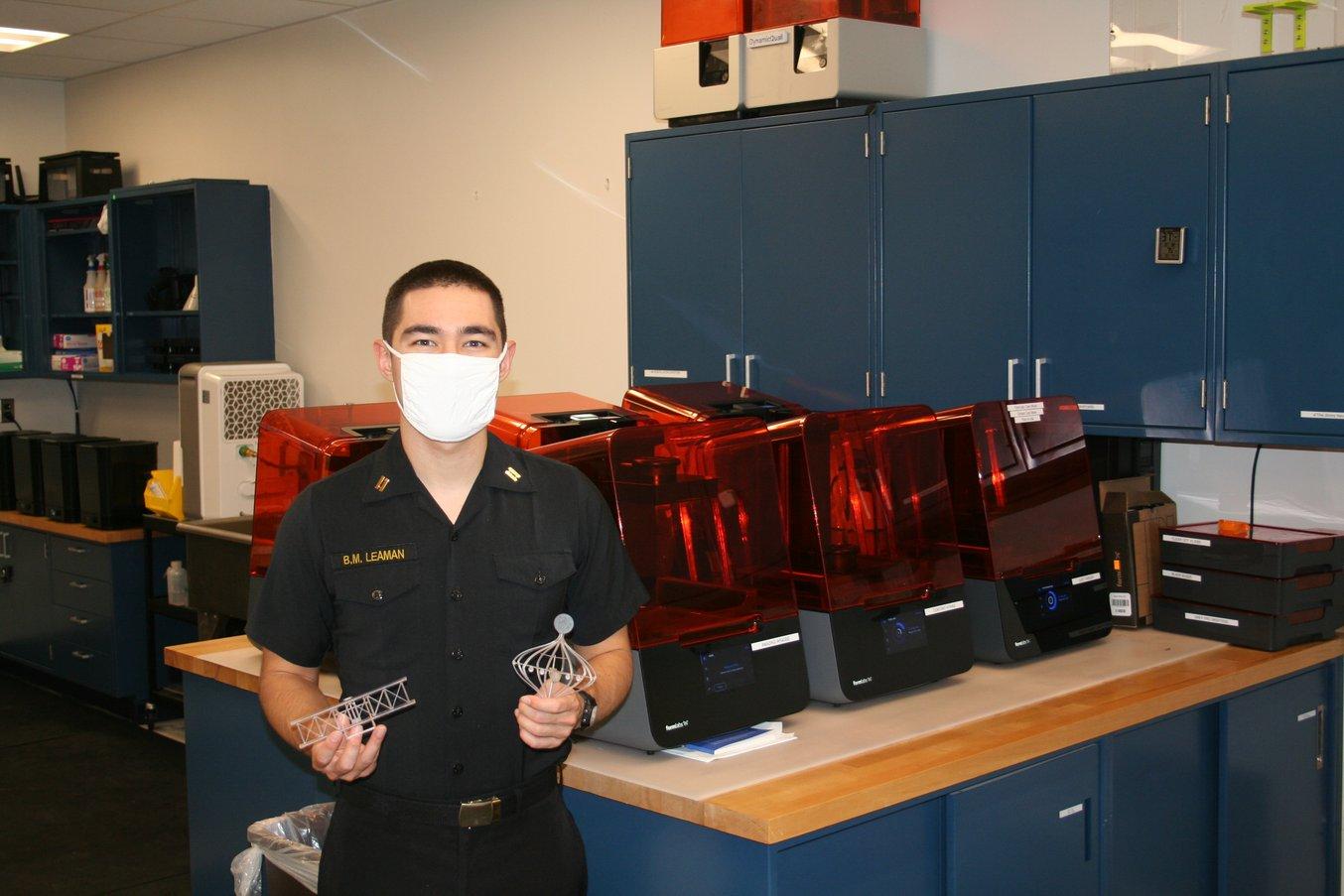
USNA 船舶建筑专业的海军军官 1/C Ben Leaman 展示他在 2021 年的 AM 奥运挑战赛上使用 Formlabs Form 3 打印机打印的获奖作品。
美国海军学院培养年轻男女成为具备美国海军和海军陆战队的专业军官。USNA 的副教授 Brad Baker 上校意识到,工科学生的迭代过程以及学习速度因缺乏制造能力而受到阻碍。即使有一家专门用于学生毕业设计的机械车间,每个人或团队在一年的时间里的模拟次数也不能超过三到四次。
Baker 上校并不是校园里第一位通过 3D 打印机帮助学生完成课程作业的教授,但当他创办 MakerSpaceUSNA 时,他将全方位的设计和制造能力集中到一起。从购置几台熔融沉积成型 (FDM) 打印机起步,他就开始将这些机器集成到机械工程课程中,并将这些机器提供给完成其毕业设计的学生。
当学生进入工程课程时,他们首先学习如何使用 CAD 软件,再学习如何操作 FDM 打印机,然后转向立体光固化 (SLA) 打印机,最后学习选择性激光烧结 (SLS) 3D 打印机。现在他们甚至学习了 3D 扫描,并且可以使用他们所学的所有工具完成完整的逆向工程项目。
凭借搭载 FDM、SLA 和 SLS 技术的高质量、可靠打印机,MakerSpaceUSNA 能够为每位 USNA 学生提供各种增材制造技术的体验。Baker 上校的实践教育理念和从失败中学习的方法让工程专业学生更进一步,并为他们在美国海军及其他地区的职业生涯做好准备。
3D 打印在航空航天领域的应用展望
随着增材制造技术日益强大、不断普及,将会有越来越多的参与者为航空航天业发展做出贡献。虽然无法肯定未来 5-10 年内最大的突破是来自原始设备制造商、供应商、公共机构、初创企业还是学术界,但随着越来越多的人开始接触 3D 打印,这些创新将比以往任何时候都更快实现。
随着整个航空航天业对 3D 打印的理解不断加深,且技术和可用材料基础日益多样化,增材技术将继续重塑我们制造和维护飞机和航天器的方式。