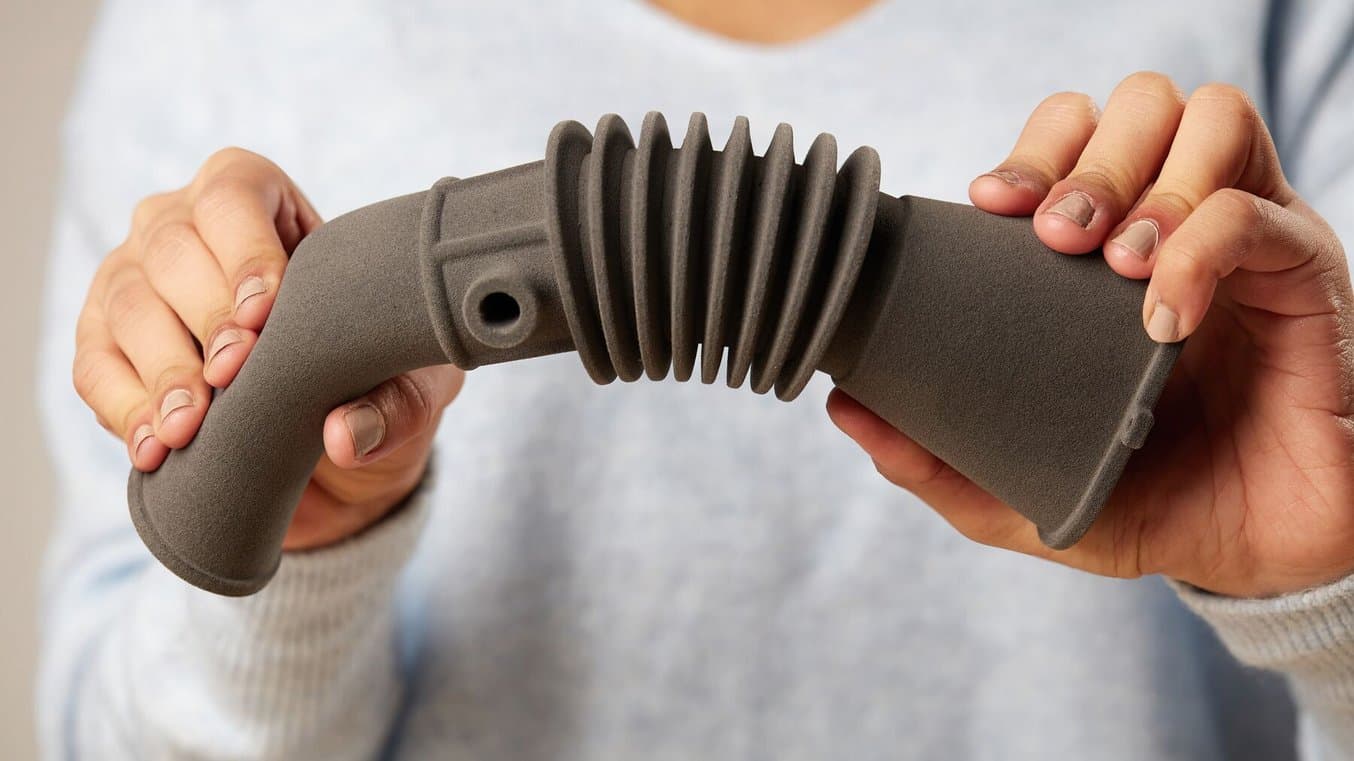
什么是 TPU?
如何制造 TPU 部件?
在我们的日常生活中,TPU 产品无处不在,热门程度使其成为大规模生产的理想选择,这种材料的最常见制造方式是采用传统注射成型工艺。许多我们以为的橡胶制品实际上均由 TPU 制成。
注射成型是一种具有成本效益的大批量部件生产方式,但在几何灵活性或定制化方面存在局限性。注射成型部件均实现标准化生产,生产量从数十万到数百万不等,因此对于医疗器械制造或体育用品等行业来说,需要更适合小批量生产或定制化的替代选择。
因为小型企业和初创公司需要依赖大型工业注射商进行外部生产,批量生产也不利于他们将产品快速推向市场。
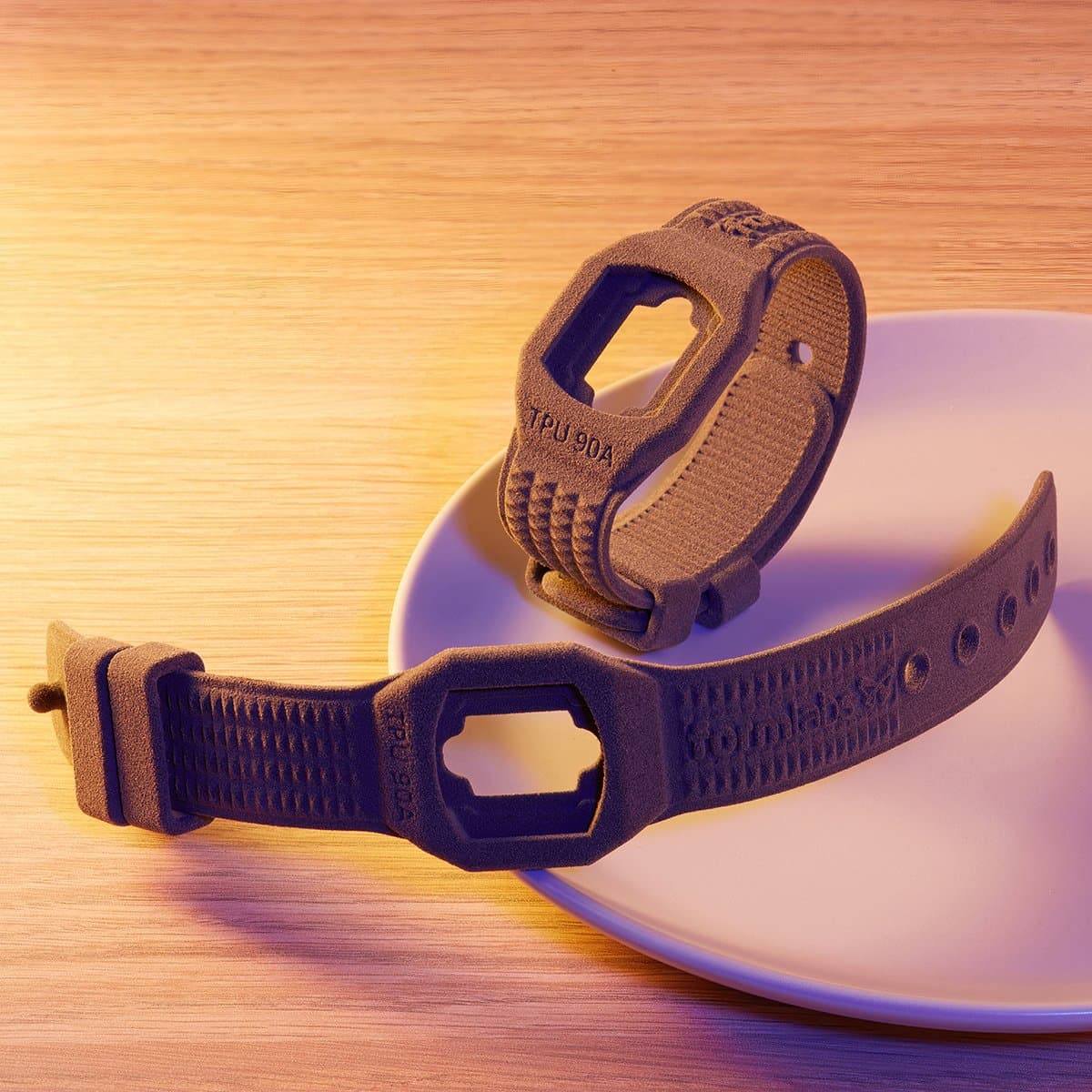
TPU 90A Powder 上市:制造可安全接触皮肤的柔韧 SLS 部件
观看我们的网络研讨会,了解 TPU 90A Powder 如何帮助您使用 Fuse 系列 3D 打印机制造柔软的橡胶部件。
为什么将 TPU 用于 3D 打印?
对于具有更高几何复杂性的部件、个性化或定制化设计、更快速的迭代和设计以及更具成本效益的小批量生产而言,3D 打印 TPU 和 TPE 材料提供了传统工作流程以外的选择。
TPU 3D 打印有多种选择,包括熔融沉积成型 (Fused Deposition Modeling, FDM) 和选择性激光烧结 (Selective Laser Sintering, SLS) 技术。随着 3D 打印技术和材料的不断发展,将此技术纳入其工艺流程的制造商数量成倍增长。
TPU 3D 打印可缩短快速原型制造应用的迭代周期,并为成品部件生产提供定制可能性。传统上,一些行业会将产品开发流程的某阶段(通常是批量生产制造阶段)外包,而 3D 打印技术可以改进并垂直整合端到端工作流程。
3D 打印 TPU 还能帮助制造商满足定制和个性化产品的需求。Deloitte 的一项研究表明,在某些类别中,超过 50% 的消费者表示有兴趣购买定制产品或服务,其中大多数人愿意为定制产品或服务支付更多费用。对于通常使用 TPU 和橡胶的应用领域(如头盔或矫形器和鞋垫等防护装备),3D 打印 TPU 部件适用于大规模定制头盔衬垫、矫形器、运动器材、护目镜、耳机或科技产品中符合人体工学的抓握组件。
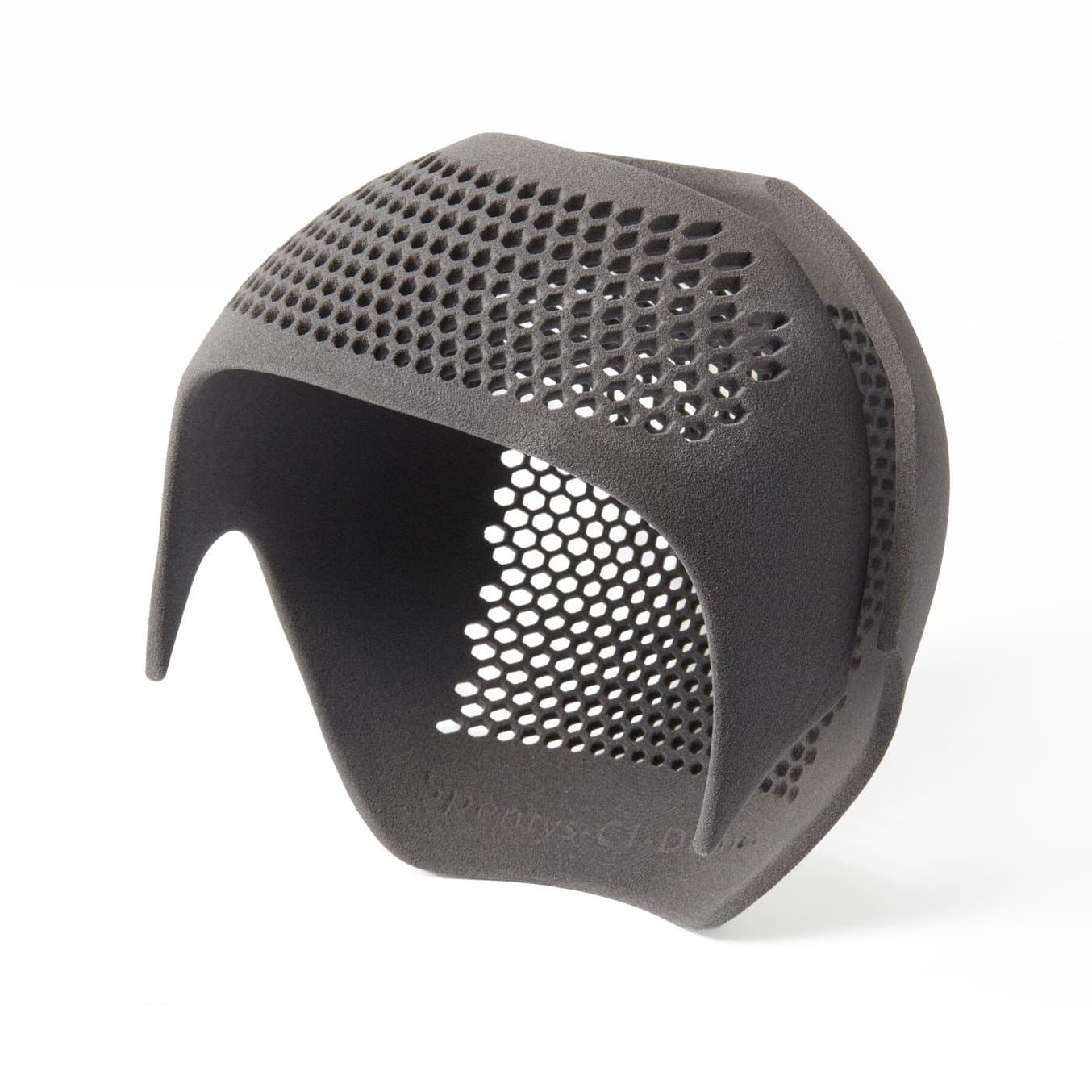
Formlabs 的 TPU 90A Powder 可以根据人体测量数据进行定制,适用于此个性化的保护性头部覆盖物等应用。
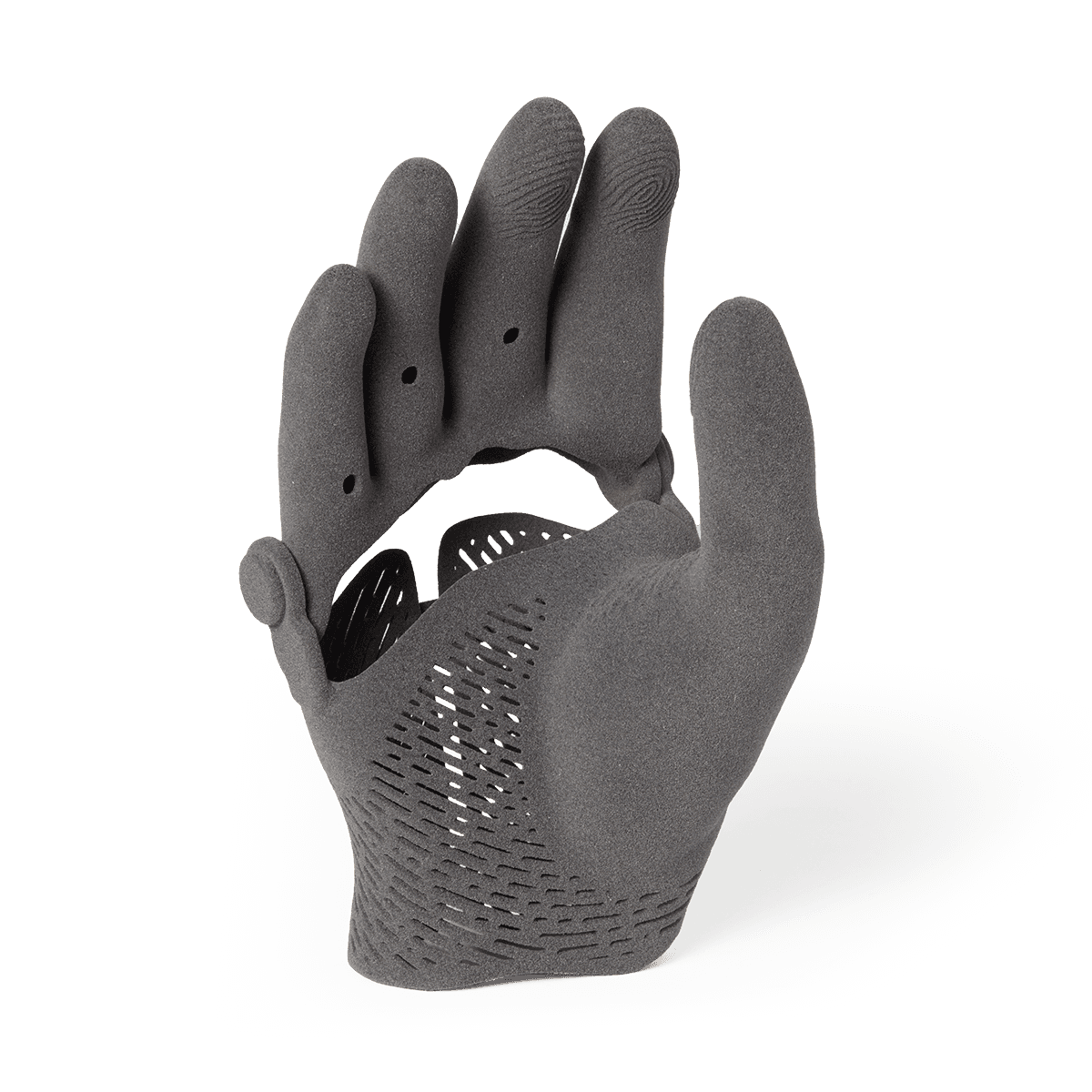
此由 TPU 90A Powder 打印的义肢手套具有柔韧性、强度和耐用性。
如何使用 TPU 进行 3D 打印
TPU 可用于在 FDM 或 SLS 3D 打印机上进行 3D 打印。每种技术都有其独特的优势,在做出选择之前,重要的是要确定哪种技术最适合自有工作流程和业务需求。
FDM TPU 3D 打印技术 | SLS TPU 3D 打印技术 | |
---|---|---|
功能材料强度 | ★★☆☆☆ | ★★★★★ |
分辨率 | ★★☆☆☆ | ★★★★☆ |
精确度 | ★★★★☆ | ★★★★★ |
表面光洁度 | ★★☆☆☆ | ★★★★☆ |
产量 | ★★☆☆☆ | ★★★★★ |
设计复杂度 | ★★☆☆☆ | ★★★★★ |
简单易用 | ★★★★★ | ★★★★☆ |
优点 | 低成本消费级机器和材料 轻松快速制造简单小型部件 | 功能性、坚固、各向同性部件 生产级产量 自支撑设计 优异的设计自由度 |
缺点 | 部件为各向异性,不防水或功能不够强大 设计自由度有限 | 表面略微粗糙 |
应用 | 低成本快速原型制造 基本的概念验证模型 | 功能性原型制造 小批量生产成品部件:汽车垫片、密封件、歧管、消费品、鞋、义肢和矫形器 |
将 TPU 用于 FDM 3D 打印技术
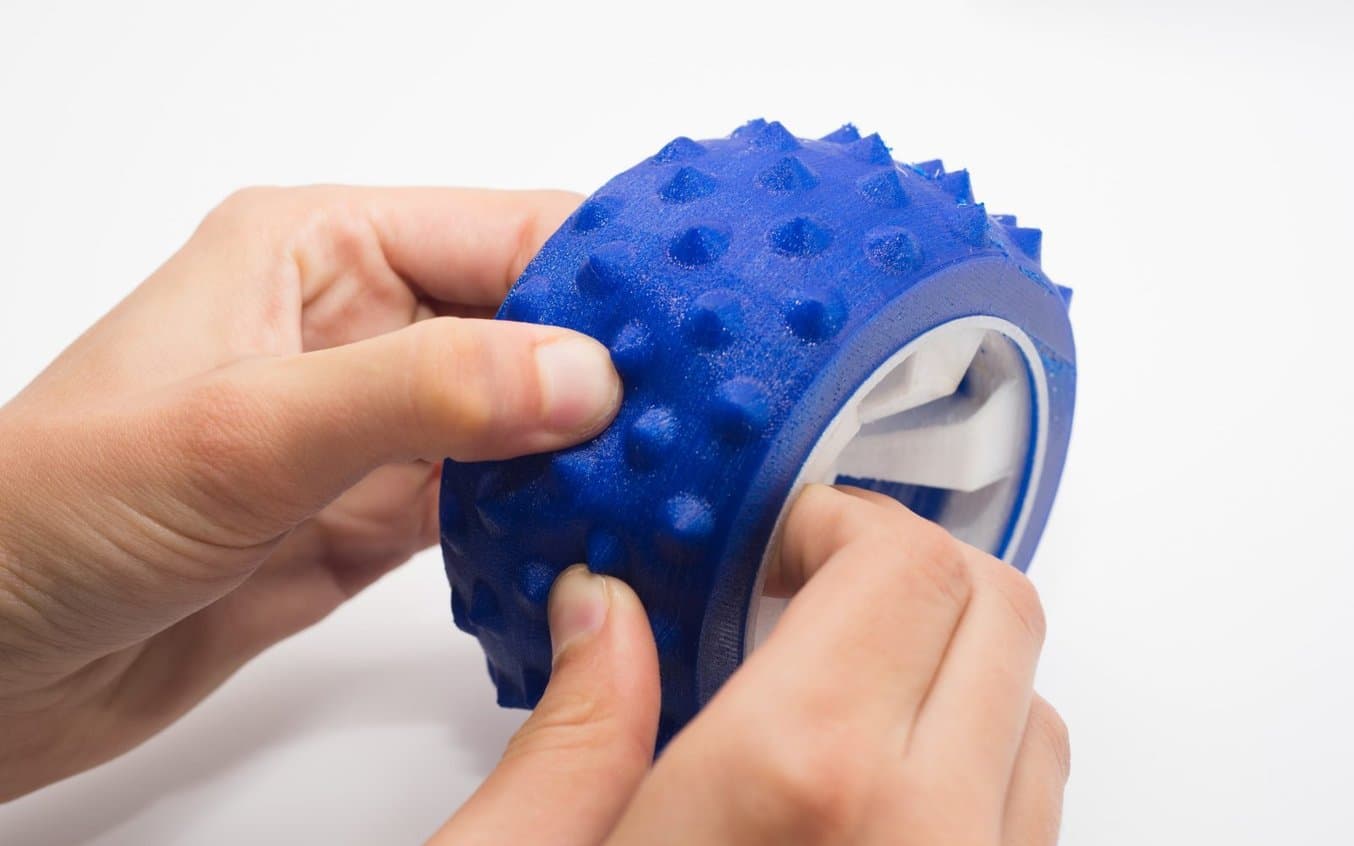
在 FDM 打印机上进行 TPU 3D 打印是个不错的入门级选择,但这种材料的 3D 打印过程颇具挑战性,而且在设计上也存在局限性。(图片来源:Hubs)
对于希望开始 3D 打印 TPU 的企业来说,低成本的 FDM 打印机是入门级工作流程的合适选择。价格低廉的 FDM TPU 长丝是证明设计概念和外观性原型的理想选择,尤其是在最终目标是通过传统注射成型方法进行批量生产的情况下。
然而,在 FDM 打印机中使用 TPU 进行 3D 打印可能并不简单,因为这种柔软而有弹性的长丝很容易使挤出机堵塞,从而导致技术问题和降低打印成功率。在 FDM 打印机中使用 TPU 进行 3D 打印还存在设计自由度有限、部件尺寸精度较低和层线明显等问题。
FDM 打印的 TPU 部件为各向异性,这意味着它们在不同轴或应力平面上的强度并不相同,换言之,从不同方向对 FDM 打印的 TPU 部件施力的效果是不同的。对于经常需要牵引、拉伸、压缩和扭曲的 TPU 部件来说,这种各向异性对任何需要功能性的部件都构成了真正的挑战,即使在原型制造阶段也是如此。
用于 FDM 打印机的 TPU 长丝
许多 FDM 打印机和材料制造商都提供具有不同材料特性的 TPU 长丝。FDM TPU 长丝通常均为较硬的弹性材料,邵氏硬度约为 95A,但这可以通过微调打印参数或设计来调整。
将 TPU 用于 SLS 3D 打印技术
SLS 3D 打印技术非常适合产量较高和功能性较强的应用,例如用于测试的功能性原型或小批量生产可定制的成品,如矫形器、头盔衬垫和可穿戴设备。SLS 3D 打印用户可以利用 TPU 的优异强度和柔韧性,更快地将产品推向市场或改善患者护理。高撕裂强度可制造出坚固、耐用的弹性部件,而立式 SLS 系统(如 Fuse 系列)的易用性可实现低单件成本。此外,由于刷新率低,不仅提高了粉末使用效率,还减少了新材料的支出,从而增强了系统的经济性和可扩展性。
SLS 3D 打印 TPU 部件非常适合需要复杂几何形状或有助于提高性能的应用。SLS 技术的自支撑特性意味着在打印过程中无需支撑结构,因此可以实现带有内部通道、晶格或流形风琴结构的复杂几何形状。在防护性头饰或鞋垫和矫形器等应用中,橡胶晶格结构具有高抗压强度,可以提高产品的功效。
用于 SLS 打印机的 TPU 材料
有多种选择性激光烧结 (SLS) 系统可使用 TPU 粉末材料。其中许多系统都是大型工业设备,具有复杂的基础设施要求,如通风系统、占地面积大或多种电路和电气要求。随着 Formlabs 公司推出 Fuse 系列等更易于使用的 SLS 系统,在粉末床系统上使用 TPU 进行 3D 打印变得更加容易和实惠。
Formlabs 的 TPU 90A Powder 可安全接触皮肤,这为可穿戴设备和医疗器械领域带来了全新机遇,因为这些领域的安全法规限制了许多 3D 打印部件的使用。借助 TPU 90A Powder,工程师和设计师就可以在一个工作流程中利用 3D 打印的设计自由度、橡胶的高抗撕裂强度和伸长率以及许多传统模塑热塑性塑料的安全接触皮肤特性。
使用 Formlabs 的 TPU 90A Powder 和 Fuse 系列 SLS 3D 打印机打印 TPU 非常简单,可以轻松集成到现有的 SLS 工作流程中,或者作为入门的首款 SLS 材料。该材料可以在空气环境中打印,无需使用惰性气体,这与其他一些 SLS 材料不同。
此外,在 Fuse 系列打印机中打印的 TPU 部件不使用 Surface Armor(在更坚硬的粉末中围绕部件形成的半烧结外壳),因此使用 Fuse Sift 后处理机器可轻松完成脱粉过程。虽然 TPU 90A Powder 部件不含 Surface Armor,但仍建议使用介质喷砂处理来清除部件上所有多余的粉末,从而获得更加整洁和更易于使用的部件。尽管 Formlabs 建议使用专用的 Fuse Sift 和成型室,但将现有 Fuse 系列打印机切换到使用 TPU 90A Powder 绝对可行。
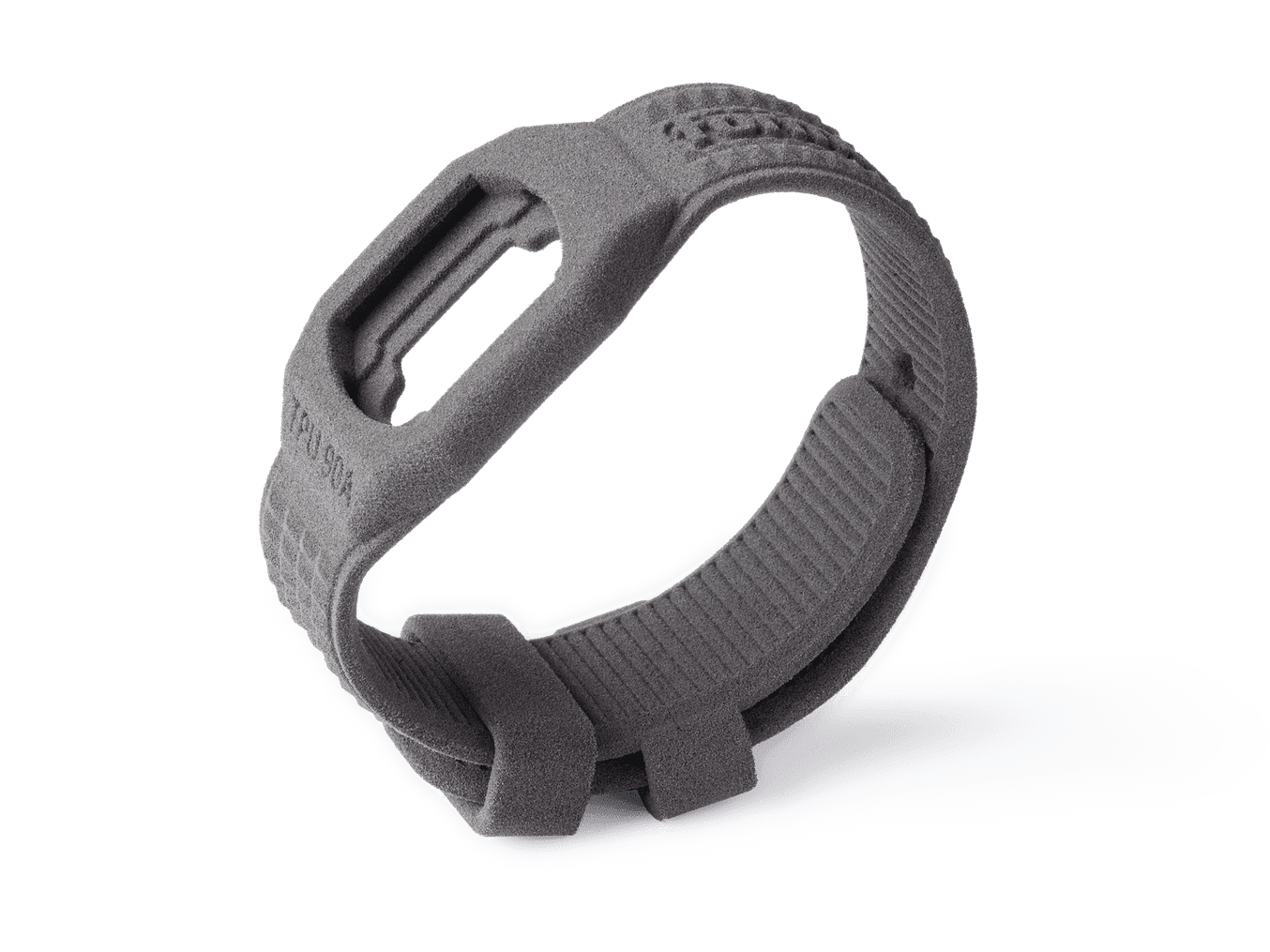
TPU 3D 打印应用
TPU 部件的传统制造工作流程久经验证,且仍然是批量生产橡胶产品的理想选择。然而,在许多情况下,3D 打印 TPU 都是一种很好的替代方案,包括满足速度或易用性需求、快速原型制造、按需制造辅助工具和定制应用。从需要快速制造原型的设计流程开始,到成品部件的最终设计,甚至是大规模定制消费品,3D 打印 TPU 都能在不牺牲机械性能或保真度的情况下,提高工作流程的速度和效率。
快速原型制造
使用 TPU 进行 3D 打印,广大企业能够在内部进行原型制造、缩短周转时间,并减少以前支付给服务机构或机械车间的费用。
例如,如需制作运动头盔的原型,则应制造坚硬的外壳以及内部柔软的缓冲衬垫。广大创新型公司正致力于为这些缓冲衬垫设计新的晶格结构和冲击抵消技术,而 TPU 恰好是一种完美的材料。
然而,尝试用传统的制模方法实现新的设计和几何结构不仅成本极其昂贵,且将其外包给设计机构也可能需要花费数周时间。使用一种工作流程和一类技术来制作坚硬的外壳和柔软的内部缓冲衬垫,意味着这些创新者能够以更高的速度进行迭代。这些头盔必须经过大量物理测试,因此每一轮测试将需要用到 10 个缓冲衬垫。如果采用手工方式精心制作衬垫表面,则工作过于繁重;而如果使用传统 TPU 成型,则成本效益较差。正确的解决方法就是在内部采取 3D 打印技术。
Fuse 系列 SLS 3D 打印机可以轻松使用 TPU 90A Powder 打印多个略微不同的橡胶晶格结构,以测试不同的设计。通过改变部件本身的设计(例如改变壁厚),您可以针对不同的应用或测试后的迭代生产不同硬度的部件。
Fuse 系列工作流程支持使用多种机械性能各异的材料,使您在内部进行开发和制造,并利用一种技术来管理众多不同组件类型的设计。搭配使用 TPU 90A Powder 与同样值得信赖的 Fuse 系列平台,通过 3D 打印直接制作原型,打造一种全新的产品类型。
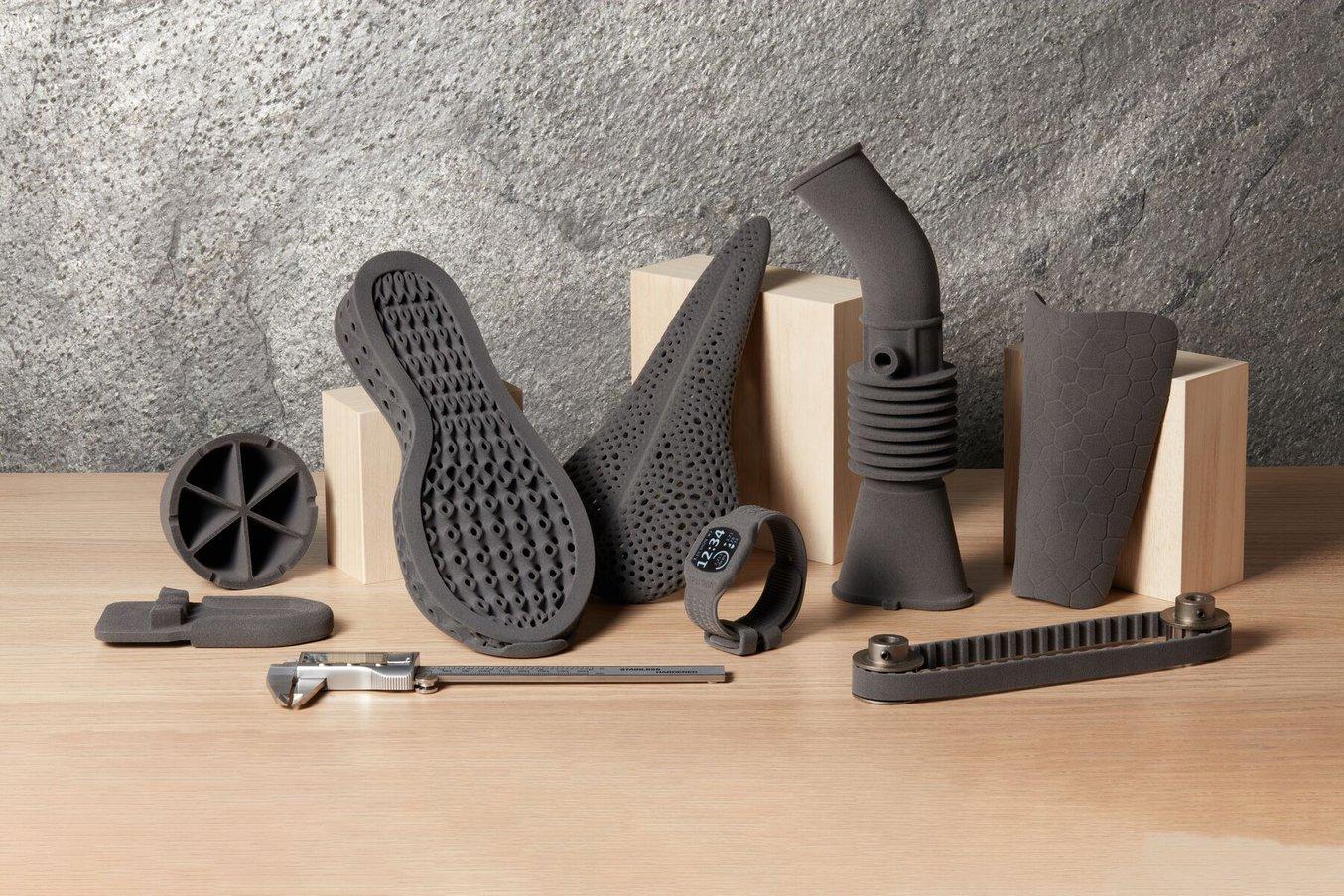
TPU 90A Powder 非常适合用来制造柔韧性部件的功能性原型,如能够安全接触皮肤的可穿戴设备、健身运动装备或鞋垫。
制作辅助工具
除非您是制造行业的内部人士,否则可能无法明确不同制造辅助工具类型间的差异。然而,无论是夹具、支架、外壳,还是其他众多的机器连接方式,最重要的都是它能否及时满足您的迫切需求。许多制造商都面临着一个相同的问题-如何避免其价值数百万美元的制造设备磨损过于严重;而 TPU 就是对该问题的完美回答。
触感柔软的制造辅助工具可以缓冲特定的冲击或是提供形状完美的夹具,从而有助于延长重型机械的使用寿命。一旦密封件或垫圈因多年反复使用而撕裂,操作人员可以立即打印出替代件,在数小时内恢复生产线并重新运行,而无需等待数天或数周才能获得新部件。
增强材料性能对于制造商来说是多重保险,可以保护他们免受意外的部件损坏或机器组件故障的影响。制造商可在内部获取到的机械性能越多,就越能避免供应链延误和 OEM 导致的高额维修成本。凭借橡胶 3D 打印部件,您现在即可按需修复或更换全新的设备部件子集。通过避免工厂生产线或流程中断,每天可以节省下数千美元。
TPU 可用于制作汽车和航空航天测试中的减振器,以及工业过程(如热压成型独特形状的部件)中的夹具。在汽车工厂,大型机器人系统需要运行于必须支持弯曲和旋转的门架上。定制衬垫和柔软外壳可帮助这些机器避免摩擦,从而延长其使用寿命。
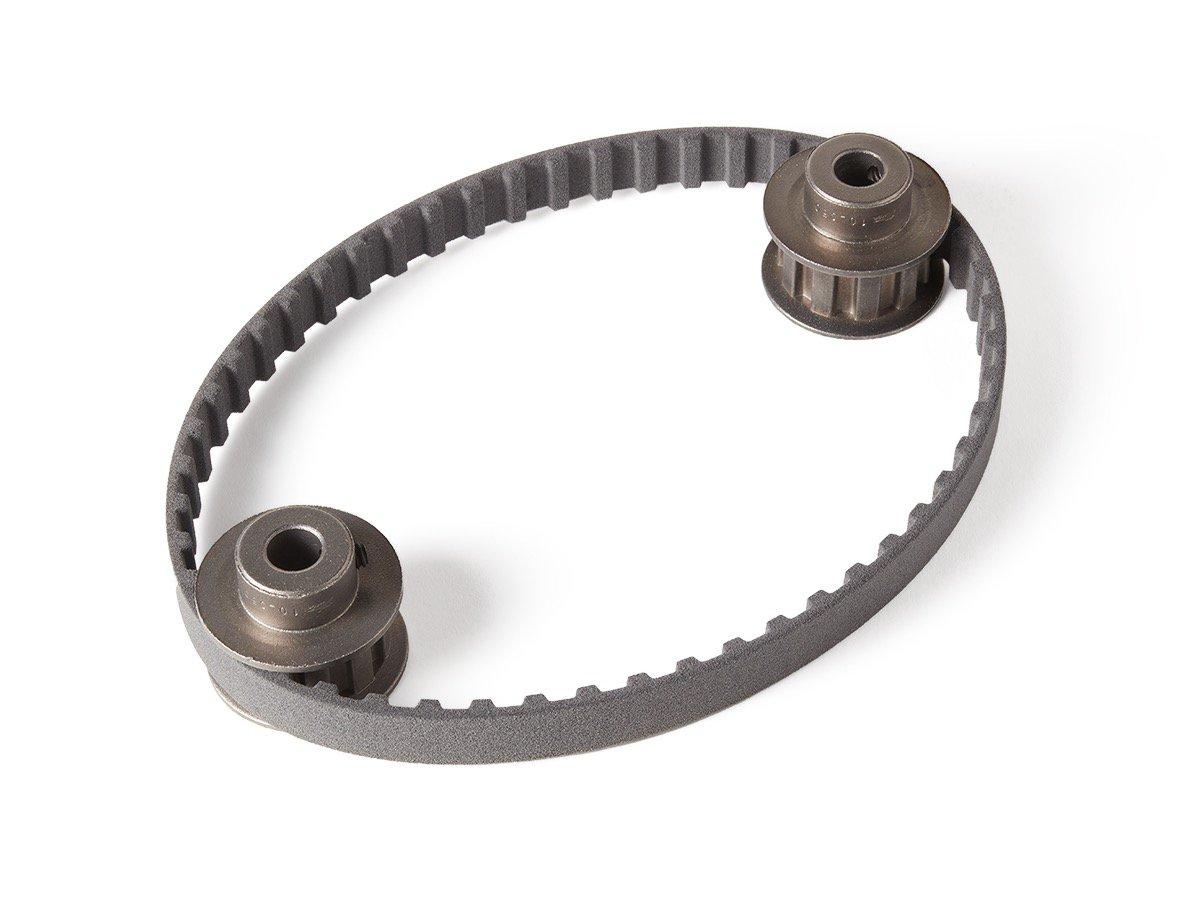
拥有 TPU 材料意味着当天即可设计并打印出柔性替换件和制造辅助工具,从而实现不间断生产。
小批量和定制可穿戴产品
在运动、时尚和可穿戴技术行业,提供个性化选项对于希望获得更多市场份额的品牌来说必不可少。高昂的模具制作相关成本使得小批量或一次性生产难以实现,而日益普及的 3D 打印则为其带来了新的可能性。
尽管如此,大多数 3D 打印材料仍因为过于坚硬而导致并不适合体育用品或可穿戴市场,这种情况一直持续到 TPU 上市为止。从可以根据个人的确切脚印和重量分布来定制的鞋底,到为了抵消冲击而设计的橄榄球头盔,再到为手腕量身定制的表带,该材料蕴含着无限可能性。
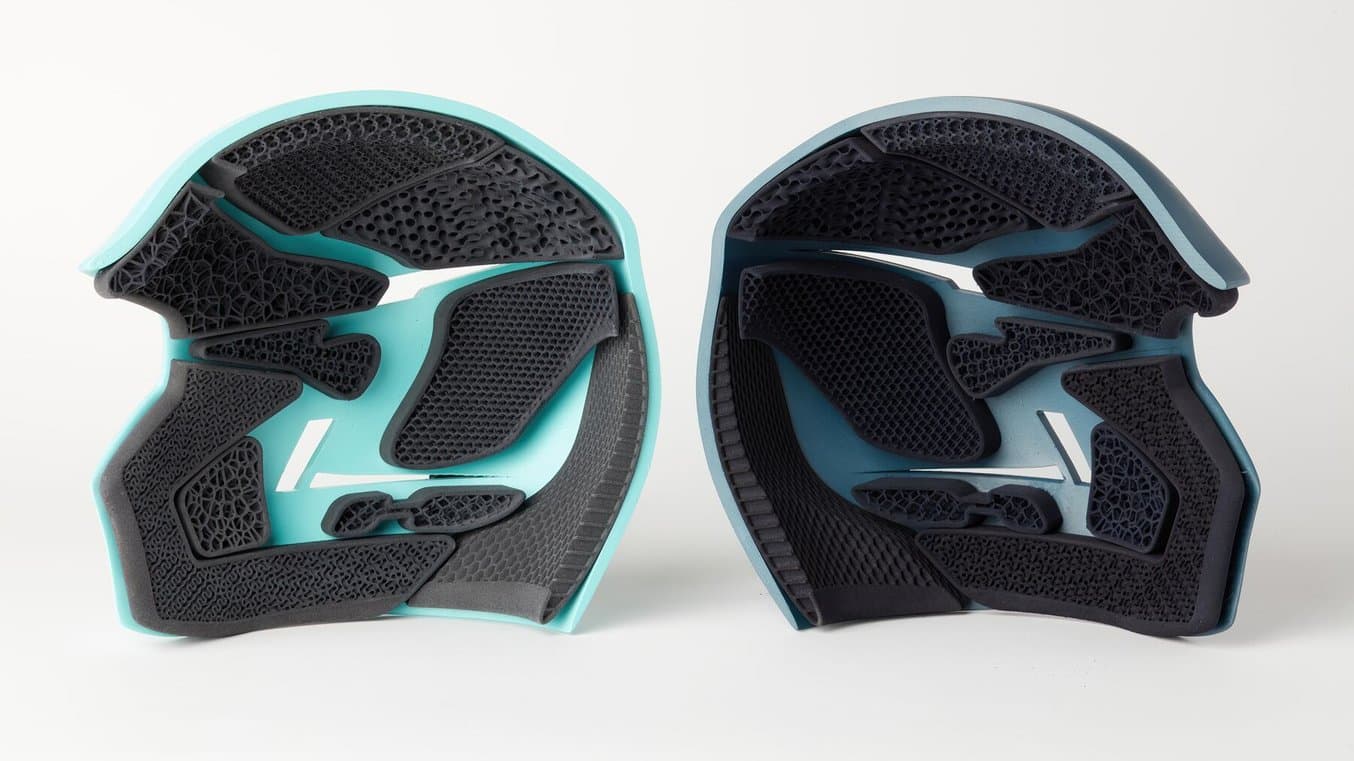
美式橄榄球头盔,采用 Fuse 系列 SLS 3D 打印机打印的 TPU 定制衬垫。
医疗器械
3D 打印 TPU 具有卓越的耐久性和韧性,适用于制造义肢、矫形器、患者特定的器械以及医疗设备。在 3D 打印制造坚固的柔性成品部件的过程中,通过将橡胶材料出色的抗撕裂强度和断裂伸长率与 SLS 3D 打印优异的设计自由度和耐久性相结合,为医疗专业人士带来了新的机遇。
TPU 是一种柔性弹性体,适合通过 3D 打印制作以下医疗部件:
-
医疗器械原型、成品医疗器械和组件
-
矫形垫和修复衬垫
-
可穿戴设备、密封件、阻尼器和管子
-
夹板、颅骨重塑头盔
-
运动和矫正鞋垫
医疗保健领域的 3D 打印技术虽然方兴未艾,但却受到严格的材料要求限制,包括安全认证以及强度和机械性能。3D 打印 TPU 为医疗保健领域的不同应用提供了更多机会,从而进一步完善了“工具箱”。
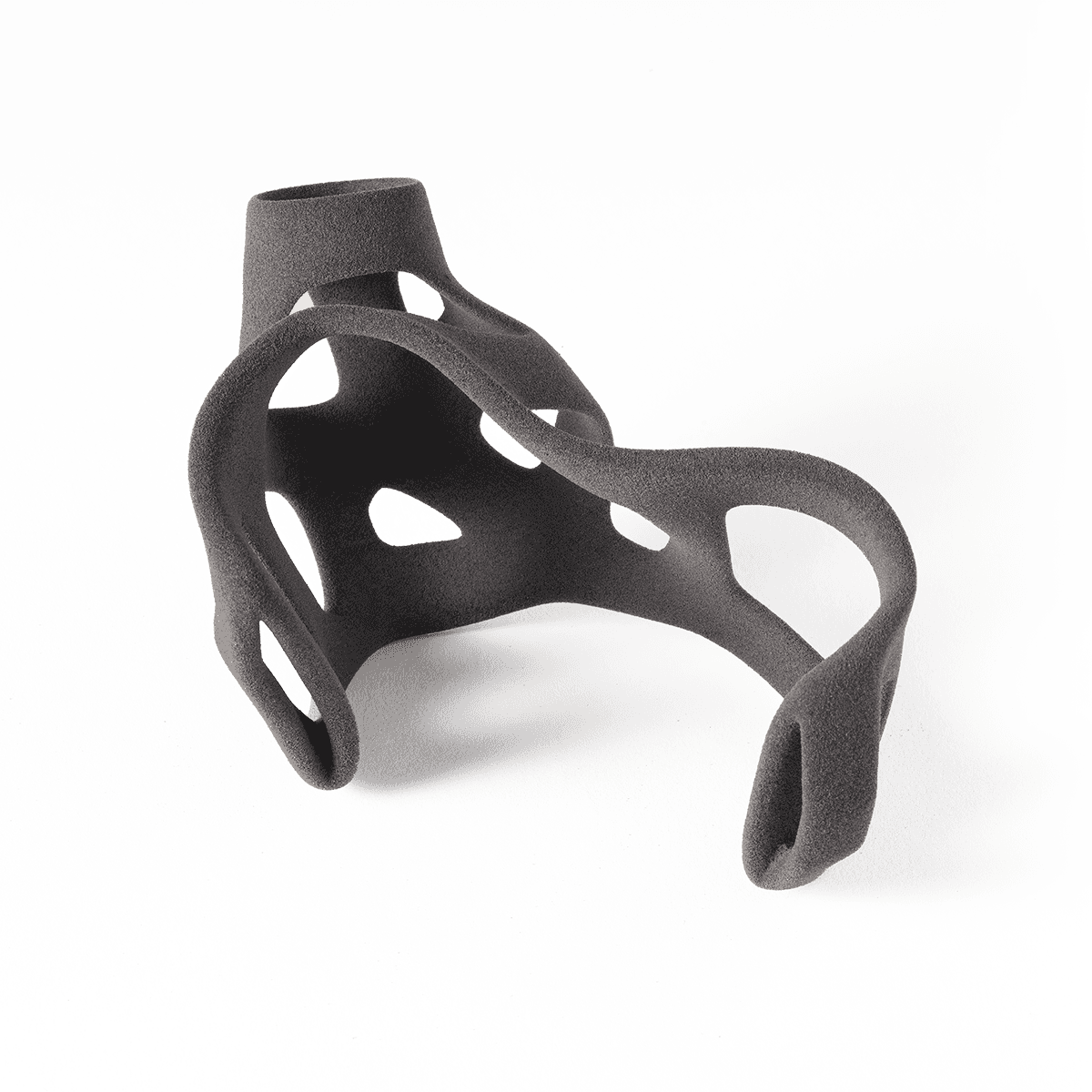
与传统支架相比,这种定制拇指矫形支架具有更好的柔韧性和更强的控制力,可为拇指提供支撑并防止进一步受伤。
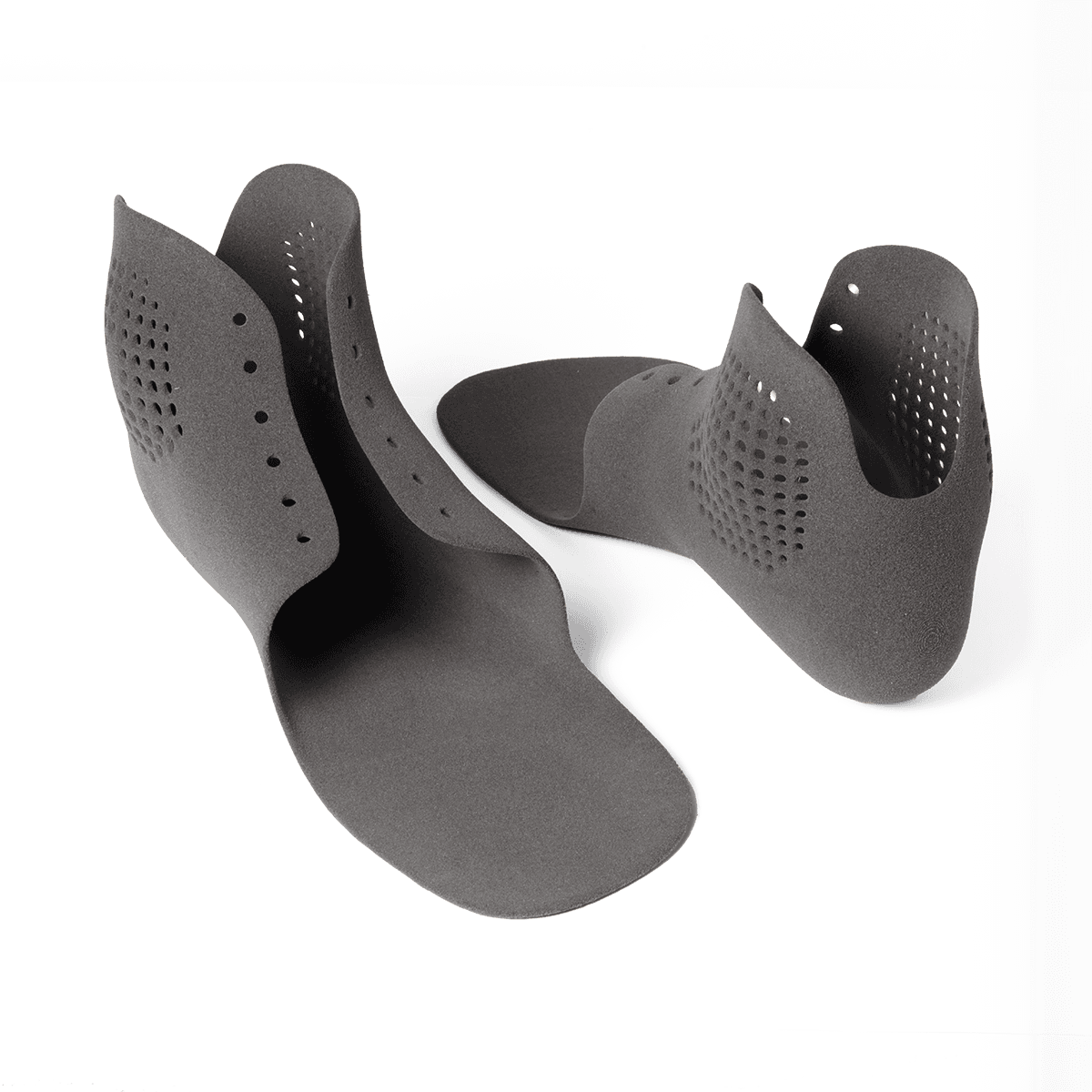
TPU 是各种矫形装置(如足部矫形衬垫)以及运动和矫正鞋垫的理想材料。
案例研究
全球印刷机领导者海德堡的机器保护部件
海德堡印刷机械股份公司 (Heidelberger Druckmaschinen AG) 是全球领先的胶印机制造商,在 170 多个国家开展业务,全球员工近万人。该公司为整个印刷价值链生产各种工具和自动化解决方案,包括最大、最快的先进印刷机以及裁切机和折叠机。
他们使用 Fuse 1+ 30W SLS 3D 打印机制造机械部件,包括拾放机器人的轻质部件、折叠机的新部件以及原钢制机器组件的替换件。TPU 90A Powder 使他们能够制造出可承受冲击的柔性部件,其延展性足以安装到现有的刚性机械上。
由于替换件或制造辅助工具需要安装在现有的机器人系统上,因此这些部件通常具有奇特的复杂形状,并根据其所承受的应力和作用力专门开发,会受到持续磨损。3D 打印部件还经常与其他组件结合使用,如具有抗摩擦特性的金属轴承或铁氟龙涂层组件。有些部件不太复杂,但仍然需要高精度或精细度。
柔性 TPU 部件可用于防止污染、遮挡尖锐边缘、保护传感器或防止磨损。使用 TPU 90A Powder 进行 SLS 3D 打印是制造此类部件的完美工作流程,可以保护昂贵的机器免受严苛使用条件所带来的损坏。
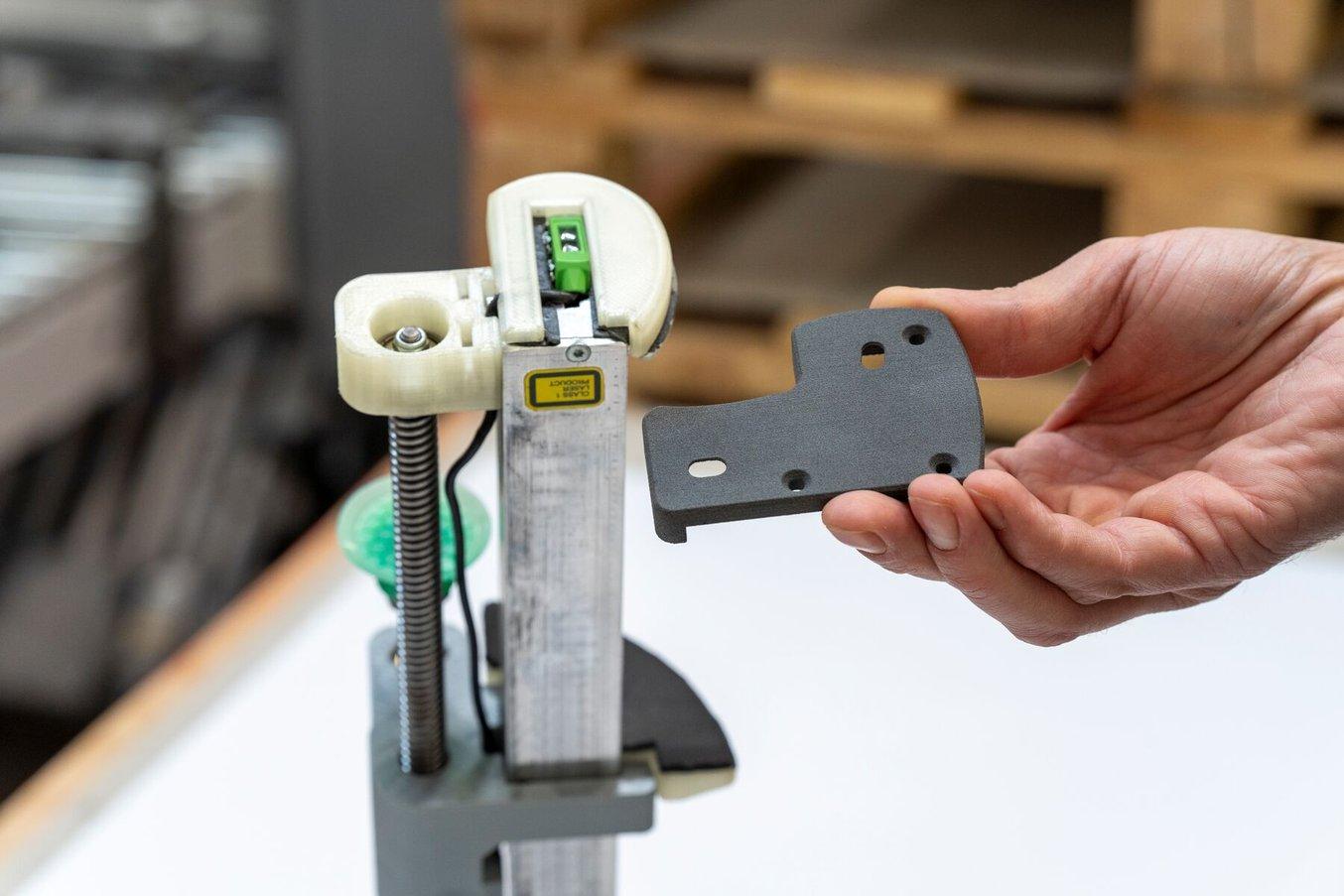
使用 TPU 90A Powder 打印的柔性部件,用于保护传感器和其他臂端工具。
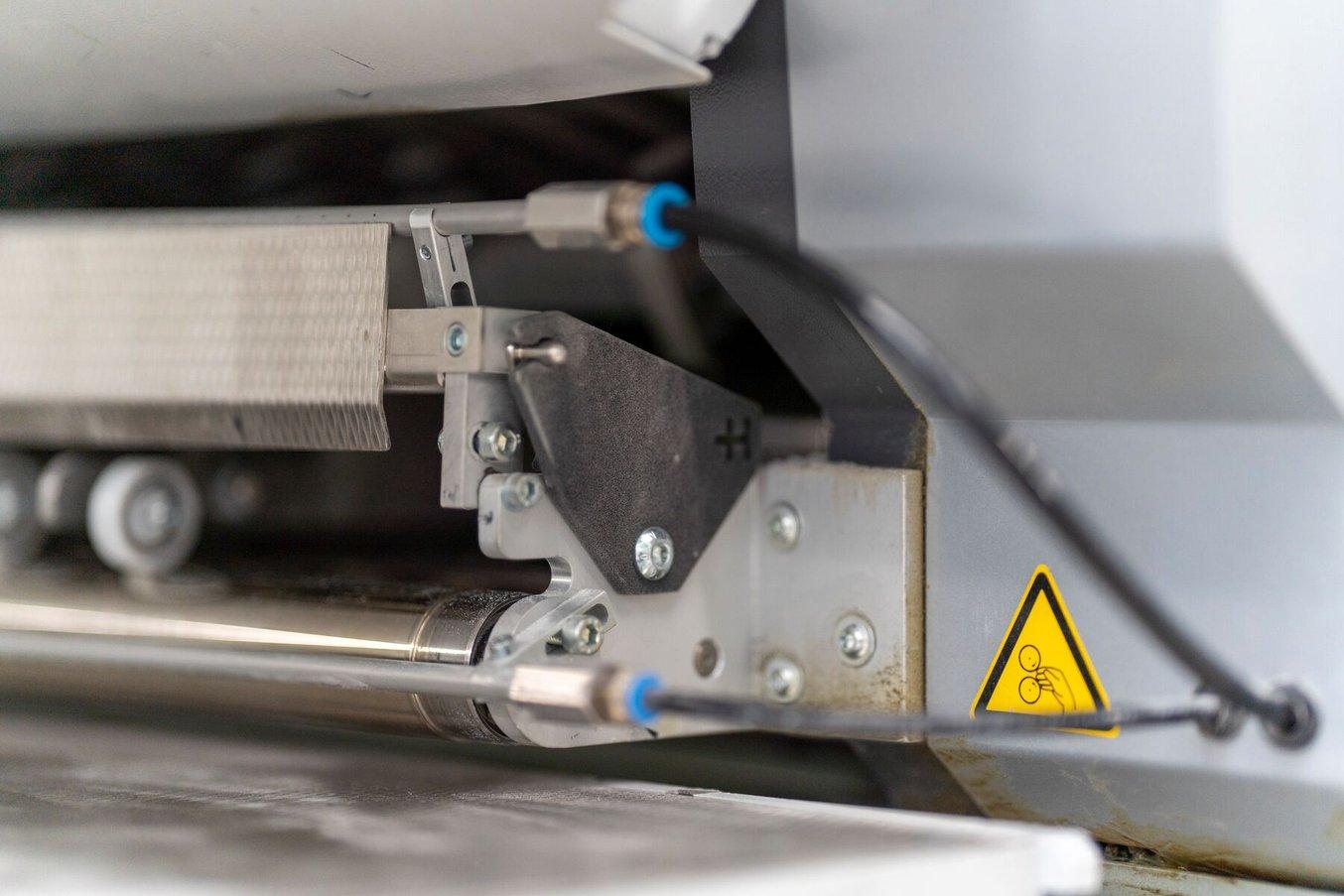
柔性部件是理想的卡扣组件。通过遮挡尖锐边缘,它们也能保护操作人员。
其中一个特殊部件,即用 TPU 90A Powder 打印的电缆导向器组件,可保护电缆免受高度摩擦,从而延长电缆的使用寿命并最大限度地减少停机时间。如果其中一根电缆断裂或磨损,整个机器就会停机,直到可以订购和安装替代电缆。诸如此类电缆导向器等保护性机器组件有助于工厂保持正常运转。
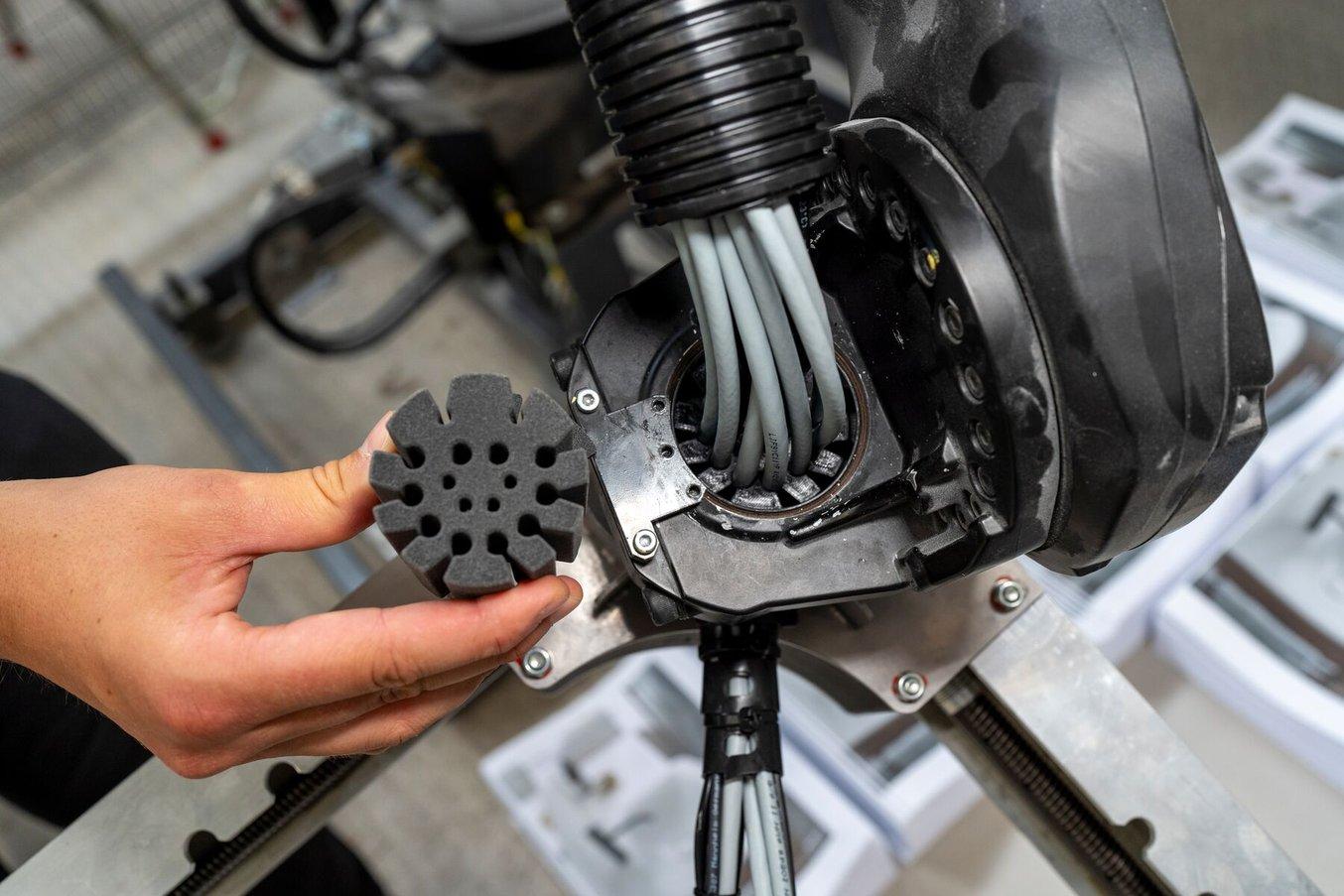
使用 Fuse 系列 SLS 3D 打印机生产的这种柔性电缆导向器不仅实现了复杂的设计,还为保护电缆免受磨损提供了长期耐用的解决方案。
Fuse 系列和 TPU 90A Powder 的易用性和经济性使该公司能够控制自己的供应链和维护需求。TPU 90A Powder 部件是保护机器、提高部件使用寿命的理想选择,最终可帮助企业降低成本,避免停机。
德国铁路公司如何利用 TPU 制造辅助工具确保列车运行正常
德国铁路公司位于 Neumunster 的车辆维修点负责检修和维护德国的公共列车,3D 打印技术有助于尽可能提高其运营效率。将 3D 打印技术融入工作流程后,德国铁路公司节省了数百万欧元,并缩短了运营列车恢复行驶的准备时间。
制造工程师兼增材制造专家 Carsten Wolfgramm 负责管理两台 Fuse 1+ 30W SLS 3D 打印机,其中一台使用 Nylon 12 Powder,另一台使用 TPU 90A Powder。“我们之所以使用 Formlabs 设备,是因为其性价比对我们来说是无可匹敌的。它们非常可靠、即插即用,尤其是 SLS 打印机。在不断迭代部件的情况下,可以简化工作。而且这些打印机可以全年不间断运行,”Wolfgramm 表示。
在一项常见的维护工作中,技术人员要拆下行李架,对列车车厢墙壁重新刷涂油漆和加固。移动行李架经常会对墙壁造成损坏,使维护团队刚刚完成的工作前功尽弃。为了保护墙壁,DB 团队用 TPU 90A Powder 设计并 3D 打印了行李架的定制保护罩。保护罩可滑动到行李架上并隔离边缘,因此在拆卸和更换行李架时不会对刚粉刷过的列车内饰造成任何损坏。
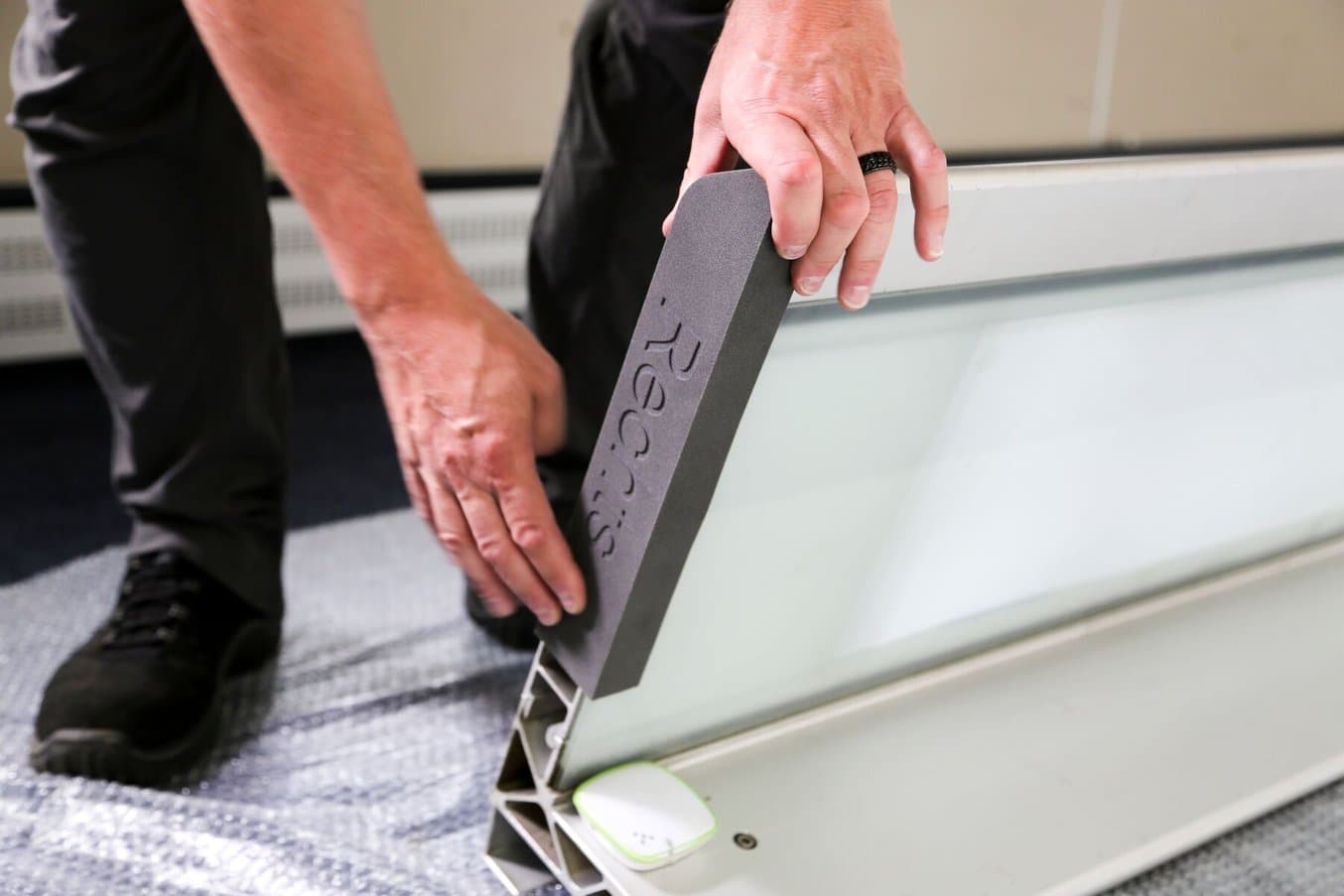
该团队使用柔性材料 TPU 90A Powder 进行划痕和冲击保护。
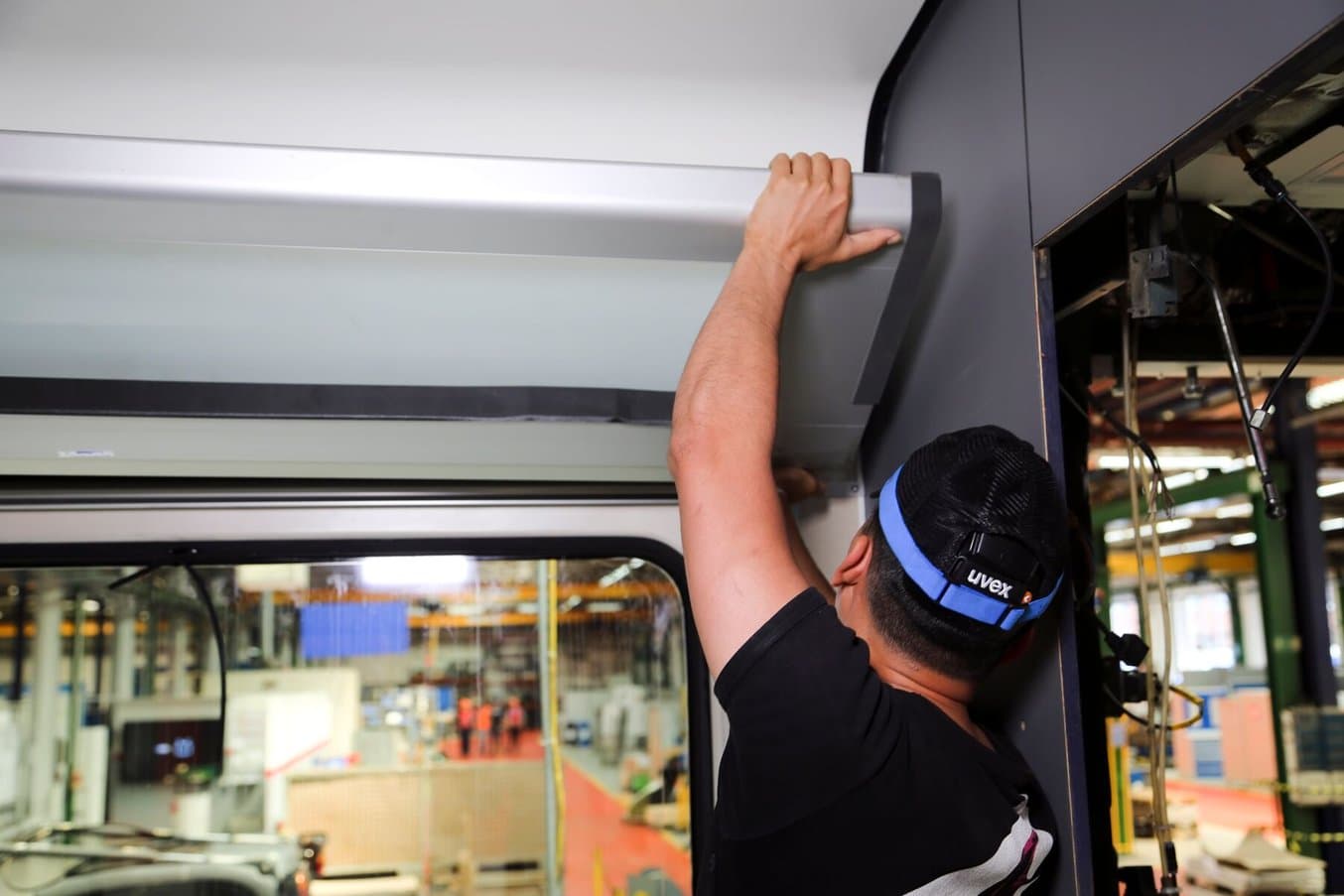
SLS 3D 打印实现了可以安装在行李架和车厢壁之间的超薄设计。
“在我们开发出这种划痕保护装置并使用 3D 打印制作出来之前,我们的同事总是使用气泡膜或类似工具进行传统遮蔽工作,以试图避免划痕,但这并非每次都能成功。由于采用了新的 TPU 部件,我们终于第一次成功地完全消除了划痕。”
Carsten Wolfgramm,德国联邦铁路公司制造工程师兼增材制造专家
通过展示使用 3D 打印 MRO 部件所能实现的成本节约和劳动时间最小化,德国铁路公司为大型运输公司提供了将 3D 打印集成到其工作流程中的设计规划。通过在内部制造可定制的柔性 3D 打印部件(如这些保护罩),德国铁路公司能够提高流程效率,让列车更快恢复行驶。
美国玩具和电动自行车公司的原型制造:Radio Flyer 和 TPU
100 多年来,Radio Flyer 深受千家万户的信任和喜爱,其代表性产品 Original Little Red Wagon® 已入选“国家玩具名人堂”。作为世界领先的车载玩具生产商,Radio Flyer 一直走在流行文化的前沿,并面向广大家庭提供货车、滑板车、三轮车、卡丁车、电动自行车和其他创新产品,以求帮助客户前往梦想之地,并始终名列孩子们的圣诞礼物清单榜首。
3D 打印是 Radio Flyer 开发工作的重要组成部分,而设计工程师 Agostino Lobello 则发现 TPU 90A Powder 有助于制作真正的功能性原型。“与我曾使用过的其他 3D 打印 TPE/TPU 材料相比,TPU 90A Powder 独一无二的表面光洁度可以提供出色的摩擦力。从这个角度来看,该材料的触感更类似于我们的注射 TPE/TPU,因此堪称原型应用的理想选择。目前,该工艺的次优替代方案是利用原型工具并注入真正的 TPE 或其他聚氨酯,而其成本和用时表现都要逊于此工艺,”Lobello 说道。
“我们对将这种材料应用于轮胎胎面、握把、保险杠、坐垫的前景充满期待,并打算将其用于制作具有特定弹簧刚度的 TPE 弹簧原型。”
Agostino Lobello,设计工程师
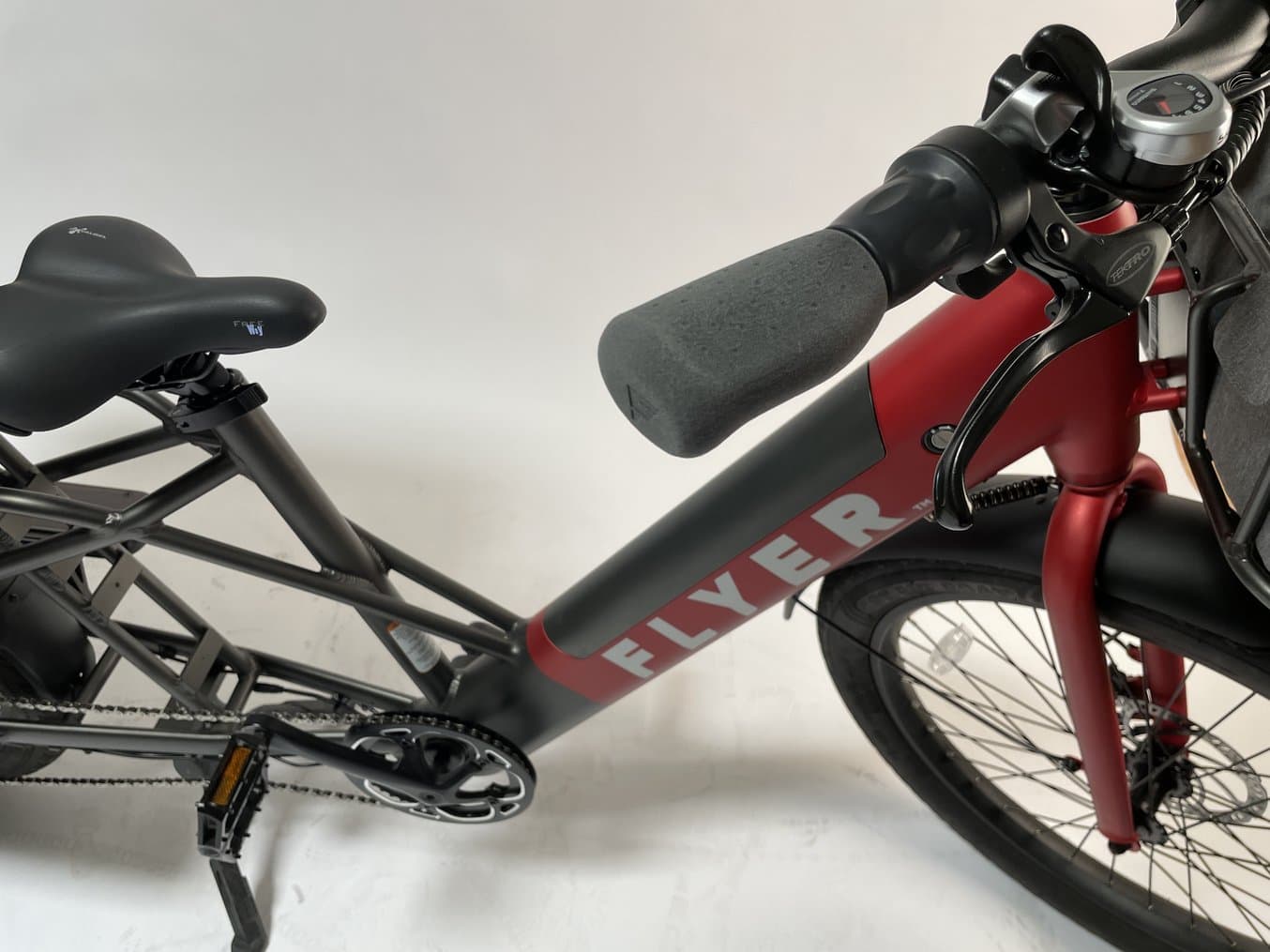
在 Fuse 系列打印机上使用 TPU 90A Powder 可帮助 Radio Flyer 制造部件的功能性原型,如其 Flyer™ L885 Family Cargo eBike 上的这些柔软握把。
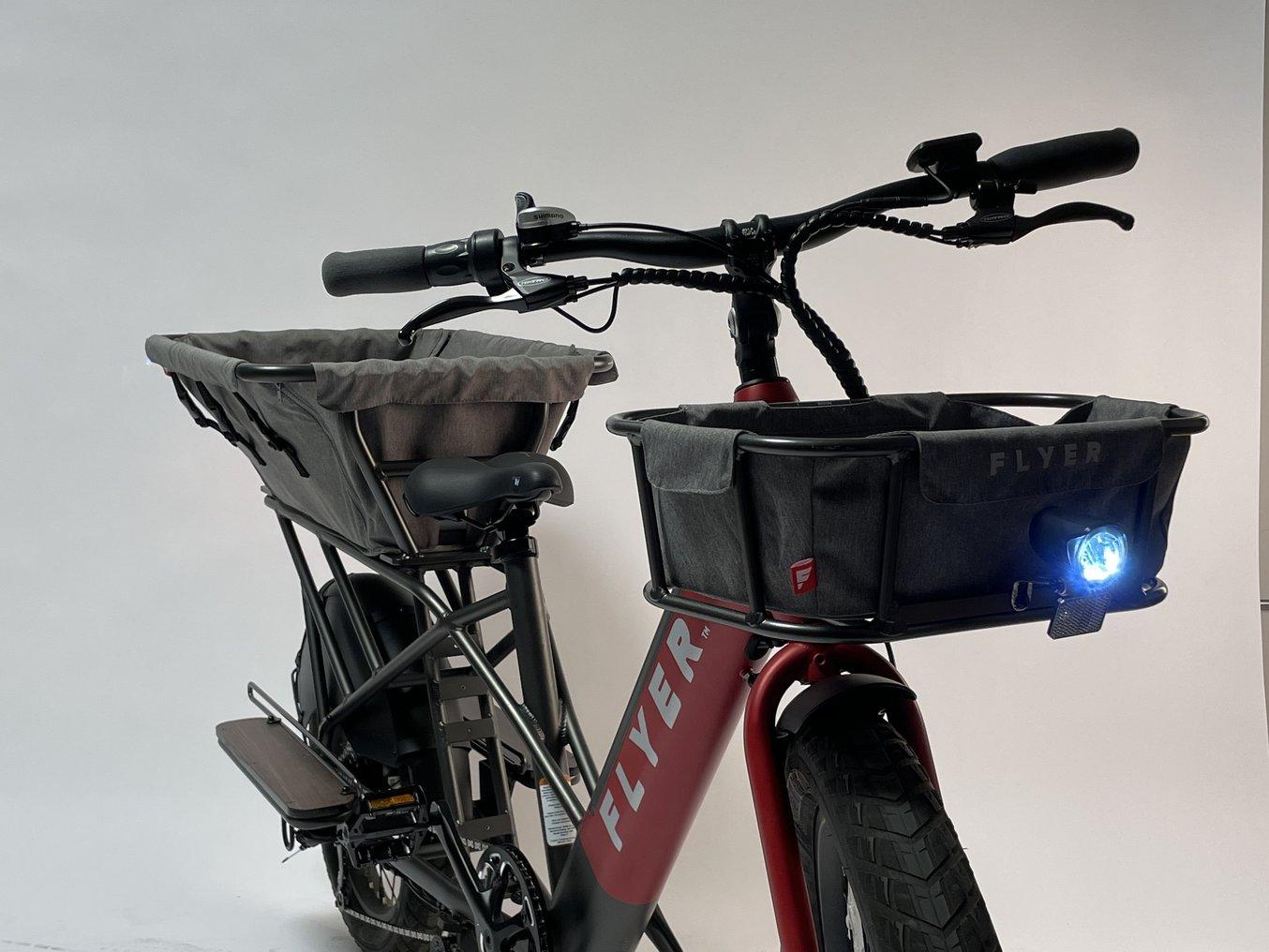
开始在 Fuse 系列中使用 TPU 进行 3D 打印
使用 TPU 粉末的 SLS 3D 打印工作流程为制造商提供了多种可能性,他们可以通过高质量的迭代原型制造来改进设计流程,或参与定制化成品部件生产。
Fuse SLS 生态圈(包括打印机和 Fuse Sift)结构紧凑、经济实惠、易于使用。Formlabs TPU 90A Powder 可制造出坚固、柔韧且具有各向同性的部件,从而实现全新应用并简化工作流程。在任何应用领域或行业,橡胶类部件的内部制造解决方案都能让您在设计和制造过程中获得更多的控制权和灵活性。Formlabs 的 TPU 90A Powder 具有可安全接触皮肤等级,这为医疗保健和可穿戴设备行业提供了更多可能性。
如需了解更多有关使用 Formlabs SLS 工作流程生产 3D 打印 TPU 部件的信息,您可以免费索取 TPU 90A Powder 样品部件,或联系我们的销售团队共同讨论您的独特应用。