汽车行业正在经历快速转型-消费者情绪指数和监管要求给汽车行业带来了日益增加的压力,使其不得不从燃油汽车过渡到电动汽车。福特汽车正引领着这一潮流,如同其在 100 多年前生产 T 型车和引入装配线一样,该公司计划到 2030 年在欧洲仅销售电动汽车。
福特汽车公司是全球第六大汽车制造商,每年生产超过 400 万辆汽车,在全球拥有超过 17.5 万名员工。福特欧洲业务的核心是福特科隆工厂,该工厂成立于 1930 年,以组装福特嘉年华汽车而闻名。
毗邻该工厂的麦肯尼希产品研发中心负责从头开始设计欧洲市场的所有乘用车,包括嘉年华、福克斯、翼虎等热门车型,以及现在的纯电动汽车探险者,这是欧洲市场的首款电动汽车,并于近期在科隆组装厂投入批量生产。该团队还与福特位于英国的邓顿技术中心合作,为商用车的开发提供支持。
但是,福特是如何应对激烈的竞争和日益缩短的开发周期的呢?请继续阅读,了解麦肯尼希产品研发中心的快速技术中心,该中心在为产品开发创建快速原型方面发挥了重要作用。
生产全尺寸汽车原型的工具
“原型制造在开发过程中非常重要。它为工程师提供了验证设计的可能性。如果日后需要重新制作注射成型模具或生产工具,成本会非常高。还需要花费大量的时间,因此在最坏的情况下,生产过程中会出现停机。使用原型制造技术并应用现有的所有技术就可以避免这种情况,”福特公司快速技术中心主管 Sandro Piroddi 说。
生产全尺寸汽车原型需要多种工具。快速技术中心属于大型设施,其中配备了最新的制造方法:拥有自己的注射成型机、成型工具和各种减材制造工具,例如,铣床甚至可以加工最大的底盘面板。
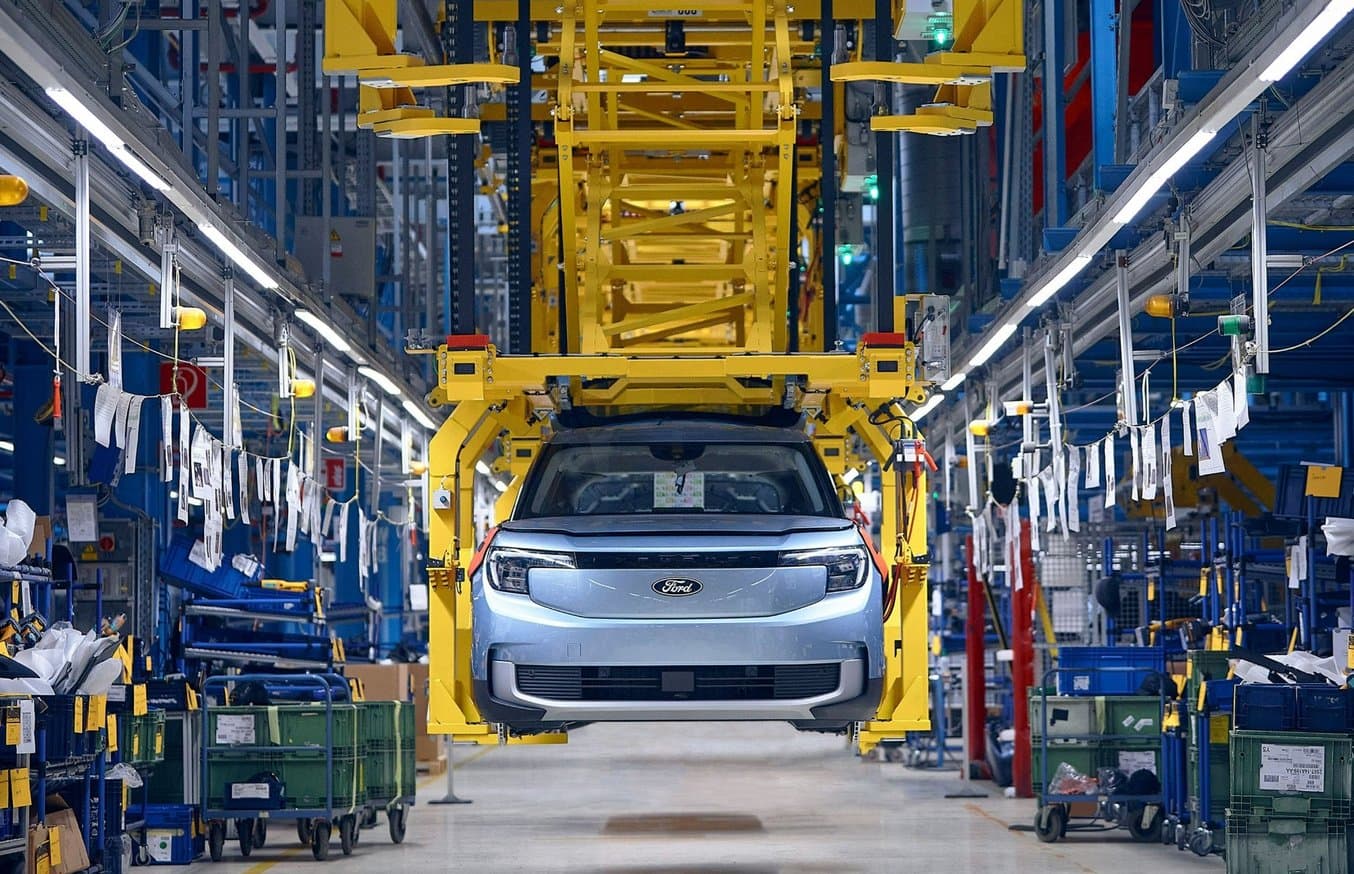
纯电动探险者汽车最近已在科隆装配厂投入批量生产。
当然,如果没有增材制造,这份清单就并不完整。麦肯尼希产品研发中心其实是欧洲第一家在 1994 年使用立体光固化 (SLA) 3D 打印机的车间,此后,其机组已经扩展到一整套熔融沉积成型 (FDM)、SLA 和选择性激光烧结 (SLS) 聚合物 3D 打印机,以及金属 3D 打印。
虽然最初的概念模型仍然使用粘土制作,但随着产品开发进入后期阶段,每个部件越来越接近其最终形状,使用尽可能接近生产的材料和工艺来测试外形和功能变得越来越重要。
“增材制造在开发过程中非常重要。该技术有助于快速、高效地生产部件,并降低成本。您还可以在短期内做出反应。从电气化的发展方向来看,开发时间越来越短,这意味着开发部件和验证车辆部件的时间也不断缩短,因此在开发过程中采用这项技术非常重要。与竞争对手相比,它能让你更具竞争力。”
Sandro Piroddi,福特快速技术中心主管
由于开发时间越来越紧迫,快速技术中心不断寻求增材制造领域的先进技术,以加快部件交付速度。
利用 SLA 3D 打印技术开发设计原型
SLA 3D 打印机主要用于在车间内设计原型,这些原型需要良好的表面质量,并需要快速生产,以实现快速迭代。麦肯尼希产品研发中心的第一台 Formlabs 打印机是 Form 2,但他们很快就扩大了规模,购置了多台桌面级设备和一台 Form 3L 大幅面 SLA 3D 打印机。最近,他们成为首批使用 Formlabs 最新 MSLA 3D 打印机 Form 4 的公司之一。
“Form 4 的速度非常快,我认为它是我迄今为止见过的速度最快的机器。与之前的型号相比,它确实是一次相当出色的升级。更易于操作,因此我们车间的操作人员可以轻松学会如何使用这台机器并获得高品质部件,”福特公司增材制造专家兼模具专家 Bruno Alves 说。
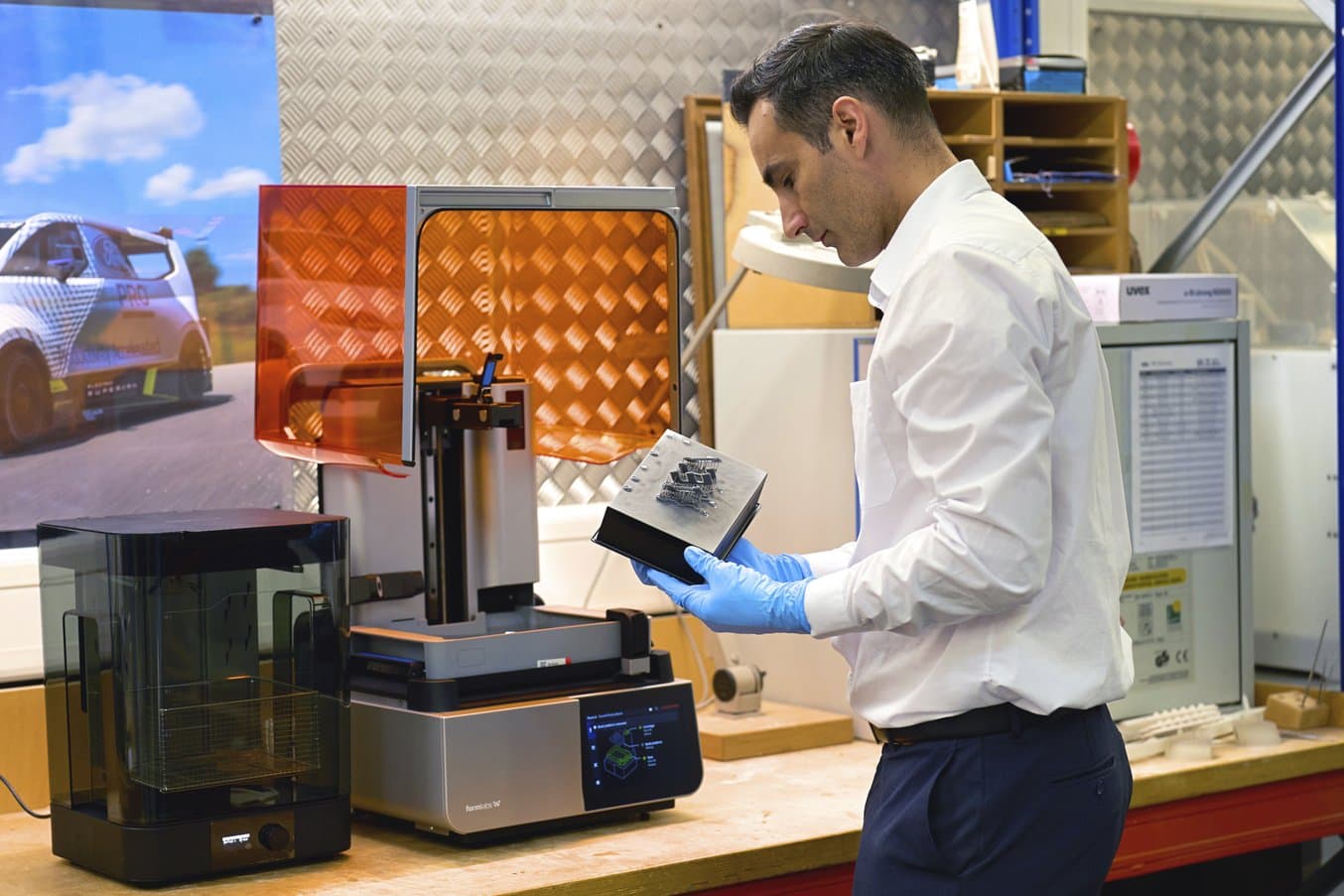
麦肯尼希产品研发中心是新型 Form 4 的测试用户之一。新打印机的超快速度使车间能够在数小时内交付新原型。
“使用 Form 4 确实为我们带来了颠覆性。打印机的速度将改变我们的工作流程。我们可以交付更多部件,从而提高产量。如果面对紧迫要求,我们还会更加灵活。现在我们可以使用 Form 4 完成这些工作。”
Sandro Piroddi,福特快速技术中心主管
“几年前,我们需要花费数天时间,而现在只需几分钟就能打印出部件。因此,工程师们不再害怕进行新的设计、迭代,因为他们知道现在可以很快获得部件,”Alves 补充说。
现在,快速打印使 RTC 团队能够在 24 小时内完成更多请求,即使是来自英国的请求,他们也能通过夜间打印快速交付部件。
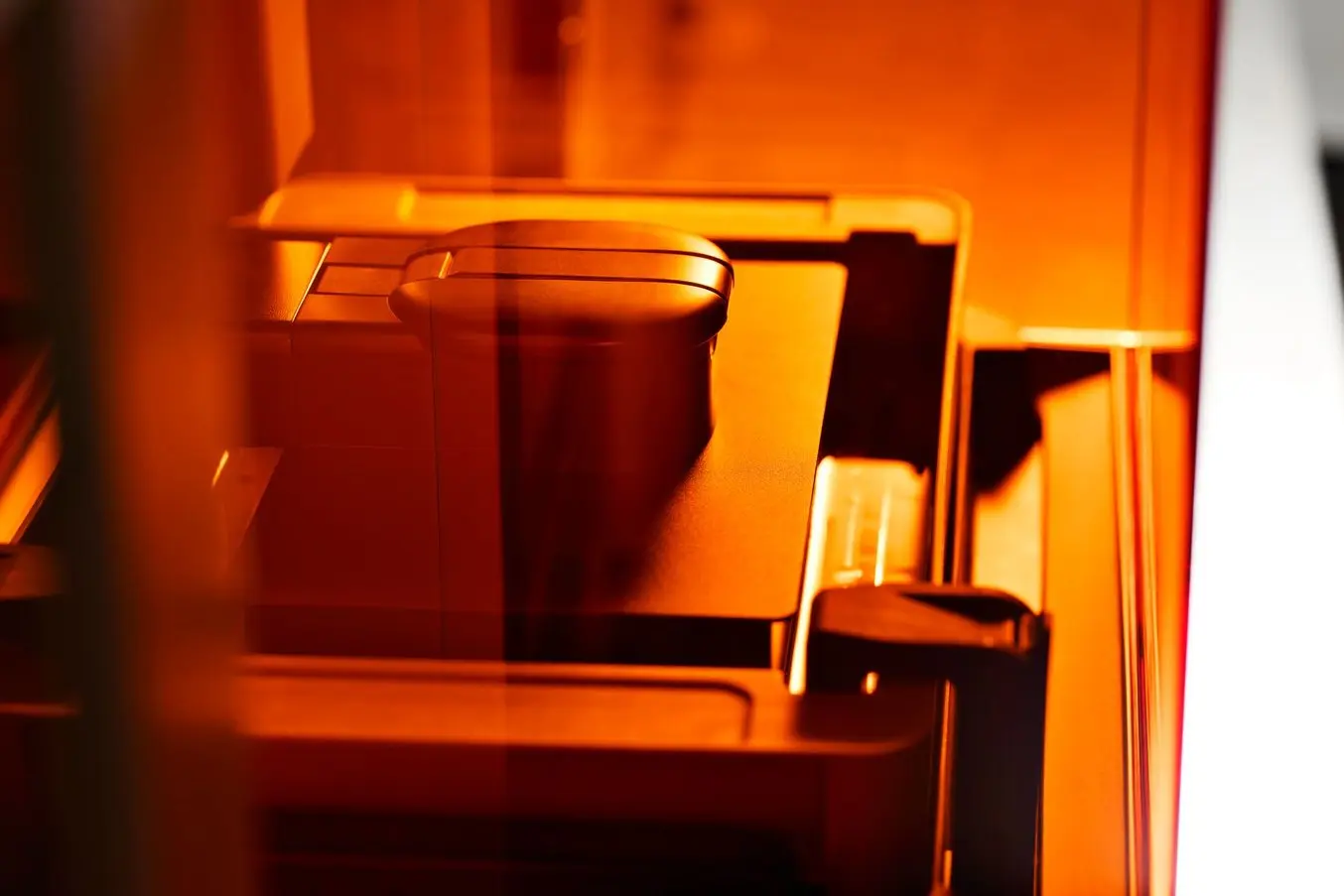
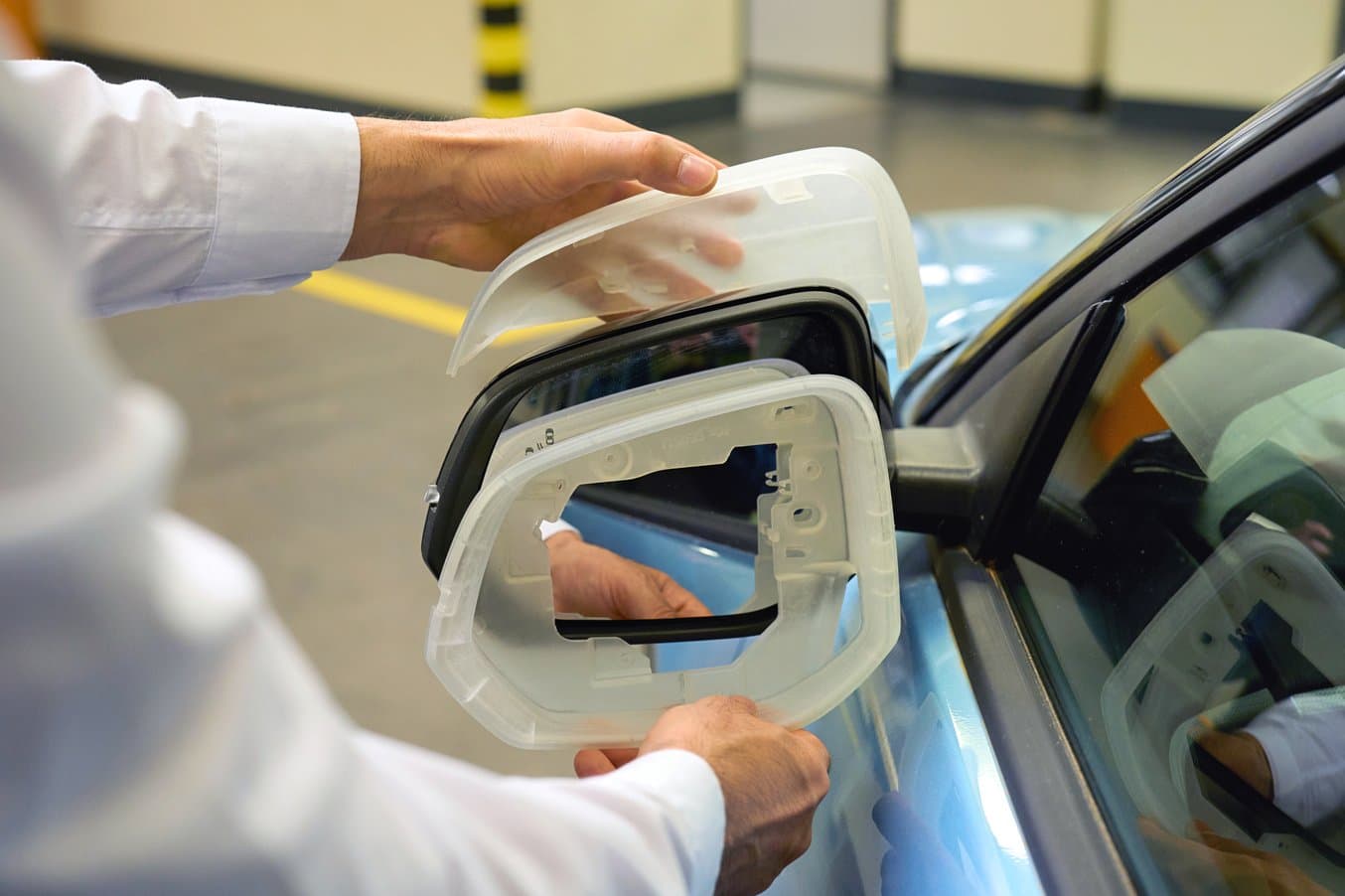
该团队使用 SLA 3D 打印技术为新款探险者的许多部件制作原型,例如后视镜组件。
对于新款探险者,该团队利用 SLA 3D 打印验证了许多外部和内部部件的设计。
“Form 3L 使我们能够打印大型部件,例如车身外部部件。我们打印了这个后视镜镜盖来验证设计。3D 打印非常适合这种应用,因为速度很快,而且与批量生产的部件相比,我们可以获得非常好的质量,”Alves 表示。
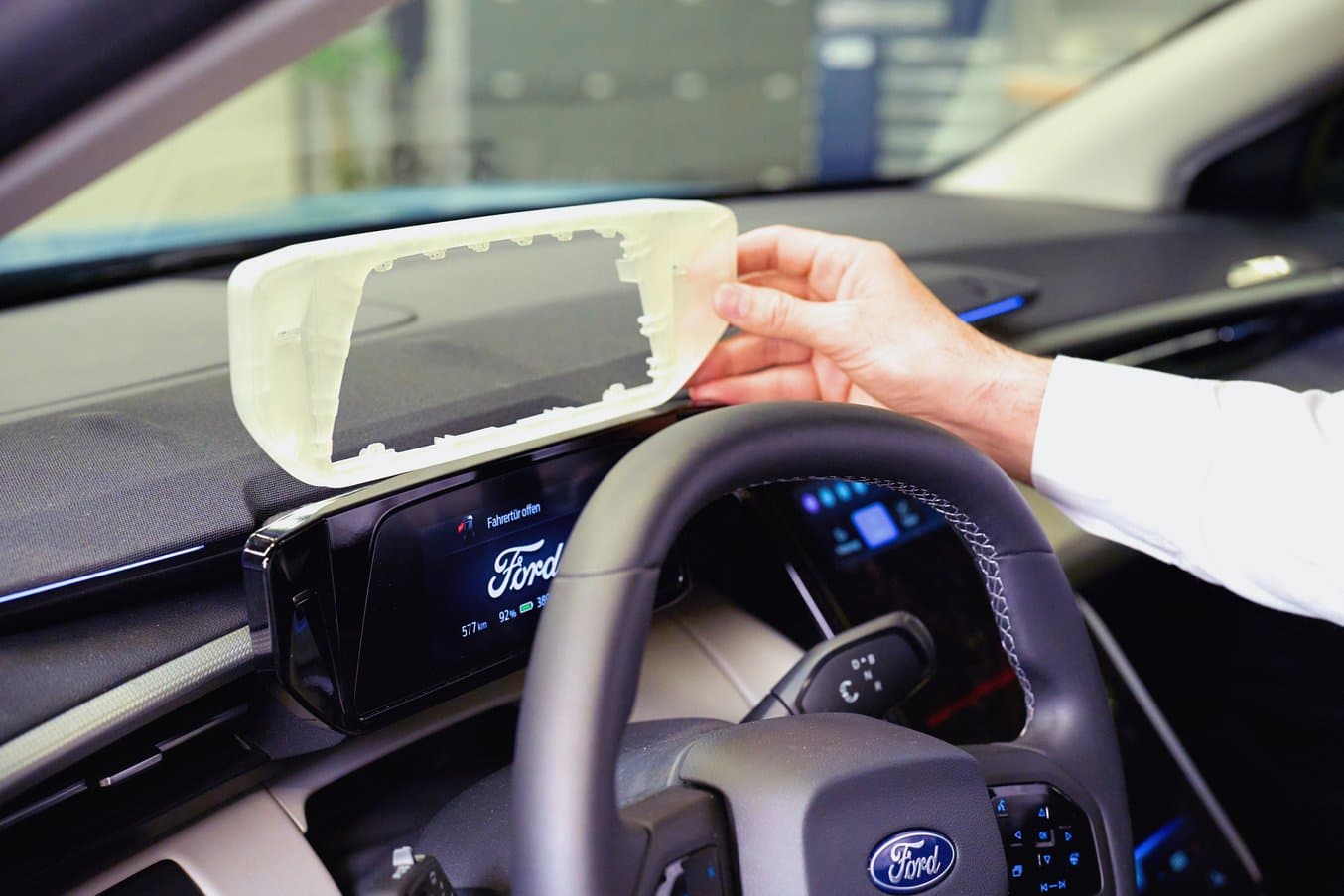
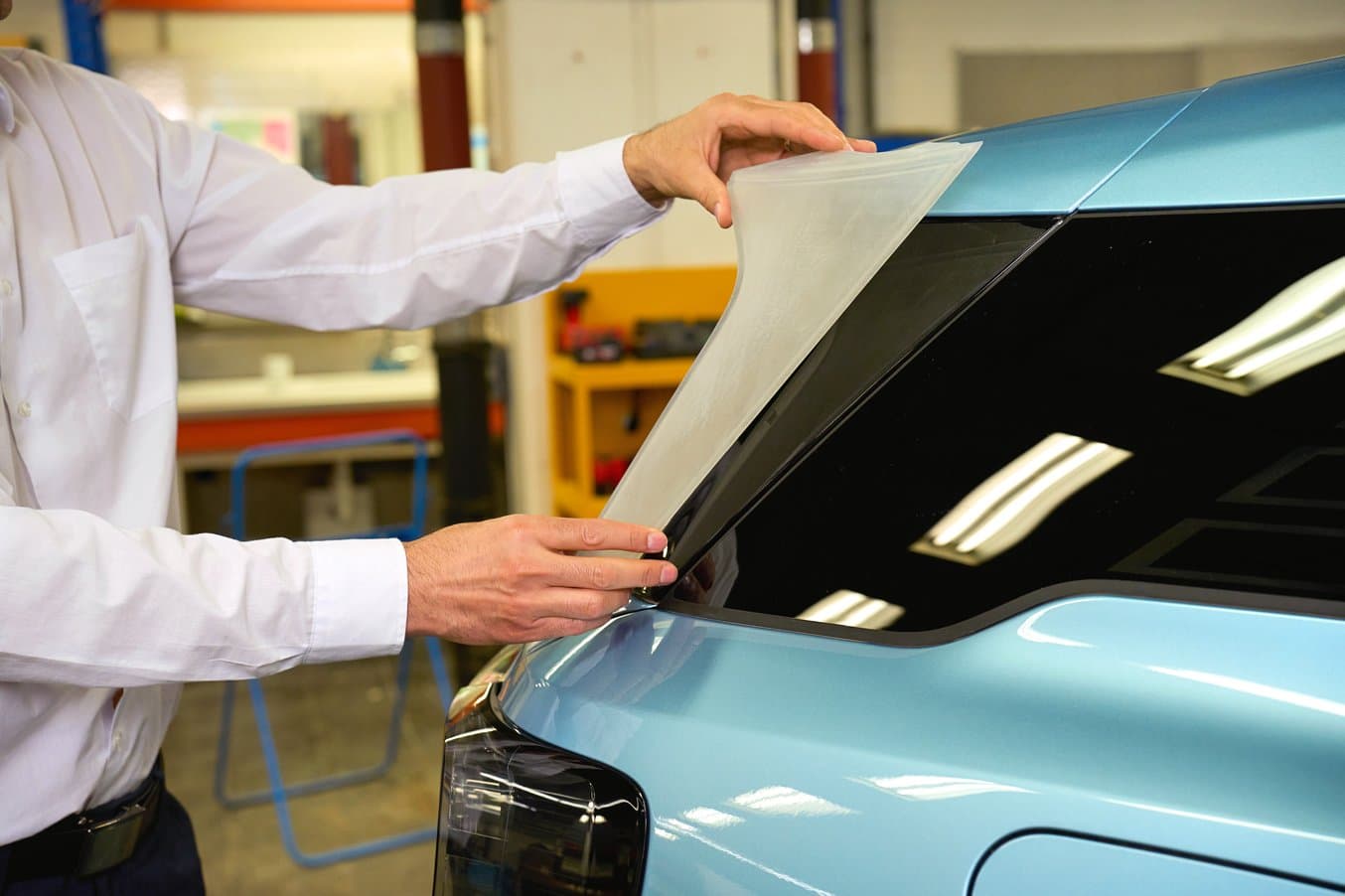
Form 3L 的大成型体积使该团队能够生产一件式大型原型。
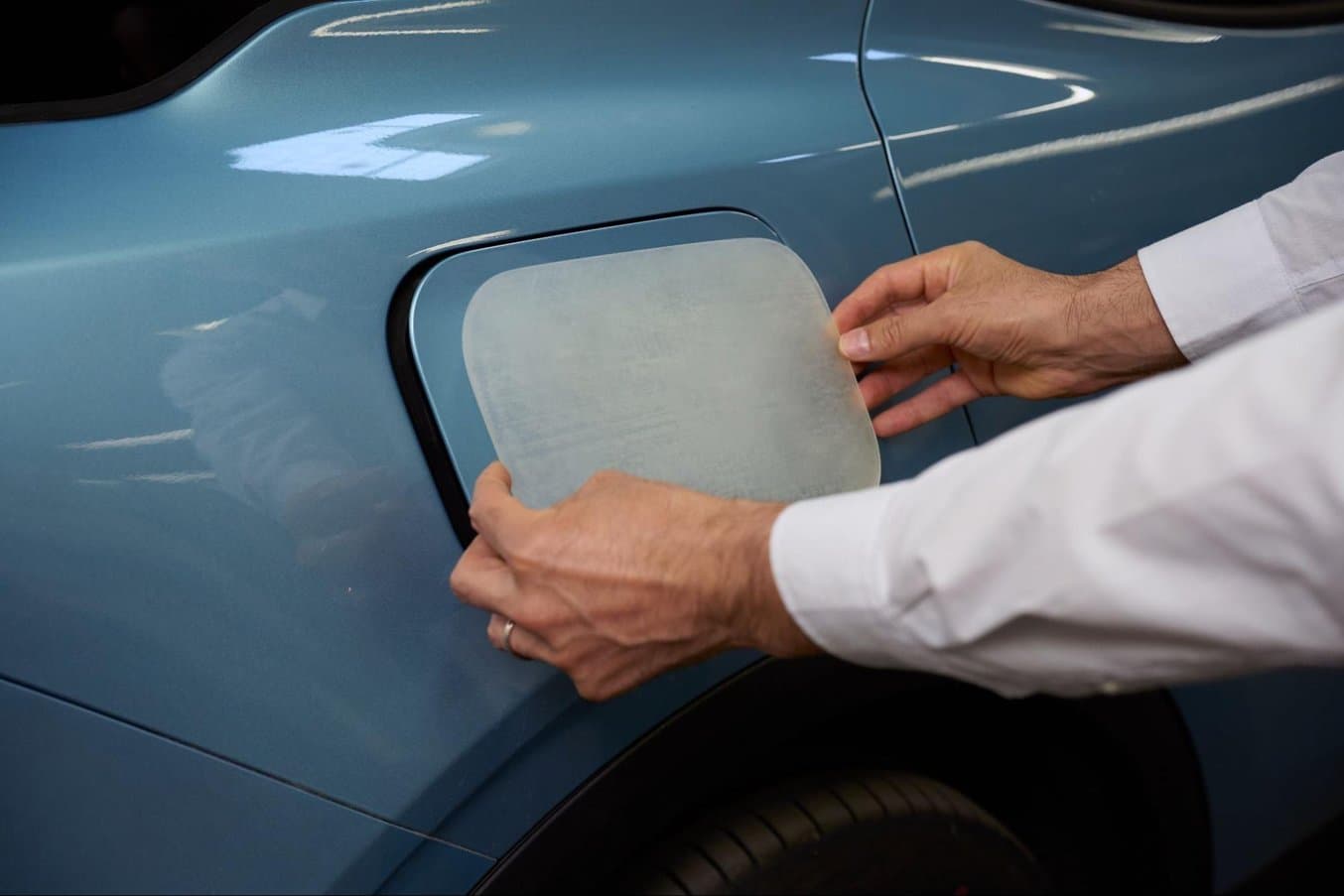
这些部件使用 Clear Resin 打印而成并在 Fuse Blast 中经过介质喷砂处理。
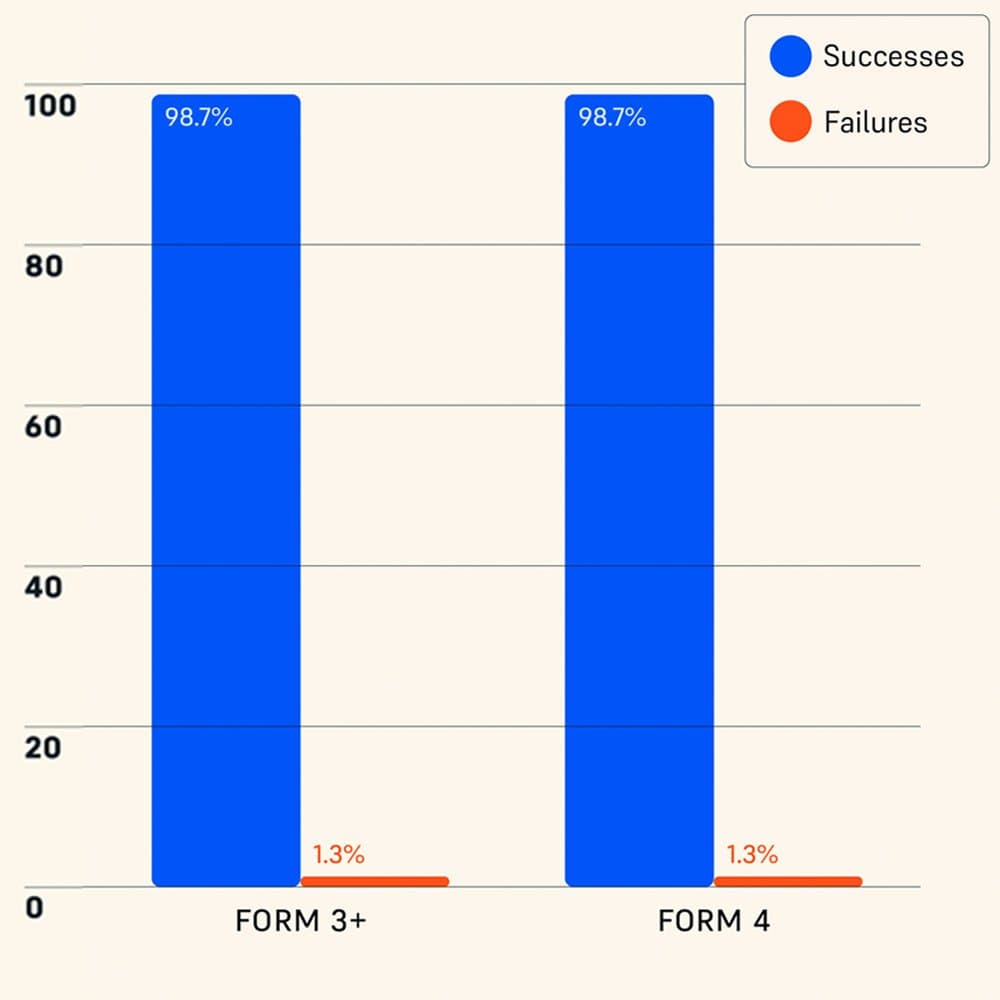
经独立测试的 Form 4 和其他树脂 3D 打印机的可靠性
据一家全球领先的独立产品测试机构测定,Formlabs Form 4 的打印成功率高达 98.7%。请在我们的白皮书中阅读测试方法的完整说明并查看测试结果。
使用 SLS 3D 打印测试机械部件
车间还拥有一组数量众多的 SLS 3D 打印机,用于测试机械部件。
“我们一直在尝试测试和验证与大规模生产中使用的材料更为相似的材料。Fuse 1+ 使用的材料 PA-12 [尼龙]与注射成型的量产部件非常相似,”Alves 说。
虽然该团队内部也有大幅面 SLS 3D 打印机,可以打印大型车身面板,但他们更愿意使用 Fuse 1+ 30W 打印机来打印适合其成型体积的任意部件。
“Fuse 1+ 比竞争对手快得多。我们的工人也可以轻松操作机器。归根结底,对我们来说最重要的是能更快地交付部件。”
Bruno Alves,福特增材制造专家和模具专家
该团队还是 Fuse Blast 自动清洁和抛光解决方案的测试用户之一,该解决方案完善了 SLS 工作流程,简化了后处理过程。
“Fuse Blast 大大加快了我们的流程,因为操作人员现在不需要手动清洁部件了。他们只需把部件放在箱子里,然后启动机器。以前他们都是手动操作,非常耗时。因此,现在操作人员可以在这段时间里做其他事情,从而加快了流程,”Alves 说。

充电端口是属于复杂组件,任何其他方法均无法制作其原型。
SLS 3D 打印的自支撑特性使其更容易制作复杂的设计。在新款探索者中,团队使用 Fuse 1+ 30W 制作了各种机械部件和组件。
“对于这个充电盖来说,使用 SLS 非常重要,因为我们需要一个能够测试机械装置的功能部件。这是一个非常复杂的设计,我们无法以任何其他方式生产。部件无法铣削。我们不能使用注射成型来生产一些样品部件。因此,最好的办法就是用一种我们可以进行物理测试的材料进行打印,”Alves 说。
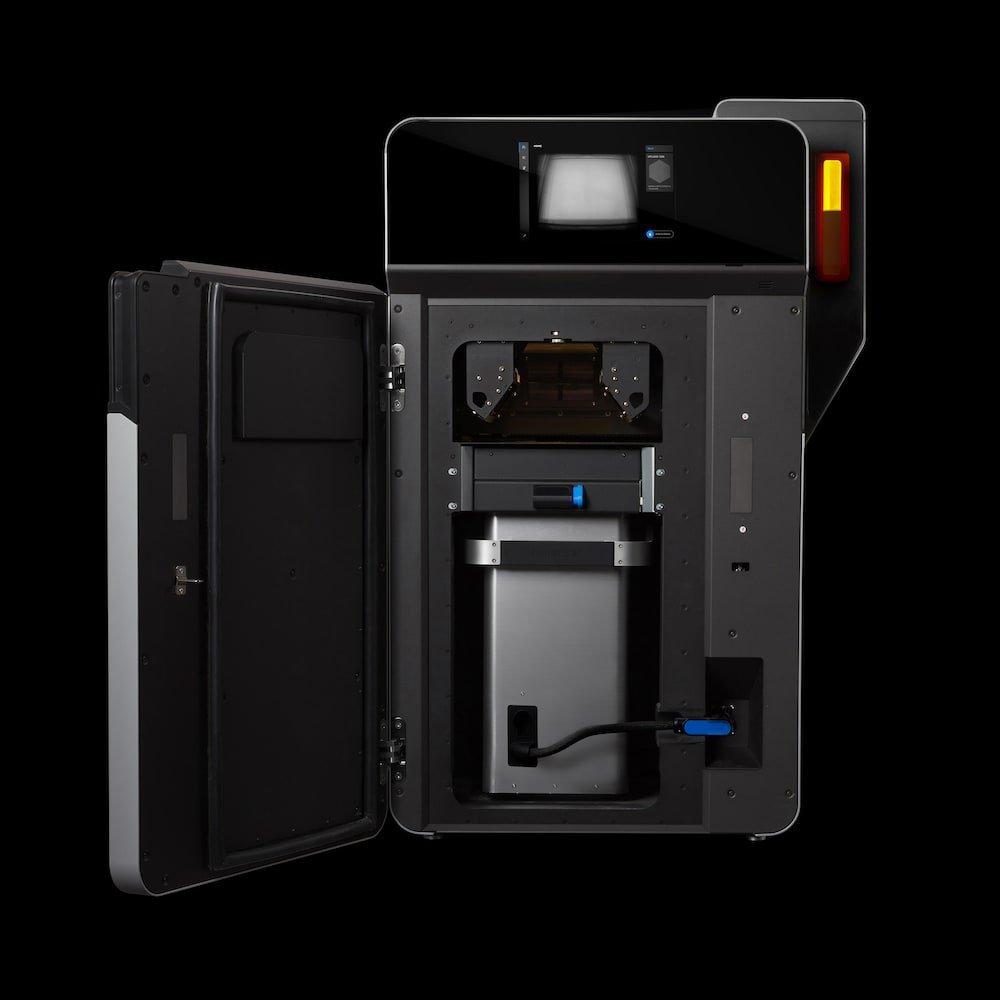
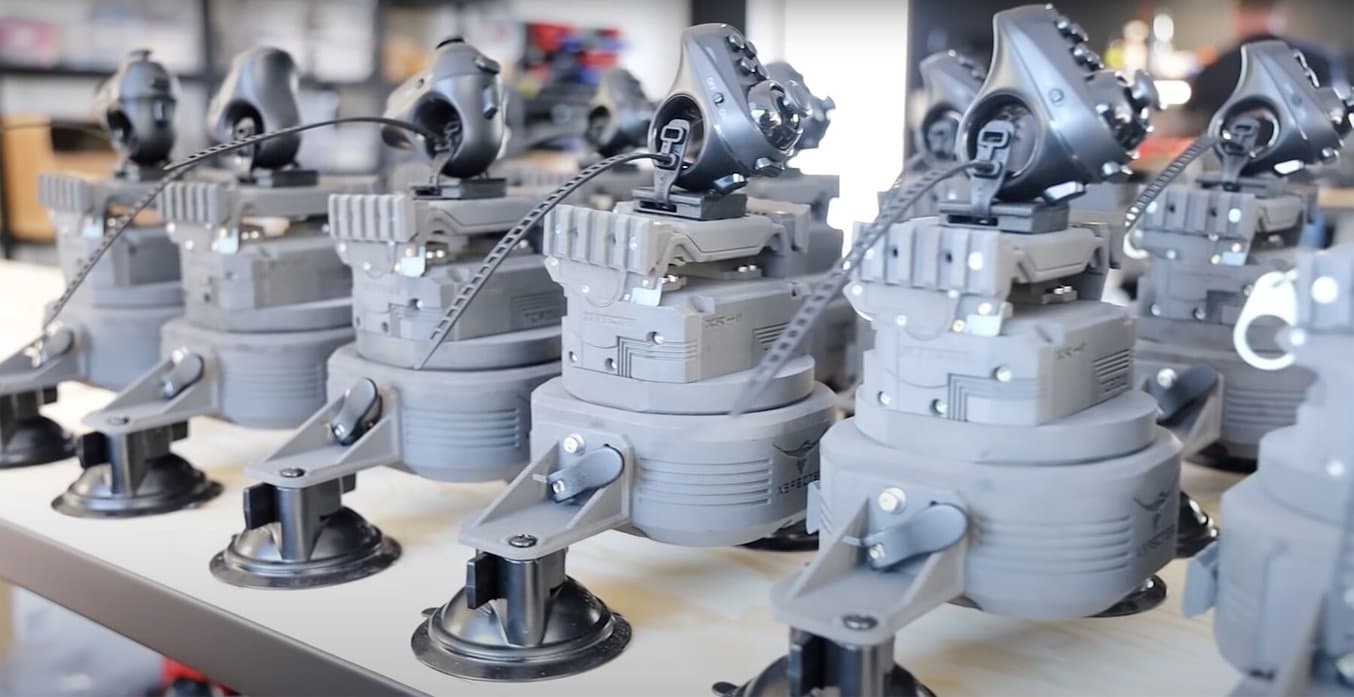
面向成品生产的 SLS
借助 Fuse SLS 生态圈,不仅可以将 3D 打印技术用于生产成品,而且进一步增强了经济性、灵活性和可扩展性。访问我们的 SLS 生产页面,比较生产方法,了解批量粉末价格,并查看目前使用 Fuse 系列的 15 家不同制造商的生产实况。
在内部使用 3D 打印模具嵌件进行注射成型
快速技术中心拥有多种内部技术,因此能够创建混合工作流程,例如将传统制造工艺与 3D 打印快速模具制作相结合。
根据预期应用,团队可以选择最合适的生产工艺和材料,从而优化工作流程的成本、速度和整体效率。例如,在碰撞测试中,部件必须使用与批量生产相同的材料和工艺制造。对于塑料部件来说,这通常涉及注射成型,而这一工艺传统上需要使用成本高、耗时长的金属模具。
“我们认为使用 3D 打印嵌件进行注射成型有很大的潜力,这样可以非常快速地重复设计。我们使用型芯打印出型腔,然后就可以在工具中改变型腔并注射成型部件,”Alves 说。
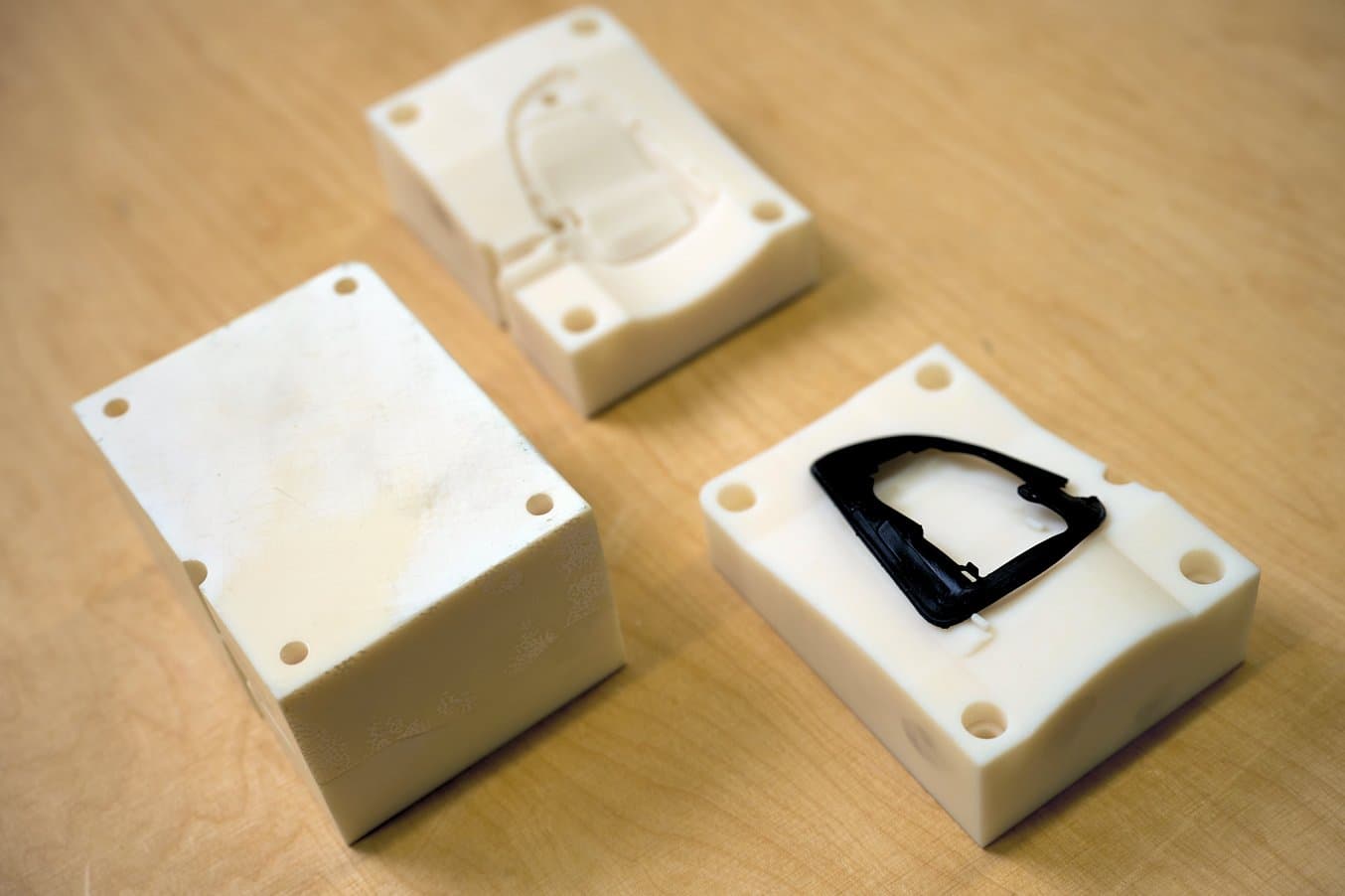
该团队使用 SLA 打印机制造了 Rigid 10K Resin 注射成型模具。
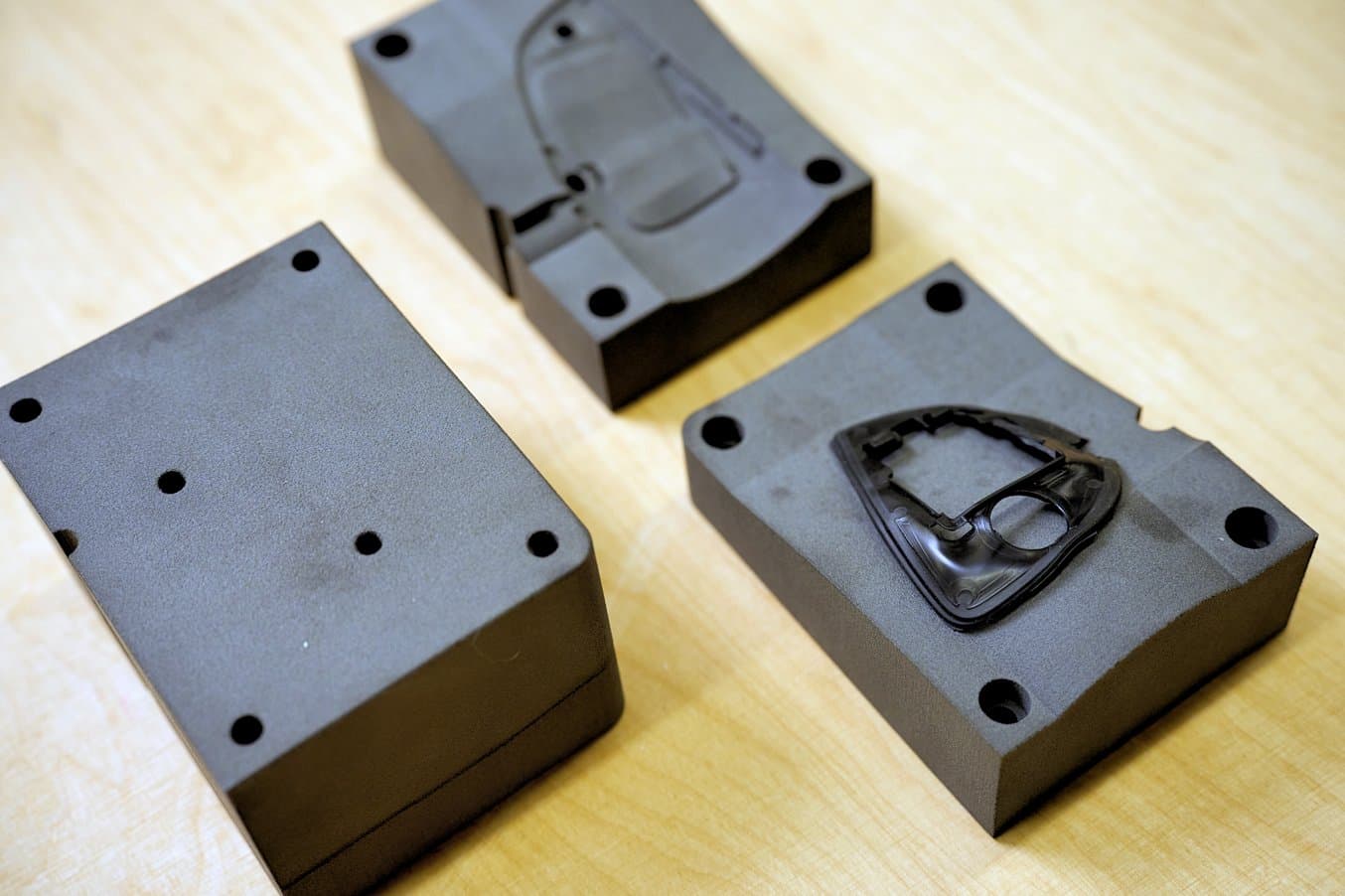
对于同样的应用,他们在 SLS 打印机上使用的是 Nylon 12 Powder。
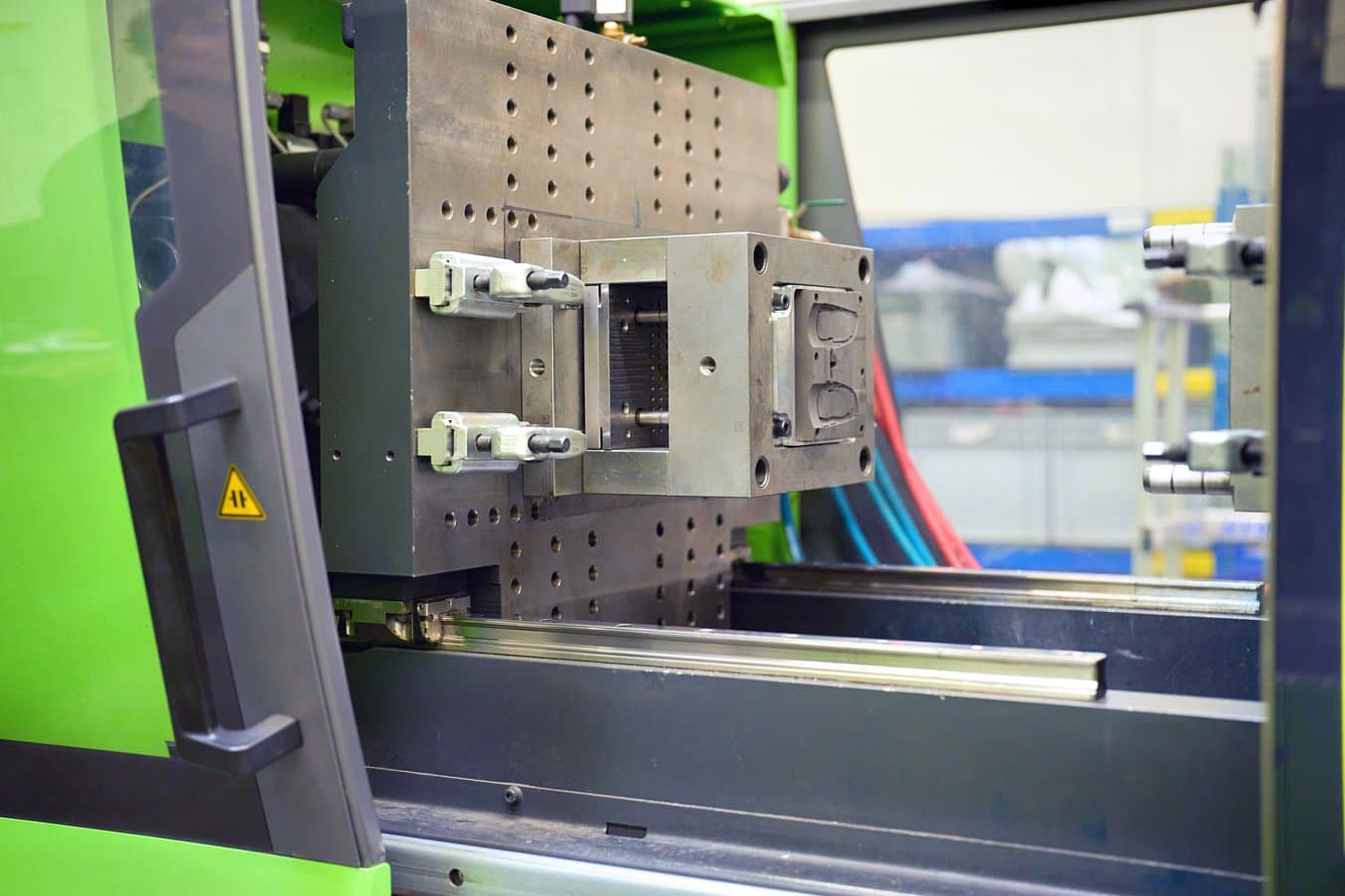
3D 打印技术使团队能够利用内部的工业注射成型机快速生产用于不同设计和快速迭代的模具嵌件。
对于新款探险者,该团队使用 3D 打印模具嵌件在内部注射成型机上生产门把手装配中的橡胶部件。
“这是一个复杂的过程,因为我们使用了多个嵌件,而且还有几种不同的设计,每种设计都可能有多次迭代。通常来说,外部注射成型可能需要两三个月。而在内部使用增材制造技术,我们可以将这一过程加快到两周或最多三周。在这个项目中,如果我们必须使用外部工具,就会耗费更多时间,而且无法按时交付部件,”Alves 说。
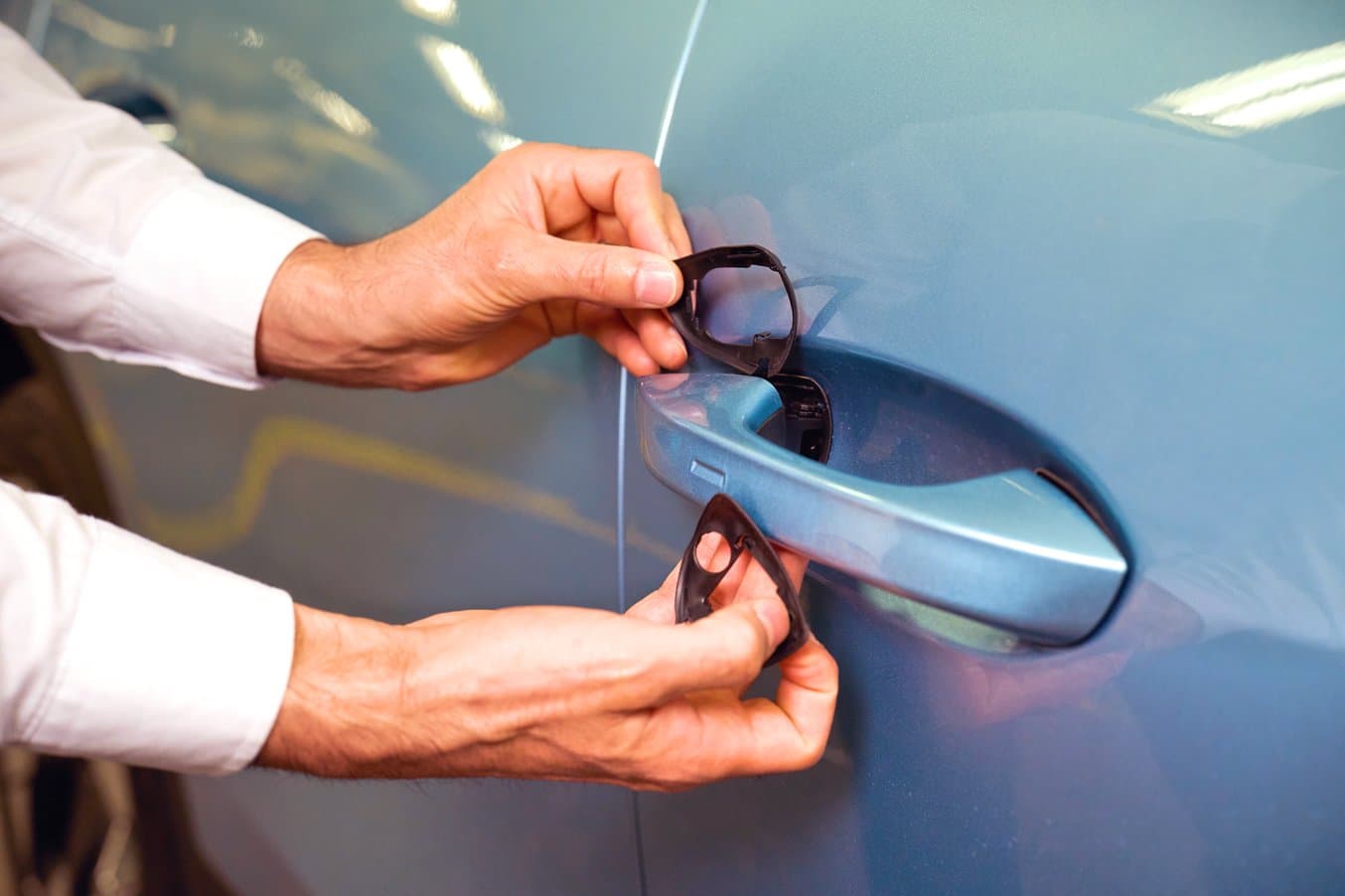
每个门把手设计都包括两个用于减振和隔热的橡胶部件。对于四门 SUV 来说,这意味着每次设计迭代都有八个独特的部件。
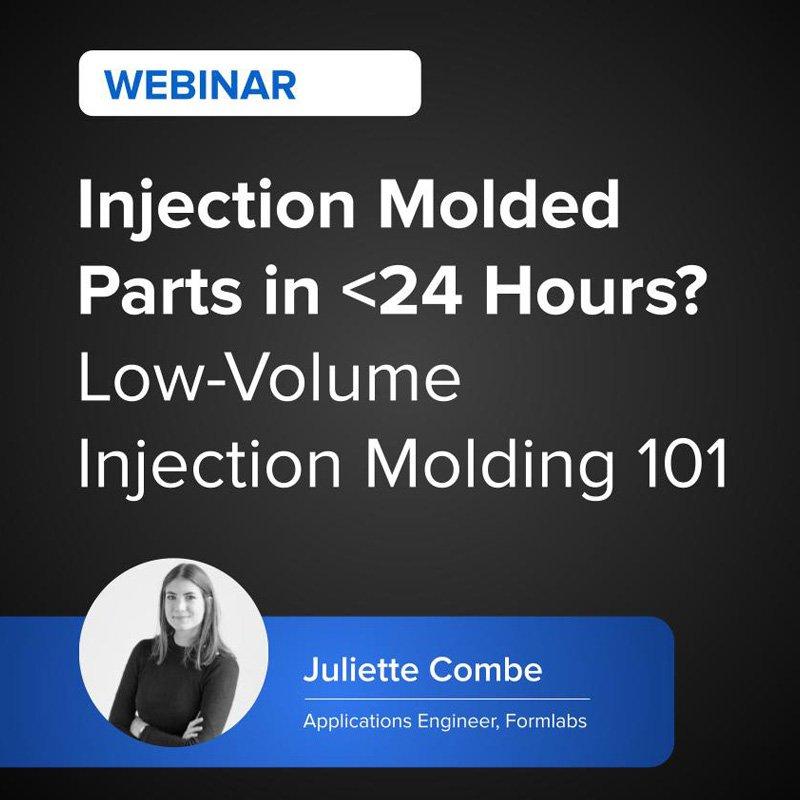
想要在 24 小时之内获得注射成型部件吗?小批量注射成型 101
在本次网络研讨会中,我们将向您展示如何在注射成型过程中使用立体光固化 (SLA) 3D 打印模具来降低成本、缩短周转时间并提高上市产品质量。
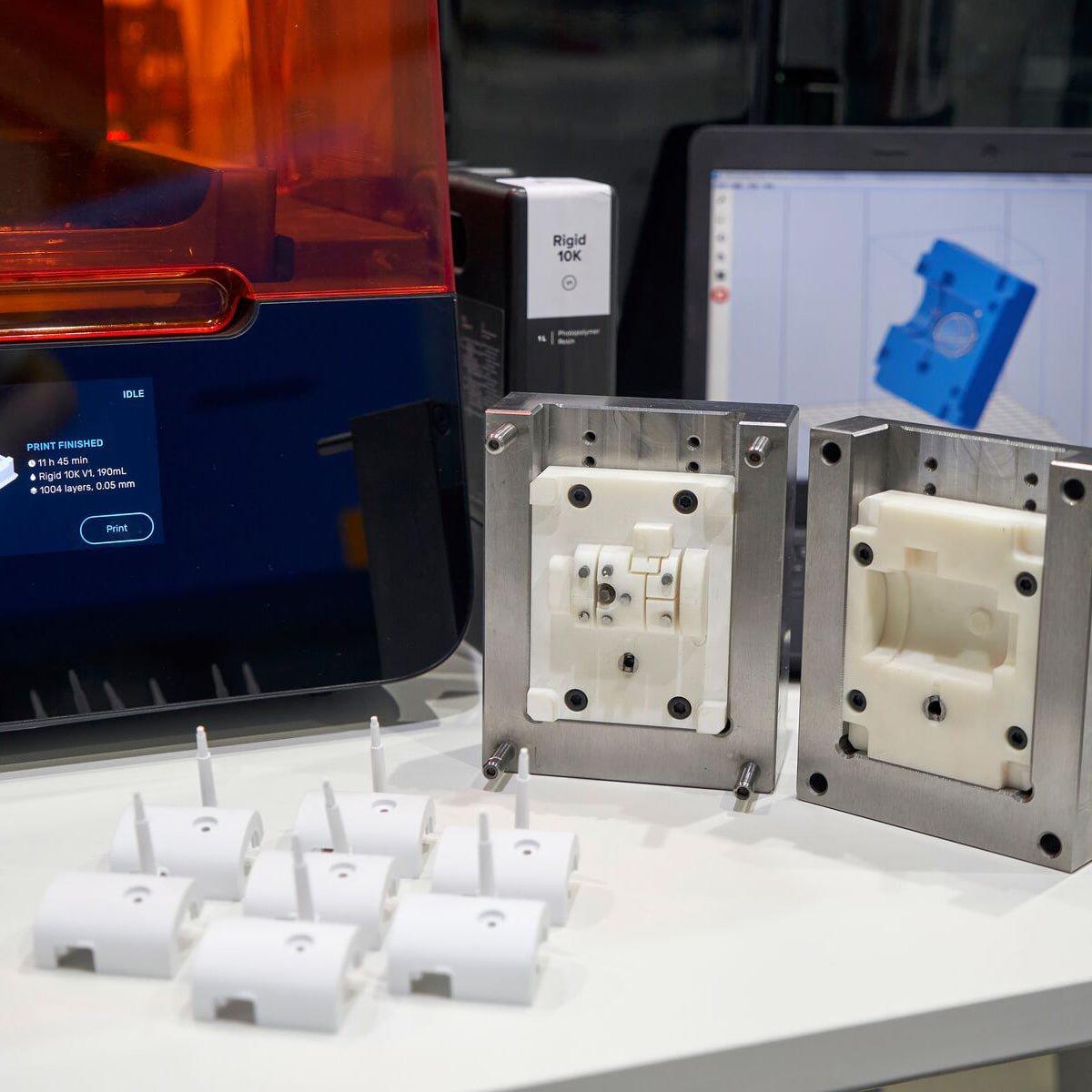
使用 3D 打印模具完成小批量快速注射成型
有关在注射成型工艺中使用 3D 打印模具以减少成本和备货时间的指南,以及 Braskem、Holimake 和 Novusr Application 的真实案例研究,请下载我们的白皮书。
加速实现电气化
福特承诺到 2030 年完全实现电动化,这为麦肯尼希产品研发中心工厂制定了雄心勃勃的路线图。为了达到必要的里程碑,公司必须继续寻找尖端技术,尝试新的创新工作流程。要保持竞争力,他们就必须突破极限,整合新材料、新工艺和新设备,如内部模具和 3D 打印。
“竞争对手正在加快研发进程。我们也需要加快速度。因此,解决方案就是测试新材料、新工艺和即将上市的新机器。目前,如果不能使用增材制造技术,我们就无法与竞争对手竞争,也无法做到如此之快速。3D 打印技术让我们能够在更短的时间内为客户提供最好的产品,”Alves 说。