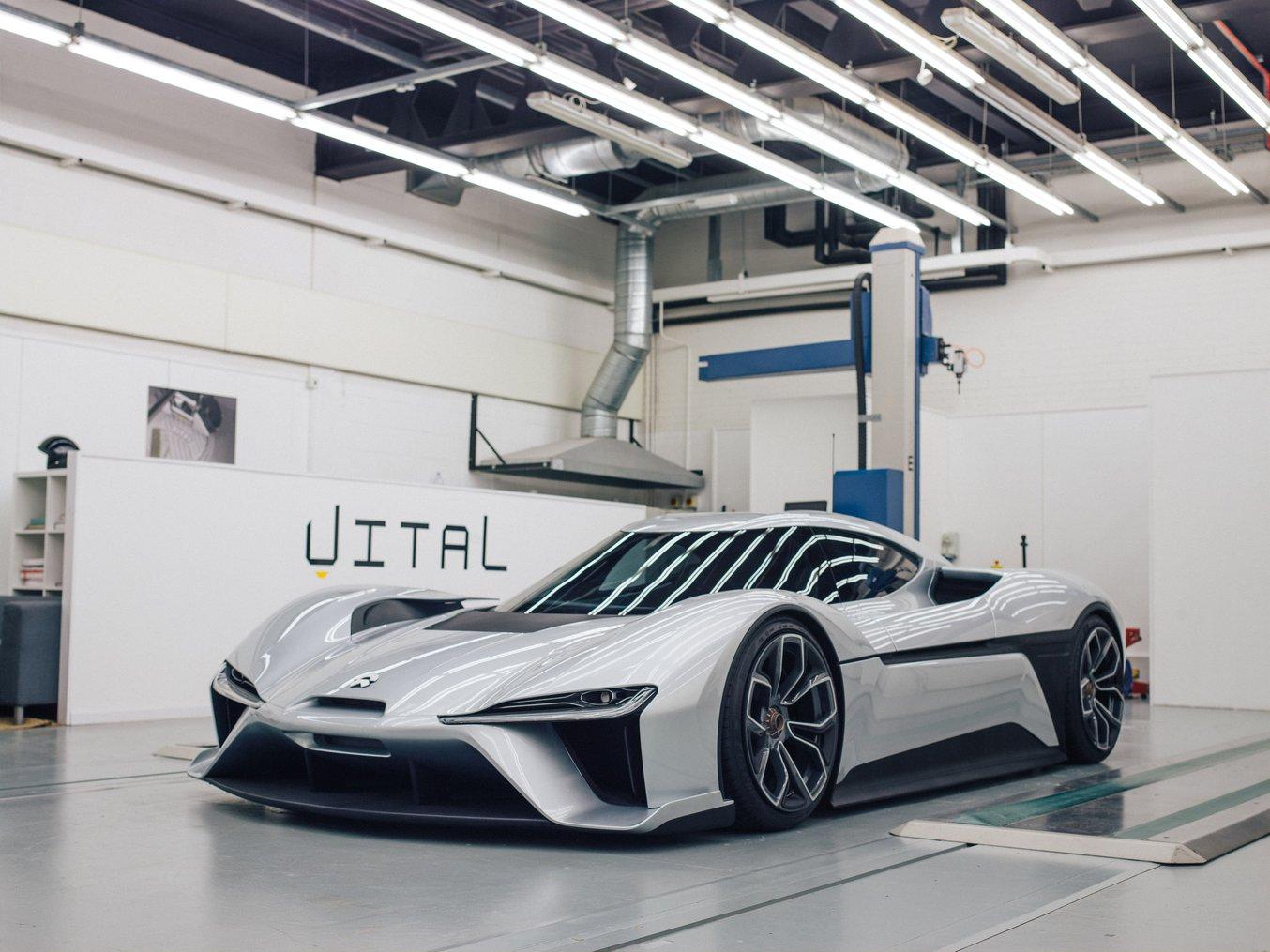
虽然我们目前还不能在经销商处购买 3D 打印汽车,但多年来 3D 打印一直是汽车开发过程中至关重要的部分。但最近我们已惊喜地发现,3D 打印用例已开始在整个制造业中站稳脚跟。
3D 打印可以为供应链带来巨大的价值,扩大生产应用范围。这项技术的可行性越来越高,价格也越来越便宜,因此公司可以在内部进行增材制造,为车间生产流程提供支持。新型弹性材料可用于生产高精度的功能性 3D 打印件,为替代最终部件、实现(大规模)定制生产和生产高性能部件带来了新的可能,但一切才刚刚开始。
请继续阅读,了解 3D 打印在从设计到制造等环节中推动整个汽车行业创新的九个重要方式。
3D 打印在汽车设计和原型制造中的应用
在汽车行业,原型制造一直是最常见的 3D 打印用例。由于使用 3D 打印可以大幅提升原型制造的速度,快速原型制造几乎已经成为 3D 打印的代名词,且该技术已经彻底改变了产品开发过程。
通过 3D 打印,汽车设计师可以快速制造实物部件或组件的原型,制造对象包括简单的内饰元素和仪表板,甚至是整辆汽车的比例模型。快速原型制造可帮助企业将想法转化为令人信服的概念验证。然后,将这些概念推进为与最终结果紧密匹配的高保真原型,并最终指导产品通过一系列验证阶段,最终实现大规模生产。
在过去,产品会经过数次迭代,因此原型制造既耗时又昂贵。凭借 3D 打印技术,我们以远低于传统制造方法的成本,在一天内即可制造出极具说服力和代表性的功能性原型。利用桌面级 3D 打印机,工程和设计团队可将 3D 打印技术引入内部,以增加迭代周期并缩短想法与最终产品之间的距离,从而强化整体产品开发工作流程。
1. 使用 3D 打印当天制作汽车原型
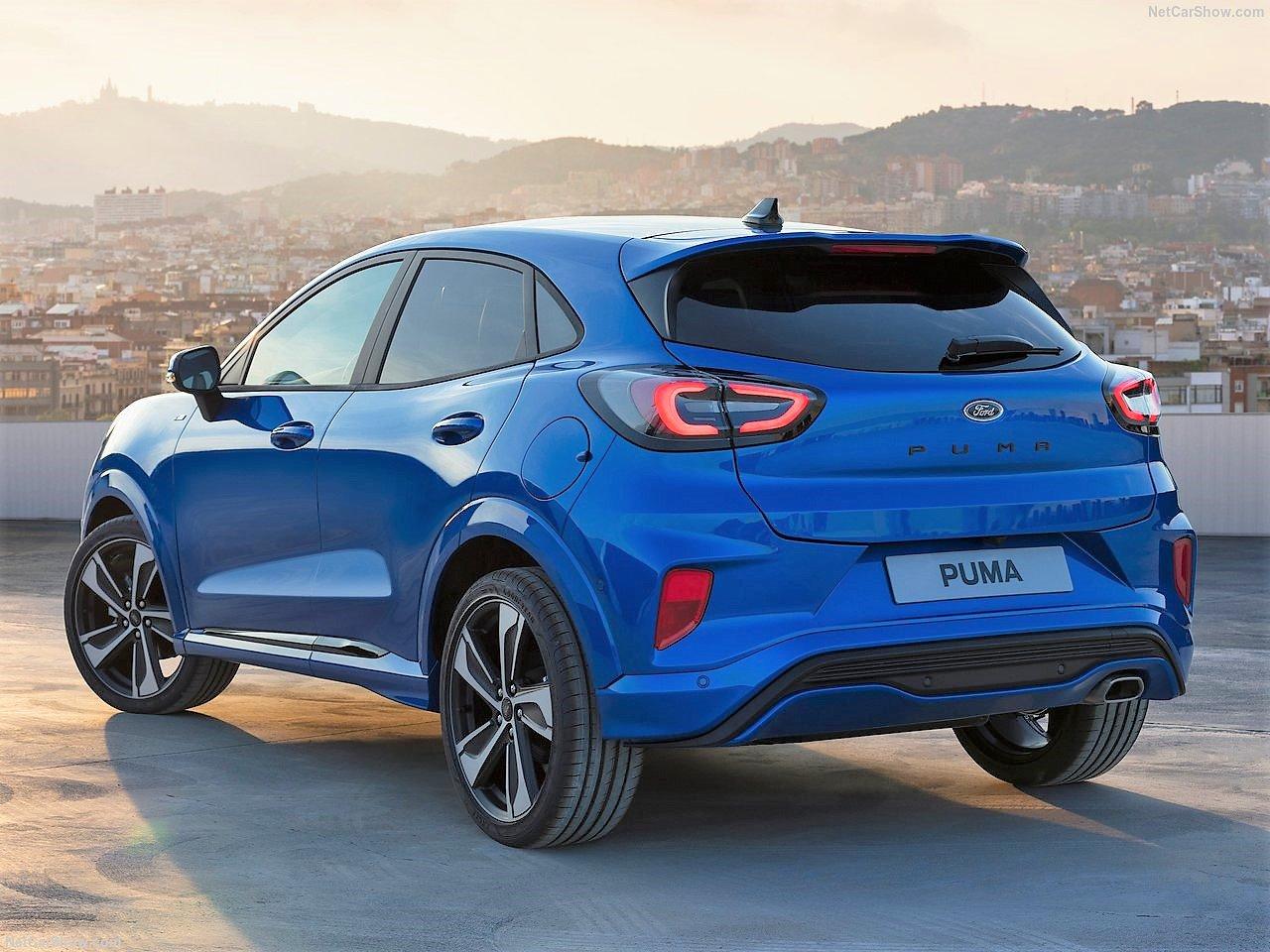
Ford 设计师使用 Formlabs 3D 打印机在几个小时内就制作出了 Ford Puma 汽车后部的字母原型。
Ford 在德国默克尼希设立了快速技术中心,以便利用多种 3D 打印技术快速制造原型。工程师和设计师不再需要将任务交付车间后等待数周,而是在几个小时内就能拿到设计成果。
在快速技术中心,设计师当天就可以制作出原型,并在短短几个小时内完成多次设计迭代。Ford 增材制造专家 Bruno Alves 表示,实物原型比数字模型更有优势。
例如,使用 Formlabs 3D 打印机制作 Ford Puma 汽车后部的字母原型,有助于设计师在不同的光照条件下查看线条和阴影的呈现方式。Alves 说:“该打印机的打印速度很快,非常适合打印这类刻字,这有助于我们为设计师提供迭代选择。” “虽然您可以在 CATIA 或其他软件中查看效果,也可以模拟光照条件,但在把字母放到汽车上时,那种视觉、触觉以及所有的反射效果都与模拟结果完全不同。”
关于 3D 打印如何推动汽车巨头进行创新,请观看网络研讨会,了解我们与 Ford Motor Co. 的 Bruno Alves 和 Brose 的 Christian Kleylein 之间的对话。
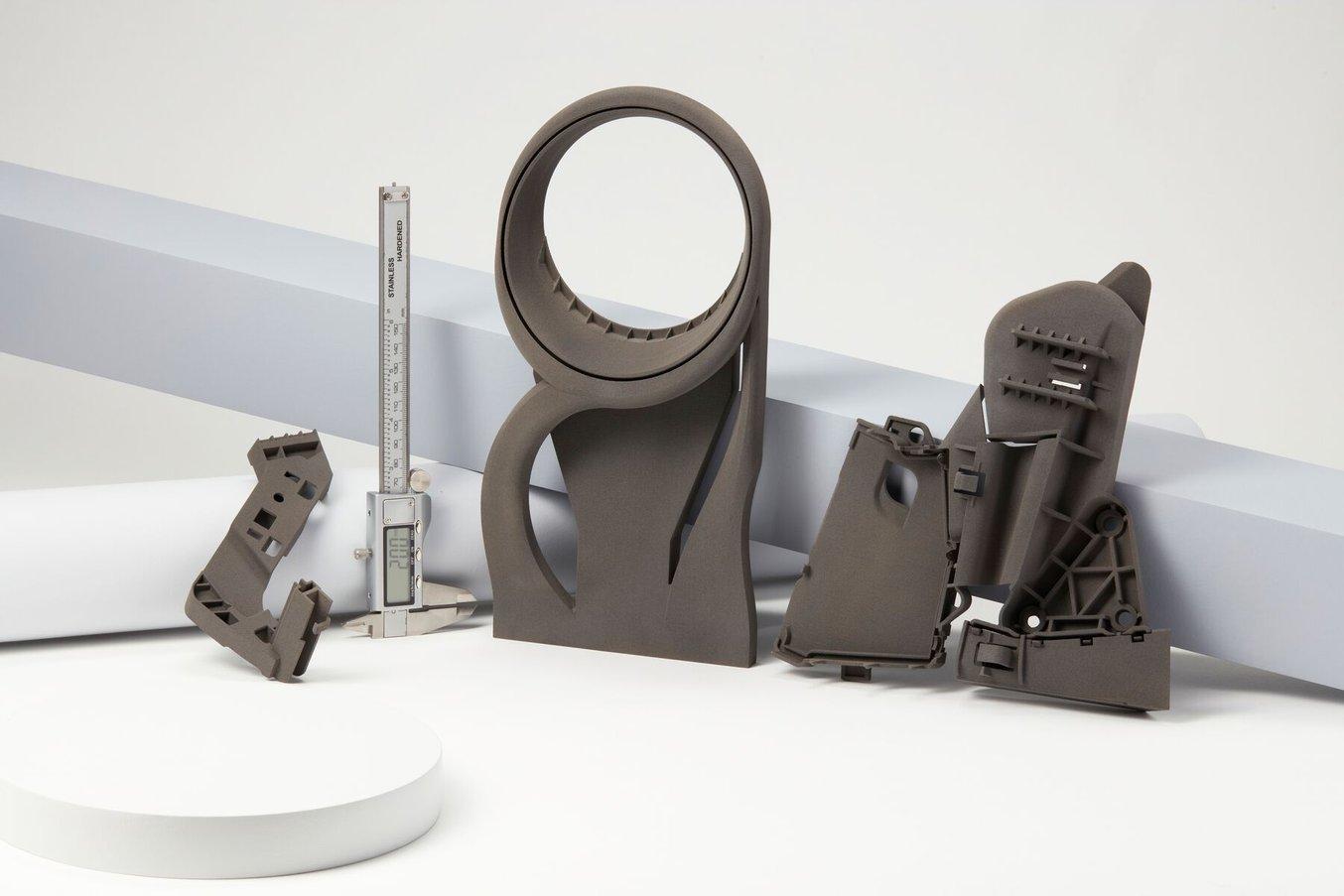
对话 Ford 和 Brose:两大汽车行业巨头如何使用 3D 打印进行批量生产
在本次网络研讨会中,最大的家族一级汽车供应商之一 Brose 的技术专家 Christian Kleylein 和 Ford 的增材制造专家 Bruno Alves 将共同分享 3D 打印如何在从设计到制造的全过程中推动整个汽车行业的创新。
2. 使用 3D 打印打造轻量化汽车部件
IGESTEK 是一家西班牙汽车供应商,专门开发使用塑料和复合材料的轻量化解决方案。从验证几何图形的概念设计阶段到实现功能性原型的详细设计阶段,IGESTEK 的团队在整个产品开发过程中均使用 3D 打印。他们还使用 3D 打印进行快速模具制作,如塑料注射模具嵌件或复合材料热成型工具。
拓扑优化是轻量化研究领域的热点。IGESTEK 可使用 Autodesk Fusion 360 根据参数列表生成多个解决方案。
针对悬架支架,该团队将基于衍生式几何结构的金属 3D 打印与更轻量化的复合材料相结合,打造出一种可提供最佳性能的多材料架构,其封装比当前市面上的解决方案轻 40%。该团队使用 Form 3L 制作了这些部件的原型,Form 3L 具有较大的成型体积,足以同时对多个设计进行原型制作,从而提高迭代和测试速度。
有关此应用的更多详细信息,以及 IGESTEK 轻量化汽车部件的其他两种制造方法,请阅读我们关于 IGESTEK 的用户故事。
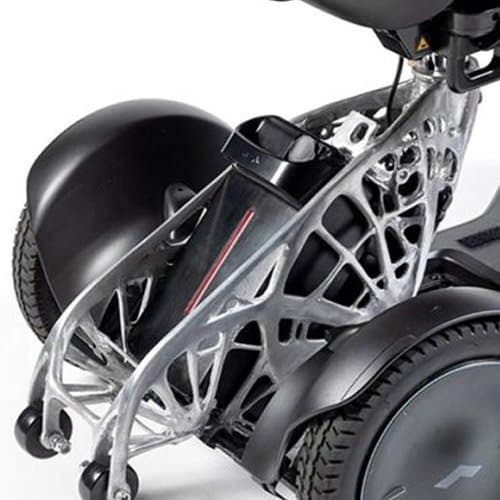
衍生式设计简介:利用 3D 打印生产轻量化部件
在本次网络研讨会中,Formlabs 产品营销主管 Jennifer Milne 将以机械部件的设计为例,简要介绍衍生式设计的原理,包括使用 Fusion 360 制作轻量支架的分步教学。
3. 使用 3D 打印将概念车变为现实
Vital Auto 是一家英国工业设计工作室,与沃尔沃 (Volvo)、尼桑 (Nissan)、莲花 (Lotus)、迈凯轮 (McLaren)、吉利 (Geely)、塔塔 (TATA) 等主要汽车品牌均有合作。如果原始设备制造商 (OEM) 自身没有时间进行实验,则他们会依靠 Vital Auto 将创意、初始草图、图纸或技术规格转化为可实现的实体模型。
“我们从一开始就使用了 3D 打印技术。我们希望将该技术引入我们的制造流程,这不仅是为了降低成本,还是为了使客户的设计和创意更加多样化,”负责增材制造的设计工程师 Anthony Barnicott 表示。
如今,Barnicott 运营着独立的 3D 打印部门,已经购置 14 台大幅面熔融沉积成型 (FDM) 打印机、3 台 Formlabs Form 3L 大幅面立体光刻 (SLA) 3D 打印机和 5 台 Fuse 1 选择性激光烧结 (SLS) 3D 打印机。“就产能而言,3D 打印机可以全天候不间断运行。我们将这些打印机用于概念和设计的所有领域。通常,我们会使用 Fuse 1 打印生产型部件,使用 Form 3L 打印概念型部件,” Barnicott 表示。
3D 打印技术不仅帮助团队更快速地打造更好的产品,还有助于吸引新客户。Vital Auto 发现,他们的许多客户之所以希望与他们合作,是因为这些客户希望应用最新的技术,并且希望使用最新的先进材料制造所需的组件。
“在过去 10 年间,3D 打印技术取得了惊人的进展。我们刚开始生产小批量的小众汽车时,根本无法实现如今可生产的产品。而现在,我们不仅能够生产这些部件,还能以极具成本效益的方式快速进行生产,”Barnicott 表示。
有关 3D 打印部件具体应用的更多见解,请查看 Vital Auto 团队的详细故事。
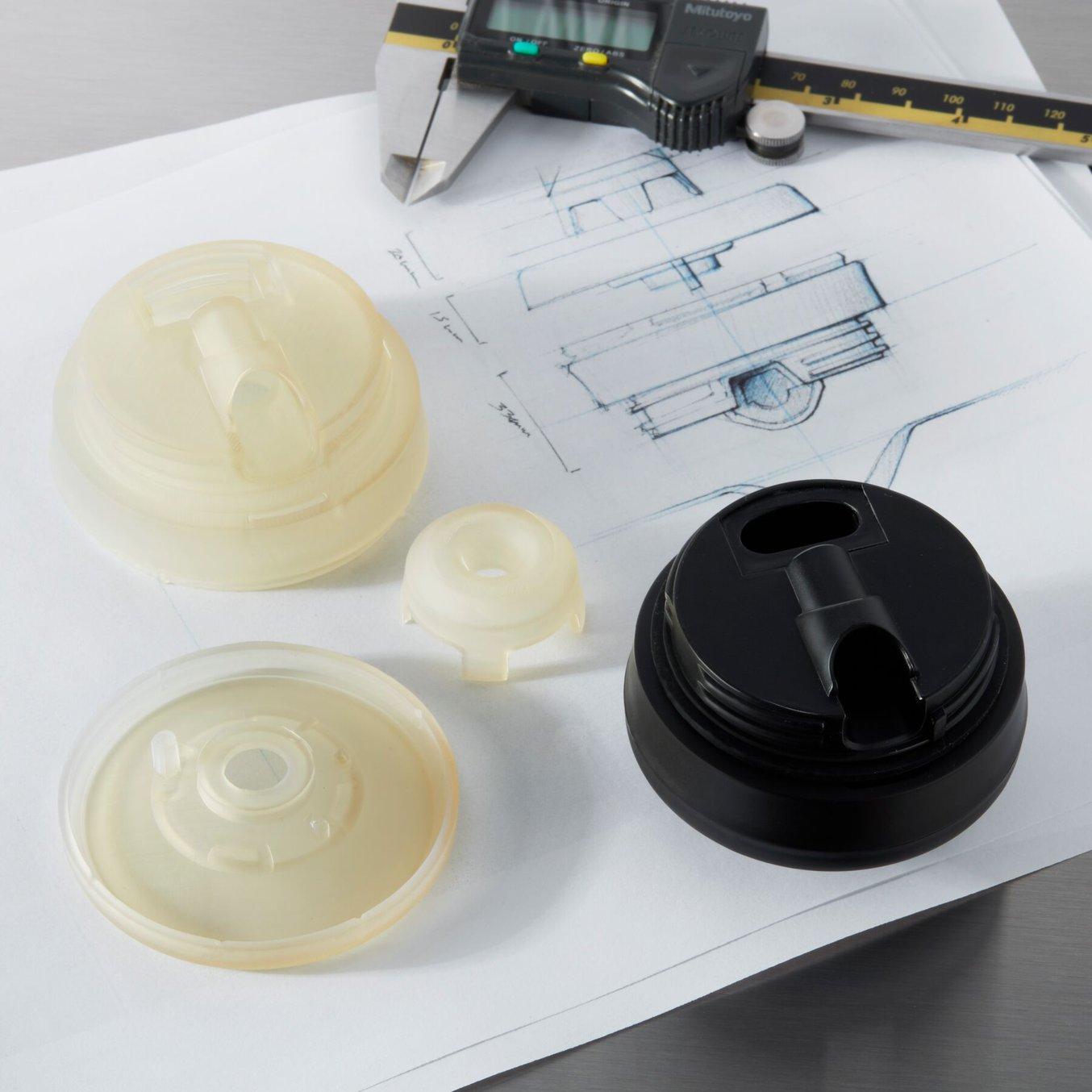
3D 打印在汽车制造领域的应用
得益于 3D 打印机和高性能材料领域的快速发展,如今增材制造已可用于生产能够应对极端环境挑战的部件。
您可在制造领域中充分利用 3D 打印技术,通过定制夹具和固定装置等制造辅助设备来减少开销并提高效率,并为注射成型或热成型等传统制造工艺快速制作小批量模具。
3D 打印成品部件在汽车行业的应用也愈发普遍,特别是在售后市场、定制或替换部件等应用领域;在这些领域,其他生产方式的成本过高且速度缓慢。
4. 将 3D 打印模具和模粒用于制作汽车部件
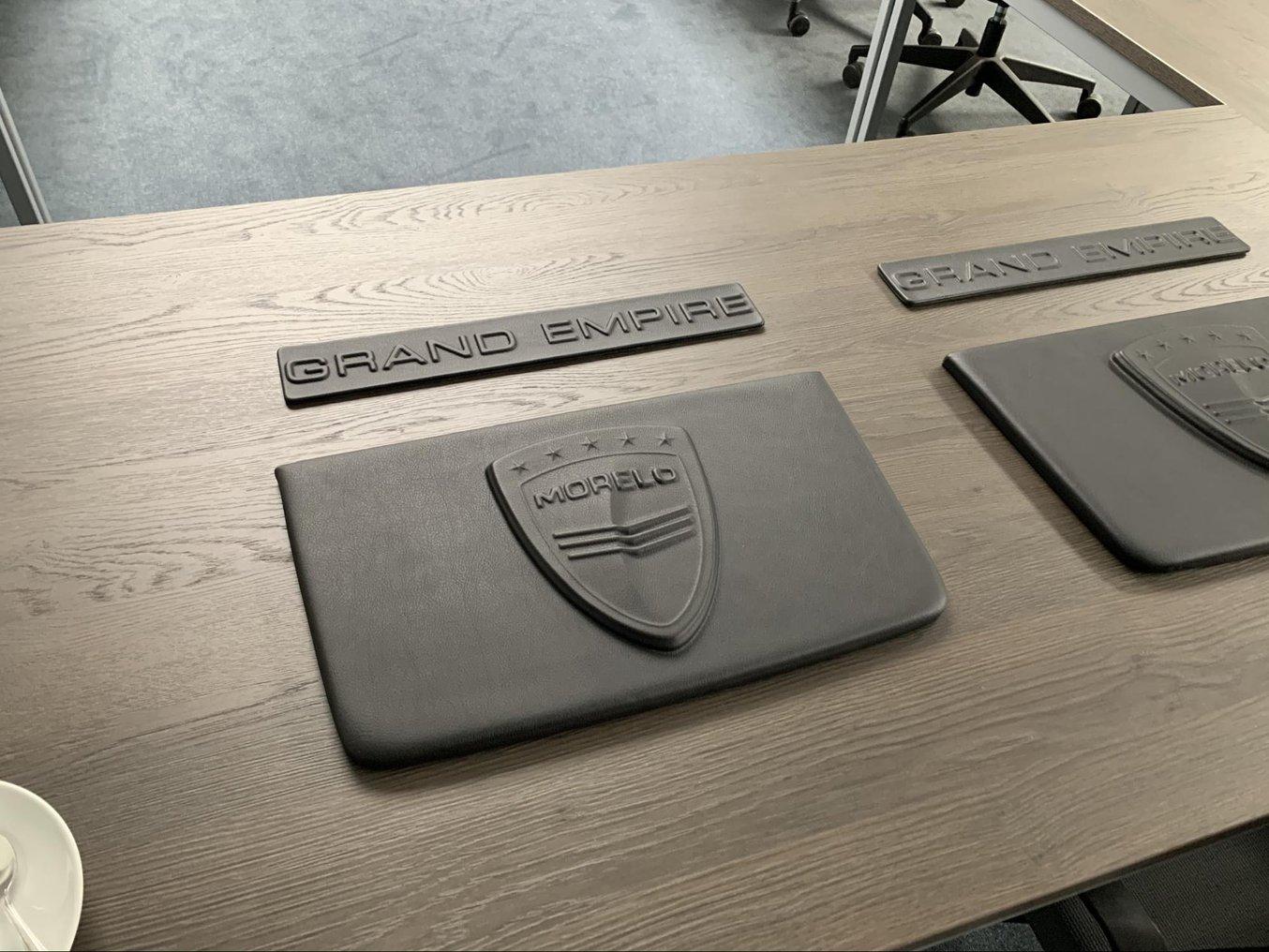
Makra Pro 开发了一种使用 3D 打印模具制作皮革装饰件的新技术。
皮革是一种常用于高档轿车但难以成型的装饰材料;而增材制造服务提供商 Makra Pro 则使用 3D 打印模粒开发了一种新颖的皮革成型工艺。他们的客户包括高档轿车、摩托车和房车的制造商;在合作过程中,他们测试了一种真皮成型和压纹的方法。
Makra Pro 在该技术中使用了 Form 3 打印的模具,并利用膨胀的泡沫在受拉皮革面板上均匀地分布压力。随着泡沫硬化,皮革被压入模具并成型。
例如,可以将成品皮革部件在汽车门板上拉伸,或将其附着在汽车的座椅套上。一家知名的限量版高档轿车改装公司将这些成型的皮革部件用于改进车辆的内壁或顶板。
阅读我们关于 Makra Pro 的完整故事或下载我们的白皮书,以了解包括注射成型、热成型等在内的更多快速模具制作应用。
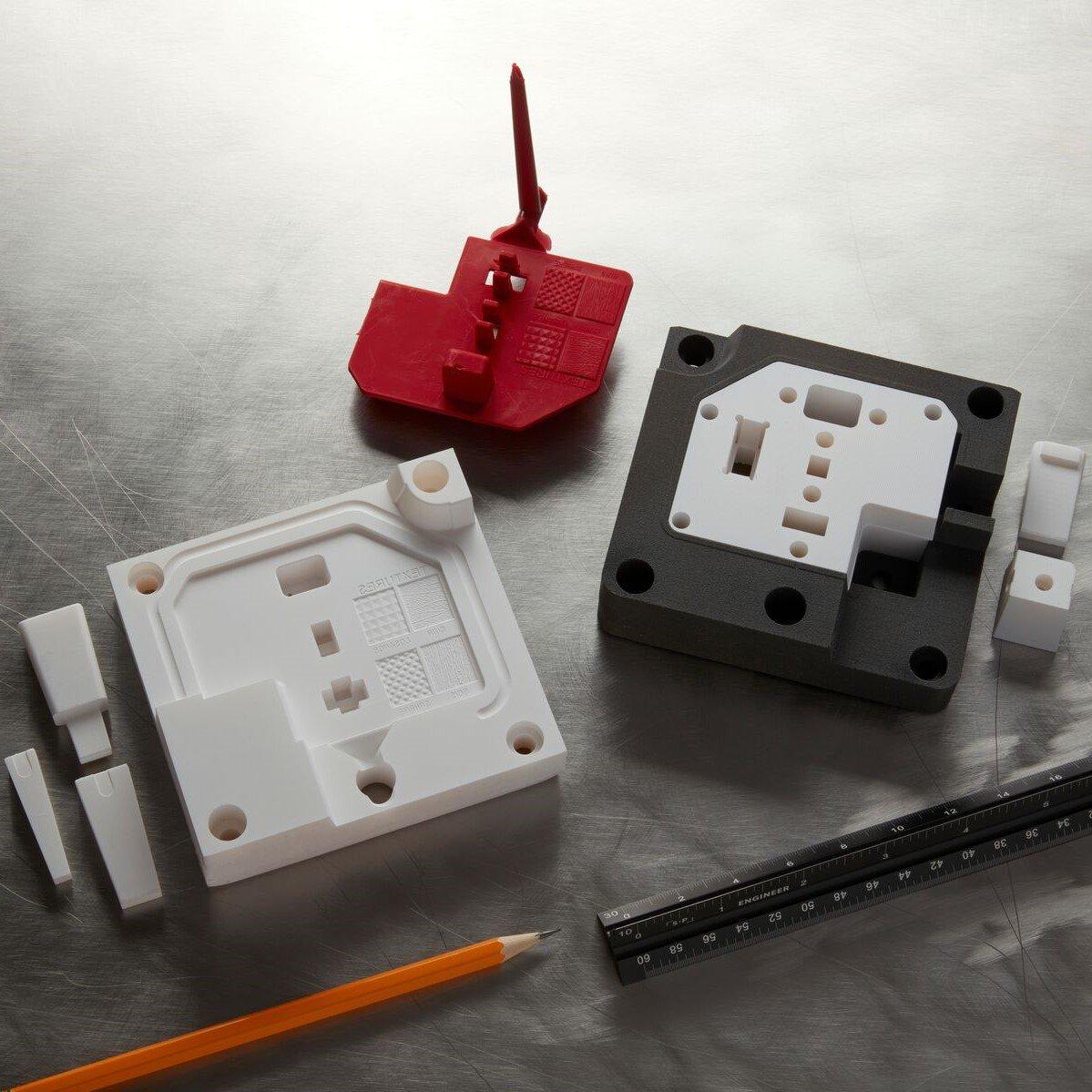
5. 3D 打印制造辅助工具
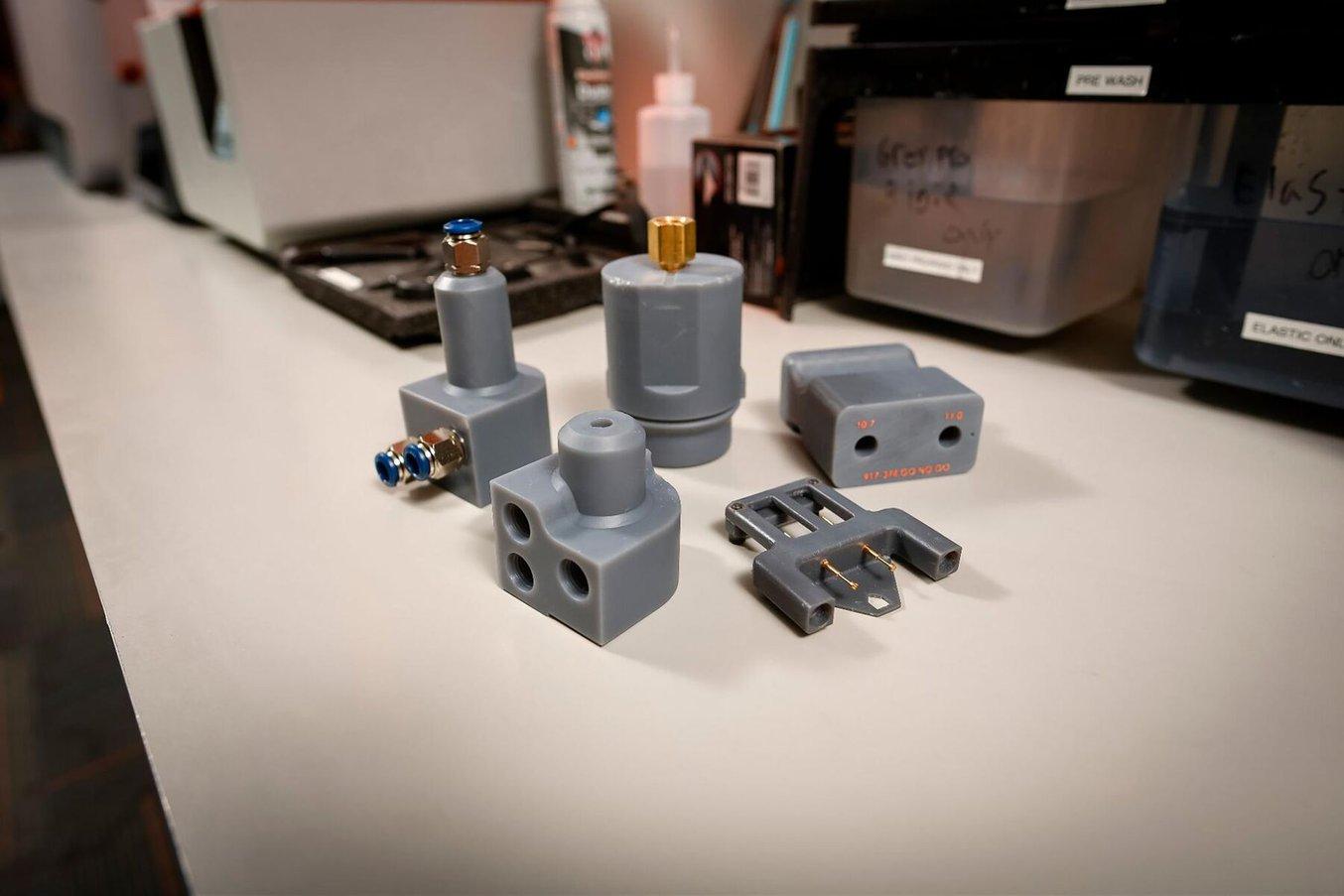
Dorman Products 使用 Grey Resin 制作通止测试夹具,其精度为 +/-0.05mm。
Dorman Products 设计并管理的数据库中包含数百种不同车辆的 10 万余个部件。机械设计团队经理 Eric Tryson 说:“过去,我们每年都会推出 4000 到 5000 个新部件。”
增材制造主管 Chris Allebach 表示,除了作为售后服务供应商要面对的纯粹物流挑战之外,Dorman 的产品设计和制造团队还需要特别敏捷。“OEM 的团队有时会在新车上市前两年就开始设计单个部件。我们需要想尽办法来确保我们的替代品可靠,同时保证其能够尽快上市。”
在将 3D 打印机纳入工作流程之前,缺乏定制测试固定装置成为了他们快速开发工作的阻碍。机械加工非常昂贵和耗时。
“现在,有了 3D 打印机,我们在制作产品原型的同时,可以开发测试固定装置和量规,所以当我们确定最终设计时,我们也可以用固定装置进行测试。我们正尽可能地主动出击,”Allebach 说。
自从十年前 Dorman 购置了第一台 3D 打印机,Allebach 和 Tryson 陆续购买了更多打印机,不断增强现有设备的性能,并在包括大幅面 Form 3L 在内的 Formlabs SLA 打印机上使用完整的材料库。
“我们在两个月内就实现了 [第一台 3D 打印机的] 购买资金回笼。进行成本或投资回报率评估时,我们发现无需花费两年时间,任何一台 Formlabs 打印机都可以在数月内获得投资回报。这让我们的领导层确信 3D 打印是一项值得投资的技术,”Tryson 说。
Dorman Products 公司正在将 3D 打印技术应用于其他几个领域。阅读我们的文章以了解详情。
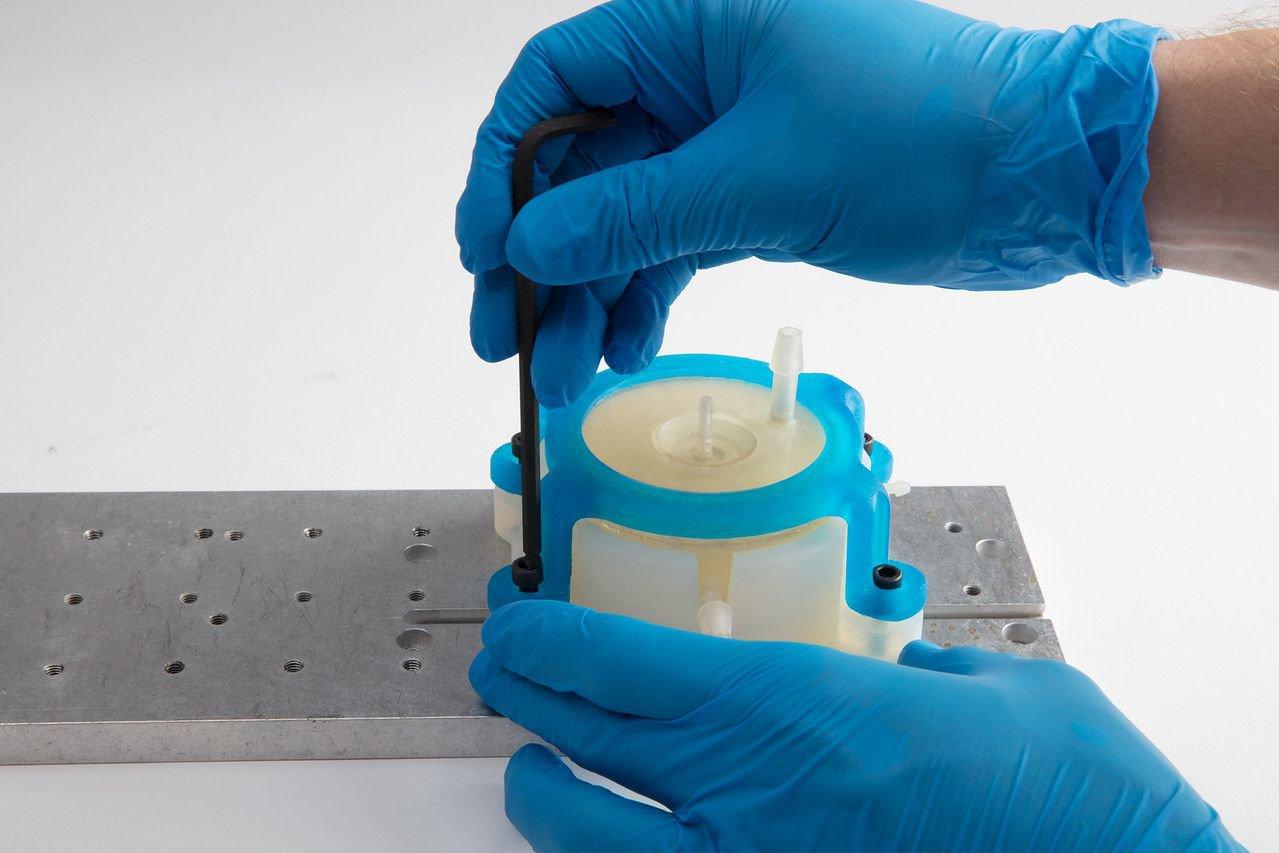
借助 3D 打印技术设计夹具和固定装置
对于制造商而言,最大限度地提高生产速度,并制造出高质量的部件是成功的关键。使用夹具和固定装置使制造和装配过程变得更加简单可靠,有助于在缩短生产周期的同时,保障工人安全。
6. 使用 3D 打印制作的成品售后部件
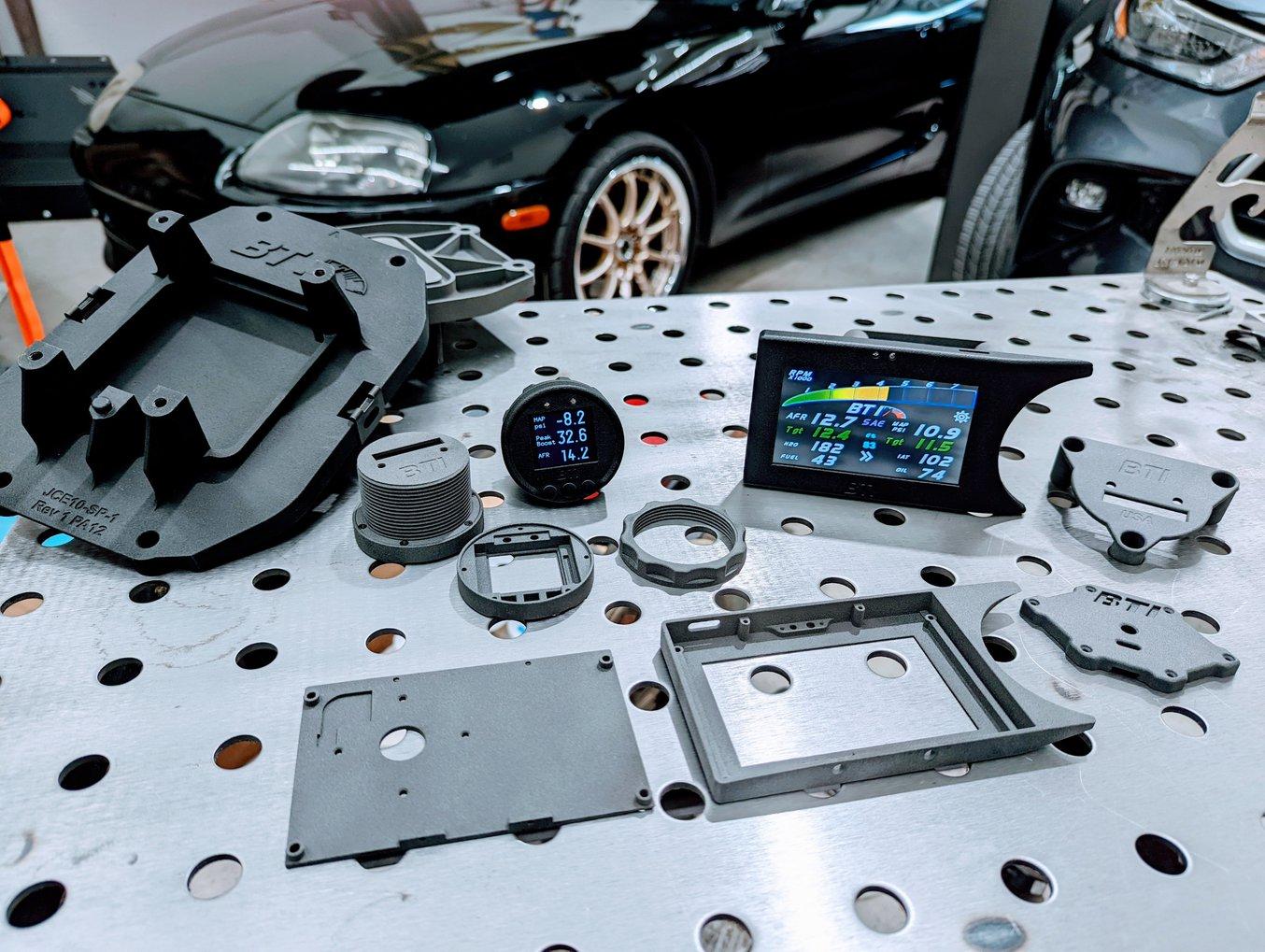
BTI Gauges 专为高性能汽车设计遥测显示器。
和许多成功的企业一样,BTI Gauges 也是从填补市场空白起家的。公司创始人兼所有者 Brandon Talkmitt 正在为他的高性能汽车寻找一种生产遥测显示器的可定制方法。
Talkmitt 曾试图寻找一种包含多种性能指标的仪表,以避免在挡风玻璃上安装多个散乱的屏幕和让人分心的读数,但并未成功。然后,他开始使用 3D 打印机制作仪表外壳的原型并亲自测试,将外壳置于汽车和烤炉内的高温环境中,并修改设计以补充多个汽车模型。
很快,90 年代风格的日本赛车、兰博基尼、道奇蝰蛇和其他高性能汽车的客户群体对他的产品产生了兴趣。
Talkmitt 开始评估其他 3D 打印选项,包括昂贵的塑料粉末床熔融 3D 打印机、树脂 3D 打印机和便宜的紧凑型 SLS 选项。但由于有些产品售价高达 50 万美元,而从其他供应商处购买材料的过程又很复杂,他并没有找到任何合适的选择。这种情况一直持续到他遇见 Fuse 1。“当我拿到样品时,我想,‘天哪,如果我的部件能像这样就好了。’ 所以我进行了一些测试,想了解它的耐高温性能。我们对测试件进行了后处理和上色,而各方面的表现都很完美,”Talkmitt 说。
在供应链问题一直持续的两年间,BTI Gauges 的触摸屏显示器和九条产品线所需的其他部件都出现过短缺。通过购置 Fuse 1 将 3D 打印引入内部后,他能够立即转向新的设计,而不必花费数千美元购买新模具,或是费心处理现已过时的积压产品。
“我原本会被那些塑料困住,但有了 Fuse 1 以后,我迅速地改变了这种局面。更改文件只需要 30 分钟。如果没有 Fuse 1,我现在肯定还在原地踏步,”Talkmitt 说。
通过我们关于 BTI Gauges 的完整故事,了解更多生产成品售后部件的信息。
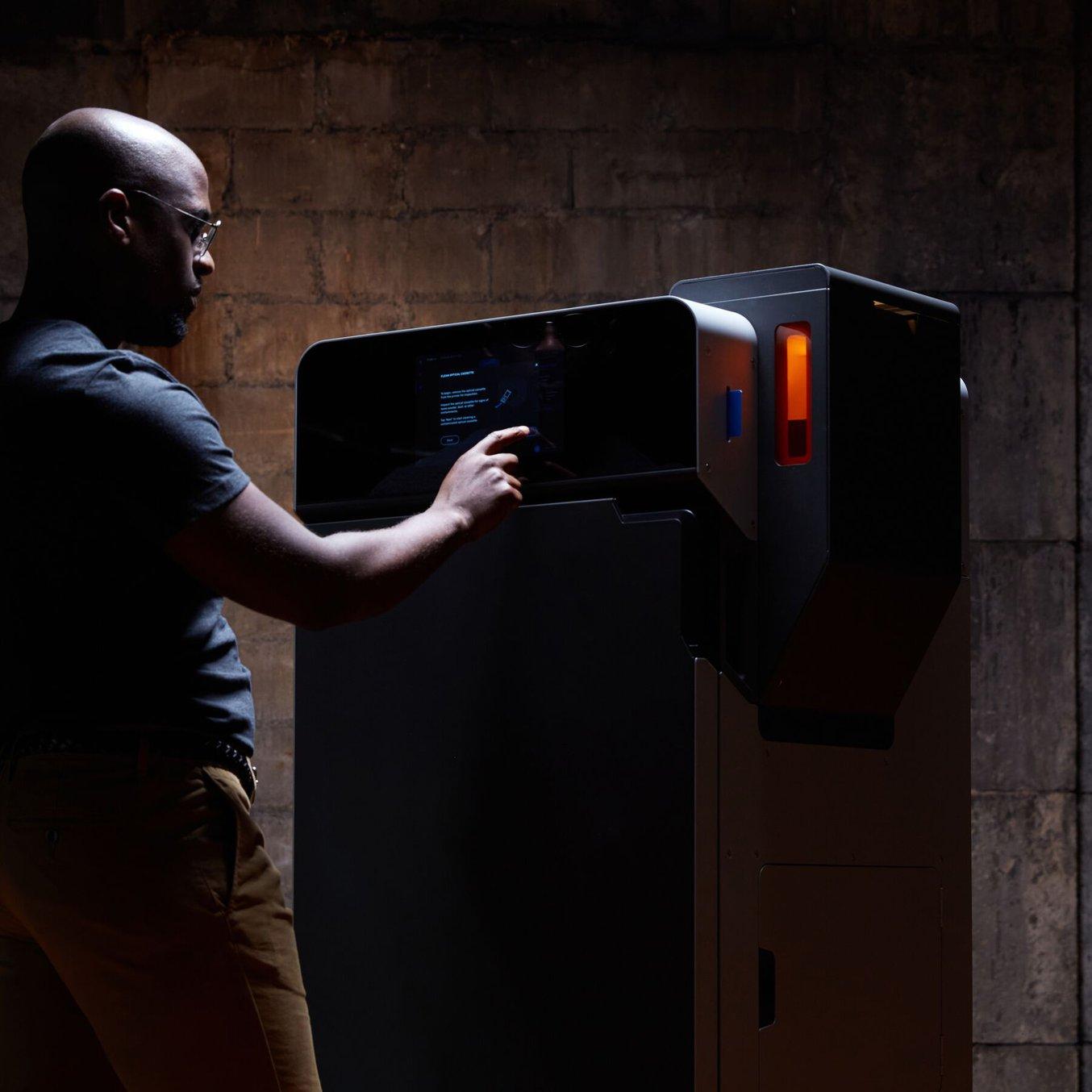
3D 打印在赛车和摩托车中的应用
3D 打印是一种无需工具的制造工艺,是赛车运动的完美搭档,也是可助您快速、经济地实现小批量生产和定制制造的强大工具。通过消除加工时间和成本,3D 打印能够帮助您灵活、快速地修改产品并加快上市速度。此外,该技术还能提高设计自由度,提供定制产品的能力,并在无需额外增加成本的情况下构建复杂形状(如晶格)。
通过使用内部 3D 打印,赛车团队可以加快开发速度、保证 IP 安全、测试更多想法,并最终击败他们的竞争对手。
7. 使用 3D 打印迭代设计改进发动机性能
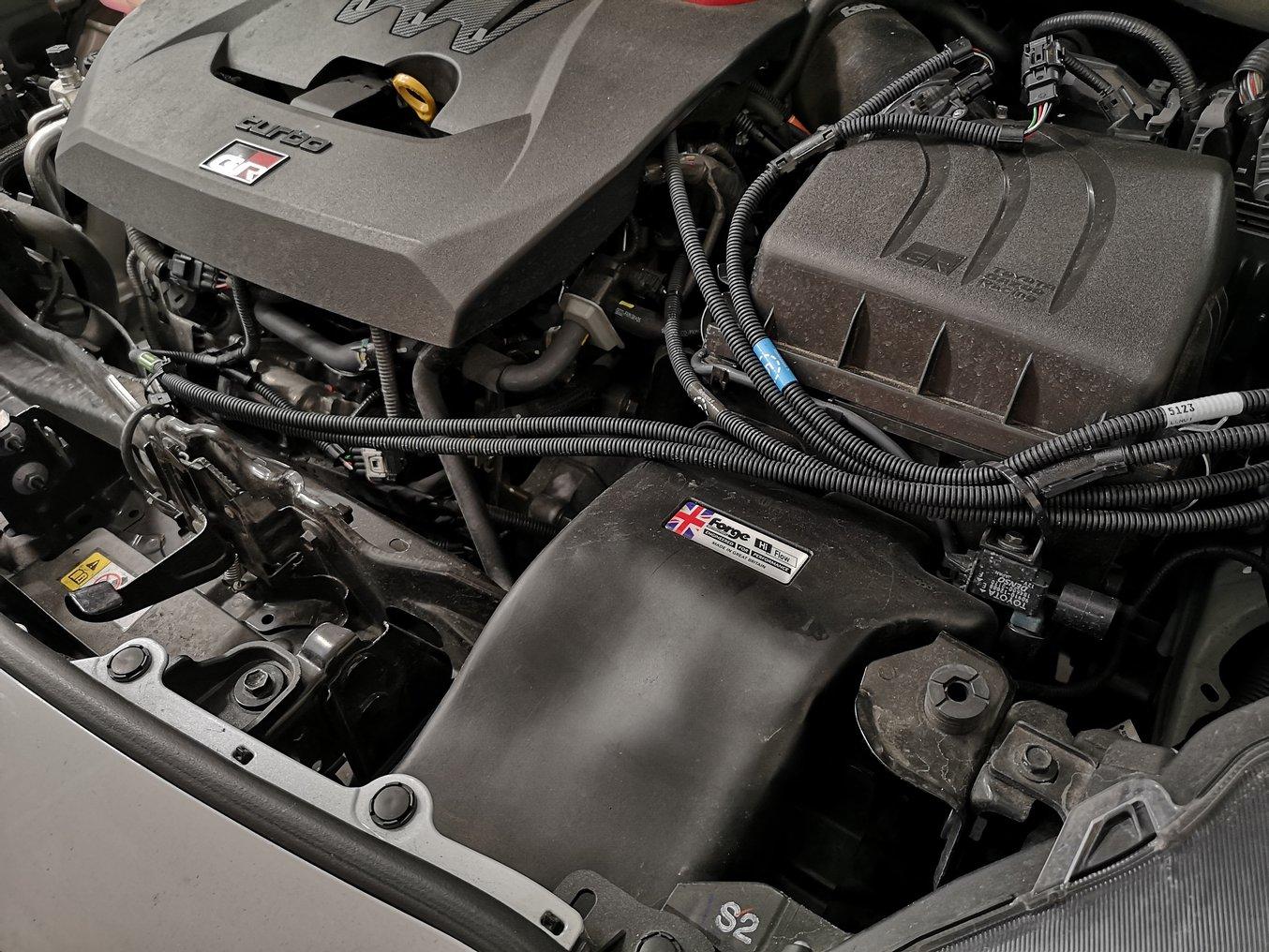
Forge Motorsport 重新设计的管道将进气温度降低了 6°C。
Forge Motorsport 是一家为高性能汽车制造售后配件的公司,他们使用 3D 打印技术来制作部件原型。在 Toyota Yaris GR 发布时,Forge 的工程师就看到了改进进气管道设计的可能性——即移动气箱的开口,增加部件的整体尺寸;此举将在减少进气温度 (IAT) 波动(导致发动机性能难以预测)的同时,降低整体平均温度。
他们使用 3D 扫描对 OEM 部件进行了逆向设计,并在能够模拟气流的 SOLIDWORKS 中进行了虚拟设计更改。在设计出可行的 3D 模型后,他们就使用可快速打印的 Draft Resin 制作原型,用以确认气箱开口的新位置能否按预期运行,同时保证部件整体尺寸的增加不会干扰其他组件或电缆。在确认了基本配合后,他们使用 Tough 1500 Resin(一种坚固的抗冲击材料)重新打印了部件,并将其涂成黑色,使其变得与最终部件相似,然后交给客户进行测试。
客户将 3D 打印部件在 Yaris GR 中使用了五个月,期间他收集了不同条件下的性能数据,包括赛道和上坡行驶数据。库存部件的 IAT 在 42-45°C 之间变化,并在比赛过程中出现了大幅变化;而对于经过重新设计并使用 Tough 1500 Resin 打印出来的部件,相关客户测量结果显示其 IAT 介于 35-36°C 之间。和预期一样,重新设计的部件具有较低的整体 IAT,温度波动也有所减小。有了这些数据,Forge 相信他们的部件是 OEM 设计的改进版本,并继续使用碳纤维制造最终的生产部件。
有关使用 3D 扫描的逆向工程工作流程的更多信息,请观看我们与 Forge Motorsport 和 Peel3D 的网络研讨会。
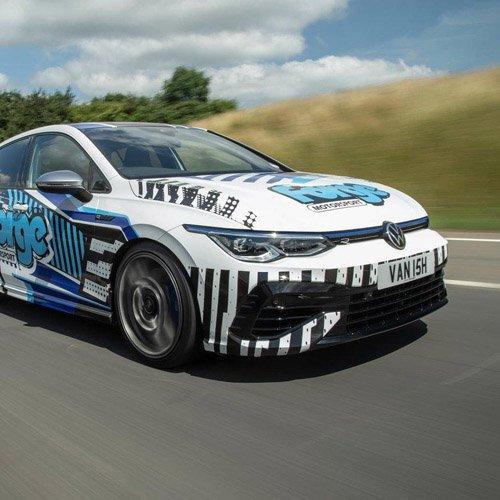
汽车行业中的 3D 扫描和 3D 打印应用:Forge Motorsport
在这次由 Formlabs、Solid Print3D 和 peel 3d 为您带来的网络研讨会中,我们将与 专门为汽车售后市场制造阀门、中间冷却器和执行器等性能升级产品的 Forge Motorsport 展开交流。
8. 方程式赛车中的碳纤维成型工艺和 3D 打印成品部件
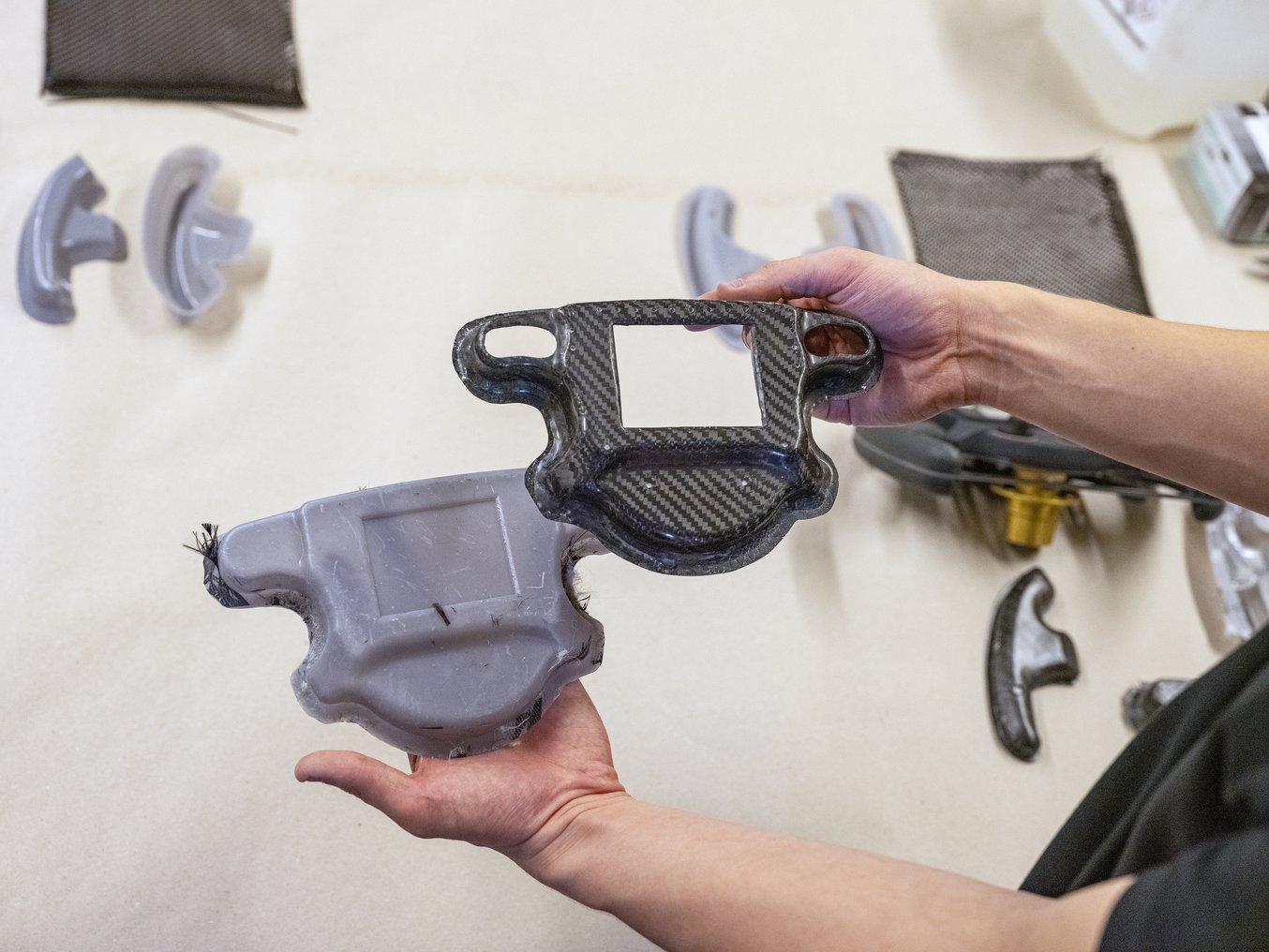
通过内部 3D 打印模具,柏林工业大学的赛车团队得以大幅降低碳纤维部件的成本和周转时间。
大学生方程式是一年一度的工程设计比赛,来自世界各地的学生团队会打造方程式风格的赛车并进行竞速。柏林工业大学方程式团队 (FaSTTUBe) 是该项赛事中最大的团队之一;自 2005 年来,每年都会有 80 到 90 名学生参与开发新的赛车。该团队在他们的成套工具中添加了一台 Form 3 SLA 3D 打印机,这样可以节省时间、降低成本并以不同方式制造任何可能非常昂贵的碳纤维部件。
在设计方向盘底盘等关键部件时,复合材料的 3D 打印模具为团队提供了更大的灵活性、缩短了周转时间,并节省了成本。如需加工该部件的模具,必须采购昂贵的专用工具方可进行,而外包成型部件则需要数周时间,且成本接近 1000 欧元。而在内部采用 3D 打印制作模具并手工层压,只需付出 10 欧元的材料成本和 1.5 小时的工作时间即可。
该团队还使用 3D 打印来制造设计原型、轻量级部件甚至制造成品部件。有关这些应用的详细信息,请阅读我们的客户故事。
3D 打印为 FaSTTUBe 团队提供了灵活性、设计自由度和并节约了成本。此外,学生还获得了为他们的项目制造原型、模具甚至成品部件的经验。他们在步入职场后还可以充分利用这些技能,为每个工程学科继续积累宝贵经验。
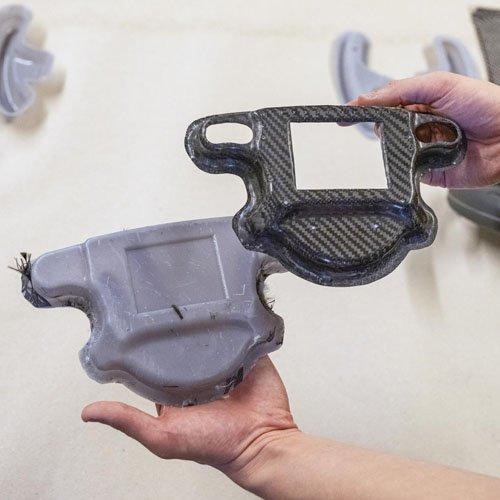
9. 3D 打印备用发动机部件
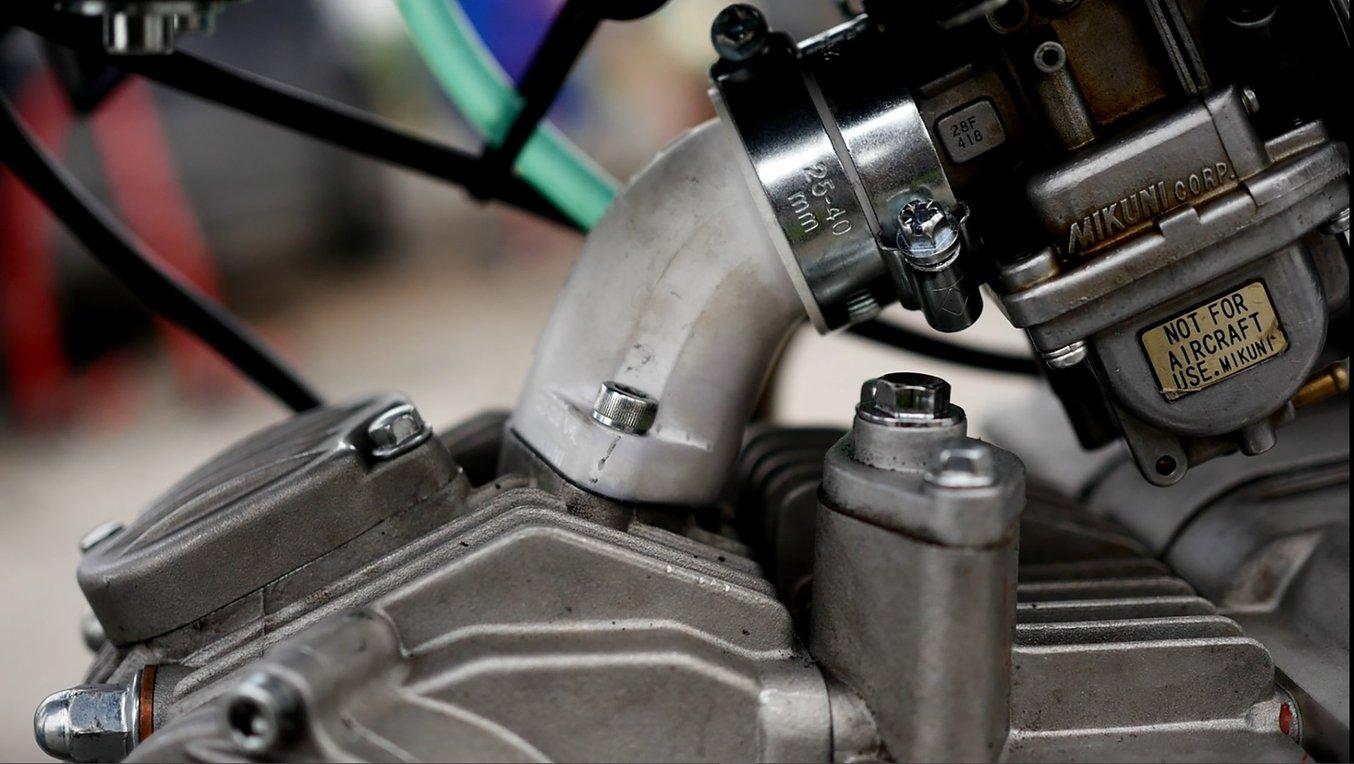
采用 Rigid 10K Resin 打印的进气歧管,在比赛结束后,其温度低于原来的铝制部件。
Andrea Pirazzini 从 2012 年开始骑摩托车。他想挑战自己,为自己的摩托车设计和制造一个功能齐全且足够安全的 3D 打印进气歧管。过去,他曾尝试使用 FDM 打印技术,但结果并不理想,因为该部件密封性不足,影响了发动机的功能。
为了开发该项目,Pirazzini 使用 3D 扫描和 Autodesk Fusion 360 软件对设计进行逆向工程。对四冲程发动机(双气门)及其框架和化油器的扫描帮助他正确确认了歧管的尺寸,然后将其定位至最佳位置。通过使用 CAD 软件,可以将头部入口的直径与化油器对齐,避免任何压降或湍流。
新的歧管设计是通过 Form 3 使用 Rigid 10K Resin 以 100 微米的层高打印而成的,从而形成了无可见层线的光滑表面。至于饰面,Pirazzini 使用经典的水性砂纸打磨表面。与必须在外部和内部进行防水处理的 FDM 歧管不同,SLA 打印可创建坚固且防水的部件。
Pirazzini 使用 Form 3 打印的歧管完美地经受住了高温和低温的考验,现在仍然安装在他的越野车上。由于使用了热成像摄像机,Pirazzini 发现 Rigid 10K Resin 还可提供明显提升的热性能:与传统的铝制歧管相比,带有散热片的 3D 打印歧管的温度降低了40-50 摄氏度。此外,在约 33 摄氏度的室外温度下,经过大约 20-25 分钟的比赛后,触摸歧管也不会被烧伤。
不仅这个项目大获成功,而且发动机的性能也得到了改进。得益于 Pirazzini 对原始设计的一些改进,与标准加工歧管相比,该发动机具有更大的马力(大约 1HP,几乎增加了 10%),同时仍处于锦标赛规则所规定的范围内。
通过我们的详细案例研究,了解更多关于 Pirazzini 如何开发该项目的信息。
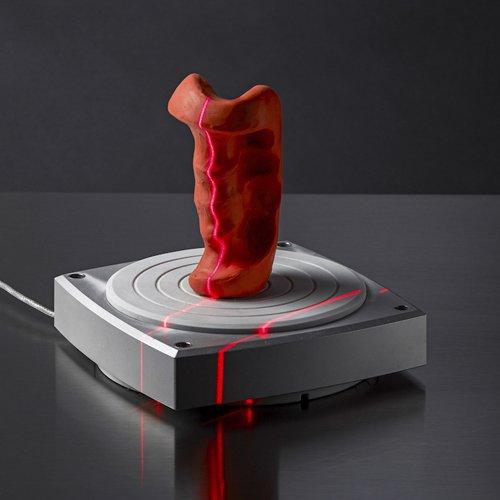
补充:3D 打印汽车
在 21 世纪 10 年代早期出现的 3D 打印热潮中,大众媒体对采用 3D 打印制造大型复杂组件(包括整个 3D 打印汽车)的兴奋之感与日俱增。然而,即使是“完全”3D 打印汽车最狂热的支持者,也将打印的重点从发动机或其他机电组件转移到了底盘、车身和座椅等结构和装饰部件上。
包括 Local Motors 和 EDAG 在内的一些公司制造了全概念车,其底盘和车身均采用 3D 打印制作,并在 21 世纪 10 年代中期的 SEMA 等贸易活动上向公众展示。然而,这些项目都没有实现量产。
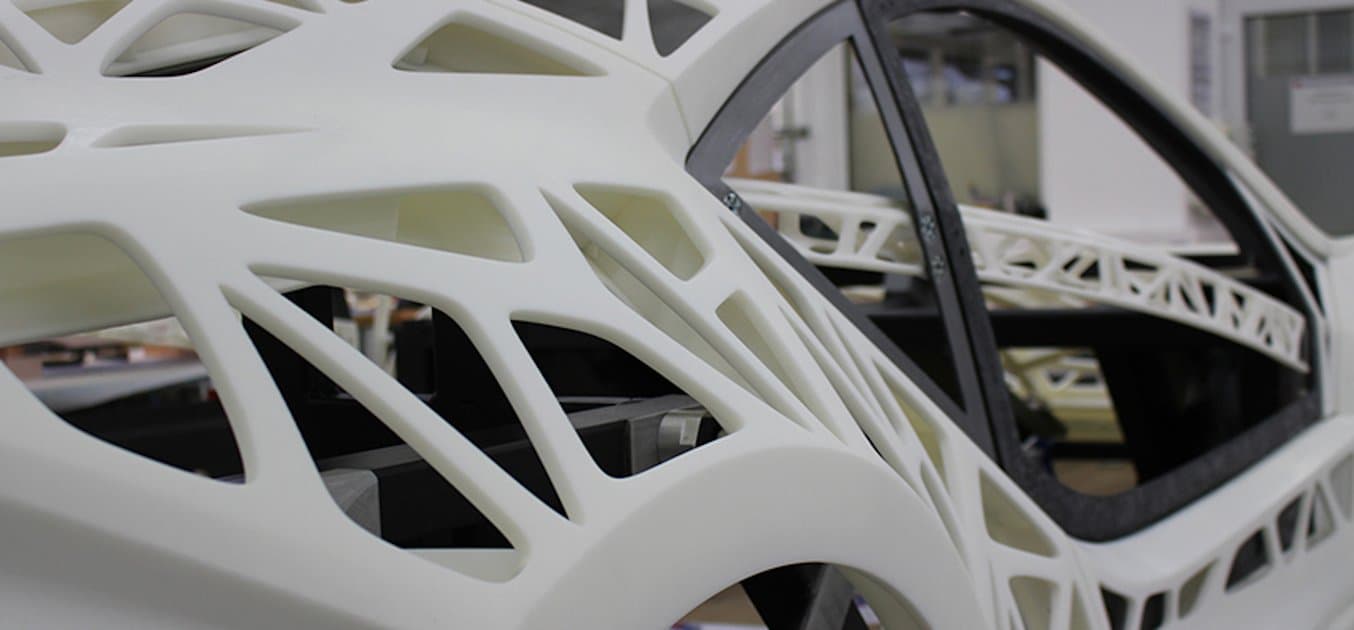
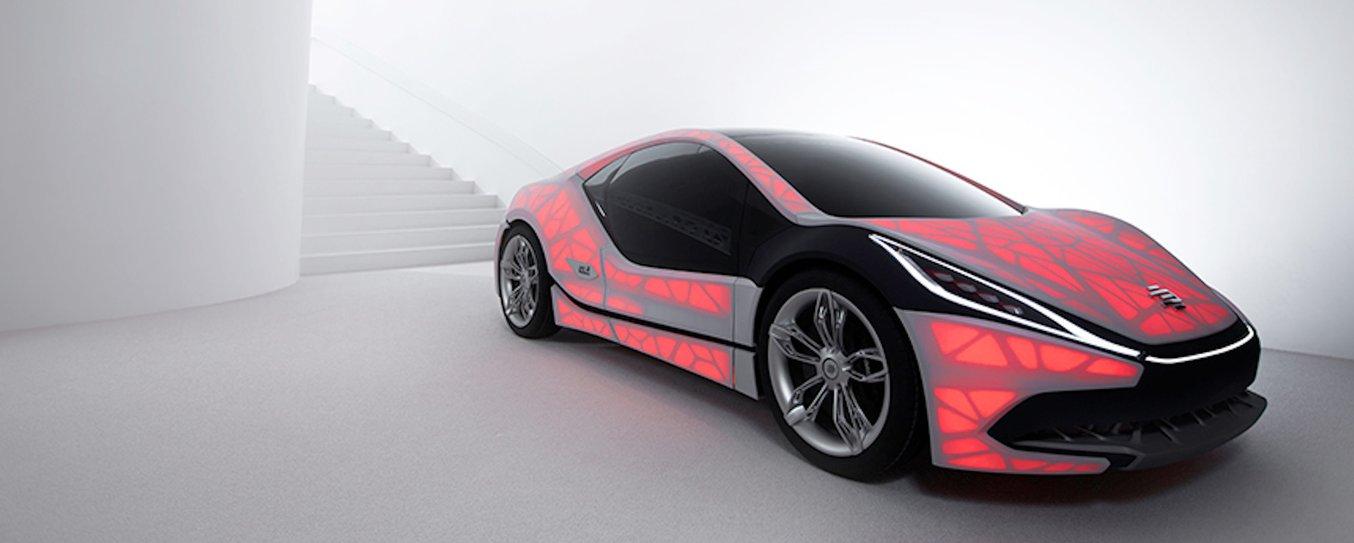
除了耐气候性之外,EDAG Light Cocoon 的车身外壳也为设计和个性化方面提供了绝对的自由度。(来源:EDAG)
目前,最接近量产的公司似乎是 Divergent 3D 和 XEV。
Divergent 3D 将衍生式设计与 3D 打印进行了结合,可为汽车部件制造商量身定制组件。完成组件设计后,该公司就会使用金属 3D 打印机进行制造。他们的第一个公开项目是 Czinger 21C 超级跑车,同时他们也是阿斯顿马丁等主要 OEM 的供应商。
另一方面,由意大利公司 XEV 开发的 YoYo 可能成为了第一款面向大众市场的 3D 打印电动汽车,目前该产品已开始向客户交付。除了底盘、座椅和挡风玻璃之外,YoYo 的所有可见部件也都采用了 3D 打印进行制作。由于 3D 打印技术的广泛应用,该公司已经成功地将组件数量从 2000 个减少到 57 个,从而实现了重量仅为 450 公斤的轻量化设计。
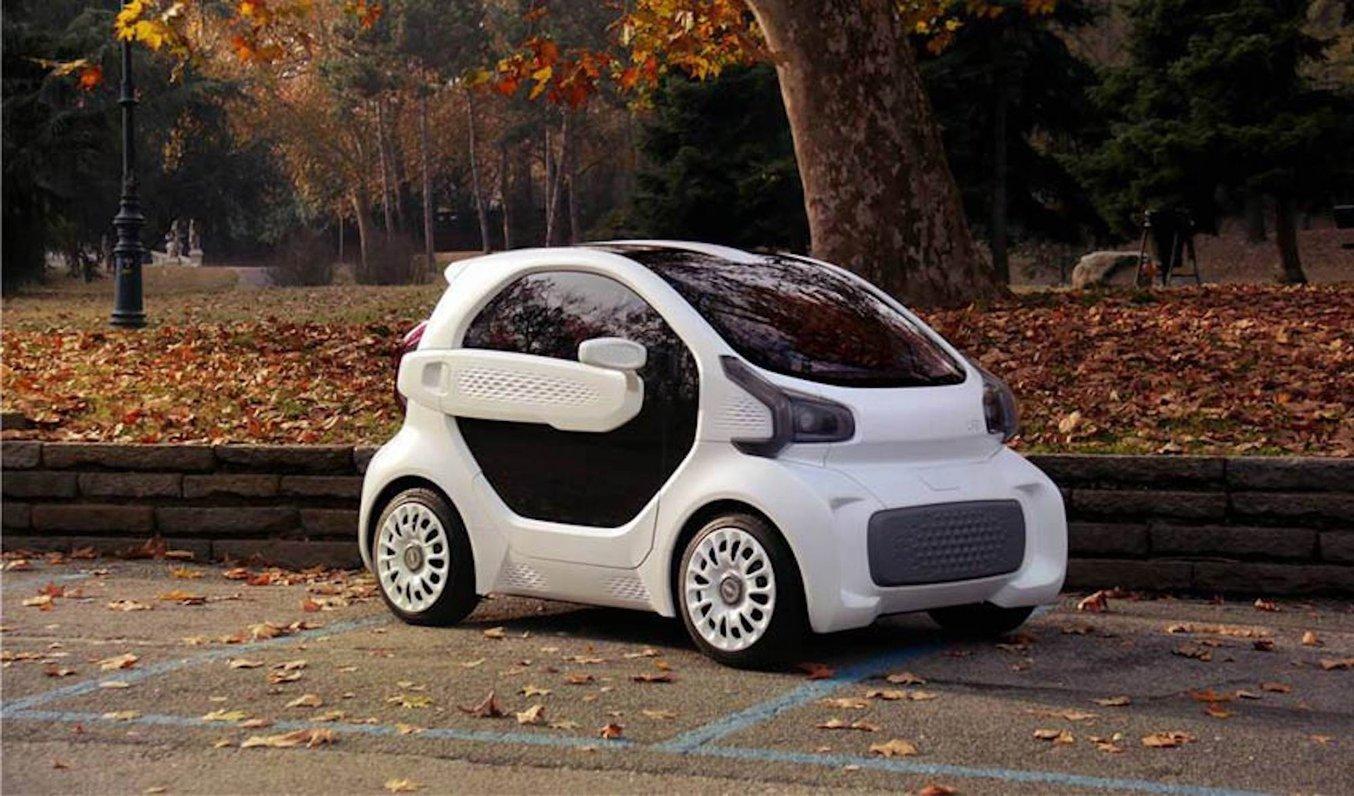
YoYo 是第一辆面向大众市场的 3D 打印电动汽车。
进一步了解汽车领域的 3D 打印应用
正如上述示例所示,经反复证明,3D 打印技术不仅能够创造性地缩短上市时间和提高车辆性能,而且可以为供应商、OEM 和消费者提供明显优势。在某些方面,3D 打印技术正在突破现有技术的瓶颈,从而为设计和生产带来全新的可能性。而在其他领域,这项技术也可以降低生产成本并节省时间。
随着整个行业对 3D 打印的价值和实际情况的理解不断加深,且技术和可用材料基础日益多样化,增材技术将继续重塑我们在世界各地设计、制造和维护车辆的方式。