MOSOLF Special Vehicles GmbH 是一家位于德国基彭海姆的领先特种车辆制造商。该公司拥有近 50 名员工,每年生产约 1000 辆特种车辆和应急车辆。他们的客户包括德国各州和联邦警察部队、国防部门、灾害控制和技术救援组织、市政当局以及工业客户,所有这些客户都要求车辆具有高度定制化的先进性能。
在汽车行业,大多数部件均通过注射成型等大规模生产工艺制造,这种工艺对于几十万辆的标准生产量来说具有很高的成本效益。然而,MOSOLF 的客户需要各种定制和小批量部件,在此情况下,模具成本使得传统制造方法在经济上不可行。对于 MOSOLF 来说,3D 打印则是理想的解决方案。
“预计现在[德国]每三辆警车中就有一辆包含增材制造部件。MOSOLF 在 3D 打印应用方面已经遥遥领先,生产场地完成的每一辆车中都安装有增材制造部件。现在,我们每年打印约 5000 个部件,而且还呈上升趋势,这意味着每辆车上至少有三个 3D 打印部件,甚至更多。”
Carsten Busam,MOSOLF Special Vehicles GmbH 项目策划主管
继续阅读,了解 MOSOLF 如何使用选择性激光烧结 (SLS) 3D 打印技术与 Fuse 系列打印机,为警车和其他特种与紧急车辆生产各种最终用途部件。
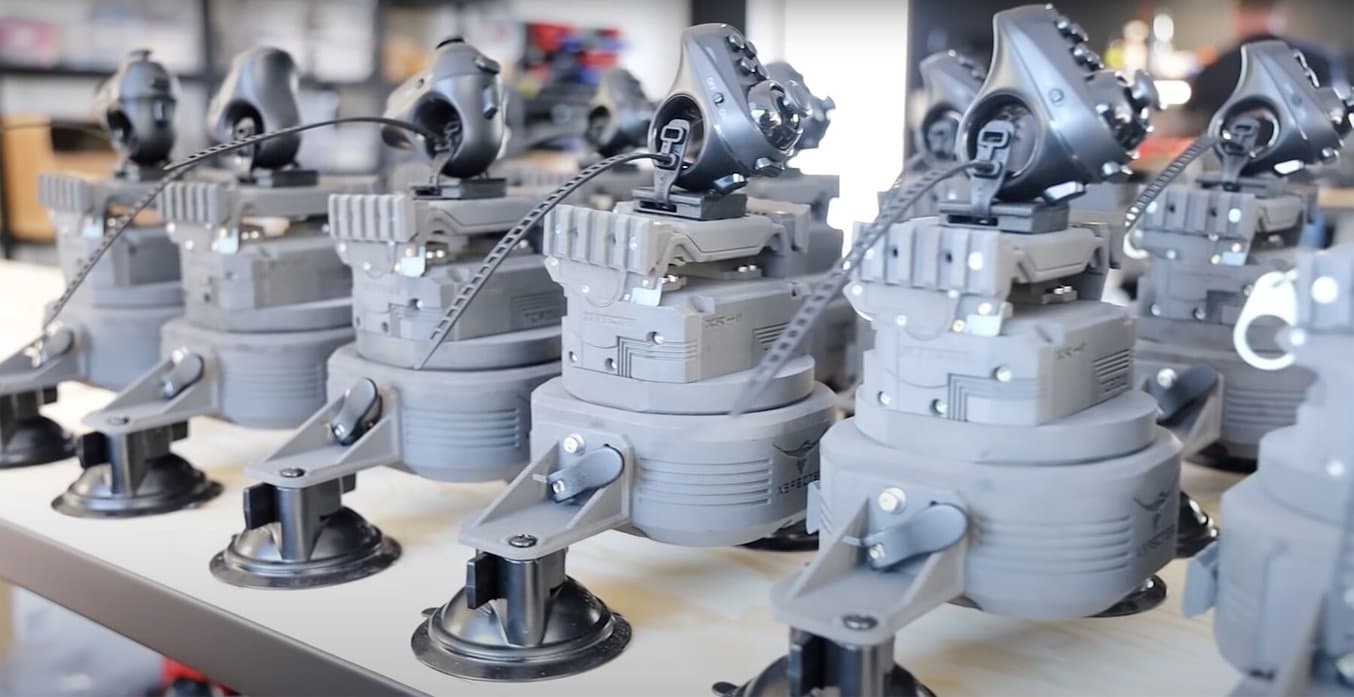
面向成品生产的 SLS
借助 Fuse SLS 生态圈,不仅可以将 3D 打印技术用于生产成品,而且进一步增强了经济性、灵活性和可扩展性。比较生产方法,了解批量粉末价格,并查看目前使用 Fuse 系列的 15 家不同制造商的生产实况。
满足德国 17 支警察部队需求的定制解决方案
Busam 表示:“我们面临的最大挑战就是多样性”。每个州和警察部门都会购买几种不同类型的车辆,每种车辆都需要根据其具体用途定制功能。必备内置部件也各不相同,例如,不同的部队使用不同制造商生产的无线电或信号系统。这意味着每辆车都需要大量定制部件。
“我们为德国 17 支警察部队制造车辆,每个人都对车辆的人体工学设计和操作方式都有自己的想法。因此,就基本设计而言,产量通常就会较高,但如果加上一定程度的定制化,则产量大大减少,”Busam 说道。
MOSOLF 的团队基于系列车辆进行制造,这意味着他们通常按照规格,对市面上的轿车、卡车和货车进行改装。团队必须为每个所需功能找到合适的安装位置,并确保其符合人体工学、耐用性和美观性要求。在老款车型中,可以轻松确定安装位置-仪表板或控制台上有多个空位可供 MOSOLF 改装。事实证明,较新的车型则颇具挑战。
“车辆显示屏中的内容越来越杂乱。车内不再有任何维修空间。虽然有一些储物格和手机充电器,但要找到能容纳所有控制装置的安装空间并非易事。特别是在隐蔽式车辆中,其外观必须与警车毫无关系,”Busam 说。
MOSOLF 的 3D 打印之旅始于 2016 年,当时德国巴伐利亚州警察局下单为其整个车队和摩托车安装新的数字无线电设备。
“我们必须为每辆车和每辆摩托车找到个性化的解决方案。如果通过钣金加工所有部件,那将会非常耗时,而且解决方案也不会特别完善,因此我们迈出了踏进 3D 世界的第一步。”
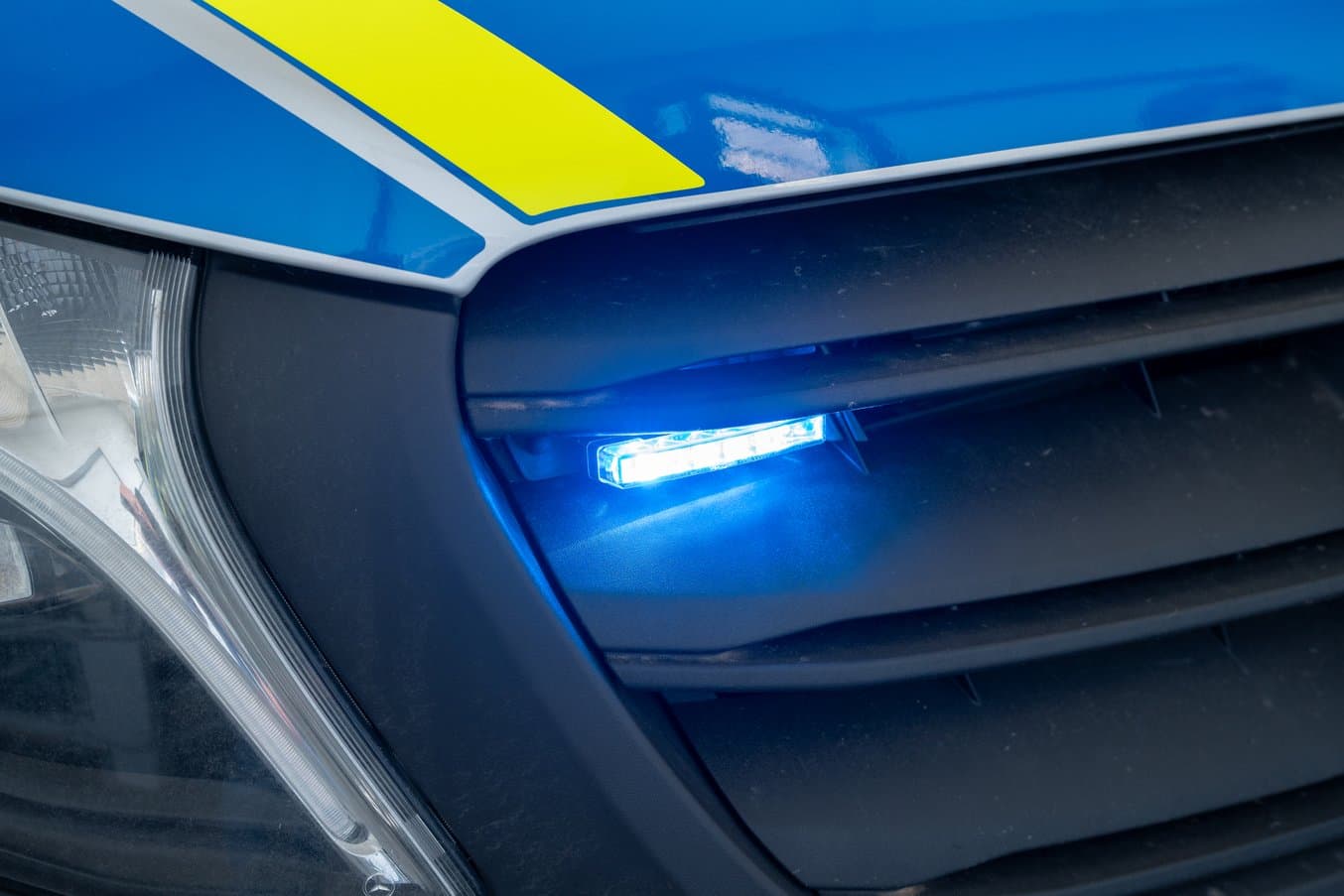
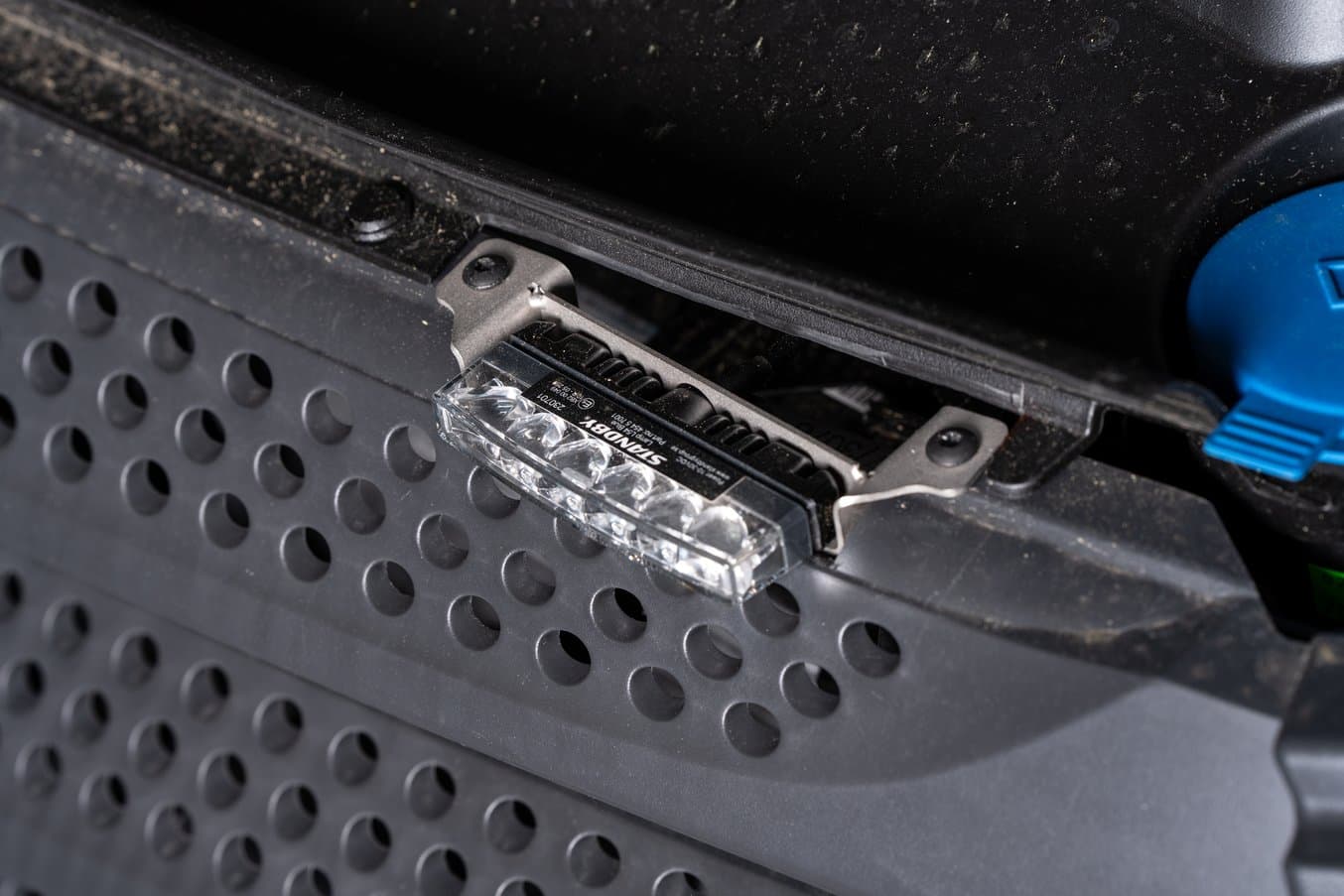
为警车上的 LED 前闪光灯定制支架。该团队以前使用钣金成型来生产这些部件。
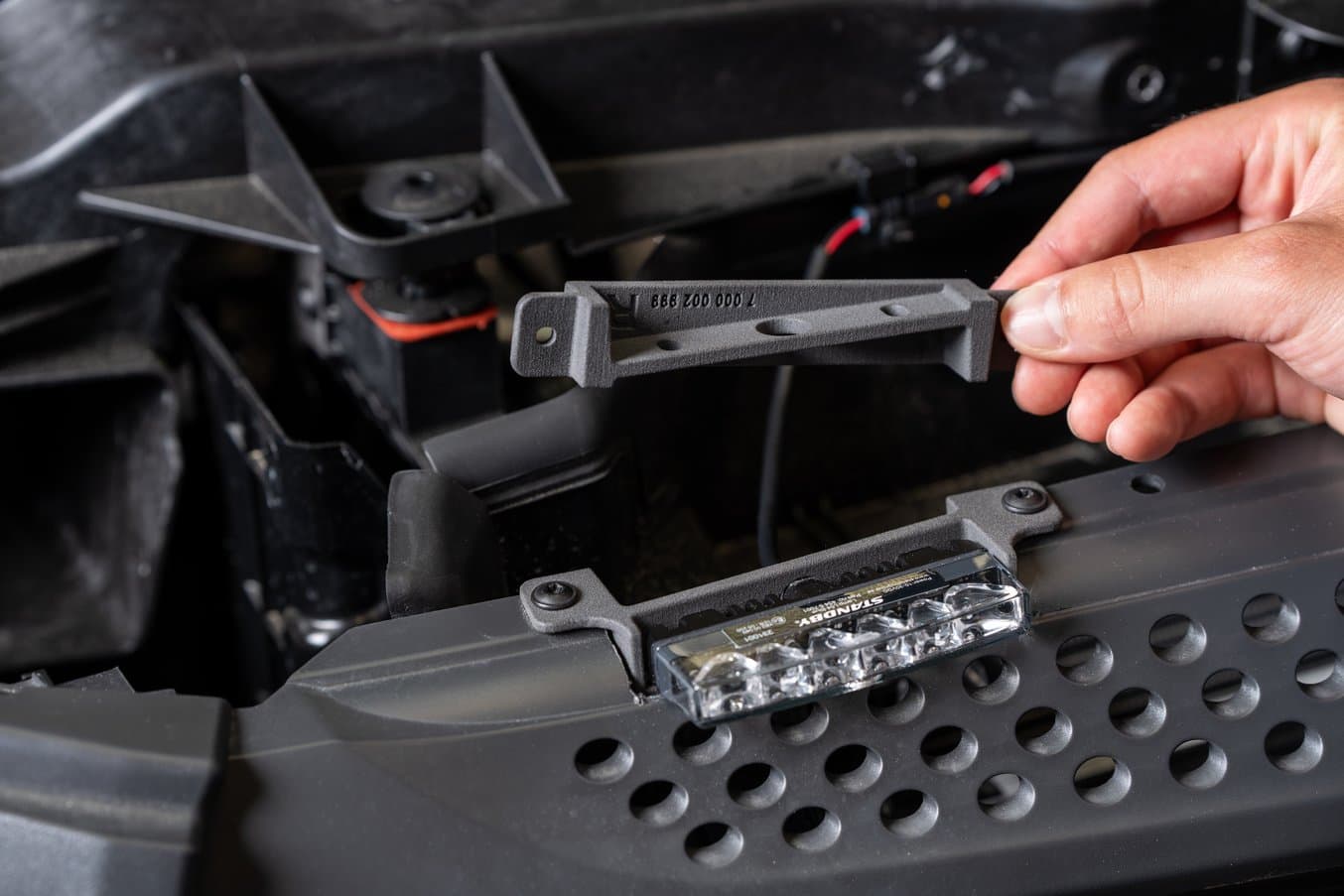
现在,SLS 3D 打印技术提供了一种更快速、简单、具有成本效益的解决方案。
该团队最初使用熔融沉积成型 (FDM) 3D 打印技术生产部件,这在当时是最符合他们需求的技术,但很快就遇到了瓶颈。FDM 很难扩展到足够大的产量来满足订单需求,而且部件本身质量无法达到工业级水平。
逻辑上来说,下一步则应该采用 SLS 3D 打印技术,但由于该解决方案的起价约为 20 万欧元,小型企业无力负担,直到 Formlabs Fuse 系列问世。
“SLS 打印是 MOSOLF 的理想选择,因为该技术可提供出色质量、高精度、高材料性能,并且可以同时生产多个部件。整个系统非常经济实惠,”Formlabs 合作伙伴 3D-WERK Black Forest GmbH 的首席执行官兼创始人 Gerhard Duda 表示,他从一开始就与 MOSOLF 团队合作,为他们的应用寻找最佳解决方案。
Busam 补充说:“Fuse 生态圈是我们的最佳选择,因为它在操作和工作流程方面最易于管理。”
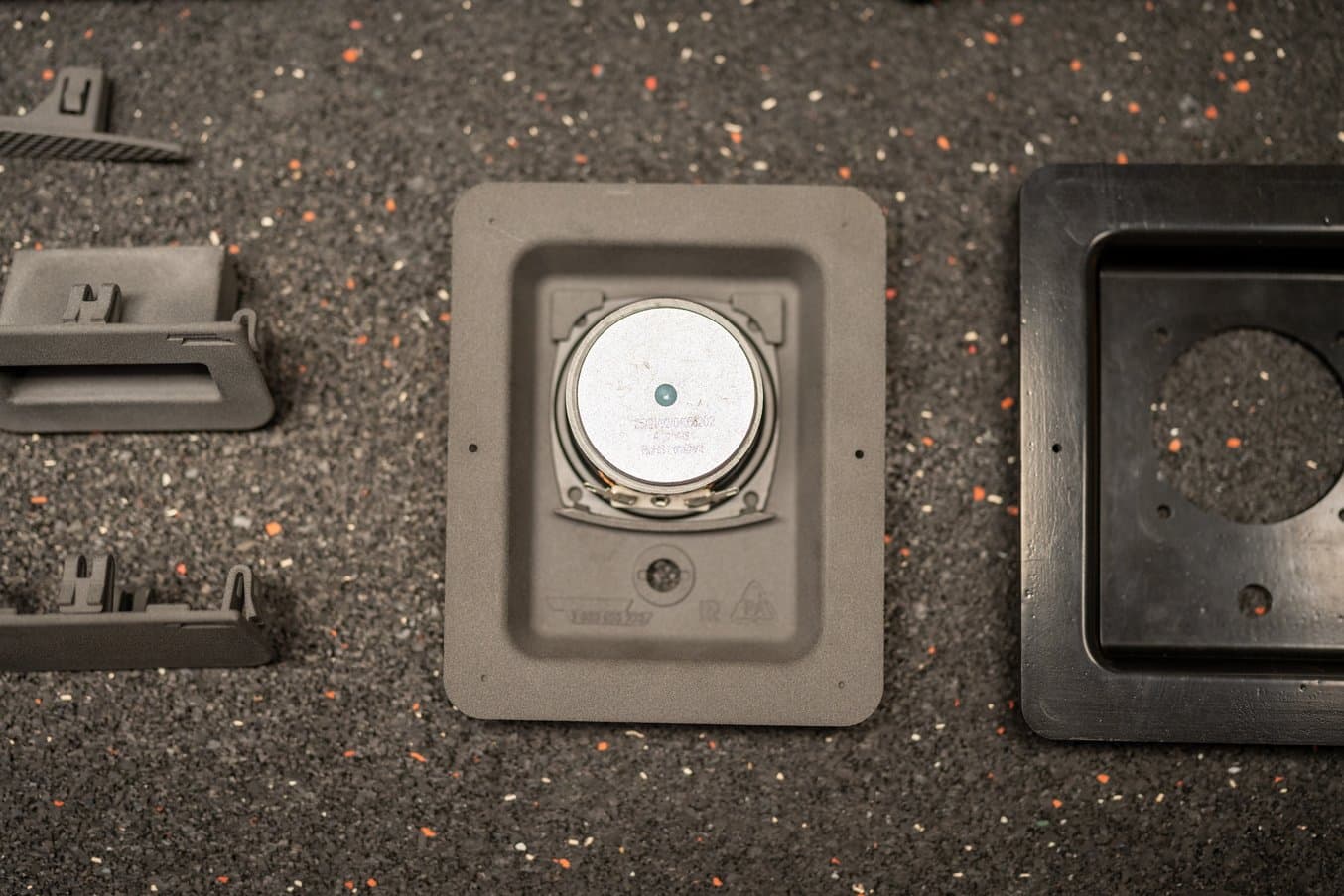
该扬声器盖设计可以节省 70% 的预安装成本。扬声器主体只需卡入插入件即可,无需粘接或机械固定。
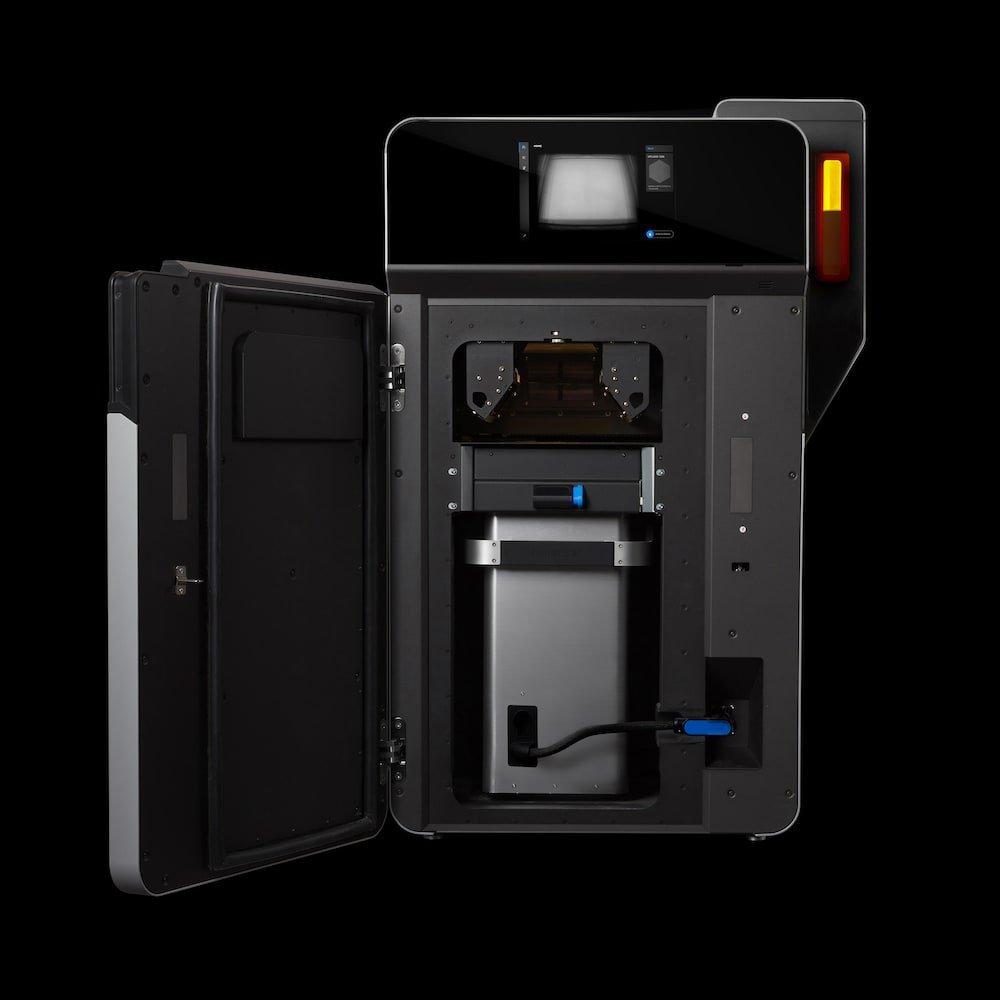
利用 SLS 3D 打印技术在 24 小时内定制成品部件
与注射成型、热压成型或钣金成型等传统的大规模生产工艺相比,增材制造的最大优势在于它可以生产定制或小批量成品部件,而无需使用昂贵的模具。
MOSOLF 的原型制造、设计和技术构思负责人 Tiberiu Morariu 说:“我们将 SLS 技术,特别是 Fuse 1+ 30W 用于制造不同的部件,从最小巧、最简单的设计到安装在车辆上的复杂控制台。我们一直在广泛使用这项技术,Fuse 满足了我们大约 80% 的需求。”
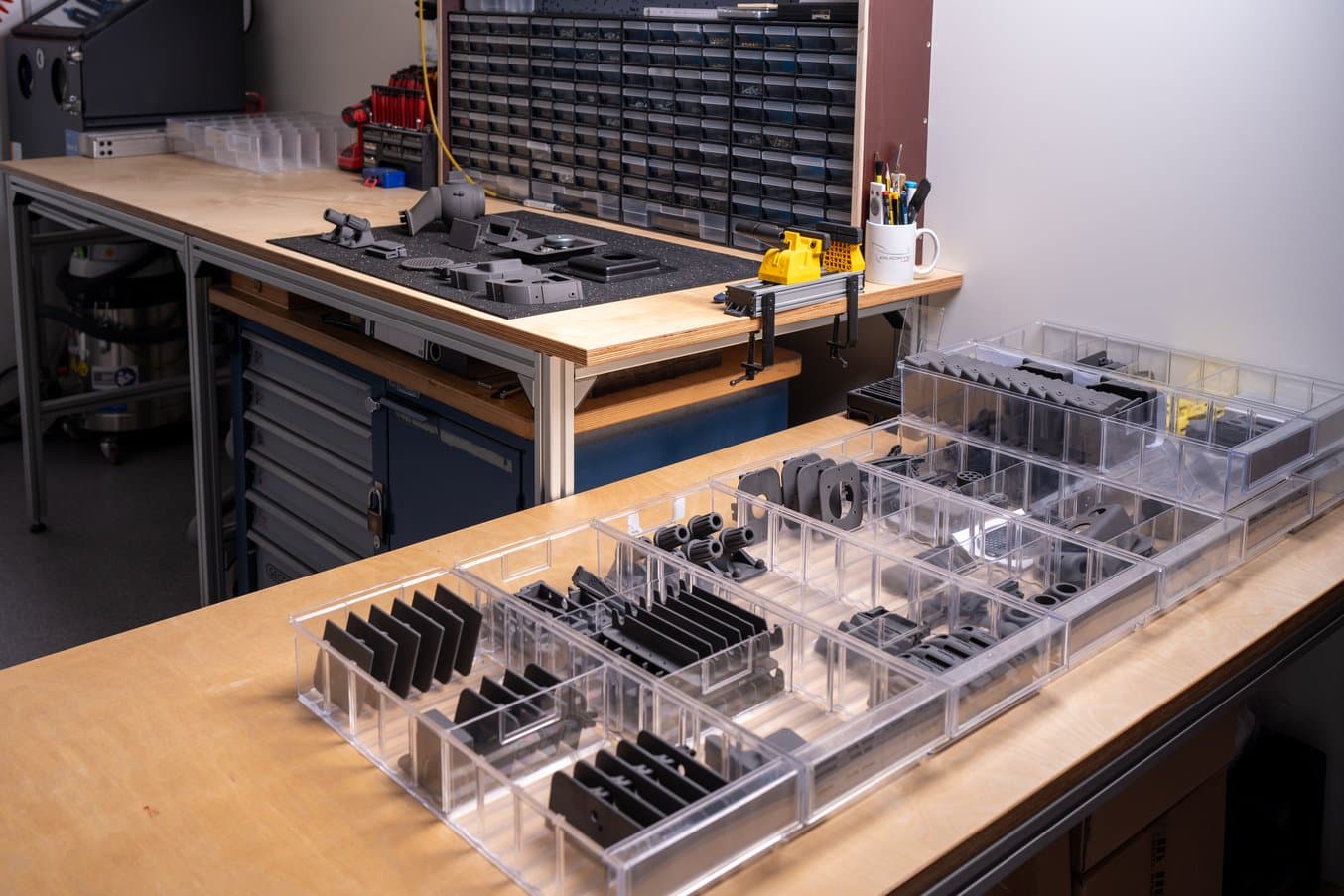
MOSOLF 的团队使用 SLS 3D 打印技术生产数十种定制设计,小到盖子和外壳,大到多件式装配和仪表板组件。
“各州、各警察局的要求各不相同。使用 3D 打印技术可以更轻松地实现这些要求。可以根据不同的车辆快速重新设计。如果车辆相同,那么外形会保持不变,但随后安装在车辆上的系统却大不相同,”Morariu 说。
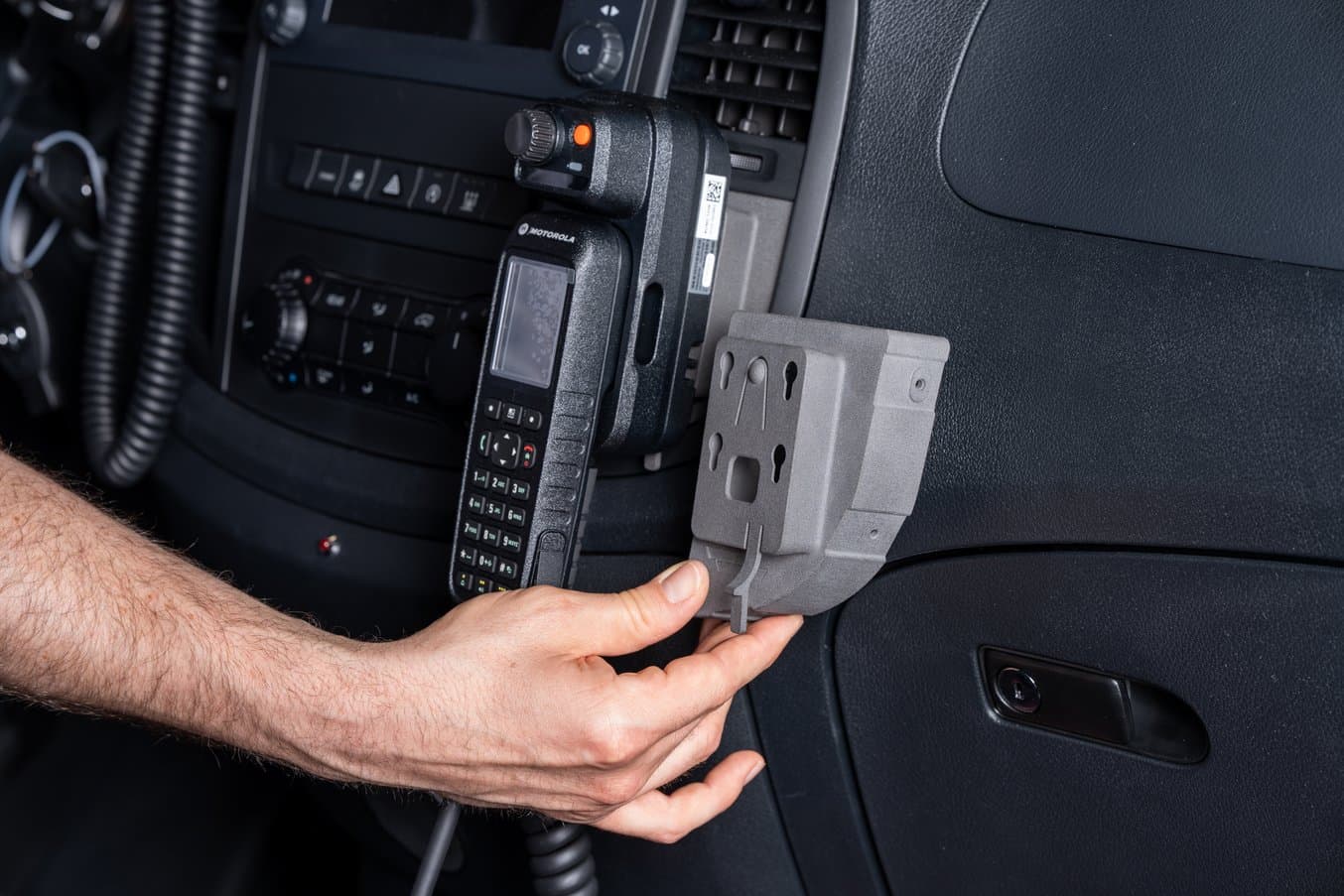
收音机支架就是出色的定制范例。每辆梅赛德斯车与控制台的连接均相同,但可以轻松改装整体装配,以便为不同制造商的收音机安装不同的支架。
这种简单的适应性大大加快了原型制造和生产的速度,特别是原型和最终使用部件都可以使用同一台设备生产。
Morariu 说:“对于设计师而言,如果我今天构思了一个创意,将其绘制出来,在第二天就能拿到实物并加以观察,那么这简直太棒了。”
“3D 打印对内部生产的最大影响在于,我们在许多方面的工作速度明显加快。使用传统工艺的周转时间需要四到六周,尤其是在部件需要涂层的情况下。有了 3D 打印,我们几乎可以在一夜之间获得部件。如果没有 3D 打印技术,我们的工作流程可能会更漫长、复杂,因为我们可能需要多次逐个制造和调整部件。”
Carsten Busam,MOSOLF Special Vehicles GmbH 项目策划主管
SLS 3D 打印 | 钣金成型 | 热压成型 | 注射成型 | |
---|---|---|---|---|
从设计到原型再到系列部件的时间 | 1-2 周 | 6-8 周 | 6-8 周 | 6-8 周 |
成品部件的周转时间 | 1-2 天 | 6-8 周 | 6-8 周 | 6-8 周 |
其他因素 | 无需制造模具 轻松定制 设计自由 外观优越 | 需要制造模具 设计自由度有限 难以定制 外观不佳 | 需要制造模具 设计自由度有限 难以定制 | 需要制造昂贵的模具 无定制选择 设计自由度较低 |
“如今的汽车内饰越来越美观流畅。储物空间不断变化且日益复杂。3D 打印对于汽车的设计和人体工学来说非常重要,因为其他技术(如热压成型或钣金成型)都无法实现这一点。3D 打印技术还能很好地解决这些复杂形状与车辆本身的连接问题。借助 3D 打印技术,我可以更加自由地进行设计,在设计和造型方面充分发挥自己的创造力。”
Tiberiu Morariu,MOSOLF 特种车辆有限公司原型制造、设计和技术概念
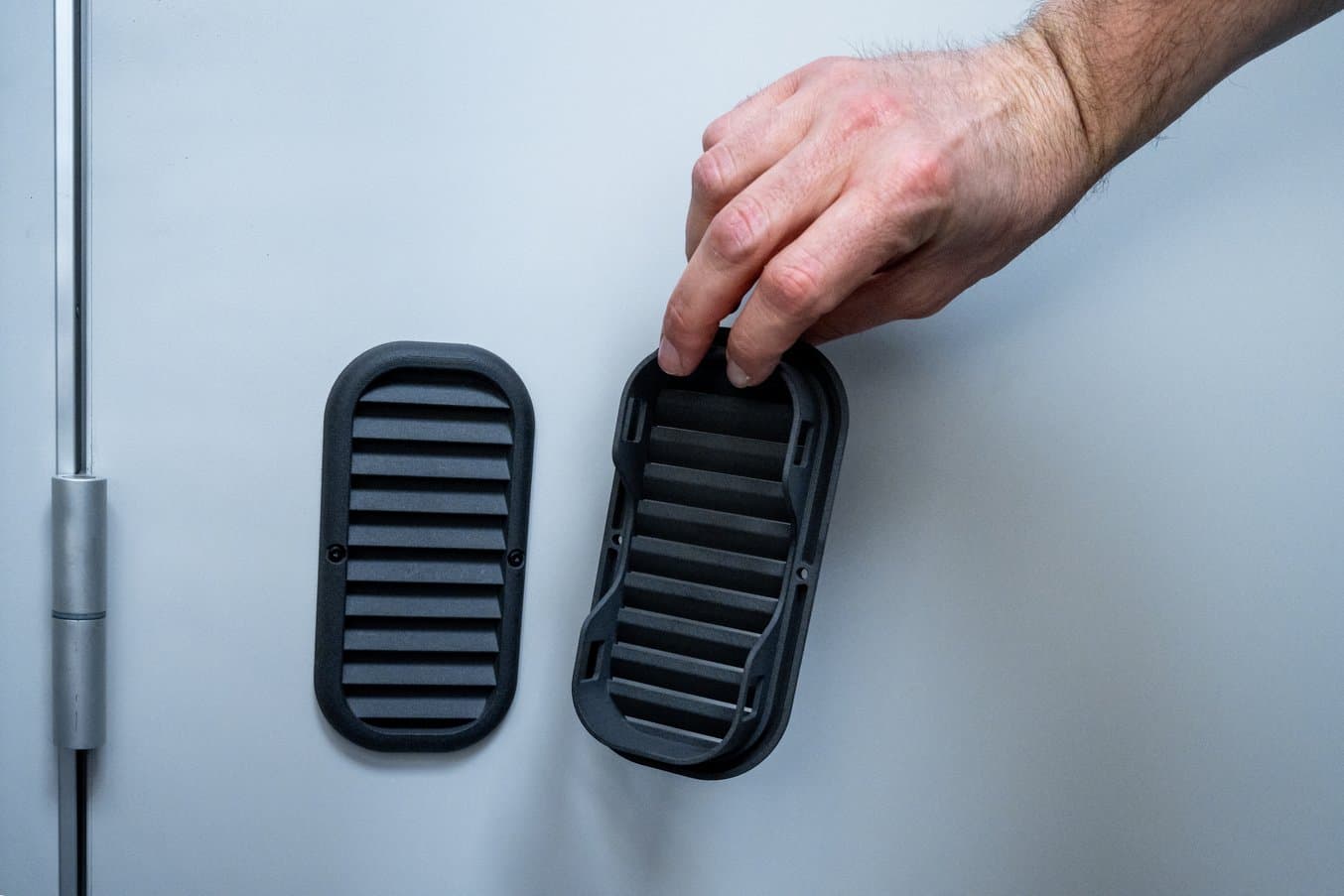
该排气口为单向阀,用于分隔火灾事故调查专用车辆的黑白车厢。该装配的设计相对复杂,由三个拧接在一起的部件组成。团队最初尝试使用 FDM 3D 打印技术来制造,但由于其圆形和薄壁的特点,遇到了一些挑战,于是转而使用 SLS 3D 打印技术,以便获得更大的设计自由度。
SLS 3D 打印的主要优势之一是工程师熟悉其可用材料的机械性能,如尼龙,这种材料常用于汽车行业的内外饰件生产。MOSOLF 的团队对 SLS 3D 打印尼龙部件的性能了如指掌,因此他们在设计时可以充分考虑功能性,甚至可以取代一些原有的金属部件。
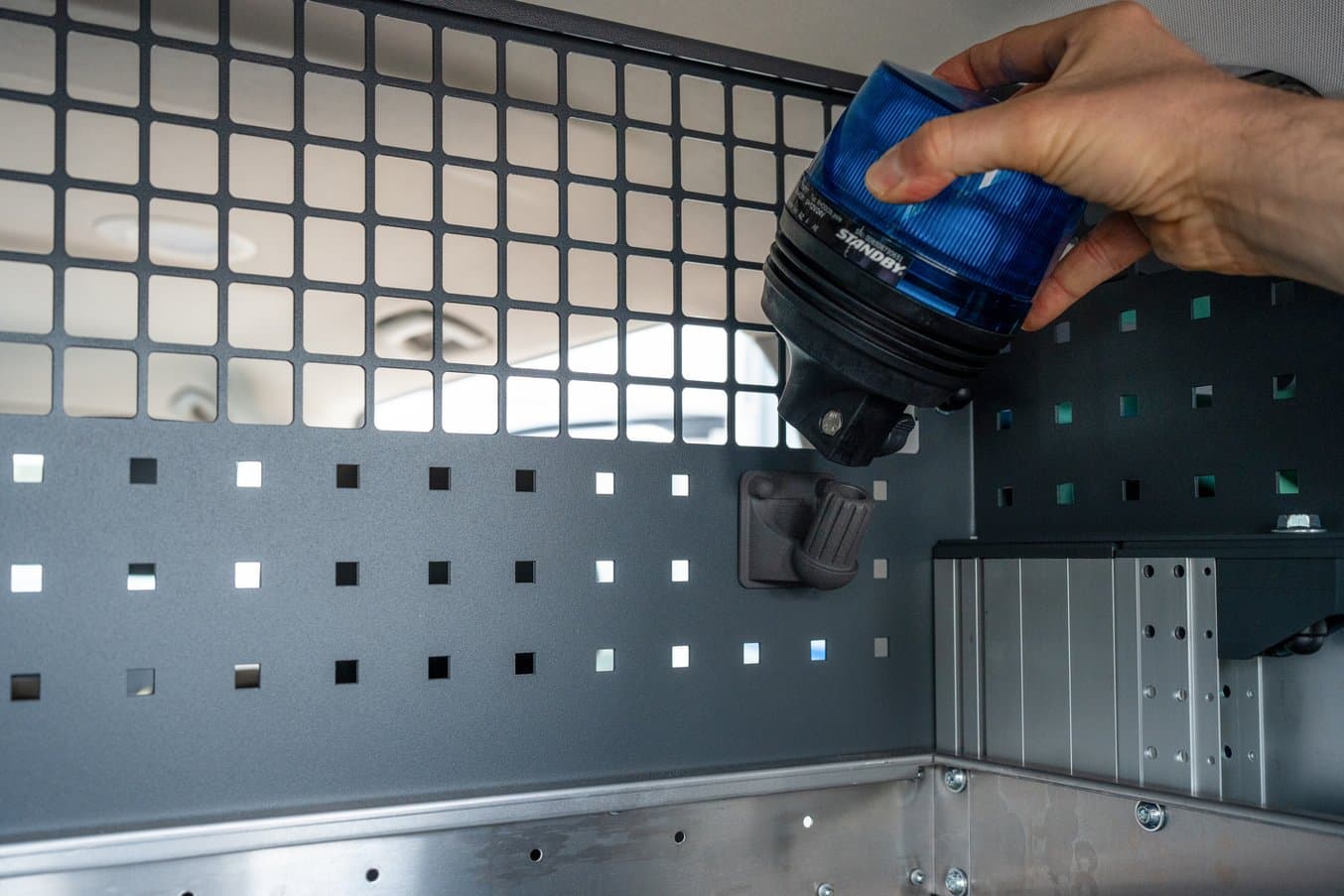
货舱内的可拆卸应急灯夹式支架。
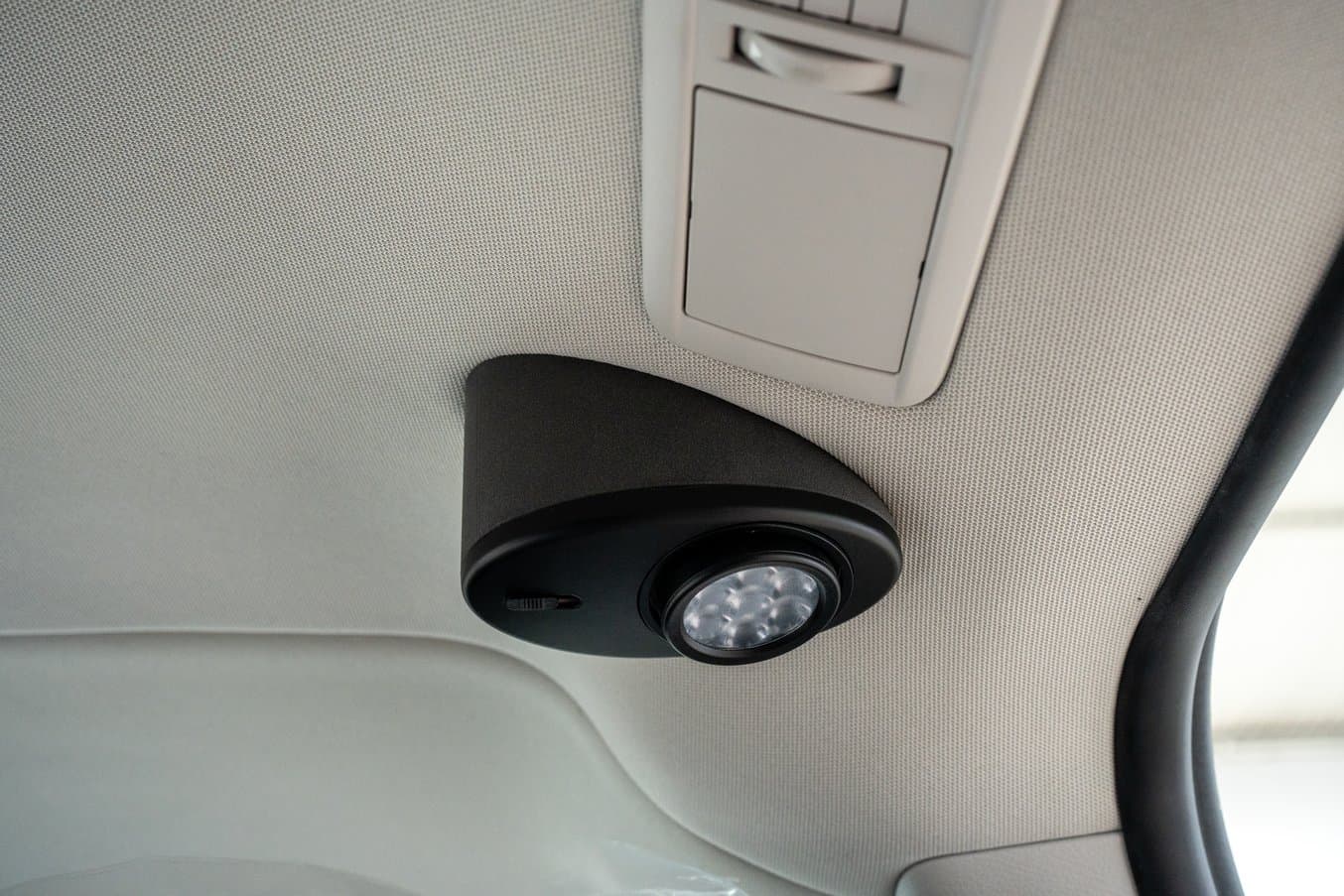
吸顶灯的外壳和支架。
“有了 Fuse 生态圈,自然而言就会获得完美的材料。可以随时使用。同时应用历史悠久。经过了全面的测试,”Duda 说。
除了耐用性,汽车应用最重要的标准之一是耐热性。对于 FDM 材料,无法使用 PLA,因为其在 0.45MPa 时的热变形温度 (HDT) 只有 50ºC 左右。ABS 在 0.45MPa 时的 HDT 为 90ºC,虽然略有提高,但仍处于或低于许多应用的极限。Formlabs Nylon 12 Powder 在 0.45MPa 时的 HDT 为 171°C,耐热性大大提高,这意味着当夏天汽车在停车场升温时,诸如收音机支架等功能性部件不会出现故障。
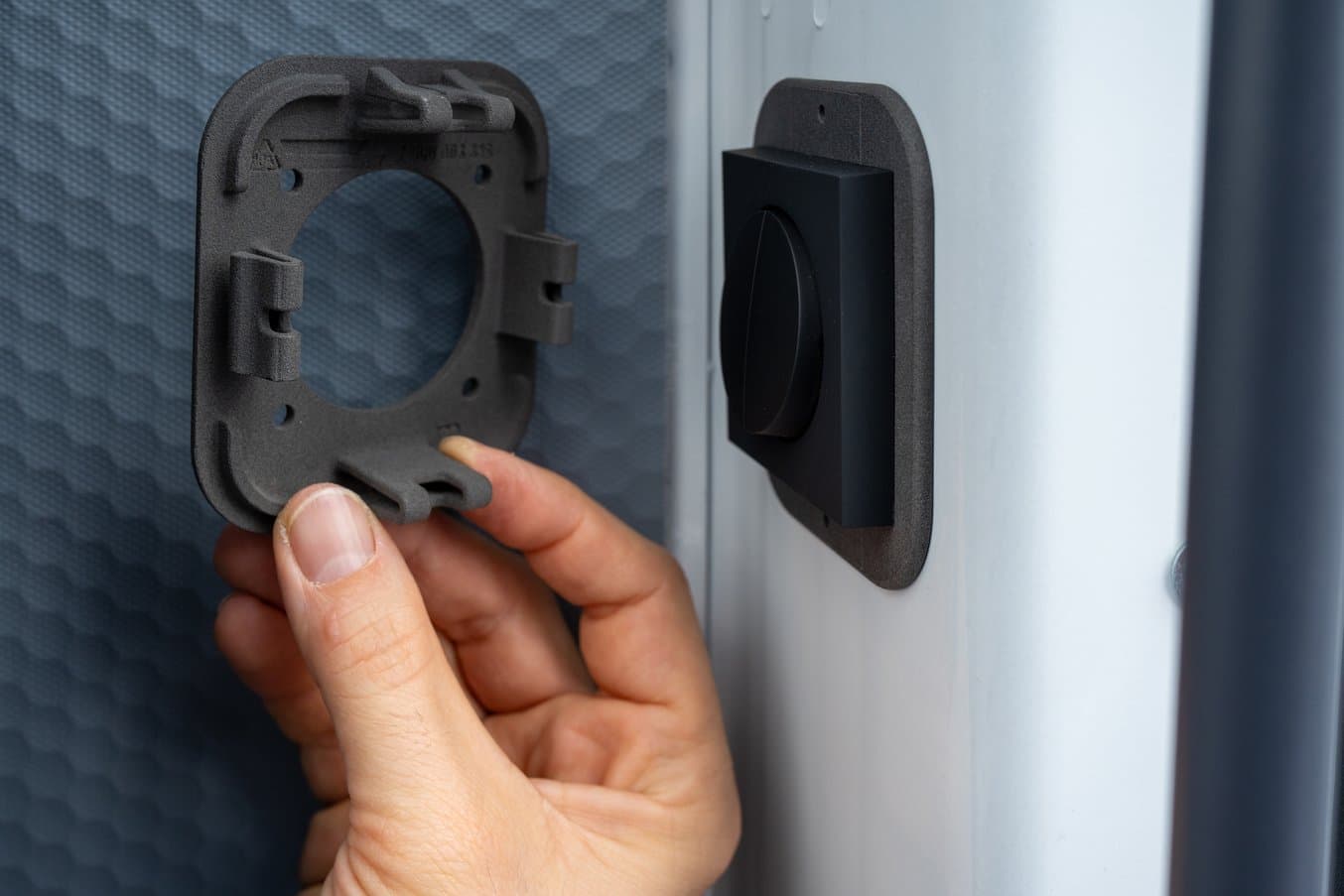
插座外壳。
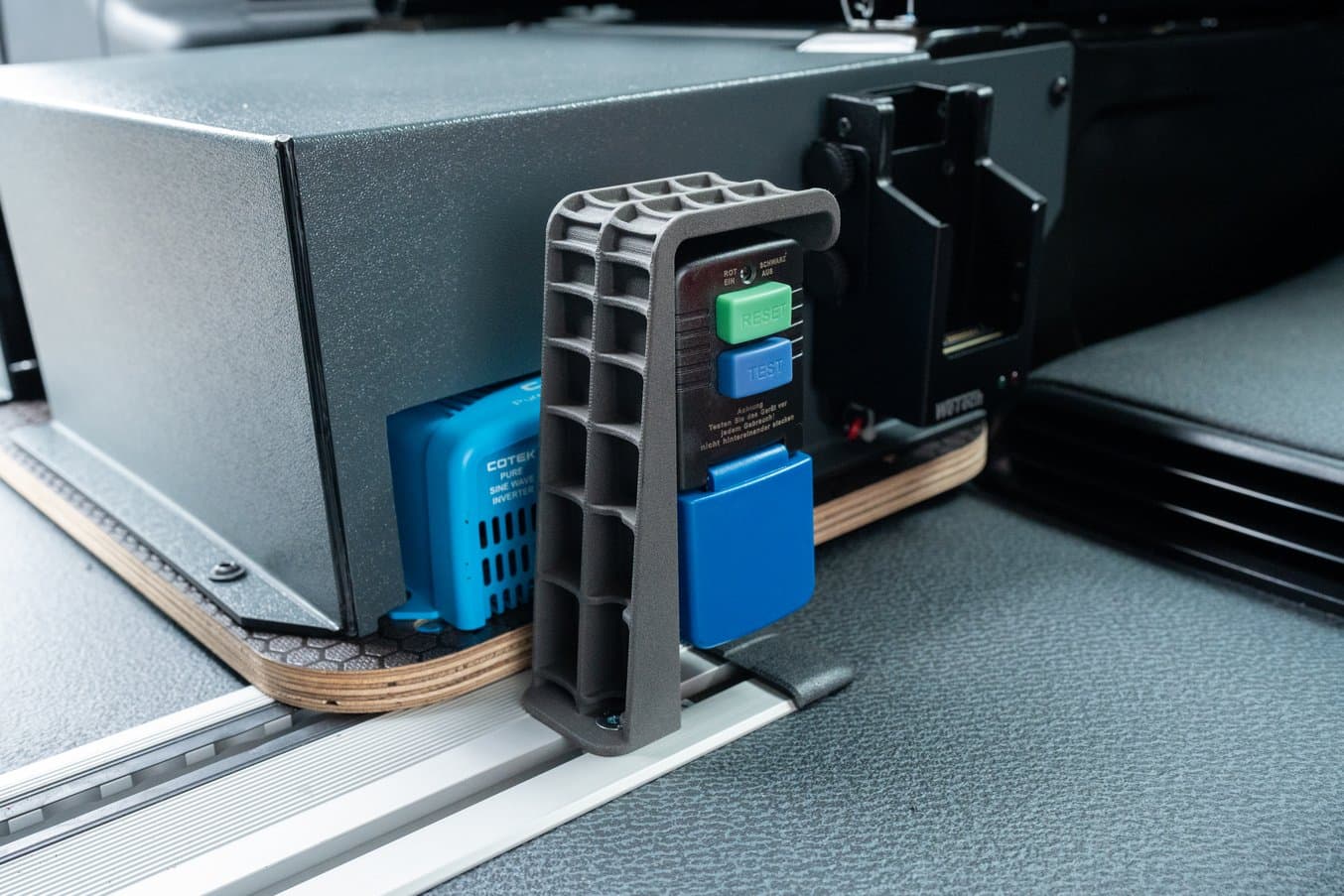
保护罩用于避免在车内移动时意外损坏。
在一些情况下,某些车辆会被租借给警察或紧急部队,使用期满后再出售给普通群众或国家其他部门。为此,MOSOLF 的团队必须在不损坏或永久性改变任何物品的情况下对这些车辆进行改装,以便在其使用寿命结束时易于恢复原状。增材制造也有助于简化这一工作,该团队不需要永久性地改装现有部件,而是用 3D 打印部件替换,之后再进行更换。
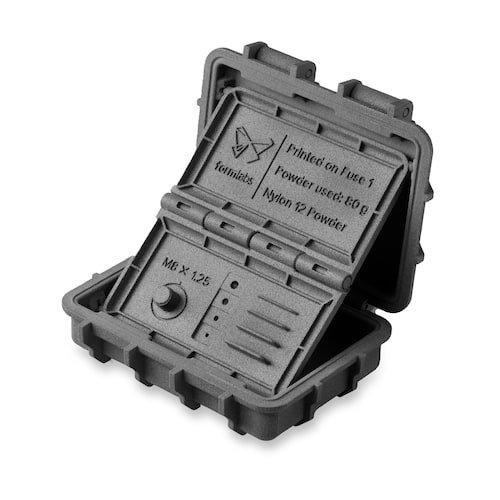
未来警车将进一步采用 3D 打印技术
在 SLS 3D 打印技术取得成功的基础上,MOSOLF 和 3D-WERK 的团队目前正在评估如何利用其他材料和其他打印机来替换特种车辆中的更多部件。
MOSOLF 总经理 Michael Ringwald 说:“在增材制造领域深耕数年之后,我现在仍然会惊讶于我们自己设计、打印的产品,这些产品具有 3D 打印提供的所有功能和可能性。”